Terry Blevins, principal technologist, Emerson Process Management, is a member of the Control Process Automation Hall of Fame (2004). Neil Peterson is DeltaV product marketing director, Emerson Process Management.
The problem with wireless
Many of the control techniques and guidelines established during the development of single-loop digital controllers in the mid-1970s are based on mimicking an electronic analog controller. Guidelines established for setting the control execution period were designed to ensure that the control response and behavior duplicated those provided by an analog controller. To minimize any delay introduced into the control loop by I/O access, the field measurements were highly oversampled; for example, a 50 msec update rate.
This update rate would quickly deplete the battery in a wireless transmitter (Figure 1). To achieve a battery life in the range of 5–7 years the wireless transmitter communication update rate should be configured to transmit a new measurement value every 8 seconds or slower.
Figure 1: The affect of update rate on battery life varies by transmitter type, but a battery life of 5–7 years generally requires a transmitting a new measurement value every 8 seconds or slower.
Thus, it is necessary to re-examine how control should be structured for use with wireless measurements. A new approach known as PIDPlus makes it possible to control using wireless measurements while delivering control performance that is comparable to traditional wired transmitters and wired final control elements. The modifications in PID introduced by PIDPlus are designed to address loss of communication and enable control using slow measurement and non-periodic measurement updates.
Also read: Addressing control applications using wireless devices
PIDPlus opens the door to wireless control
Within the process industry, the standard and/or series forms of the PID algorithm have been adopted by the major distributed control system (DCS) suppliers. Conventional PID design is based on the assumption that a new measurement value is available each execution, and that the PID control is executed on a periodic basis. When the measurement is not updated as fast as the PID execution rate, the calculated reset action may not be appropriate. Thus, at first it may appear that there is no technical solution that minimizes how often a measurement may be communicated without compromising control performance.
The key to understanding how the PID must be modified is to realize that the PID reset contribution is a direct reflection of the process dynamic response. This relationship is clearly shown in established model-based tuning rules.
To provide the best control using slow non-periodic measurement updates, the PID may be restructured to reflect the expected process response since the last measurement update as the reset contribution. When the reset contribution of the PID is implemented using positive feedback network, the modifications required for PIDPlus behavior are illustrated in Figure 2.
Figure 2: For the best wireless control, PID may be restructured into PIDPlus so the reset calculation automatically compensates for setpoint changes that are made between measurement updates or changes in output introduced by feedforward action.
Here, the reset calculation automatically compensates for setpoint changes that are made between measurement updates or changes in output introduced by feedforward action. Within the PIDPlus implementation, the positive feedback network used to create the reset contribution is modified to have the following behavior:
- Maintain the last calculated filter output until a new measurement is communicated.
- Use the new filter output as the positive feedback contribution when a new measurement is received.
For those processes that require derivative action, the derivative contribution should be recomputed and updated only when a new measurement is received. To account for the fact that a new measurement value is not available for each execution of the PID, the elapsed time since the last new measurement was communicated is used in the derivative calculation.
How PIDPlus is implemented
In an application where PIDPlus is used in wireless control, the control execution rate is set much faster than the wireless measurement update rate. For example, the control execution rate may be set to 0.5 seconds even though the communication update rate is set to 8 seconds. This is necessary since the control execution within the DCS is not synchronized with the measurement communication. Scheduling the control execution in this manner minimizes any delay in a new measurement value being used in control. Also, this permits immediate control action to be taken on setpoint changes and changes in feedforward inputs.
The PIDPlus tuning is based strictly on the process dynamics. For example, if the RESET units are seconds per repeat, then RESET = process time constant + process deadtime (sec). The PIDPlus reset implementation automatically compensates for variations in the measurement update rate and slow measurement update rates. No change in PID tuning is required for slow or varying update rates or for variations in measurement communications.
A timestamp accompanies new measurement values that are communicated by a transmitter to the wireless gateway accessed by the DCS. This timestamp may be used in the DCS to determine when a new measurement has been communicated. However, some distributed control systems use a change in the measurement value to detect that a new measurement has been communicated. If this mechanism is used to identify a new communication, it is critical that filtering not be applied in the measurement path to the PIDPlus. If filtering of the measurement is required, it should be done by adjusting the transmitter damping.
Wireless vs wired: Lab tests
Extensive tests of wireless control using PIDPlus have been conducted in one of Fisher Controls' flow labs located in Marshalltown, Iowa. In these tests, closed-loop flow control was evaluated using both wireless and wired flow measurement. The primary objective of these tests was to measure and quantify the deviation of the control parameter from setpoint as a measure of control performance. In addition, communication statistics were collected for tests that used wireless transmitters.
Two different tests were conducted with the option to select the source of input used in control i.e. wired or wireless:
- Control Response to Setpoint Changes: The control response was observed for a series of changes in PID/PIDPlus setpoint in Automatic mode. For this test, the load valve installed in series with the valve regulated by the PIDPlus was maintained at a constant (normal operation) position.
- Control Response to Unmeasured Process Disturbance: The control response was observed with the PID/PIDPlus in Automatic mode and at a constant (normal operation) setpoint while unmeasured disturbances were introduced by a series of changes in the load valve.
Tuning for the wired flow transmitter and wired throttling valve was established using a standard DCS PID tuning application. This was intentionally done to demonstrate that no special skills were used in tuning the PID. The average tuning for three operating points was:
Gain = 0.8 Reset = 3.2 Rate = 0
The tuning established for the wired control loop was used without modification in the wireless control tests where the wireless update rate was 8 seconds or 16 seconds. During each of these tests, the integral of absolute error (IAE), and communications statistics were calculated. Screen captures of the chart showing the control loop parameters were made after each automated test. The response to setpoint changes using a wired valve and wireless transmitter with communication update rate set to 8 seconds is shown in Figure 3. A similar well behaved control response was observed when an unmeasured disturbance was introduced into the flow process.
Figure 3: When wired control loop tuning was used without modification in wireless control tests, integral of absolute error (IAE) and communications statistics showed a well behaved control response.
The wireless control test results achieved in the flow lab using PIDPlus with a wireless flow transmitter and industrial-size valve and piping can be summarized as follows:
- PID tuning was set strictly based on the process gain and dynamics. The fact that the tuning was never changed throughout the wireless test illustrates that the PIDPlus tuning is not impacted by transmitter update rate and delay introduced by communications. Good control was achieved in all wireless transmitter tests using this tuning.
- The wireless transmitter update rate was set to 8 seconds for most of the tests and introduced variable delay in the flow measurement used in control. However, this had no impact on the stability of PIDPlus control and had minimal impact on control performance.
- When a wireless transmitter was used with PIDPlus, the number of changes in valve position was reduced by a factor of 47 since the output of the PIDPlus only changes when a new measurement is received or the setpoint is changed.
- Changing the wireless transmitter update rate from 8 seconds to 16 seconds had minimal impact on control performance.
Wireless in the field
The ability of PIDPlus to use slow and variable communications from wireless transmitters allows wireless control to be used in a wide variety of industrial applications. For example, wireless control has been demonstrated on the following sample applications from the life science and specialty chemical industries:
- Bioreactor control: Wireless control of pH and temperature.
- Column splitter: Wireless control of reboiler steam flow and column pressure.
The benefits of PIDPlus for these applications are typical of those using wireless measurements. The field experience using wireless transmitters with PIDPlus in these applications may be summarized in the following manner:
- The performance of PIDPlus in a wireless control network is comparable to that of PID with wired inputs.
- PIDPlus tuning depends upon process dynamics only, not on wireless update rate.
When the PIDPlus algorithm is used with a wireless transmitter in a control application, the performance will be comparable to that achieved using a wired transmitter. If immediate response to an unmeasured process disturbance is not critical, then an 8-second update rate may be used.
The power required for the transmitter can be significantly reduced when long-interval periodic communications and PIDPlus are used. Compared to the wired transmitter, wireless communications reduced the number of new measurement values using communications by over 96%. The resulting reduction in transmitter power requirements enhances the potential for an increased number of control applications that may be addressed using wireless transmitters.
Behavior on loss of communication
The reliability of WirelessHART device communication has been well established. Even so, the expected control behavior in the event of communication loss is of interest and must be considered when using wireless measurements in closed-loop control.
The behavior of PIDPlus on loss of wireless communication has been compared to PID with a wired transmitter where the measurement is frozen for a period of time. The PIDPlus response on loss of communication during a setpoint change or an unmeasured process disturbance was observed to provide superior dynamic response. If standard PID is used with a wireless measurement to control slower processes, it is critical to add logic to shift the control to manual on loss of communications. Unless this logic is added, the PID output will wind up on loss of communications. When using PIDPlus in wireless control, the last reset contribution is automatically maintained on loss of communication.
Wireless control with a legacy control system
Where PIDPlus is a standard feature of the distributed control system, users will encounter little difference when implementing wireless control. For example, enabling PIDPlus capability may be an option parameter of the PID. If PIDPlus is not supported by the DCS, then in many cases it is possible to create PIDPlus control using existing tools within the DCS.
In a legacy control system, it is possible to construct PIDPlus capability if the PID supports external reset. This is done by setting the reset of the PID to a value that eliminates the impact of the filter in the positive feedback network, then constructing the external reset input to duplicate that used in the PIDPlus (Figure 4). To provide bumpless transfer when the PID mode is switched to Auto, the filter should be initialized to the PID output value when the block is in Out-of-Service or Manual mode.
Figure 4: If the existing PID supports external reset, it is possible to construct PIDPlus capability by setting the reset to a value that eliminates the impact of the filter in the positive feedback network, then constructing the external reset input to duplicate PIDPlus.
When PIDPlus capability is constructed in a legacy control system, the way the operator interacts with the PID is not affected. However, from a maintenance standpoint, it is necessary to provide training on the impact of the PID modifications for PIDPlus: The calculation added to provide PIDPlus capability can be implemented in various ways depending on the legacy control system's toolset for implementing calculations.
For more information on control using wireless transmitters, see Chapter 5 of the book, Wireless Control Foundation – Continuous and Discrete Control for the Process Industry. Workshops contained in the book are used to highlight key points. YouTube videos showing workshop solutions can be viewed at the book's web site (www.wirelesscontrolfoundation.com). The book may be purchased through the ISA web site and on Amazon.
- Blevins, T. “Improving PID Control with Unreliable Communications” Proceedings of ISA EXPO Technical Conference Houston, 2006.
- Blevins, T. “PID Advances in Industrial Control” Proceedings of IFAC Conference on Advances in PID Control PID'12 Brescia, Italy, 28–30 March 2012.
- Broadley, S., Benton, T. and Blevins, T. “WirelessHART Benefits Single-Use Disposable Bioreactor” Emerson Exchange, 2009.
- Seibert, F. “WirelessHART Successfully Handles Control” Chemical Processing vol. 74, no. 1, pp. 39–42, January 2011.
- Shinskey, F. G. “The Power of External Reset Feedback Control pp. 53–63, May 2006.
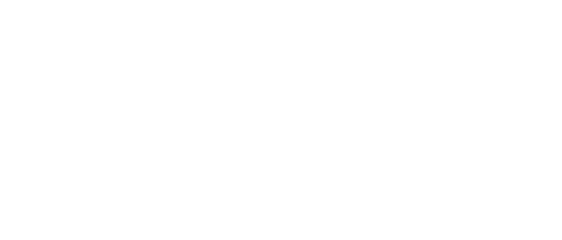
Leaders relevant to this article: