Machine safety: go digital to advance risk-assessment practices
According to the Occupational Safety and Health Administration (OSHA), some 18,000 workers are injured and another 800 workers killed each year in the United States due to contact with unguarded or inadequately guarded machinery or other equipment. Despite these large numbers, most organizations continue to assess machine- and process-related risks in traditional ways: with manual identification and management processes. Manual processes make it difficult for manufacturers to track progress, document measures and derive valuable learnings from safety data.
My colleagues at L&T Technology Services and I have had the opportunity to participate in many client discussions around machine modernization. Usually they're well-attended and involve a lot of conversation on profitability and revenue. Often left unsaid are details involving the cost of safety, usually displayed as a small statistic on a slide deep in the presentation deck.
This has proved to be one of the biggest challenges in machine modernization. How do you quantify the cost of safety? How will it affect productivity and efficiency? How will it affect business profitability? How these questions are answered affects the lives of those who work with these machines.
Machine safety risk assessments have been long employed and with fair outcomes, but not at a rate that matches technology advances.
We believe, however, that current technological innovations can augment machine safety by digitalizing risk assessment and management. With a focus on minimizing workplace health hazards, it's time to pursue a technology-first approach, ensuring airtight machine safety and risk assessment processes.
Manual preparations
While emergent technologies, such as artificial intelligence (AI) and machine learning (ML) are making rapid strides in the business spectrum and bring fresh concepts to the table, when it comes to machine safety, some initial steps must be performed manually.
Identification and observation of machines: The first step is to gain complete understanding of the worksite environment and processes, the machines in use, and the best means to safely use these machines. A thorough review of accident history, near misses and hazardous scenarios form the bedrock of machine safety. New safety parameters and directives can be implemented by using past data records to identify high-risk machines. This helps prioritize safety measures on the basis of risk quotient. It's also important to recognize the fact that, while machine designs may be similar, their application determines risk. To mitigate possible hazards, each machine must be treated individually and not as clusters.
Collection of information and identification of hazards: The next step is to identify the machines for risk assessment and gather all pertinent information about them. This information includes design details, system descriptions, energy sources, lifecycle requirements, functional limits and incident history. It's also important to list the individuals who are currently exposed or are expected to be exposed to these machines. Up next, the possible hazardous scenarios that these machines and personnel can run into must be identified. These hazards include electrical failures and shocks, nip points and pinch points, ergonomic strains, slippages, leakages and any other potential risks.
Identification and evaluation of risk levels: After identifying the hazards for the corresponding machines, the risk levels of each of those machine-hazard pairings must be ascertained. The tools and software applications used for risk level assessments must be compliant with industry standards and guidelines, and must ensure complete conformance and understanding for the assessment team.
Risk levels are identified by the function of the hazards: severity of the potential injury, possibility of exposure and avoidance of the hazard, and likelihood of occurrence. Risk estimation must be done in all scenarios. This will enable a thorough evaluation of the risk levels and hazard mitigation.
Deploying a risk-reduction system: Once risks and hazards are identified, evaluated and estimated, protective measures must be formulated to prevent accidents and reduce risks. Elimination or substitution of hazards is a time-tested method of risk reduction, and it can be done at the design stage. However, when this isn't possible and the machine is already in use, the next best option is to apply engineering controls and use ancillary devices and technologies to reduce risks. For any risk reduction system to work seamlessly, organizations must supplement with appropriate signage at the worksite, training for the workforce, and required personal protective equipment (PPE) for those at risk of exposure.
Cost estimation, follow-up assessment and closure: The risk assessment team or committee must be able to estimate the cost of final deployment, and decide whether to get it done inhouse or with the help of an external service provider. After final deployment, dry runs and follow-up assessments must be implemented to ensure the risk level has been successfully mitigated to tolerable limits. This phase also offers a fair view to identify any anomalies and correct them. After the committee or team approves the final assessment, the machine safety risk assessment process can be closed.
With technological innovations and a fast-changing digital paradigm, it's advisable that enterprises onboard the right service providers for their risk-assessment needs. To grow inhouse capabilities in emergent technologies is not only costly and time-consuming, but also runs the risk of frequent operational disruptions. For instance, when emergent technologies, such as Industrial Internet of Things (IIoT), robotic process automation and cloud computing are applied to business operations, the risks are altered. Only specialized personnel can ensure thorough risk assessment and devise appropriate protective measures.
Look to leverage cloud computing and AI
Digitally-enabled risk assessment tools help manufacturing organizations ensure business continuity by streamlining and simplifying the risk assessment process, augmenting manufacturers’ overall safety and compliance processes by reducing or eliminating incident rates. Managing safety and compliance of all machinery and equipment across sites can be a challenging process as manufacturers face a range of domain and market-specific requirements.
To accurately assess machine-related risks, manufacturing enterprises must adopt dynamic, cloud-based solutions to manage hazards at worksites. An ideal solution will be one that incorporates relevant safety standards, guidelines, safety designs and machine guards, plus safety device selection and installation with the help of a cloud-based comprehensive software, supported by engineering and data analytics. Integrating analytics with a cloud-based risk assessment tool can provide insights to managers to fine-tune safety and compliance guidelines, and effectively reduce risks across the organization. A cloud-based risk assessment solution often comes with added layers of security to guard against data breaches and cyber-crimes.
An ideal risk assessment framework should incorporate a cloud-based, secure and scalable risk assessment solution meant for global usage accessible from any computer or mobility platform over browsers. Role-based access and machine safety assessment functionalities with a rich user interface will make it user-friendly and easy to adopt. The ideal solution should have the following features:
Machine identification: All machines requiring assessment must first be identified and added to the machine list, along with facility, making/packing line, location and machine details. Users must also be provided an option to upload machine images for better reference and accessibility in both online and offline modes on mobile platforms or computers.
Compliance to standards: The solution should be compliant with global machine safety regulations as well as geo-specific requirements.
Risk assessment: The solution must offer the option to define dynamic checklists based on applicable standards, region and client-specific safety design, processes and guidelines, as well as record observations from manual assessment on site.
Hazard identification and mitigation: The solution must ensure proper identification of all hazards during assessment along with hazard images, risk evaluation and estimation, possible risk reduction measures, design recommendations and foreseeable residual risks. This assessment outcome should initiate a resultant workflow that must be integrated in the solution.
Metrics and report assessment: The solution must provide comprehensive insight into the risk assessment and machine safety processes, helping fine-tune the safety and compliance guidelines and effectively reduce risks across the organization. The solution should also provide insights on risk estimation and evaluation, helping enterprises view their risk reduction measures and mitigation decisions. Apart from this, the solution should also provide detailed risk-assessment and hazard reports.
Digital risk assessment solutions account for all environmental, health, safety and sustainability objectives and help manufacturing enterprises address these goals in an integrated way. Cloud-based risk assessment solutions driven by data analytics will also successfully identify, simulate and explore accident scenarios. This will result in extension of risk assessment into a complete framework of future resilience. Additionally, future solutions will account for robust safety and security assessment of cyber-physical systems to ensure safeguarding of data and prevent cyberattacks.
With growing acceptance of the concept of digitalized risk assessment, the scope of innovation and the breadth of solutions will both increase. As we continue our machine modernization spree with the help of disruptive technologies, we must not lose sight of the corresponding safety risks. As much as we need ROI to enable new investment, the human cost must not be ignored. New-age hazards need future-ready risk assessment methods, and digital solutions now hold the key.
Latest from Asset Management
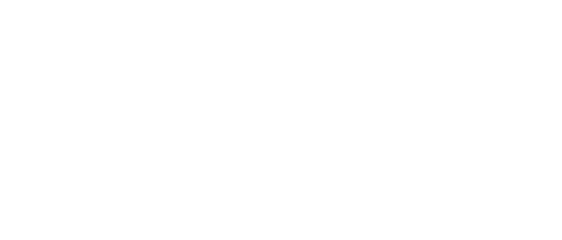
Leaders relevant to this article: