Batch processes pose particular challenges for closed-loop control and optimization due to inherent process nonlinearity and non-self-regulation. At the same time there is a greater potential for increasing capacity in batch than in continuous processes. Solutions need to address the interrelationship between yield, capacity, quality, and repeatability. Here are opportunities and techniques for getting the most out of your batch.
Overview
Batch composition, pH, pressure, and temperature control can be approximated as integrating processes and integrating tuning rules used. The setpoint response of control loops (e.g. temperature, pH, and pressure) is important in batch operations. For fed-batch operations, feed rates can be optimized to meet batch performance objectives, such as yield, quality, repeatability and/or capacity. For traditional batch operations, sequences are automated and the timing and charges are optimized to achieve batch objectives.
For high value small volume products, such as biologics, the quality is critical. The product quality that involves complex folding of the protein is difficult to measure and correlate. Repeatability is important for all batches particularly for pharmaceutical and for food and beverage processes. Large blend volumes downstream of the batch operation may make these requirements less stringent on a batch to batch basis. For mature higher volume products, yield and capacity takes on a greater emphasis.
Yield, capacity, quality and repeatability are interrelated. Variability affects all of these metrics and the solutions to improve one metric have benefits that extend to the other metrics. Often batches are held longer than necessary due to the concern about variability. Interruptions in the execution of the batch logic and the dependence upon operations to resolve problems directly affects batch cycle time and repeatability.
If all interruptions and manual actions have been eliminated by automation, most of the remaining sources of variability can be traced to variability in the composition and mass totals of components added to the batch and deficiencies in the control system components, strategy, implementation, and tuning.
For chemical processes, the totals of each component added must be accurately set and achieved. Coriolis meters can be used to measure the concentration of a key component in the feed stream via an extremely precise density measurement and to provide the ultimate in feed totalization by an exceptionally accurate mass flow measurement. For reactions, achieving the right stoichiometric ratio and best temperature are critical. If the concentration of just one component is deficient, the other components remain unreacted.
The presence of trace components in the raw materials can inhibit conversion and cause product quality problems. Raw material storage should have at-line analyzers if feasible. If laboratory analysis must be used, the time from when the sample taken to the result in entered into the control system must be fast enough to compensate for the effect in an existing batch and correct the feed for the next batch.
For pharmaceuticals the principal source of variability are the cells (incredibly complex microscopic reactors) and the magical mixture of nutrients. For fermentation processes, the variability is in the composition and processing of the grains (e.g., fermentability) and in the recycle streams (e.g., backset for ethanol). Analyzers of the feeds can provide an opportunity for an immediate adjustment in feed rate to the unit operations for processing of the feeds (e.g., slurry tanks for ethanol) and the feed totals to the fermenters.
Multivariate statistical process control better known as data analytics can be a particularly effective tool for tracking down the source of variability in batch operations and making mid batch corrections. The current batch is compared to an average batch. Principal Component Analysis (PCA) can tell you if anything in the current batch has changed. Drilling down into the PCA can give the contribution of each batch measurement to the variability observed. PCA along with a process understanding can be used trace abnormal batches back to equipment and automation system problems. The PCA is also employed in Projection to Latent Structures also known as Partial Least Squares (PLS) to predict key compositions at various points in the batch cycle. Often a correction at the mid batch point provides enough time to achieve a better endpoint.
The PLS predictions of endpoint do a piecewise linearization of the batch process conditions and can thus handle the process nonlinearity inherent in batch processes. Unlike in the use of PLS for continuous processes, delays do not need to be inserted on the PLS inputs to synchronize with a PLS output for batch operations. In continuous processes the process time constant and transportation delay for each PLS input must be used to provide the coincident effect in the path to a downstream process variable that is the PLS output. In batch processes these time delays are not needed since the effect is on a PLS output at a given point in the batch cycle (e.g., end point).
The response of temperature for heating without cooling, pH for a single reagent (acid or base), and product composition are in one direction only. For heating without cooling the temperature, for a base reagent the pH, and for a non-reversible conversion the product concentration can only increase. Although the control valve is totally closed, temperature and pH still ramps up due to the residual heat in the jacket and reagent in the dip tube, respectively. The effect is more pronounced as the vessel volume decreases. Any integral action will cause overshoot of the setpoint from which there is no recovery. Proportional plus derivative control is needed. A smart bang-bang control to stop the process variable just short of the setpoint can minimize rise time. A translation of the temperature, pH, or composition to a batch profile slope can give a decrease as well as increase in the controlled variable enabling the use of PID or MPC for profile optimization.
Inferential measurements enable more effective monitoring and automation of batch processes. The measurements can be representative of the rate of product formation or in the case of biological processes, cell growth and death rate.
The cooling rate in chemical processes offers an inferential measurement of an exothermic reaction rate or crystallization rate. The totalized cooling rate can be an indicator of total conversion. Cooling rate can be computed by the temperature difference between jacket or coil inlet and output temperatures multiplied by the flow through the jacket or coil. The inlet temperature is passed through a dead time block to mimic the transportation delay to synchronize the inlet with the outlet temperature.
The oxygen uptake rate (OUR) in bioreactor can be computed as the oxygen flow from air or oxygen spargers minus the overhead vapor oxygen concentration measured by a mass spectrometer multiplied by the vapor flow. For tight dissolved oxygen control, the oxygen flow may be representative enough of changes in oxygen demand. The OUR offers an inferential measurement of cell growth rate assuming oxygen uptake for cell maintenance and product formation are negligible.
In ethanol and wine production, the carbon dioxide production rate (CPR) in a fermenter can be computed as the overhead vapor oxygen concentration measured by a mass spectrometer multiplied by the vapor flow. The CPR in fermenters can also be computed as the loss in weight measured by load cells. The CPR gives an inferential measurement of yeast growth rate and alcohol production rate.
A dielectric probe and spectrum analyzer can provide an inferential measurement of cell volume, size, and membrane integrity (cell viability). The rate of change of this measurement can be used as an inferential measurement of cell growth or death rate (e.g. cell membrane rupture).
A sudden increase in conductivity may signal the end of chlorination processes. Similarly, a sudden change in pH may indicate the completion of a reaction where a reagent is being consumed.
When a batch composition or temperature profile is measured but not controlled, a decrease in the slope of the process variable is indicative of the end of a conversion processes. If the profile is controlled, a decrease in the slope of the manipulated variable (e.g. feed or cooling rate) is indicative of an end point being reached.
The computation of the rate of change of a process or manipulated variable is useful in providing batch profile slopes, inferential measurements, and future values for the intelligent scheduling of PID outputs and detection of batch end points. If the variable is passed through a dead time block equal to the process dead time, the signal to noise ratio is improved and the computation of the future value and rate of change is simple and immediate (new results for every update of the process or manipulated variable). The block input (new value) minus the block output (old variable) gives the change in variable in one dead time (delta variable). If you add the block input to this delta variable, you have a value of the variable one dead time into the future. If you divide the delta variable by the dead time you have the rate of change of the variable. If you want to compute a future value more than one dead time into the future you can multiply this result by the desired time interval into the future. If you want to increase the signal to noise ratio, you can set the block dead time to be greater than the actual process dead time.
Valve position control (VPC) and override control has been effectively used to push fed-batch feed rates to the maximum controllable throttle position for jacket and overhead condenser coolant valves and overhead vapor valves. The lowest output of the VPC for each valve pushed to the throttling limit is selected as the setpoint of the lead feed flow rate controller. Override controllers on process variables can prevent violation of process constraints such as high level from bubbles, density changes, and higher batch volumes.
RecommendationsĀ
-
Use Coriolis meters on liquid feeds for precise concentration control and extremely accurate component totalization.
-
Analyze raw materials for trace components that could affect conversion time or product quality and take compensatory actions.
-
Make unit operations such as filling, heating, and pressurization as simultaneous as possible to reduce batch cycle time.
-
Automate all manual actions by operations.
-
Eliminate wait and hold times by proceeding without manual operator or lab data entry or approval by using inferential measurements and online data analytics.
-
Reduce failure expression activation and automate failure expression recovery in batch manager software.
-
Use data analytics to monitor batch repeatability and predict endpoints.
-
Use integrating process tuning rules for primary batch composition, pH, pressure, and temperature PID controllers.
-
For unidirectional (single ended) process responses where process variable can only go in one direction (e.g. heating with no cooling), use a proportional derivative controller (no integral) or translate process variable to be the slope of the desired profile.Ā
-
To control the slope of the batch profile and eliminate the one direction response setpoint overshoot, use the rate of change of the key batch process variable as the controlled variable.
-
Optimize the setpoint response for overshoot and rise time by the choice of structure and the use of setpoint lead-lag and the scheduling of PID output and PID tuning.
-
Compute the rate of change of a process variable or manipulated variable for indicators and controllers, respectively to predict and detect the completion of batch phases.
-
Compute inferential measurements of conversion such as cooling rate and total for chemical reactors and crystallizers, oxygen uptake rate and total for bioreactors, and carbon dioxide production rate and total for fermenters.
-
To compute the rate of change or future value of a process or manipulated variable, use a dead time block to improve signal to noise ratio and immediacy.
-
Optimize feed rates based on raw material and batch composition analysis.
-
Use the enhanced PID for batch composition control with at-line or offline analyzers, for stopping limit cycles from deadband, and resolution limits, and to enable direction move suppression for split range point discontinuities and valve position control.
-
Use valve position control and override control to maximize fed-batch feed rate.
-
Use a virtual plant to explore and develop opportunities.
For more on batch optimization see the Sept 2012 Control article "Get the Most Out of Your Batch"
Latest from Home
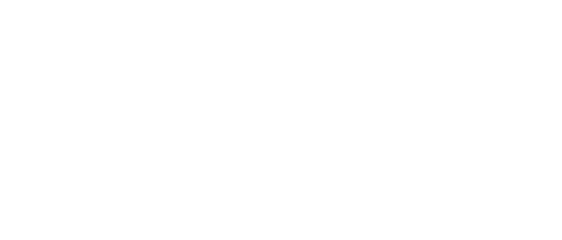
Leaders relevant to this article: