Process manufacturers must achieve stable and profitable operations in the face of a business environment characterized by a high degree of volatility, uncertainty, complexity and ambiguity. To meet these challenges, companies are embracing a plethora of established and emerging digital technologies to significantly transform operations, control costs, reduce downtime and improve profits.
Not only does digitalization improve efficiencies, it also allows companies to develop new production, operations and distribution capabilities. From an organizational perspective, the application of advanced intelligence and cognitive technologies enables digital transformation initiatives to support adaptive and dynamic responses to changes in demand, product customization, high product quality and real-time self-optimization of production processes.
Ideally, these technologies will allow devices, equipment, businesses and production systemsāor even an entire plantāto operate autonomously.
Autonomous operations
For the past several years, industry and commercial sectors have been moving toward autonomous systems. This is evident by the significant progress in areas such as robotics, discrete manufacturing, self-driving cars, autonomous vehicles in mining and offshore/subsea operations, personal assistants and other applications.
Autonomous cars are characterized by five levels of autonomy. Level 0 refers to conventional cars where a driver has complete responsibility of driving the vehicle. In Levels 1 and 2, the car assists the operator with some tasks, but the driver is still the primary operator, and must take total control for any safety-related functions. In Level 3, the vehicle monitors and controls itself using advanced sensors to detect dynamic external conditions, and it uses predictive algorithms for adaptive control and safety purposes. However, there's still a need for a human driver to take control in case of an emergency. In Level 4, the car is capable of completely driving itself, and informs the driver when it's safe to operate in this mode. Level 5 is completely autonomous, and requires no human intervention during driving.
Automation to autonomy
The process industries have significantly benefited from industrial automation, and will benefit even more with industrial autonomy. The change is happening slowly, but its pace will pick up rapidly with the advancement of enabling technologies like artificial intelligence (AI), machine and deep learning, cloud and edge computing, wireless sensors, and improved communications and networking.
Assets and operations will have human-like learning and adaptive capabilities, allowing responses without operator interaction to situations within a secure, bounded domain.
Autonomy is different from automation in many subtle ways. Automation performs a sequence of highly structured preprogrammed tasks, each of which require human oversight and intervention. The sequence of tasks could take minutes, hours or even longerāas is the case with steady-state continuous operations. However, in-between these tasks humans must perform tasks as well, and they're ultimately responsible for the safe, timely and profitable completion of the operation. For example, an operator could be responsible for safely starting up a unit, or for making crude switches or grade changes.
Autonomy goes beyond automation by adding layers of smart sensing and machine cognition to anticipate and adapt to unforeseen circumstances, removing the need for human intervention. In a fully autonomous operation, the system is responsible for all aspects of the operationāfrom startup to shut downāincluding safety.
In the near future, there will be several mixed states or levels of autonomy, and plant personnel will need to be part of operations to work and interact with industrial automation and autonomous systems. Their roles will change as they take on higher value-added activities.
Levels of autonomy
Similar to self-driving cars, one can define levels of autonomy for an industrial plant. In autonomous levels 0 through 2, operators are the lead actors responsible for control, and are assisted by autonomous systems. In autonomous levels 3 and 4, the autonomous system plays a more leading role, and is assisted by humans, while Level 5 requires no human intervention.
Autonomy will permeate process plants in multiple functional domains, including process operations, planning and scheduling, engineering, field operations, maintenance and engineering. For field operations this means going from low levels of autonomy, where field operations are done by humans, to mid-level autonomy, where the system identifies and guides operators on what to do, and provides instruction on how to accomplish the task. Further autonomy requires converting manual tasks to fully automated tasks, where human action is only required by exception.
Level 5 field operation autonomy requires no human interaction. For field operations and maintenance, robots will play a key role by taking over routine operator rounds and sample collection, as well as monitoring, inspection and surveillance tasks.
Path to autonomy
The process industries are moving closer to autonomy than ever before. Many operating companies are making an effort to āde-manā and achieve unmanned remote operations. This is particularly true for highly complex, remote and hazardous facilities. The reasons are simple: reducing costs, improving potentially adverse effects to environmentally sensitive areas, alleviating the difficulty of attracting people to operate facilities onsite, removing people from remote or unsafe situations, and improving management of dispersed assets with centralized and remote or scarce resources. Many steps necessary to achieve remote operations are also needed to achieve autonomy, including:
- Converting manually operated equipment to fully automated;
- Implementing procedural automation for manual operations, including complex operations like startups and shutdowns;
- Using resilient and redundant communications, controllers and critical equipment;
- Adopting intelligent sensors to improve condition monitoring of both equipment and the process;
- Conducting remote monitoring, surveillance and inspection via robots;
- Using robotics for routine maintenance;
- Applying predictive and prescriptive maintenance using analytics, machine learning and other AI techniques;
- Applying AI and other analytics techniques to monitor processes for impending abnormal conditions, and automatically applyingĀ corrective actions; and
- Using rigorous modeling techniques to create digital twins.
There are several other ways for companies to adopt industrial autonomy. One way is to build greenfield autonomous plants, and another is to deploy autonomous technologies in existing plants to make entire units or areas operate autonomously. This could be in the form of an AI algorithm learning to manipulate and control process variables by opening or closing valves, for instance, or it could involve combining procedural automation and AI to perform even more complex tasks.
Not only can production processes be made autonomous, but so can higher-level functions. Autonomy could expand beyond its traditional controls and efficiency focus to include safety, reliability, margin optimization, compliance, supply-chain management and other manufacturing operations and functions.
Final thoughts
In my discussions on this topic with major players in the oil and gas industry, the response is universal: āWe need industrial autonomy, and we need it sooner rather than later.ā
These demands are driven by anticipated benefits, and this input leads me to believe industrial autonomy will be driven by end-user demand and is inevitable in the long run.
There are many benefits to achieving some level of autonomy in the process industries. More integration of automation and domain applications will provide higher levels of productivity, flexibility, efficiencies, reliability and profitability. It will reduce or eliminate human error, provide uninterrupted operations, and remove people from remote or hazardous environments.
Much of the technology and data to enable autonomy already exists. A significant portion of the data emanates from sensors in the control network, or is obtainable with wireless sensors. Various technologies, like AI, are available to process the data and add intelligence. While AI may be essential to achieve high levels of autonomy, it may not be required for low autonomy levels. For higher levels, there's a need to develop an all-encompassing architecture to integrate internal and external domains.
In the short to mid-term, completely autonomous plants will be unlikely. However, it's reasonable to expect that certain functions will be autonomous to some level based on application, needs and cost/benefit ratio. The requirements to implement these lower levels of autonomy include appropriate sensors, actuators and communication networksāalong with enabling technologies to provide intelligence. Other requirements include integrating data from a multitude of plant and business systems, and even from value-chain partners.Ā
An autonomous plant needs to perform real-time control, detect and react to abnormal conditions, detect and correct potential faults, and perform self-diagnosis. It also needs to alert, prompt and guide humans when appropriate.
The majority of companies in the process industry operate at level 2 autonomy or below. Those companies at level 3 autonomy may be in this state for a long time as technology, trust and workforce dynamics advance. In these cases, human intervention and decision-making will remain important as plant personnel learn to work alongside autonomous systems.
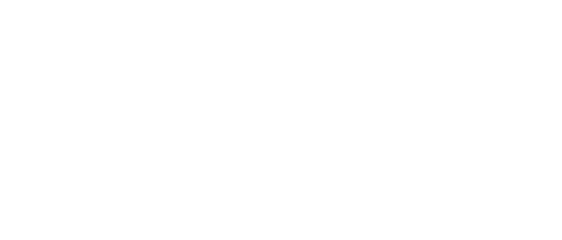
Leaders relevant to this article: