Ammonia plant simulation shortens ramp up, improves training
Explosives maker Austin Powder Co. recently faced a supply challenge. The company based in Cleveland, Ohio, sells detonation products used in quarrying, mining, construction and seismic exploration. And, because ammonia (NH3) is a key ingredient in the ammonium nitrate used in explosives, Austin Powder requires a secure NH3 supply at the right price. Its challenge is that ammonia is also used to produce plastics, fibers, pharmaceuticals and fertilizers—with the last category consuming 80% of total world production. This means all other applications have to get what they need from the remaining 20%, which can create some tight supply situations.
Consequently, Austin Powder formed a subsidiary, U.S. Nitrogen, to build and operate ammonium nitrate production plants. The first is under construction near Greeneville, Tenn., and will eventually produce 420 tons of liquid ammonium nitrate per day.
To help its new plant start producing ammonium nitrate sooner, U.S. Nitrogen used advanced simulation technology to debug its control system, and train operators in startup and shutdown procedures—as well as how to handle rare process excursions. All of this occurred before the physical plant was built.
"The use of the simulator is near to the real-life experience of operating a processing plant," says Barry Cunnington, U.S. Nitrogen's lead trainer and longtime ammonia industry consultant. "After the system FAT [factory acceptance test], I see it's going to be a very helpful tool."
However, simulation's benefits at U.S. Nitrogen won't stop after startup. Simulation and its supporting models are a way to capture the expertise of skilled personnel. Initial and future training will instill this knowledge in new operators for smoother and more efficient plant operations.
Making ammonia step-by-step
Though starting an ammonia production plant from scratch can be a risky business, U.S. Nitrogen eliminated most of that risk by licensing a NH3 production process. Making ammonia involves reacting one part nitrogen with three parts hydrogen at about 400-450 °C and at up to 340 atmospheres of pressure. The operating pressure and temperature are a compromise between the need to produce ammonia and the cost of running pumps, as well as the added capital expense of using strong pipes and reaction vessels.
To produce ammonia, a hydrocarbon such as natural gas is processed to produce hydrogen, while atmospheric nitrogen (N2) is the source for the other feedstock. The nitrogen-nitrogen bond is strong, so iron-based catalysts are used to prod the reaction along. The single-pass ammonia yield is only about 15%, but using multiple passes boosts the yield to better than 95%.
The block diagram in Figure 1 illustrates this multi-step process. It requires careful control due to the presence during processing of hydrogen sulfide, hydrogen and carbon monoxide. These gases are poisonous, corrosive, flammable, explosive or all of the above. Hence, ammonia manufacturing can require extensive capital investment to ensure proper process control and safety.
Figure 1: The ammonia-making process includes primary and secondary natural gas reformers that free hydrogen. There are also shift reactors to convert carbon monoxide to carbon dioxide. Sulfur is removed from the feed at the beginning of the process because it kills the catalysts, and the acidic gas H2S is eliminated by reacting it with zinc oxide. The final step before ammonia synthesis removes small residual amounts of carbon monoxide or dioxide from the hydrogen stream.
Photo credit: Milton Beychok
The process includes primary and secondary natural gas reformers that free the hydrogen. There are also shift reactors to convert carbon monoxide to carbon dioxide. Sulfur is removed from the feed at the beginning of the process because it kills the catalysts, and the acidic gas H2S is eliminated by reacting it with zinc oxide. The final step before ammonia synthesis removes small residual amounts of carbon monoxide or dioxide from the hydrogen stream.
Recreating Experience
At first glance, it might seem that the ideal solution for training operators to manufacture ammonia in U.S. Nitrogen's plant would be to have them practice startup, shutdown and response to various scenarios using actual equipment. However, taking such an approach in the real world is not practical or efficient.
On the practical side, training with real equipment would be expensive and dangerous. After all, there's a specific sequence that boilers and other modules must follow to be brought on line or taken off, and there are high pressures that must be dealt with, not to mention dangerous gases. The correct sequence of actions is specified in the plant’s standard operating procedures (SOPs). The same documents also contain instructions about how to handle such problems as stuck valves, pump failures and boiler mishaps.
If actual plant equipment were used, failure by operators to follow recommended procedures could result in damage to expensive equipment, harm to plant personnel, or even an incident noteworthy enough to make the national news. What’s more, deliberately putting a plant in an unsafe operating condition as part of a training exercise could result in regulatory review or litigation, if and when the practice came to light, even if nothing catastrophic happened.
One reason why U.S. Nitrogen located its plant in the Greeneville area is its pool of skilled personnel. They're capable of standing on the plant floor, listening to the machinery, and determining, despite the din, that a particular pump is having problems and needs maintenance. They can do this because they have decades of experience. However, this long work history also means some are nearing retirement, which means they'll soon leave and take their expertise with them. An efficient solution would codify this accumulated knowledge, and make it available for use by others.
Training with actual plant equipment wouldn't accomplish this because rare events, by definition, do not occur very often. Thus, they may not arise before skilled employees depart. Consequently, a live plant is not the best way to transfer expertise from more to less experienced personnel.
Lifelike, but Safe
Confronted by the need for safe, effective training and the requirement to capture scarce expertise, U.S. Nitrogen decided that dynamic simulation was the right solution. This approach offered the ability to run through start-up and shutdown procedures with no risk to anyone. In this way, operators could gain valuable experience by training before the new plant was completed. Also, a parallel training and construction approach would minimize any delay in plant startup.
In addition, scenarios could be devised that included such simulated events as pump failure, valves sticking open or closed, pipe ruptures, or other rare events. Familiarity with such process excursions could be critical to the ability of operators to successfully resolve them if they happened.
However, this approach presented U.S. Nitrogen with its own set of requirements. Chief among them was that the simulation had to be lifelike. There had to be a high degree of fidelity between the simulation and the actual plant, or the training would be counterproductive, with operators familiarizing themselves with something that diverged in critical ways from reality.
Done with high fidelity, dynamic simulation offers benefits beyond operator training. It can aid in capturing the knowledge and lessons learned by experienced operators, ensuring expertise is not lost. It can also help analyze safety and environmental risks. Dynamic simulation can also help process optimization by allowing process improvement studies. During the capital phase of a project, it can also assist in testing control systems for operational readiness by allowing very lifelike exercising of the distributed control system (DCS). This testing can include both the basic process control system (BPCS) and safety instrument system (SIS). There are also other areas in the capital and operational phase of a project that can benefit from dynamic simulation.
In addition to high fidelity, other important simulator characteristics are the ability to communicate with external control systems and the use of modeling standards. The first ensures that control systems can be fully exercised, while the second avoids problems that can arise from proprietary solutions.
The Simulation Solution
After considering the alternatives, U.S. Nitrogen selected Mimic simulation software from Mynah Technologies. This simulator has an ammonia plant module with access via an OPC server to all model parameters, and has bridge communication with external control systems. All model objects in the simulator are industry-standard IEC 1131 function blocks. When it comes to ammonia production, Mimic's dynamic simulator includes the important process areas of:
- Natural gas primary reformer, coupled with a waste heat boiler;
- Natural gas secondary reformer;
- High- and low-temperature shift reactors;
- Acid gas removal system;
- Methanator;
- Ammonia converter; and
- Auxiliary separators, heat exchangers, fluid movers and piping.
Each of these areas is rigorously modeled, ensuring that the entire process can be simulated with a high degree of fidelity. Doing so involves dynamic, real-time mass and energy balances, vapor-liquid equilibrium, catalyzed reforming and oxidation reactions, along with other factors.
Once the selection process was complete, U.S. Nitrogen approached Mynah with a desired schedule. Only six months were allocated from initiation of the project to FAT of the simulator. During that span, a design specification would have to be devised and approved, followed by development of the simulator. The timeline ran from mid-March to mid-September 2013.
Figure 2: To aid testing, training and optimization, U.S. Nitrogen adopted Mimic simulation software from Mynah Technologies, which has an ammonia plant module with access via an OPC server to all model parameters, and has bridge communication with external control systems.
Photo credit: Mynah Technologies
The control system for the plant was Emerson Process Management’s DeltaV. It includes a control system emulator, DeltaV Simulate, which can configure features, such as continuous control, batch control, advanced control and associated workstation displays, alarms and historian data collection. The simulation is highly accurate, and there's no need to actually have DeltaV hardware deployed. Because it offers integrated simulation of BPCS and SIS, modules for both can be designed and tested. Next, Mimic simulation software communicates directly with DeltaV Simulate via OPC. As a result, the control system believes it's communicating with real equipment in the field, providing a highly realistic experience to the user.
By mid-September 2013, Mynah had fully developed the simulator for U.S. Nitrogen. However, the plant had run into permitting and construction delays, so there wasn't a need to train operators yet. So, by early October, the simulator was put to work debugging the control system.
"The programming used to simulate the process reaction is second to none," says Cunnington. "It responds to process changes similar to the actual plant."
Weatherly Inc. in Atlanta, Ga., a subsidiary of Sweden-based Chematur Group, was the engineering firm in charge of designing the ammonia and nitric acid plants and the rest of the facility. Weatherly has been designing and overseeing the building of ammonium nitrate manufacturing facilities for more than 50 years, but even with all of its experience, designing and debugging a complicated control system is not trivial. So, while the permitting and construction process played out, Mynah worked with Weatherly by testing the plant’s DeltaV DCS against the Mimic model.
The expected results from the start-up and shutdown procedures were known, as were the predicted outcomes of the process excursions found in the training scenarios. The simulation results obtained from the model for these various situations were compared to what was expected, with any discrepancies noted. Lists of deficiencies attributable to either the BPCS or SIS were delivered to Weatherly, and these were then used to solve and correct control system issues.
Real-World Results
The simulator underwent FAT late in Q3 2014. That was several months before the projected completion of the plant and its expected start-up. Thanks to using the Mimic simulator in its control system testing, U.S. Nitrogen reports its start-up should be smoother and faster, and will continue to positively impact operator training.
Figure 3: Mimic software simulator at U.S. Nitrogen's new ammonium nitrate plant will make its s start-up smoother and faster, and will continue to positively impact operator training because its high-fidelity simulation will ensure its training exercises are effectively indistinguishable from real operations. They'll also gain experience in how to handle process excursions, and will be better prepared for unusual occurrences.
Photo credit: Mynah Technologies
Current employees will be well versed in how to start up and shut down the plant because its high-fidelity simulation will ensure its training exercises are effectively indistinguishable from real operations. Operators will have experience in how to handle process excursions, and will be better prepared for unusual occurrences. In addition, the development of training scenarios is ongoing, and new ones will be devised to capture the expertise and knowledge of skilled operators. In turn, these scenarios will be used to train new operators and further the professional development of the plant’s staff.
"The operators will gain a lot of experience from using the training system, and the company can ensure the operators are qualified to actually operate the plant before initial plant startup." adds Cunnington. "This is especially important because this is a greenfield plant complex."
Finally, the result of U.S. Nitrogen's successful simulation will be a more efficient and smoother operating plant, with the added benefit of faster ramp up to full production due to a fully debugged control system. This assures that U.S. Nitrogen will be able to meet the needs of its parent company for ammonia and ammonium nitrate, which will solve the initial problem the plant was meant to tackle.
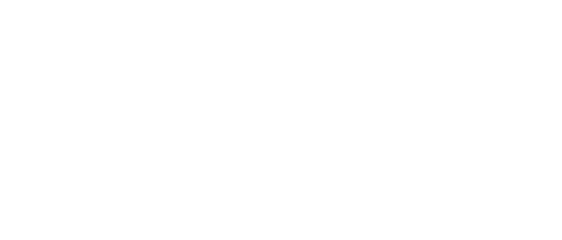
Leaders relevant to this article: