ExxonMobil commits to thinking differently with electrical integration, configurable I/O
[embed width="80" height="90" class="left" thumbnail="http://www.controldesign.com/assets/images/voices/bacidore.jpg?r=77800"]http://www.controldesign.com/assets/images/voices/bacidore.jpg[/embed]Mike Bacidore is the editor in chief forĀ Control DesignĀ magazine. He is an award-winning columnist, earning a Gold Regional Award and a Silver National Award from the American Society of Business Publication Editors. Email him atĀ [email protected].
āIn the old days, we would improve processes incrementally and consistently. Itās a lot more complicated than that now,ā explained Sandy Vasser, I&E manager at ExxonMobil. He spoke at Schneider Electricās CONNECT 2016 user group event this week in New Orleans. Vasser has led a charge to change the way his organization acts by changing the way it thinks.
āWe had to challenge our traditional automation practices and technologies,ā he said. āWe really had to think completely differently and put the old practices to the side.ā
Vasser also stressed the importance of not waiting. āThe oil and gas industry is currently at a low point in terms of number of projects, but this lull wonāt last forever,ā Vasser said. Further, all disciplinesānot just automationācan make these changes. They translate well to other disciplines within the organization.
Because thatās how weāve always done it
What prompted ExxonMobil to start thinking and doing things differently? Historical challenges were many. āThere were numerous dependencies on other disciplines, and this forces sequential execution,ā said Vasser. āDesign input was provided throughout the project lifecycle, and this forces numerous changes. The resulting designs are highly engineered, which makes them very customized and frequently changing.ā
āWe had to challenge our traditional automation practices and technologies.ā ExxonMobilās Sandy Vasser on the companyās move to re-examine decades-old project execution practices.
To reduce customization and rely more on standard solutions, ExxonMobil has pushed customization to the software, which allowed it to use standard hardware. This eliminated the need for custom project specifications and for the infrastructure to support customized solutions.By reducing complexity and simplifying designs, it reduced the component count and the number of divergent systems, taking advantage of the capability of the installed systems. It simplified interfaces; it automated and sometimes eliminated processes; and it mitigated the effects of dependencies. āIntelligent I/O has allowed us to progress the hardware design without even knowing how the I/O will be used,ā said Vasser.
ExxonMobil reduced the amount of documentation or often generated it automatically. It accepted managed risk and compromise, as it developed and enabled trust with suppliers and contractors.
āAll of this has resulted in fewer components, reduced engineering, fewer drawings, reduced number of design reviews, elimination of FATs [factory acceptance tests], shortened schedules, smaller project teams, higher quality and lower costs,ā explained Vasser.
Configure this
Smart, configurable I/O in standard field junction boxes is one of the key enablers that Vasser cited. Virtualization, not just of computers, but complete hardware virtualization has allowed the company to validate control system logic independent of system hardware.
āWhen we can test out all of our graphics and our alarms, thatās a significant improvement,ā said Vasser. āCustomization has been pushed from hardware to software. Cabinets, for example, were all different. But today all of our cabinets are a standard solution.ā
ExxonMobil also is seamlessly integrating its automation and electrical systems. āWeāve combined them, and itās all included in the automation systems,ā explained Vasser. Instruments are automatically detected, interrogated, configured, enabled and documented (DICED).
āWeāve used smart I/O to replace MCC [motor control center] wiring, simplified package PLC [programmable logic controller] interface solutions and increased use of dc power distribution. The smart I/O has allowed us to eliminate 60-70% of cabinet wiring; weāre getting rid of a lot of hard wiring between the packages and the MCCs. Electrical control interface improvements include monitoring of the electrical system. Weāre always looking at ways to take advantage of smart I/O.ā
Age in place
One of the important new opportunities, or challenges, depending on your perspective, that updated control systems bring is the concept of āaging in place,ā where the infrastructure allows for upgrades as the system ages or technology changes.
ExxonMobil has embraced this by making system architectures simpler. āSystems consist of building blocks that can be easily upgraded to current technologies,ā explained Vasser. āUpgrades or repairs will not be intrusive, disruptive or unnecessarily costly, and rip-and-replace will never be necessary. Control system selection for a facility is for life.ā
As connectivity concerns become more prevalent, ExxonMobil has adopted cybersecurity by design. āSecurity canāt be solved only by rings of protection, such as firewalls, or by reactionary measures such as virus protections,ā he said.
āWe started with how to deal with change,ā explained Vasser. āThere are many opportunities to eliminate or streamline processes. Think about what youāre trying to achieve, and think differently about how youāre going to achieve those things.ā
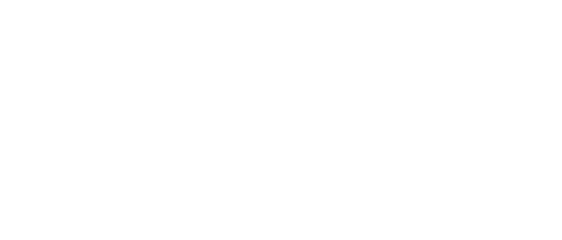
Leaders relevant to this article: