Otto Bock plant uses Profinet, smart drives for accurate liquid plastic mixing
Until the 1950s, the Otto Bock company focused on fabricatingĀ prostheses, which were still made of wood. However, evenĀ as supplies of appropriate wood became scarce, the firm wasĀ already considering more suitable materials, which turned out toĀ be synthetics such as plastics.
Founded by Mr. Otto Bock in Germany in 1919, followingĀ World War I, the company has marketed polyurethane foamĀ products and systems for more than 60 years. Otto Bock KunststoffĀ GmbH is headquartered in Duderstadt, while its NorthĀ American headquarters were established in 1958 in Minneapolis,Ā Minn. More recently, it was wholly acquired by FoamPartner/Conzzeta AGĀ based in Wolfhausen,Ā Switzerland.
Otto Bock reports its 5,000 employees focus on efficient,Ā high-quality manufacturing at all its facilities in Germany, theĀ U.S. and China. That efficiency, whether it's on the productionĀ line or in engineering design, is the primary goal, but achieving itĀ requires an integrated approach where every element contributesĀ to the greater whole.
This big-picture view was the driving force for engineering recommendationsĀ made by system integrator Process AutomationĀ Solutions (PAS) for a new Otto BockĀ plant in Rochester Mills, Mich., near Detroit. Located in Atkinson,Ā N.H., PAS is an associate member of the Control SystemĀ Integrators Association (CSIA).
Figure 1: To control the accuracy and quality of its liquid polymer blending process, Otto Bock worked with system integrator PAS to design a control system built on a foundation of Profinet and 18 smart drives from Siemens. Source: PAS
Built in 2018 next to the company's production facility, workstationsĀ at the new plant blend liquid polymers for the soft, nonflammable,Ā sound-absorbing plastic parts used inside vehiclesĀ or similar applications. The result of PAS' input was a state-of-the-art controls system built on a foundation of Profinet and 18Ā smart drives from Siemens (Figure 1)."Our thought is to always save as much money for clientsĀ as possible, though that doesn't always mean the lowest initialĀ cost," says Ingo Magura, senior project manager at PAS. "WeĀ tend to review with clients all aspects. For instance, using aĀ reputable electrical installation contractor with a history of suchĀ projects may be a better long-term fit than a subcontractor thatĀ is less expensive at first, but has no experience with control systemĀ installations."
Polymer blending process
To begin its batch process, Otto Bock receives truck deliveries ofĀ different polymers, which are transferred by automated pumpsĀ into one of four storage tanks. Operators then start one of theirĀ 20 recipes, and add different polymers in varying quantities toĀ one of three mixing tanks, which circulate and mix the raw materialsĀ before the operators manually add quantities of specialĀ additives. When a batch is approved by the quality assurance/control department (QA/QC), the final liquid polymer product isĀ automatically pumped into 1,000-kg totes, smaller storage bins,Ā or into other trucks for delivery to customers.
Tight batch process control is critical for ensuring final product quality, and requires controlling setpoints, current flow and motor speeds, as well as monitoring equipment status to detect potential faults. This process criticality helped underscore the case for using networked smart drives for Otto Bock's new control system, which would allow online diagnostics from the engineering station as well as remote accessibility.
"Exact quantities are key to this polymer blending application,Ā including the amount pumped from a storage tank into a mixingĀ tank, and also the quantity of finished product transferred intoĀ the totes before shipping," says Magura. "In this case, tight batchĀ control means speed for agitation while mixing product, so exactĀ quantities are pumped. Upgrading to automated systems fromĀ the company's former manual procedures has labor efficienciesĀ and increases accuracy."
The smart approach
Although Otto Bock originally intended to use a traditional, motor-mounted drive system, PAS calculated that using networkedĀ smart drives would significantly reduce engineering, hardwareĀ and commissioning time and costs, as well as contribute additionalĀ information needed for measuring system performance.
"In the old facility, there was an old control system by a little-known brand with limited capabilities and pretty much no support,"Ā adds Magura. "The new system is energy-efficient, automatedĀ (reducing manual intervention), allows automatic reports,Ā and is remote-accessible through a secure connection."
Control components in the polymer blending solution by PASĀ include Siemens TIA Portal v15 software, WinCC SCADA system,Ā S7-1515 CPU and remote I/O rack, as well as 18 Siemens SinamicsĀ G120 drives and two Siemens Comfort panel field HMIsāall networked with Profinet. The drives work with 460-V, 3-phaseĀ NEMA motors, ranging from 1.25 kw to 11 kW, which serve theĀ blending application's pumps and agitators (Figure 2).
Figure 2: Control components in the polymer blending solution by PAS include Siemens TIA Portal v15 software, WinCC SCADA system, S7-1515 CPU and remote I/O rack, as well as 18 Siemens Sinamics G120 drives and two Siemens Comfort panel field HMIsāall networked with ProfiNet. The drives work with 460 V, 3 ph NEMA motors, ranging from 1.25 kw to 1 kW, which serve the blending application's pumps and agitators. Source: PAS
"Having the smart drives, Profinet and the control system allowsĀ for seamless integration," says Magura, who was confident that thisĀ integrated approach would achieve the goals set for the new blendingĀ facility, and details how using smart drives networked by ProfinetĀ reduced Otto Bock's hardware and commissioning expenses.
"Since Profinet already connects all the components, commissioning time is drastically reduced compared to using traditional drives, which require that a dedicated cable be hooked up to each drive from an engineering laptop PC for commissioning," he explains. "In contrast, with smart drives connected by Profinet to the PLC, there's just one Ethernet cable, compared to eight that would have been needed if Ethernet wasn't used."
The functions of these cables include:
- Speed setpoint (4-20 mA);
- Actual speed (4-20 mA);
- Actual current (4-20 mA);
- Drive Ready (discrete input);
- Drive Enable (discrete output);
- Drive Fault (discrete input);
- Drive START (discrete output); and
- Drive STOP (discrete output).
"Since no additional hardware such as I/O cards is requiredĀ to read the actual speed of the drive/motor, this technology enhancesĀ accuracy. Plus, when you multiply these cabling and I/OĀ costs by 18 drives, it becomes evident that a smart bus systemĀ reduces both hardware and cable installation costs. The cablingĀ and I/O would have cost at least $31,000 more if hadn't wiredĀ the drives to the PLC using Profinet.
"In addition, remote access to PAS has been implementedĀ with Siemens Sinema Remote Connect system, which is secureĀ and allows us to perform software modifications or troubleshootĀ remotely. Production adjustments can be from a password-protectedĀ screen on the WinCC SCADA system."
Multiple ongoing gains
Beyond initial equipment and commissioning savings, deployingĀ smart drives and Profinet is paying ongoing dividends for bothĀ Otto Bock and PAS, according to Magura. "Profinet is deterministic,Ā so we can fine tune the control loops immediately and efficiently,"Ā he said. "In addition, we have all the measured valuesĀ from the devices at our disposal, such as hours run, which canĀ be sent from a drive to the PLC in a few mouse clicks. That's efficientĀ engineering.
"By using this fully integrated control system platform, includingĀ the drives, HMIs and Profinet, we were able to estimate ourĀ engineering costs more tightly, reduce the price to the customer,Ā and demonstrate that PAS is a more efficient solution partner."
Finally, key performance indicators (KPI) can be easily calculatedĀ using the vast amount of data now available from the company'sĀ polymer blending application. This Profinet networkedĀ system also makes it easy for users to add new KPIs by analyzingĀ data from the smart drives. These KPIs also bring further insightsĀ into Otto Bock's network and manufacturing process, andĀ are potentially critical for planning preventive maintenance andĀ future hardware upgrades.
"As for the future, Otto Bock has similar blending systems inĀ Germany and Asia," concludes Magura. "So, the goals of its U.S.Ā team apply these best practices in the other facilities."
About the author
Jeanne Schweder has written about automation technologies for more than 20 years, and has been a freelance writer for the past seven years. She can be reached at [email protected].
Latest from Industrial Networks
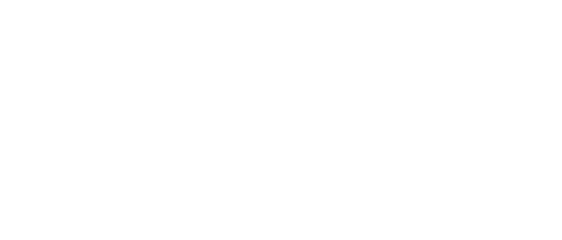
Leaders relevant to this article: