This Control Talk column appeared in the February 2018 print edition of Control. To read more Control Talk columns click here or read the Control Talk blog here.
Greg: The most common measurement is flow. Often, we use a secondary flow loop to correct for pressure disturbances and nonlinear installed flow characteristics. Good flow measurements enable ratio control, which is incredibly valuable for startup, correcting for nearly everything, including feedback correction by primary loops and getting a plant to move in concert for changing production rates. Analysis of disturbances in a tightly controlled plant is best done by looking at the changes in the flows. The fidelity of a virtual plant is best seen in how well the actual and virtual plant flows match up. If we don’t know the mass flows, we don’t know our process.
The co-founder of the ISA Mentor Program, Hunter Vegas, gives us considerable insight as to what flow measurements can and cannot do. Since this is such a vast topic, we focus on liquid flow.
Stan: How did you gain your knowledge?
Hunter: Sizing and selection of instrumentation is becoming a dying art. The subject is almost never taught in schools, and suppliers may not know or appreciate all of your plant operating conditions and requirements that determine the lowest lifecycle cost. Like most veterans in the automation industry, I learned at the knee of several very patient mentors when I was starting out, but even the opportunity to learn from more experienced engineers is vanishing as the older generation retires and large plant engineering groups are disbanded. All I can offer right now are articles like this to help young engineers understand the selection process. One thing to realize right off the bat is that the pipe must be full of liquid for all of the meters discussed.
Greg: How do you choose the right flowmeter for a process liquid flow application?
Hunter: It is important to realize that virtually every flow instrument has its strengths and issues, and there is no “one size fits all” solution. Therefore, it is important to understand the limitations of each flow technology and choose the one best suited for your budget and process. Since space is limited in this format, we will quickly hit the good, bad, and ugly for each of the most common flow technologies (ugly being show stoppers that will usually eliminate that technology as a viable option). So cue the cowboy music, throw on your cape, pull down your hat, and let’s look at our options……
Stan: How about vortex meters?
Hunter: The vortex meter measures volumetric flow. Liquid moves past a bluff body in the middle of the flow stream and generates vortices. A sensor counts the vortices as they are shed to determine liquid velocity. Good: The meter is inexpensive to buy and install. It requires no special freeze protection (just insulated pipe). It works regardless of the fluid conductivity and has no moving parts, though polymerization can plug ports and/or affect the sensors on some vortex designs. Bad: The requirements for straight meter runs upstream and downstream are particularly long for accurate readings. The bluff body post makes a wonderful startup strainer. If a mass flow is desired, the flow must be temperature-compensated. It generally needs fairly clean fluids. The flow coefficient is affected by kinematic viscosity. The meter differential pressure (DP) drop is less than an orifice plate, but more than a magmeter. UGLY: Vortex cannot handle slurries or viscous or slow-flowing fluids. It cannot handle high vibration, pulsing flow, cavitation or entrained air. Probably the biggest issue is low flow cutoff: A vortex meter cannot read low flows, so if the flow drops below a certain value the meter will read zero.
Greg: What about magnetic flowmeters (magmeters)?
Hunter: The magmeter measures volumetric flow. Conductive liquid moves through a magnetic field and generates a voltage sensed by two small electrodes. The voltage indicates liquid velocity, which is converted to flow. Good: These meters are fairly inexpensive to buy and easy to install, requiring no special freeze protection (just insulated pipe). They have virtually no obstruction to flow and can handle slurries, thick/viscous fluids and corrosive materials since only small electrodes are exposed to the process. Only a short meter run is needed. The electrodes can tolerate some coating, but not extensive amounts. Magmeters have no moving parts, can read down to very low flow rates, and will remain accurate despite changes in density, temperature, etc. Bad: Temperature compensation and a constant composition are needed to compute mass flow. Heavy coatings can keep a meter from working. Some magmeters cannot handle a steam-out and vacuum condition because it collapses the liner. If a catalyst is injected upstream of a magmeter, the electrochemical reaction can cause erratic flow readings. If the pipe is nonconductive, grounding rings must be used. Ugly: The process liquid must have a minimum conductivity under all conditions. The meter will read nothing if conductivity is too low.
Greg: My favorite flowmeter, if the materials of construction are available and lifecycle cost is justifiable, is the Coriolis flowmeter. It is a true mass flow measurement regardless of composition. No other flowmeter can get close to its accuracy and rangeability. Installation and maintenance requirements are minimal. An incredibly accurate density measurement is inherent, and that can give a composition measurement (e.g., two major components). Some meters can provide inferential measurements of the concentration of different phases (solids and bubbles). For reactant flow measurements, that is the key to accurate control of reaction stoichiometry (mass flow ratios) to improve yield. In my dreams, I envision the dollars of lost process efficiency and capacity due to meter error and rangeability being included in lifecycle costs, making Coriolis meters much more easily justified. What is your take?
Hunter: The Coriolis meter measures mass flow. Flow moves through vibrating tubes (or a single tube). Vibration frequency determines density, vibration phase determines mass flow rate due to Coriolis effect. Good: The meter requires no special freeze protection (just insulated pipe). In fact, the entire meter can be encased in a steam jacket for materials with high freeze temperatures like sulfur. The meter works well regardless of fluid properties (e.g., conductivity, density, pressure, temperature, viscosity). There are no moving parts and it requires no special meter run. Coriolis flowmeters can read very low flows, and the flow and density readings are very accurate. They can measure liquids with some entrained air. Bad: The meter is very expensive but installation is generally not difficult. Pressure drops are higher for dual tubes than for single tubes, and will always be higher than a magmeter. Single-tube meters pose minimum flow obstruction, but they are usually much longer than a bent, dual-tube meter. Ugly: Coriolis meters are not an option if you are on a low budget.
Stan: What about differential pressure (DP) orifice flowmeters?
Hunter: The DP orifice meter measures volumetric flow. Liquid moves through a restriction orifice in a pipe and creates a differential pressure (DP) due to the Bernoulli Effect. The square root of DP is converted to volumetric flow. Good: The meter and orifice are inexpensive to buy. It works regardless of the fluid conductivity, and has no moving parts and no low-flow cut-out, however, rangeability of a DP meter, even with dual transmitters, is significantly less than a magmeter and extraordinarily less than a Coriolis meter. Rangeability is less because the signal-to-noise ratio deteriorates due to the square root relationship, and because accuracy is a percent of span rather than a percent of reading. Bad: Installation is more expensive than vortex due to the costs of impulse lines, freeze protection, etc. A long meter run is needed to read accurately. The permanent pressure drop is significant. If a mass flow is desired, the flow must be temperature-compensated, and composition must be constant for the temperature effect on density to be accurate. DP orifice generally needs fairly clean fluids, and the meter reading is based on a specified fluid density, viscosity, temperature, etc., so if the fluid properties change significantly, the reading accuracy will suffer. Ugly: DP orifice meters cannot handle slurries or processes that tend to plug the impulse tubing.
Greg: How about wedge DP flowmeters?
Hunter: The wedge DP flowmeter measures volumetric flow. Liquid moves through a wedge-type restriction in a pipe, causing a DP due to the Bernoulli Effect. The square root of DP is converted to volumetric flow. The meter usually uses capillary seals to measure DP. Good: The meter works regardless of the fluid conductivity and has no moving parts. A wedge meter can handle sticky, viscous fluids that might plug an orifice plate. Bad: A wedge meter is more expensive than an orifice meter because the transmitter usually includes two seals as well as the wedge assembly. The meter needs a fairly long meter run. The permanent pressure drop is significant. If a mass flow is desired, the flow must be temperature-compensated. The meter reading is based on a specified fluid density, viscosity, temperature, etc., so if the fluid properties change significantly, the reading accuracy will suffer. Ugly: Very high temperatures may exceed the limits of the diaphragm seals.
Stan: What about other meters?
Hunter: There are other, less common meters that can be used to measure liquid flows. Some of the more typical ones are turbine meters, positive displacement (PD) meters, and ultrasonic flowmeters, among many others. Turbine and PD meters are not used as often due to long-term wear issues with moving parts, susceptibility to damage from solids, and/or limited conditions in which they function. For custody transfer of pure, clean liquids, they can be the right choice. They can be the most economical choice as well. Nearly every pump at a gas station has a PD meter.
Greg: Often not taken into account are the rangeability limitations. Most flowmeters, except for possibly Coriolis flowmeters, have less than the published rangeability due to meter or orifice size not being ideal, or deterioration of the signal-to-noise ratio at low flow. Using valve position or variable-frequency drive (VFD) speed to provide a calculated flow to give more rangeability may not work because of the installed flow characteristics of the control valve or VFD, and dead band and resolution limits. For more on the practical limitations to rangeability, see the 10/18/2017 Control Talk blog, “Common Mistakes not Commonly Understood - Part 1.” The McGraw-Hill Process/Industrial Instruments and Controls Handbook Sixth Edition that Hunter and I are working on will have much more practical information on all types of measurements. Stay tuned—in a future column, we’ll discuss gas flowmeters.
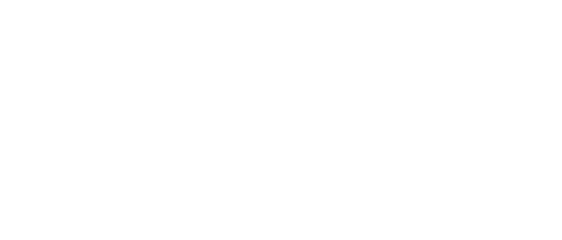
Leaders relevant to this article: