Q: The tubes in our methanol plant steam reformer ruptured because of overheating, and the investigation team recommended installation of UV flame detectors. I had bad experience with UV detectors in furnaces because they led to false alarms, trips and process disturbances. Can you please guide me on this issue?
Safdar Toor
Brega, Libya
[email protected]
This column is moderated by Béla Lipták, automation and safety consultant and editor of the Instrument and Automation Engineers' Handbook (IAEH). If you have an automation-related question for this column, write to [email protected].
A1:
Your investigation team is wrong, and your question deserves a more detailed explanation.
In steam reforming, a mixture of gases at high pressure and temperature are sent through catalyst-filled pipes, where they break down into their constituents and, depending on the catalyst used, recombine (reform) into product gases. If desulfurized hydrocarbons are mixed with steam (water), this process can be used to produce hydrogen-rich synthesis gas, methane, methanol, ammonia, etc.
This is a heat-balance process, where the heat sources are burner heads on the outside of catalyst-filled pipes, located inside refractory-walled furnaces. This heat passes through the pipe walls and heats the gases in the radiant section of the reformer furnace, reforming the gas mixture as it passes through the pipes. Under steady state conditions, the temperature of the reformed gas product leaving the furnace (TI-5 in Figure 1) is controlled constant by modulating the fuel flow to the furnace burners. Plant productivity rises with temperature, but the pipe temperature must stay below the "creep limit" of the pipe. Tube wall temperatures range from 700 °C to 1,200 °C (1,292 °F to 2,192 °F), and industry rule of thumb is that a 20 °C increase in tube wall temperature above its maximum allowable temperature will halve the tube life. So, plants maximize production by operating as close as possible to the temperature limits of the pipes without exceeding them.
The startup of these processes is slow, and speeding it up can cause accidents because, if the heat input of the pipes increases without a commensurate cooling by increased gas flow inside the pipes, overheating can occur.
Catalyst maldistribution may cause local overheating or channeling and, hence, shorter life of the reformer tubes. The catalyst should be mechanically stable under all process conditions, as well as conditions during start-up and shutdown of the reformer. In particular, resistance to conditions during upsets may become critical. Breakdown of catalyst pellets may cause partial or total blockage of some tubes.
Similarly, during the production phase, build-up of catalyst powder or coke formation on its surface can increase pressure drop through the pipe, reduce gas flow and cause overheating. The lifetime of pipes is often estimated using the Larson-Miller parameter (LMP), which predicts the lifetime of material vs. time and temperature. This parameter is usually expressed as LMP = T(C + log t), where C is a material-specific constant (often approximated as 20), t is the time in hours, and T is the temperature in Kelvins. Because reformer tubes expand when heated and because this expansion is related to the tube's temperature, overheating can theoretically be detected by measuring "tube growth." (In this answer to your question, I will not cover such—in my view—unreliable techniques.)
Catalyst protection, excess steam controls
Steam must be provided in excess of the reaction requirements to prevent the side reaction of coke formation on the catalyst. The coking of the catalyst deactivates it, and can even plug the pipe, requiring expensive replacement. To minimize coking, steam is usually supplied in a ratio of 3.5:1 by weight, relative to feed gas. Figure 1 shows the control system that maintains the excess steam at all times, since even a few seconds of interruption in the steam flow, while feed gas continues, can completely ruin the catalyst charge.
As Figure 1 also shows, feed gas flow is maintained by using a pressure-compensated flow controller (FIC-1). Pressure compensation of flow corrects the measurement for fluctuations in feed gas pressure. The steam rate is maintained by means of FRC-2, and the ratio of steam to feed gas flow is manipulated to keep the steam-hydrocarbon ratio constant.
The ratio relay (RY-2) divides the gas flow signal (FT-1) with the steam flow (FT-2). If this ratio falls below approximately 3:1, a low flow ratio alarm (LRA-2) is sounded, and if the ratio continues to fall below approximately 2.7:1, the feed gas is shut off by closing the valve (MV-1).
If there's no separate shutoff valve (HV-1), the feed valve (FV-1) must be a quick-closing valve (4 to 5 seconds for full closure), so the gas flow can be stopped almost instantly, thus protecting the reformer catalyst.
An effluent analyzer (not shown in figure) can be used to determine reaction completion by measuring the product concentration in the effluent stream. This analyzer can be either an infrared or a chromatographic type. Because of the excess steam present, water removal devices are required in the analyzer sampling system. The degree of conversion can be controlled by the furnace temperature profile, and the fuel flow to the burners can be throttled by the effluent temperature (TI-5). During plant transients, when flow rates are well below design values, reliance on standard plant instrumentation, such as in Figure 1, (controlling header or pigtail exit temperature) alone is dangerous because under low-flow conditioons, the reformer gas exit temperature doesn't indicate the temperature of the tubes.
Now, turning to your question concerming tube overheat detection in furnaces, the two most commonly used principles are based on either thermocouple (TC) or infrared (IR) technologies. These topics are too large to be discussed in this column. (They take up about 1,000 pages in the 5th edition of my handbook.) Therefore, I'll make only a few brief comments about them. I might also mention that production departments tend to use spot infrared pyrometers, while inspection departments often use portable thermal imagers.
Infrared pyrometers thermal imagers
Every object radiates IR energy, in proportion to the temperature and the emissivity of the object. Noncontact IR thermometers measure temperature by detecting the intensity of this radiated energy. The reformer imager allows measurement of the tube wall temperature profile along the full length of the reformer tube, and will allow measurement of the maximum tube wall temperature. A further benefit with the reformer imager is it provides a high-resolution image rather than a single-point measurement. It would be impractical to take the same number of measurements as the reformer imager does using point sensors. When measuring the surface temperature of reformer tubes, the main limitation of IR sensors is that the emittance of both the target and its background varies because of intervening dust, smoke, moisture and dirt. These all affect the amount of radiated IR energy received by the detector.
Gold cup IR pyrometers
Gold cup pyrometers are the most accurate contacting tube wall temperature sensors. These spot temperature detecting pyrometers measure the surface temperature of objects by simulating a blackbody condition in order to eliminate errors caused by reflected temperature sources. By using a hemispherical reflector, a measurement area is produced that is independent of emissivity.
Such a radiometric infrared borescope imaging camera is ideal for measuring the temperature of tubes of unknown emissivity. It measures temperatures from 600 to 800 °C (1,122 to 3,272 °F), and is ideal for applications with high differential temperature between the target and its surroundings. These sensors are often used as reference sensors to calibrate thermocouples or non-contact thermal imagers. They're relatively expensive, hard to manipulate and their operation requires a fair amount of training.
Thermocouples
Thermocouples are usually welded onto the tube’s surface or embedded in the tube wall, and connected to a reader or recorder. They're inexpensive point sensors. Their limitations include that, due to weld mass, they don't detect the actual tube temperature. They also drift and are difficult to shield against furnace radiation or recalibrate. Also, they don't last long in the harsh furnace environment. Daily Thermetrics' CatTracker system claims to use special thermocouple technology that can handle the harsh environment, when directly connected to the reformer tubes, overcoming these limitations.
Béla Lipták
[email protected]
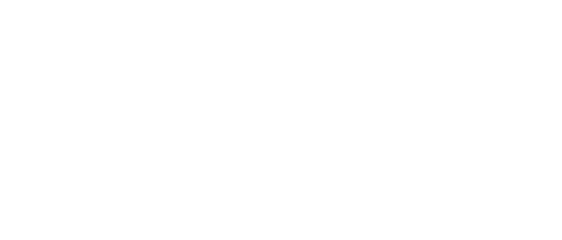
Leaders relevant to this article: