Some problems arent as bad as they appear, and some are worse. Dealing with counterfeit process control devices isnt one of the easy ones. This is because fake equipment, its makers, and its collaborators constantly shiftdisappearing and reappearing to avoid detection.
Even definitions of what constitutes counterfeiting have many shades. For example, faking a manufacturers device and name is counterfeiting, but precisely mimicking its product is defined as imitation, which is harder to prosecute. Meanwhile, false process control components are accompanied by counterfeit plates, marks, documentation, certifications and other forms of verification. Some ambitious counterfeiters even use false sales representatives and set up fake corporate entities to further distract and deceive their victims (see Sidebar, Beware of Bogus Agents at the end of this article).
Similarly, besides fabricating fake devices, some counterfeiters take an even easier way out, and simply misidentify old or refurbished components. Likewise, many repair shops fix devices, but some unknowingly or knowingly leave on original plates and/or dont perform the testing needed to make sure these devices have as-new capabilities and service lives.
Internet = Wider Net
Lately these historical difficulties have been compounded by two recent trends. First, Internet-based businesses, such as eBay and others, routinely sell millions of dollars worth of process automation equipment and enable the smallest shop to market and deliver items worldwide. These speedy, global transactions can be helpful, but participants reportedly dont conduct as much verification and certification as traditional manufacturer-to-distributor channels. Second, besides the liability burden that end users must usually take on for their applications and equipment, increasing federal regulation of process controls used in pharmaceutical and food and beverage applications and more stringent documentation requirements are making it even more important to have genuine, tested and certified process devices in place.
We havent personally identified any counterfeit items, but our customers report seeing many items on eBay for more than 30% off list prices, says David Stock, a system integrator at Innovative Control Inc. (ICI), Crystal Lake, Ill. If someone else wants to purchase equipment that way its fine with me, but I think buying in an environment without distributors and traceability is a serious risk.
Stock agrees the Internet has added to this problem, and the usual distribution channels havent acknowledged it enough. Ive run into being audited by a customer on the software side, and had to verify that all my purchases were certified and legitimate licenses, says Stock. I think hardware will follow this model because users and suppliers need to identify the counterfeits.
Worldwide Scope
The International Chamber of Commerce (ICC) estimates that trademark counterfeiting accounts for about 6% of world trade and is worth an estimated $350 billion annually, according to a white paper, The Threat of Counterfeit Product Approval Marks Warrants Aggressive Detection and Enforcement Action, by a recent alliance between U.S. Occupational Safety and Health Administration (OSHA) and the American Council of Independent Laboratories (ACIL). In its mid-year 2005 report, the U.S. Department of Homeland Securitys Customs and Border Protection division reported that customs seized more than $64 million dollars worth of counterfeit products in 3,693 seizures. Electrical equipment, much of it intended for the U.S. workplace, alone accounted for over $6 million, stated the OSHA-ACIL alliances report. The International Anti-Counterfeiting Coalition (IACC) reports the majority of counterfeit products come from Asia, primarily China, and that Eastern Europe has also become a significant source. The manufacture and distribution of counterfeit products has been linked to organized crime. Counterfeit approval marks have been found on electrical products built using substandard materials and exhibiting compromised electrical spacingboth of which pose potential shock and fire hazards to U.S. employees.
Rob Bartlett, director of the British Valve and Actuator Association, says his organizations technical director reports there was very little counterfeiting of mainstream valves just five or 10 years ago, but now theres more anecdotal evidence than ever before about fake products and parts, coming mostly from Asia and specifically China. Everyone has a story. A lot of device manufacturers have seen their own literature cannibalized by XYZ Co. Theres not much evidence, but no western manufacturer has said another western manufacturer is doing it.
Whats happening is that the global energy industry is booming now after contracting and consolidating, but supplying this booming market is increasing lead times for equipment by weeks and months, and that can make it very tempting to accept devices with documentation that isnt what it should be. When youre in a rush, you may not check some certifications as close as possible. So, besides checking that documents arent bitmapped images and telephoning to confirm suppliers claims and identities, buyers also must be responsible for their devices audit trails, and make sure where, when and who makes these products.
Willing Participants
Unfortunately, some end users accept counterfeiting and knowingly buy fake devices that potentially endanger themselves, their co-workers, end users and the public.
Some people actually choose to purchase counterfeit products, assuming theyre paying less for products that are equal in value to the legitimate products they mimic. People who deliberately choose to buy counterfeit products are not victims. Instead, they support the criminally deceptive practices of counterfeiters by creating a built-in market for their goods. If consumers stopped using counterfeit products, counterfeiting wouldnt disappear. However, in many cases, counterfeiting would be less profitable and more risky without these easy sales, states the OSHA-ACIL report.
Bob Arnold, president of Rotork Controls Inc., Rochester, N.Y., says his firms U.K.-based parent found another company, Autork, producing and attempting to sell copies of its valve actuators in China and then exhibiting them in the Netherlands (see Sidebar, Rotork Copes with Copies at the end of this article). It all depends on what the market is willing to accept, says Arnold. What scares us is that the world has grown so much smaller. Folks have easy access to email addresses. For instance, they can buy a list at ISA and just start pumping out product introduction emails. Fortunately, customers we deal with say they wont buy copies. This is why its so important for users to make sure suppliers have legitimate certificates of compliance for each device, as well as original copies of FM and/or CSA approvals, and approvals for operating in hazardous areas, if needed. Weve found suppliers that say theyre compliant, but they usually dont have their certificates. We hoped that Chinas joining the World Trade Organization would have an impact on this situation, but it has not.
Repair and Refurbish
Though not strictly defined as counterfeiting or copying, misuse of identification when devices are repaired or refurbished is at least as unethical, and can cause many of the same problems and possible hazards. Several engineers report they havent seen fake process devices, but routinely see misrepresented or missing plates on those devices.
Bob Baker is a process safety consultant focused on educating process control end users about potential non-compliance with plant equipment design codes and standards, OSHA and/or EPA safety regulations, including process safety management (PSM), when using salvaged, refurbished, remanufactured, or repaired process control equipment. The need for greater end user understanding and visibility is due to ever-increasing amounts of used equipment being salvaged and resold into many plants. The supply of used equipment is especially large as the numerous facilities built in the 1970s and 1980s are retired and torn down, especially along the Gulf Coast.
This use of salvaged equipment really started in the offshore oil and gas industry and began to pick up in the early 1990s, says Baker. In 2001, it was estimated that only about 5% of Gulf Coast process plants were actively buying such salvaged/refurbished process equipment. By 2005, process plant use of such equipment was estimated to have grown 65-70%. This was driven primarily by its significantly reduced costs, yet providing operating viability comparable to new equipment.
Yet the overlooked aspect of such equipment was whether it continued to meet the original manufacturers design criteria necessary to comply with appropriate safety and regulatory standards for safe use. Statistics being what they are, an ever-increasing installed base of potentially non-compliant equipment may increase the risks incurring an incident.
For example, approximately two years ago, an OEM repair facility received that was supposed to be a Class 600 control valve from a major oil company refinery (removed from a Class 600 piping system handling hot hydrocarbons), and found that years earlier the valve was originally manufactured and shipped new to a major chemical process plant as a Class 150 valve, adds Baker. Apparently, at some point in time, the valves Class 150-rated flanges were cut off, and Class 600 flanges welded on. Since the OEM repair facility had never had prior access to the valve during its lifetime, further inquiry yielded information that more than one independent, third-party shop had previously performed repairs on the valve, but no traceability existed as to when the flange change occurred or who did it. The installation and use of a Class 150 valve (modified to have Class 600 flanges) for use in a hot hydrocarbon application with Class 600 piping system specifications could have resulted in a fire or explosive incident had the valve failed.
When a new plant is designed or an old one is repaired, everything within its piping systems needs to meet applicable ANSI and ASME pressure class ratings for wall thickness and shape, so theyll be able to safely contain the applications pressures and temperatures. If a plant doesnt meet its original standard, and theres a fire, explosion or hazardous chemical release, it can mean a huge increase in liability because the compliance burden is on the end user, says Baker. Thats why its important to be educated and aware of the potential safety issues with equipment on the plant floor. For instance, you can buy refurbished process equipment like used car parts, and they may work fine, but the question is: does the equipment continue to meet original OEM design requirements necessary for safe use and meeting safety and regulatory requirements?
For example, a refurbisher may buy a Class 600 valve from a former plant, and sell it as a Class 600 because thats what the nameplate says, but fail to account for the valves previous experience. Before selling, a salvager/refurbisher/remanufacturer should measure valve wall thickness at appropriate critical stress areas, and verify that it continues to meet specifications as originally designed by the OEM to meet applicable code requirements, but many may not know how to do it, may not care, or may not have the proprietary design information to for verification, says Baker. In addition, there can be uniform wall thickness degradation that isnt readily noticeable (unlike the visible signs of localized erosion). So, a valve may have been sandblasted and repainted, and looks like new, but its walls may not be thick enough to meet the valves original pressures class rating. OSHA and EPA process safety management regulatory standards typically refer to use of equipment suitable for the process.
Baker adds that checking wall thickness is so important because the traditional hydro test is only one of the two elements necessary to meet ASME B16.43 intent. Hydro testing involves filling a valve or component with water, and pressurizing it to 1.5 times its cold, working pressure rating. Many people in our industry have a paradigm that hydro testing is all thats required to ensure pressure class integrity, but buyers should ask their suppliers to certify wall thickness in addition to hydro testing.
With increasing age and typically unknown prior application history of salvaged/refurbished/remanufactured valves, meeting both of ASME B16.34 (paragraphs 6.1.7 for additional metal thickness and 7.1 for shell testing) should be a critical requirement.
To reduce the risk of non-compliance and better increase plant safety associated with salvaged/refurbished/remanufactured equipment, end users should implement appropriate awareness, specifications, and purchasing procedures to ensure that suppliers of such equipment are fully capable of restoring to original OEM design specifications.
In addition, to containing process pressures, the certification of electrical/electronic devices for use in hazardous (classified) locations is another critical issue associated with salvaged/refurbished/remanufactured instrumentation.
The Electrical Side
OSHAs 20-year-old Nationally Recognized Testing Laboratory (NRTL) program inspects the 18 labs presently authorized to test products (see Sidebar, Nationally Recognized Testing Laboratories at the end of this article), and confers non-incendive, intrinsic safety, and explosion-proof ratings on OEM-designed, new products. A subset of the 18 labs are authorized for specifically certifying process equipment for use in hazardous location. However, its the end users that bear the responsibility for ensuring compliance to OSHA 1910 electrical approval requirements. Any change made to an NRTL-approved device, even if inadvertent, may alter the devices design attributes as originally tested and certified by the NRTL too appropriate consensus standards.
When end users purchase equipment for use in hazardous locations, the NRTL certification mark on the device nameplate provides the confidence that the device continues to meet the codes and standards that the NRTL lab originally tested to, says Baker. For example, take the everyday, common task of removing and replacing the cover on an NRTL-approved device, such as during calibration, instrument installation, etc. When replacing the threaded coveran explosion-proof enclosureone must ensure the cover is screwed on with a specified number of threads engaged, or else the explosion-proof approval is not valid as originally tested by the NRTL. Further, if damage to the threads occurs due to cross threading (or a technician subsequently filing the threads to facilitate full engagement), then that instrument has incurred a change, and is no longer considered by NRTL as equal to what it originally tested and approved. When threads are damaged on an approved, explosion-proof device, then a potential flame path is created at the location of thread damage. Depending on instrument brand and design, there are other parts of and flame paths that could inadvertently create a change to an approved device during repair or component replacement.
My last several years of experience indicate that few end users fully understand the issues and requirements of NRTL approvals for instrumentation used in hazardous locations. And, similar to the control valve example mentioned earlier, an instrument salvager/refurbisher/remanufacturer may sandblast, repaint, and recalibrate an NRTL-approved device, and then usually leave the old nameplate containing the original NRTL approval certification mark on it. Some remanufacturers even create new nameplates, and weve seen unauthorized NRTL certification marks applied to them (NRTLs have classified such as counterfeit marks). NRTL labs, such as FM Approvals, have taken the position that if a devices ownership changes, then, until the device is re-certified by an NRTL-approved facility, the device is no longer considered approved, and its nameplate or certification mark and certification description should be removed.
Removing these should assist end users in appropriately applying the instrument, and avoid installing it in a hazardous (classified) location, because the NRTL certification mark or certification descriptions would no longer be present on the device.
While copying relatively big-ticket items like valves is attractive, it can be it can be even more tempting to fake smaller, more easily built items, such as circuit breakers and contactors.
Theres a tendency to think of counterfeiting as an outside-the- U.S. problem, but weve been getting a wake-up call in the past three to five years that this is a problem in the U.S. too, says Jim Pauley, industrial and government relations VP for Schneider Electrics North American operating division. For example, we received a phone call from the U.S. customs office in San Francisco a couple of years ago because they found a person trying to get through from China with a suitcase full of circuit breakers with our Square D logo and UL labels on them. All of them were fakes. This has led to several ongoing litigations, and six settled lawsuits, but we think the overall state of the problem is still much worse than people realize or are willing to admit that it is.
Pauley adds that users can learn more or report possible fake circuit breakers by visiting www.squared.com and clicking on more information about counterfeit circuit breakers.
The old adage that if a deal seems too good to be true, then it probably is was never more true than now, says Pauley. However, for us, counterfeits also mean that the safety capabilities that users depend on from products with our name on it may not be available. The danger is that users may not realize this until years later, when those fake devices are called on to work and fail instead. So counterfeiting doesnt just involve stealing intellectual property, it also puts people at risk.
Pauley adds that Schneider estimates there are hundreds of thousands of counterfeit devices presently in use worldwide. This is what we know, and there are probably more, he says. Customs usually inspects about 2% of all cargo, and the rest cant all be crystal clean.
Retesting Recommended
Though it does add an extra step, users can get questionable or salvaged/refurbished/remanufactured devices recertified through inspection and testing. Most end users and process suppliers dont understand the issues and NRTL approval status of such equipment, so were trying to make them more aware of what they can and should do, says Baker. For example, anyone who specifies or buys electrical process instrumentation for use in hazardous locations should require the seller to provide proof that its salvage/refurbish/remanufacture facility is approved by the appropriate NRTL for the specific brand and model of the used device being purchased. If the facility is not NRTL approved as noted, then the end user should require that the original OEM nameplate be removed, or that all NRTL approval certification marks or descriptions be removed.
Regardless of the above safety and regulatory compliance issues associated with pressure integrity of valves or NRTL approvals of instrumentation, Baker adds that end users can assume risk, and purchase any type of devices they want, whether certified or not. However, in light of todays litigious society and the availability of OEM-aligned facilities that offer certification to OEM design standards, they can perform appropriate supplier due diligence, and reduce such risk. Engineers are typically very attentive to codes when specifying valves and instrumentation for new plants, but something just seems to get lost when in the small project or maintenance areas that may turn to salvaged/refurbished/remanufactured equipment. Sure, the salesman says a valve or instrument will look and operate as good as new when its refurbished, but you just dont know if the equipment is safe (meeting all original OEM valve design specifications or instrument NRTL approvals) until its tested and certified. The crux of all this is getting buyers to ask for salvaged/refurbished/remanufactured valve or instrument certifications, and for sellers to provide it or acknowledge to having the capability to provide it.
Unfortunately, most buyers still dont ask these questions, and still rely on mostly visual inspections. Given the increasing use of salvaged/refurbished/remanufactured equipment, this logically means that thousands of such devices are being reinstalled without securing valve integrity/pressure class certification and/or ensuring instrument NRTL approvals for use in hazardous locations.
Its sad that the marketplace tends to overlook the above issues, and focuses on prices of such equipment that typically cost only 40-50% of he cost of new, adds Baker. Still, there are a lot of OEMs doing the right things, and end usersjust by asking the right questionscan find and buy rebuilt devices (at comparable savings) from qualified suppliers that are doing the proper testing and certifications. You can get the savings you need, and still reduce risk and increase plant safety by appropriately qualifying your supplier base. Just ask a prospective supplier if you can have the valve tested, and certified for both wall thickness and hydro. If not, find someone who can. Or, with electrical devices for use in hazardous locations, ask to see the suppliers facility records, showing approved audits by the appropriate NRTL (for brand and model instrumentation). If not, find someone who has them.
Stay Close to Suppliers
Perhaps the best way to avoid counterfeit devices is to buy from manufacturers and distributors that are well known to your own company and its engineers. However, its also vital to maintain frequent personal contact with authorized suppliers because counterfeiters can set up false representatives and corporations to support their fake products and documentation.
We buy directly from distributors and manufacturers we know well, and this forms a closed-territory network, so heres really no way for a counterfeiter to get into that chain, explains Rick Caldwell, a system integrator at SCADAware Inc., Bloomington, Ill. Now, if we decided to buy a new PLC on eBay, there might be a problem because the seller could be a trunk slammer or some other fly-by-night supplier.
Rick Pierro, a system integrator with Superior Controls, Seabrook, N.H., says the process control fields culture is very careful, and that its engineers dont buy components based on price. We see a lot of emails from China offering very inexpensive flowmeters and other components, but weve never bought them, says Pierro. These days, we often have to validate and confirm our software licenses, and I think these kinds of certification are going to find their way into hardware, too.
When eBay Works
Despite all the criticism against using eBay to buy process control devices, some users report that its worked well for them, though they add caution, due diligence, testing, validation, certification and documentation are even more crucial in any online marketplace.
We know an older foundry that recently needed some old Modicon components and bought them on eBay, adds Caldwell. However, these were very simple parts, and the foundrys engineers knew that what was being offered was exactly what they needed. Even so, they checked out the components before buying them, and everything worked out fine.
Pierro adds that one of his New York-based firms recently had a contract for a project with a large pharmaceutical manufacturer, but this contract couldnt be altered once it was validated. Unfortunately, the contract also referred to a pump that was needed by model number instead of function, and faced renegotiating the contract when the precise device couldnt be found. They found the pump on eBay in the U.K., and got it shipped to them in two days, which saved a lot of time and expense, says Pierro. So, eBay really helped in this case.
Pauley adds its probably fine to buy a contractors leftover 10-pack of circuit breakers on eBay, but greater numbers raise more questions about where theyre coming from. When you see higher volumes and a supplier saying it can deliver any amount, you have to ask if this is a legitimate source, says Pauley. This is why you cant just run to the Internet to buy circuit breakers. You have to know your sources and start further up the food chain. If you wait until a product is delivered, its probably too late.
Anthony Todarian of the Canadian Standards Association (CSA) adds that it and other agencies regularly issue product alerts and recalls when it finds counterfeit products, and that eBay and other online sellers have promised to remove them when theyre notified.
Better Cosmetics = More Headaches
While close visual inspection of devices and documentation is supposed to help find counterfeits, several sources say the external appearance of many fakes is so good that theyre almost indistinguishable from their genuine counterparts. In fact, even newer identification technologies, such as RFID chips and laser etching can be quickly adopted by counterfeiters too. This makes it even more crucial for users to check the insides of devices and test their performance.
Many counterfeits look pretty much like the real thing. They may even have duplicate die marks and moldings that serve no purpose. We even added a holographic label to one product, and then the counterfeiters did it nine months later, says Pauley. Sometimes our engineers have to take apart devices to compare the legit and counterfeit version, and the fakes ones quickly fail if their performance is tested. Todarian adds these failures occur because the only way for counterfeiters to make money is by leaving out the needed capabilities and safety features included in genuine products.
The bottom line on counterfeiting is that its an ongoing battle, much like the eternal manufacturing and business challenges to innovate, gain efficiencies and do more with less. To stay one step ahead, you just have to keep stepping.
Beware of Bogus Agents
Everyone knows that fake documents can accompany fake products, but sometimes counterfeiters will even send out fake peoplecounterfeit representatives posing as authorized agents. The British Valve and Actuator Association (BVAA) reported in its Valve User publication, Spring 2007, that one of its members recently appointed a new sales agent in an Asian nation and attempted to register this change with the countrys national oil and gas company, which is itself a leading multinational firm. BVAAs member was stunned to find that another agent, claiming to be its official representative, had already formally registered with the oil company!
Further investigation revealed that the bogus agent had furnished the oil company with forged agency documentation, including forged signatures, stated Valve User. The oil company reportedly hadnt verified the fake agents status directly with the manufacturer. Thankfully, the national oil company immediately ended its association with the bogus agent when the fraud was discovered.
The publication adds that its not just the counterfeiting of products that presents problems these days. The Internet makes downloading and copying of company literature and logos extremely easy. BVAA recommends that users should study such documentation carefully for the telltale signs of poor quality logos and illegible signatures. In any case, its always advisable to verify that agents truly are the local representatives of manufacturers. A simple email to a manufacturers global headquarters could avoid a great deal of trouble later on.
Beware Tips for Identifying Counterfeits
The alliance between U.S. Occupational Safety and Health Administration (OSHA) and American Council of Independent Labs (ACIL) has drafted recommendations to help users identify counterfeit devices. These tips include:
- Look for the markA system of standards exists for testing and certification of products. Be wary of electrical, mechanical, plumbing, gas or other standardized products if they dont have a certification mark from a nationally recognized testing laboratory (NRTL).
- Inspect the markLegitimate certification marks have distinctive graphics that often arent accurately reproduced by counterfeits. For a current list of NRTLs or their marks, visit OSHAs website at www.osha.gov/dts/otpca/nrtl/index.html.
- Poor spellingLook for misspellings and unclear printing on packaging, products, labels or instructions.
- Inferior packagingCounterfeit packaging often has poor design or shows only partial illustrations. Also, foreign newspapers may be used as packaging, and there may be questionable or meaningless markings, incorrect language or spelling errors.
- Missing itemsCheck for missing product information or discrepancies between package contents and the items description on the package. There also may be missing instructions, screws and terminals.
- Know your sourceBuy only from reputable, well-known distributors or retailers.
- Significantly lower pricingDeals that are too good to be true could mean a device is counterfeit, and so it should be checked even more closely.
- Cheap productionIf a devices look and feel is too tight and flimsy, it might be a fake. Check for signs of used appearance, evidence of tampering/repairs, broken seals, scratches, obvious wear, corrosion, pitting, components with no certification markings, different material types, finishes and/or inconsistent colors.
Rotork Copes with Copies
Rotork Controls had been working in China for about 10 years when its sales staff learned in 2003 that a firm called Autork Digital Apparatus was selling imitations of U.K.-based Rotorks IQ Series actuators, and even using a catalog featuring photographs of genuine Rotork actuators. Then things got worse.
Graham Ogden, Rotorks R&D director, says his 50-year-old company tried to get Shanghai-based Autork to stop its selling activities, but found this to be very difficult. This is because Chinas Administration for Industry and Commerce (AIC) bases its enforcement on trademark infringement, but cant prevent imitations sold under other company names, particularly when the infringer has registered its name themselves, says Ogden. As far as Autork is concerned, Rotork presently has several intellectual property lawsuits moving through the Shanghai Peoples Court of China, but these can be hard to prosecute, especially if the counterfeiters have registered their own trademarks, and pretend to be engaged in lawful competition. Then things got worse againjust before getting better.
Before the opening of a Netherlands-based tradeshow in late 2004, Rotork was notified that Autork was going to exhibit its imitation actuators. Ogden says Rotork appealed to the Court of The Hague, which granted an ex parte action. This allowed it to secure an injunction, and have Autorks products seized as the event began. Subsequently, the court ruled in April 2007 that Autork was guilty of slavish imitation, breach of copyright, violating design rights of Rotorks actuators and infringing Rotorks trademark. The court ordered Autork to immediately stop infringing Rotorks proprietary rights throughout the European Community, and to remove infringing product from storage addresses, distribution points and customers. Meanwhile, Autork reportedly continues to be active in some parts of China.
In a statement, Rotork urged its customers and users to avoid inferior imitations of its products, which havent been subjected to the same level of third-party approvals and certifications. We offer the same advice to all valve and actuator usersbe wary of what you buy and from whom you buy it, stated the company.
As a result of its experience, Ogden reports that the only way to have any protection against imitations and counterfeits is for manufacturers to register designs, trademarks, copyrights and patents in whatever country it plans to do business. In China, this means registering trademarks, making a required check of the names translation and pronunciation in Mandarin, employing a trademark watch service to advise of similar registrations, and checking on the Internet to see if a planned trademark has already been registered by someone else. In the U.K., design rights are granted automatically for a limited period, although in both Europe and the U.K., manufacturers can make formal registrations, which may give stronger protection against slavish imitation. Because automatic protection isnt available in other parts of the world, he suggests checking on the local countrys intellectual property laws, and perhaps filing 3-D design registrations in those regions.
Action can be taken against infringement in other nations, but manufacturers must determine what rights they have there, and register their intellectual property, says Ogden. End users shouldnt buy a device or components unless theyre sure where it came from, and they need to understand the entire supply chain between where a device was built and their plant. If you can completely trace a product back to its manufacturers, then you can be as sure as possible that you have the genuine one you wanted.
Nationally Recognized Testing Laboratories
The NRTL program recognizes 18 private-sector organizations that have met the necessary qualifications to be NRTLs, and they determine that specific products meet consensus-based safety standards to assure that theyre safe for use in U.S. workplaces. However, each NRTL has different scopes of recognition, which are the standards, sites, and programs that OSHA has recognized for that lab. These can be viewed at www.osha.gov/dts/otpca/nrtl/index.html. The present NRTLS are:
- Applied Research Laboratories (ARL)
- Canadian Standards Association (CSA), also known as CSA International
- Communication Certification Laboratory Inc. (CCL)
- Curtis-Straus LLC (CSL)
- Electrical Reliability Services Inc. (ERS), also known as ETI Conformity Services, and formerly Electro-Test Inc. (ETI)
- Entela Inc. (ENT)
- FM Approvals LLC (FM), formerly Factory Mutual Research Corp.
- Intertek Testing Services NA Inc. (ITSNA), formerly ETL
- MET Laboratories Inc. (MET)
- NSF International (NSF)
- National Technical Systems Inc. (NTS)
- SGS U.S. Testing Co. Inc. (SGSUS), formerly UST-CA
- Southwest Research Institute (SWRI)
- TÜV America Inc. (TUVAM)
- TÜV Product Services GmbH (TUVPSG)
- TÜV Rheinland of North America Inc. (TUV)
- Underwriters Laboratories Inc. (UL)
- Wyle Laboratories Inc. (WL)
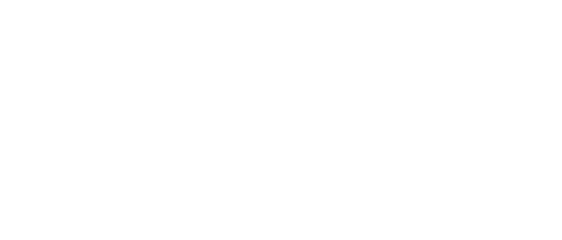
Leaders relevant to this article: