Technology is an instrument of change. It can be disruptive, enabling, subtle or timely, but recent technological leaps have affected not just research and development (R&D), but the way companies think about R&D in industries as diverse as power, mining, automation and oil & gas.
In a roundtable discussion at ABB Customer World in Houston this week, several technology officers shared their fears and their triumphs in the face of the continuing waves of technology advances.
“In the utility sector, we’re facing some huge changes with how we’re producing and using energy as a society,” said Terry Oliver, chief technology innovation officer at Bonneville Power Administation (BPA). “Electricity used to flow one way in the system. Now customers have photovoltaic systems, and we’re seeing two-way flows on systems that were designed for one-way flows.” To monitor the quality of these new power flows, BPA is using a technology developed in the 19th century to look at the grid 60 times a second—a significant adjustment to a technology that was used once every two seconds when first introduced.
Luiz Mello is technology innovation director at Vale, a $26 billion global mining company. Vale is a large producer in iron ore and nickel, with the bulk of its mining operations in South America and the largest segment of its product destination being Southeast Asia. “I was brought to Vale to bring a new perspective to structure its corporate R&D function,” explained Mello. “Despite being a global company in more than 30 countries, there’s a lot of focus on Brazil, where the educational level is similar to the United States’ in 1910. We try to foster connections with academia. We created ambitious programs in Brazil and Mozambique, as we need to hire people in these areas.”
Vale’s primary investment focus has been on creating an autonomous mine. “Mining has a geographical constraint, by nature of where the ore body sits, which is usually in remote countries where the education level is not very high. Getting a job at the mine requires a skillset that the people there do not have, so they must be trained.”
Although Ahmed Hashmi’s job title at BP is head of upstream technology, he thinks of himself as a business leader responsible for driving change. “I’ve been with BP 30 years on,” he said. “Oil prices dropped in half in 2014, and we are still not making money at today’s prices, but things have improved a lot. There’s a desire within the industry to reset itself, whether you’re talking about extraction, refining, logistics or labor costs.” Everything in oil & gas is being reset, he emphasized.
“People talk a lot about change through digitalization,” added Hashmi. “Digitalization is not something new. But software development is still too slow. If we can automate software development, then we’d have something.” Still, digitalization has compressed development time. When gas was recently discovered in Egypt’s Nile Delta, it took only two years for BP to be up and running. “It used to take seven to 10 years for that,” said Hashmi.
“The time from concept to introducing a product is getting shorter: fail fast and fail cheap,” agreed Bazmi Husain, CTO, ABB. “In the 36 years I’ve had with the company, I can’t recall another time when business impact, energy efficiency and technology have changed more quickly than today. Last year, there was more renewable energy coming on line than there was conventional energy coming on line. The ecosystem of how we do things is changing.”
All that stays the same
“When we develop something today, it comes out of the factory with a digital twin.” BP’s Ahmed Hashmi explained how technology has changed the oil and gas business at ABB Customer World this week in Houston.
In the electric power industry, the change in consumer behavior is causing utility executives to shake with fear, said BPA’s Oliver. “If you don’t need capital infrastructure and your loads are changing, you have to change your business model,” he explained. “Our tradition has been to think of least cost as the way of keeping things going. But now we need to look at what we’re doing in terms of a value proposition.”
A lot of improvements in products used to be in hardware, explained ABB’s Husain. “Going forward the differentiator is going to be more in the software aspects,” he said. “Your motor will be more reliable because you’re measuring its operating conditions, and you’ll be able to predict whether it can take a higher load or be able to predict failure before it even shows physical signs. The connectivity and digitalization are already there, and the sensing will continue to advance.”
The differentiation between hardware and software will become more outcome-based, predicted BP’s Hashmi. “It’s not hardware versus software. It’s based more on the outcome. In the past, the biggest problem with changing software was there were new forms that you couldn’t connect to the logic. Now you don’t have to program all the way down to your data structure. You have cloud platforms and new data structures.”
What shall we build today?
Vale’s recently completed Brazilian mine was a huge capital project, costing $14.5 billion, and digitalization played a huge role. “All of the processing units were built and then brought to the site afterward,” said Mello. “It’s a huge LEGO project, and you need to make sure everything will fit. Visualization was critical on that, and it brought up some faults in the design, which were fixed before construction. Drones with sensors can collect data on the facades, and we combined that with geological data for a much better plan.”
The oil and gas industry has seen multiple waves of technology, and the digital twin has risen to the surface. “Automation isn’t necessarily nirvana,” warned BP’s Hashmi. “Insight matters more than automation, and that leads to better decisions sooner. Artificial intelligence and machine learning have been around for a long time. We have a lot of stuff that has been created in a different era. But, when we develop something today, it comes out of the factory with a digital twin. Before you do anything to an asset, you do it to the digital form.”
How to get it done
Digitalization’s benefits are documented, but the challenge often is in navigating the culture change. For BPA, it was all in the framework. “We asked, ‘What do we want to be when we grow up?’” said Oliver. “We asked managers and middle executives, and then we found out what was in the way. That helped us to focus our research investment on stuff that matters to BPA. You can get carried away with engineering curiosity.”
There’s often a disconnect between corporate and operations, explained Vale’s Mello. “Diminishing that disconnect was critical for us,” he said. In the first year of an innovation initiative, Vale employees generated 7,000 new ideas. “And some of them had patent possibilities,” said Mello. A slightly overzealous management team was so pleased that it pressed harder the following year and received 22,000 new ideas. “That was just not manageable,” explained Mello.
“More things can go wrong than can go right,” BP’s Hashmi. “If I don’t understand the business ahead of technology, then I’m not doing my job. There are things we think we should be doing that will change the business in the future, but the business isn’t asking for them now. You have to balance the times. Not everything can be long-term. You have to bring results every day, and then you earn the right to do the long-term stuff.”
For Vale, training and educating future employees is half of the battle, but replacing certain tasks with automation is equally effective. “We do not believe people in Brazil and Mozambique are getting the proper training,” said Mello. “But we’re also aiming to get a complete fleet of autonomous trucks. We’re partnering with nearby schools to get the people trained. While there is a perspective of jobs lost from a given community, startups may emerge and provide software solutions that live together with diminished job opportunities in the mines themselves.”
Mechanized automation has been impacting the labor force since the first industrial revolution, added Hashmi. “As you work on lower-level stuff that doesn’t require a basic understanding of the mechanism in place, your job will get automated out at some point,” he said. “That’s true of anything in the world. If you look at unemployment today, it’s almost zero if you have a high level of education. It behooves us to invest in that.”
Husain agreed. “The jobs that robots take today are dirty, dull and dangerous,” he said. “The cage around the robot is not to keep the robot in. It’s to keep the people out. We might have to get used to going to school several times in our lifetime.”
Download the full report from ABB Customer World 2017
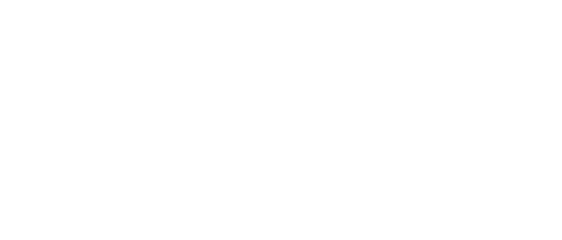
Leaders relevant to this article: