Challenge – Control Using Wireless
Since most wireless transmitters are battery-powered, minimizing how often a measurement value is sensed and communicated to reduce transmitter power consumption is desirable. However, most multi-loop controllers used in DCS systems today are designed to over-sample the measurement by a factor of 2x to 10x to avoid the restrictions of synchronizing the measurement value with the control. Also, to minimize control variation, the typical rule of thumb is that feedback control should be executed 4x to 10x times faster than the process response time, which we will define as the process time constant plus process delay. Also, the conventional PID design used in DSC controllers assumes that a new measurement value is available each execution and that control is executed on a periodic basis. The measurement update and control execution that are typically assumed in a traditional control application using wired transmitters is illustrated below.
The conventional PID design (based on difference equation, z-transform) used in DSC controllers assumes that a new measurement value is available each execution and that control is executed on a periodic basis. When the measurement is not updated on a periodic basis, the calculated reset action may not be appropriate. If control is only executed when a new measurement is communicated, this could result in a delayed control response to setpoint changes and feed-forward action on measured disturbances that occur between measurement updates. Also, as the PID execution period is increased, the basic assumptions made in the PID design of the reset and derivative calculation may no longer be valid. For example, two common ways of implementing PI control are shown below.
In many cases, the reset contribution of the PID is realized using a positive feedback network (top implementation) in which the time constant of the filter in this network defines the reset time in seconds per repeat. This approach is often taken, since it supports the implementation of external reset for use in cascade and override applications. When the reset is implemented as an integrator (bottom approach), then logic is used to avoid reset windup. However, using either approach, as the period of execution becomes significant compared to the process response time, then the approximations in the reset implementation often break down and negatively impact control performance.
It may at first appear that there is no technical solution that minimizes how often a measurement is communicated without compromising control performance. In fact, both requirements can be met using a combination of the communication capability of WirelessHART devices and a modification in the way the PID is implemented. The key to understanding how the PID must be modified is to realize that when the PID reset is implemented using a positive-feedback network (top implementation above), the filter-time constant is a direct reflection of the process dynamic response. For example, when the Lambda PID tuning rules are used, then the reset (filter-time constant) is set equal to the process time constant plus the process dead time.
WirelessHART Solution
The standard communication techniques that are supported by a WirelessHART device are defined in the HART 7 specification that has been adopted as an international standard, IEC 62591Ed. 1.0. The device may be configured to communicating new measurement values using one of five defined burst message-triggered modes. For control applications, the two communication techniques that best fit control applications are
Continuous – The device wakes up at a configured update period, senses the measurement and then communicates the value.
Window – The device wakes up at a configured update period, senses the measurement and then communicates the measurement if the specified trigger value is exceeded.
Window communication is the preferred method of communications for control applications, since for the same update period window communications will always require less power that continuous communications. When window communication is selected, a new value will be communicated only if:
- the magnitude of the difference between the new measurement value and the last communicated measurement value is greater that a specified trigger value;
- or if the time since the last communication exceeds a maximum update period.
Thus, the measurement is communicated only as often as required to allow control action to correct for unmeasured disturbances or response to setpoint changes. For windowed mode you must specify an update period, a maximum update period and a trigger value. The update period and the maximum update period are separate configured values. For best control performance process disturbances, the update period configured for window communications should be one-fourth the process response. If disturbance response is not critical, then a slower update period may be used.
To provide best control, the PID must be restructured to correctly handle continuous measurement updates that are communicated much slower than 4 times the process response time. The PID also must be able to work with the non-periodic measurement updates that are provided when window trigger mode is configured. The PIDPlus capability included in DeltaV v11 is specifically designed to address control using wireless measurements. The implementation of the PIDPlus in DeltaV v11 is shown below.
The filter output used in the positive feedback network is calculated in the following manner when a new measurement is received.
Where
FN = New filter output
FN-1 = Filter output last execution = filter output after last new measurement
ON-1 = Controller Output last execution
ΔT = Elapsed time since a new value was communicated
Control execution is set much faster than measurement update. This permits immediate action on setpoint change and update in the faceplate. PIDPlus tuning is based on the process dynamic (e.g. RESET= process time constant plus dead time); PIDPlus reset automatically compensates for variations in the measurement update rate. No change in PID tuning is required for varying update rate.
To further enhance the response for continuous changes in setpoint, the implementation of the PIDPlus may be modified as shown below.
Figure 4 – PIDPlus in DeltaV v12
This PIDPlus implementation is standard in DeltaV v12 and allows the reset calculation to automatically compensate for setpoint change and measurement update rate. When either PIDPlus implantation is used, there is no need to modify tuning as sample rate changes; i.e., reset is based strictly on the process response dynamics.
The derivative component of the PIDPlus is also modified to account for the fact that a new measurement value is not available each execution of the PID. The changes in the derivative calculation are shown below.
The derivative contribution is only updated when a new measurement becomes available. Also, the calculation is based on the elapsed time since a new value was communicated.
Control Performance Comparison
When the PIDPlus is used with a wireless transmitter in a control application, the performance will be comparable to that achieved using a wired transmitter with a wired transmitter. To demonstrate this, the module shown below was created in DeltaV that allows the control using PIDPlus using a wireless communication to be compared to the control achieved using PID and a wired transmitter.
Figure 6 - Wireless test environment
The simulated processes controlled by the PIDPlus and PID were identical and designed to use the same unmeasured disturbances. Also, using a module parameter, the setpoint value to the PID and PIDPlus can be changed at the same time. Using this capability, tests were conducted in which changes were made in the setpoint and unmeasured disturbance. The PID and PIDPlus control response is shown in the following trend.
For the test shown above, the communications window trigger mode was utilized with a maximum update period of 10 seconds and a trigger value of 1%. As shown, the control performance using wireless was comparable to that achieved using a PID and wired transmitter executing once per second. However, by using window trigger mode, the wireless communications used by the PIDPlus were 96% less than the number of new measurement values provided by the wired transmitter to the PID. The impact of non-periodic measurement updates on control performance as measured by integral of absolute error (IAE) is minimized through the use of PIDPlus for wireless communication as summarized below.
The reliability of WirelessHART device communication has been well established. Even so, in the event of loss communication, the expected control behavior is of interest. The simulation environment was used to compare the behavior of the PIDPlus for loss of communications to a PID with a wired transmitter where the measurement value is frozen for a period of time. The response observed when the measurement was lost during a setpoint change is shown below.
Figure 8 - Response for measurement loss – during recovery for a setpoint change
The response observed when the measurement is lost after a process disturbance is shown below.
Figure 9 – Response for measurement loss – during disturbance recovery
The conventional PID provides poor dynamic response when the measurement is lost. As illustrated by these tests, the PIDPlus provides improved dynamic response under these conditions.
Field Results
During the development of the PIDPlus, the control performance using WirelessHART communications was tested extensively using a simulation environment. Before this capability was incorporated in DeltaV, the performance was also verified in several field trials where the PIDPlus was used for control using WirelessHART transmitters. Two of the field trial installations were on the following processes:
- Disposable bioreactor – pH and temperature control
- Stripper Column –Column pressure, steam flow control
The performance documented at these field sites for control using the PIDPlus and WirelessHART transmitters was shown to be comparable to that achieved using wired transmitters and conventional PID for control.
Broadley James Bioreactor Control
Broadley James manufactures bioreactors and control systems (based on DeltaV) that are used in the life sciences industry. To explore the use of WirelessHART transmitters in bioreactor control, a portable Hyclone 100-liter disposable bioreactor was instrumented with a Rosemount WirelessHART gateway and transmitters for measurement and control of pH and temperature. A WirelessHART transmitter was also installed to monitor pressure. The installation is shown below.
Figure 10 – Hyclone disposable bioreactor at Broadley James
At this site, the WirelessHART pH transmitter was configured for window communication, and the temperature transmitter was configured for continuous communications. The temperature control provided by PIDPlus and the WirelessHART transmitter for a batch run using mammalian cell culture is shown below.
Very precise pH control was achieved using PIDPlus and window communications as illustrated below.
Separations Research Program, University of Texas at Austin
The Separations Research Program was established at the J.J. Pickle Research Campus in 1984. This cooperative industry/university program performs fundamental research of interest to chemical, biotechnological, petroleum refining, gas processing, pharmaceutical and food companies. CO2 removal from stack gas is a focus project for which WirelessHART transmitters were installed for pressure and steam flow control on a stripper column. A picture of the process is shown below.
Figure 13 – Stripper and absorber column at UT
Standard WirelessHART pressure and flow transmitters were installed to demonstrate and test control using WirelessHART and the PIDPlus. The control was modified to allow the operator to switch between control using WirelessHART and PIDPlus and the wired transmitters and PID. The stripper column pressure control is shown below for each manner of control.
The same dynamic control response was observed for SP changes as illustrated above. Original plant PID tuning was used for both wired and wireless control. The control performance for wireless vs. wired control is summarized in the following table.
Comparable control as measured by IAE was achieved using WirelessHART measurements and PIDPlus vs. control with wired measurements and PID. However, the number of measurement samples with WirelessHART vs. wired transmitter was reduced by a factor of 10 times for flow control and 6 times for pressure control – accounting for differences in test duration.
Conclusions
Field experience using WirelessHART in control applications may be summarized in the following manner:
- WirelessHART measurements may be used in closed-loop control applications.
– Window communications mode minimizes power consumption - PIDPlus is a standard feature of DeltaV and works with standard WirelessHART devices.
– Standard DeltaV Tools support simulation and tuning - The performance of PIDPlus in a wireless control network is comparable to PID with wired inputs.
– PIDPlus handles lost communications better than conventional PID. - PIDPlus tuning depends only upon process dynamics, not on wireless update rate.
For best control performance process disturbances, the guideline provided for update period should be observed. If disturbance response is not critical, then a slower update period may be used.
References
PID Advances in Industrial Control, IFAC Conference on Advances in PID Control PID'12, Brescia, Italy, March 28-30, 2012. http://pid12.ing.unibs.it/sp_blevins.html.
DeltaV v11 PID Enhancements for Wireless, DeltaV Whitepaper, August, 2010, http://www2.emersonprocess.com/siteadmincenter/PM%20DeltaV%20Documents/Whitepapers/WP_DeltaV%20PID%20Enhancements%20for%20Wireless.pdf.
WirelessHART Successfully Handles Control, Chemical Processing, January, 2011, http://www2.emersonprocess.com/siteadmincenter/PM%20Articles/WirelessHART%20Successfully%20Handles%20Control.pdf.
Wireless – Overcoming Challenges of PID Contro l& Analyzer Applications, InTech, July/August, 2010, http://www.isa.org/InTechTemplate.cfm?template=/ContentManagement/ContentDisplay.cfm&ContentID=83041.
PIDPlus, An Enhanced PID Control Algorithm for Wireless Automation, AS-74.3199 Wireless Automation, Aalto University, Finland, http://autsys.tkk.fi/intranet/as-0.3200/attach/S09-19/loppuraportti.pdf.
Incorporating Wireless Devices into Single-Use Disposable Bioreactor Design, 2009 Dhirubhai Ambani Life Sciences Symposium, http://www.modelingandcontrol.com/Wireless-Devices-in-Single-Use-Bioreactors.pdf.
Improving PID Control with Unreliable Communications, ISA EXPO Technical Conference, 2006, http://www.automation.com/pdf_articles/10_improving_pid.pdf.
Similarity-based Traffic Reduction to Increase Battery Life in a Wireless Process Control Network, ISA EXPO2005, Houston, TX, www.cs.utexas.edu/~sjp/publications/isa06.doc
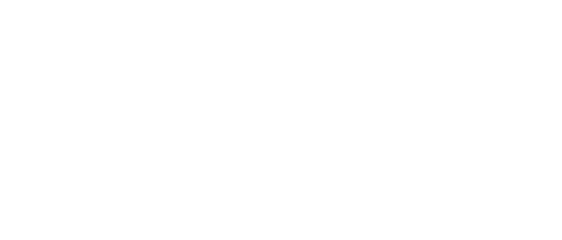
Leaders relevant to this article: