William L. Mostia, PE, Fellow, SIS-TECH Solutions, is a frequent contributor to Control.
Our list is by no means exhaustive, as many technologies are just now emerging out of their cocoons, and there's no telling what else might be lurking out there, in companies big and small, and in the garages of the DIY'ers.
Of course, the process industries are notoriously conservative, with a large installed base of equipment that ranges from pneumatic to sophisticated digital control systems, all of which are currently making money. So while we will see rapid changes in commercial technology, adaptation by the process industries will be on a value-added basis, and always dependent on the cultural acceptance of the involved personnel.
Also See: The Control Room of the Future - Smarter Reality
Current Trends Are Safe Bets
First, we can expect continued incremental improvements in our currently available control systems technology. Many of our DCS systems are underutilized, and their future may already be lurking within them or with the DCS vendor's current offerings.
Moore's Law, "the number of transistors in a dense integrated circuit doubles approximately every two years," is expected to continue into the next decade or so, but may slow from doubling every two years to doubling every three years. Coming developments in carbon nanotube field-effect transistors, junctionless transistors, single-electron transistors and memistors may well extend Moore's Law's life. So we will continue to see improvements in computing and memory, which will support the emerging technologies. We'll get larger operator screens with higher resolutions, and control hardware platforms will run faster, smarter and with more memory.
Network capacity will have to expand to meet demand, placing pressure on the existing infrastructure. Process control algorithms will advance in sophistication, but the next generation of systems will see self-aware controllers and sensors incorporating artificial intelligence (defined as capable of cognitive and memory functions, resilience, awareness of its environment and its place in the process context, etc.) to develop advanced control strategies to achieve the controller goals. Cloud computing will play a part in the next generation of DCS/SCADA, but the extent and balance between the virtual and the hardware/software world is unknown and controversial.
Control Rooms Center on the Operator
The trend of centralization of the control room remote from the process area is likely to continue, says Pierre Skonnegard of CGM in Sweden, a partner with ABB in designing the control rooms of the future. Skonnegard also felt that operator attentiveness, awareness and health would be given greater consideration.
The video arcade environment, with the operators sitting during a substantial portion of their shifts looking at video screens, can lead to operator health concerns. Chairs are being developed that will automatically adjust to the operator's physique using biometric sensing, and in the future, will be able to monitor the operator's health and attention level. DCS consoles are already available that have two positions to accommodate the operator sitting down or standing up, with an easy transition between the configurations. Biometric sensing will be used to support security, and to allow the control room to adapt to the people currently in it. Ambient intelligence, where electronic systems and environments are sensitive and responsive to the presence of people, will be given greater attention.
Displays to Expand and Collaborate
Our displays will become even larger and in some cases curved, with higher definition allowing us to display larger amounts of data with higher resolution, which we'll be able to see from farther away. We can display more than P&ID-based and physical process graphics to help operators deal with Big Data and abnormal situations by providing rapid access to information without having to navigate screens for improved situation awareness. It is reasonable to assume that operators will interact with the control system by talking (using natural language processing and Bluetooth technology), as well as hand gestures, touch and the traditional pointing device and keyboard.
Using large edgeless displays, we can now build movie theater- or wall-sized panels. For example, Saudi Aramco has installed a wall of video 67 meters (220 ft) long by 3 meters (10 ft) tall with 150 screens by Barco—in its Operation Coordination Center. It serves as a nerve center for all Saudi Aramco operations and can display all their operational data. Shades of full graphic panels!
Currently available displays embedded in tables, such as the ABB 3D KPI dashboard, have horizontal or a vertical modes of operation and can be used as collaborative workstations. Microsoft is introducing an 84-in., 4K Surface Hub with state-of-the-art digital whiteboarding that could be used as a collaborative workstation in the control room and conference rooms.
Clouds Work Better with Fog
Cloud computing refers to remote, public Internet- or private intranet-based virtual servers where application software and data may reside rather than in local computers. These applications may share resources and provide redundancy (dedicated and just-in-time). Some of this represents virtualization of local hardware, e.g., control functions in the cloud while I/O is local. Cloud computing for process control would have process control applications, other virtualized control functionality and data residing in the cloud.
Issues of privacy, security and reliability will delay the adoption of this technology, even in local clouds. Still, some cloud-based DCS products are appearing, such as the Invensys Industrial Cloud Historian, designed to deal with big data.
The cloud, in any case, will probably hold the key to the next generation of DCS/SCADA. Of interest in this area is the Architecture for Service-Oriented Process (IMC-AESOP) project (http://www.imc-aesop.eu/), whose goal is developing the next generation of SCADA/DCS systems. The plant and corporate IT side will likely adopt this long before the control people.
Our ability to store information also has risen exponentially and the cost of memory has come down tremendously. In 2004, the cost of a megabyte of storage was about $0.175; in 2014 it was $0.0085, a reduction of 95%. Moore's Law predicts that memory costs will continue to fall.
On the other hand, one of the corollaries to Parkinson's Law is, "Data expands to fill the space available for storage." Sensors are becoming more pervasive and cheaper as well smarter, offering more data. Digital bus communication will become the norm even within legacy systems. Wireless is expanding, allowing instruments to be placed in many heretofore unavailable locations, powered by batteries or by power harvested from the environment.
Figure 1. A corollary of Parkinson's Law says, "Data expands to fill the space available for storage." As sensors become cheaper and smarter, we have become data-rich, but information-poor and risk being overwhelmed by the quantity, velocity, noise and uncertainty in the data.
We cannot leave out the final elements, where increased diagnostic data has become available. Video cameras and other sources only compound the problem of overflowing data. For example, a plant with just 300 tags, each transmitting just one measurement per second, generates more than 9 billion data points in a year. For the operator, engineer, manager or control system, having all the necessary data to make decisions is great and desired, but there's no such thing as a free lunch. With this big flood of data, we have become data-rich, but information-poor, and can be easily overwhelmed by the quantity, velocity, noise and uncertainty in the data. It's a lot like the old joke about the dog that chases cars—what would he do if he caught on one? We risk putting our operations in a similar situation (Figure 1).This is where the cloud and data analytics come in. The common definition of cloud computing—using a network of remote servers hosted on the Internet—is too simple for the process industries. We are averse to using the Internet to store proprietary company information, and concerns about cybersecurity, reliability, safety and liability are big issues. Our more likely configuration resembles a cloudy day, where multiple external clouds use the public Internet, private corporate clouds use the company intranets, and local plant clouds, each providing cloud computing functions at their level, share applications, computing and memory resources as needed to provide data analytics on demand and dynamically.
Figure 2. Rather than the cloud of commercial computing, industry will prefer a set of private, corporate clouds, with a "fog" level near the local control systems and instrumentation to ensure speed, support mobility and enable local control.
In addition, as has been proposed by Flavio Bonomi, et.al., Cisco Systems, in their paper, "Fog Computing and Its Role in the Internet of Things," we need a "Fog" layer with low latency, location awareness, widespread geographical distribution, mobility, a very large number of nodes, predominant wireless access, a strong presence of streaming and real-time applications, and heterogeneity. This concept is shown in Figure 2.Data Analytics Poised to Explode
Data analytics is the science of examining or analyzing large, small and sparse quantities of raw data with the purpose of drawing conclusions, finding relationships and converting the data into useful information. Data mining is an example of this. Data predictive analytics extract information from existing large data sets to determine patterns and predict future outcomes and trends.
Data analytics will be used to take the Big Data in the fog and/or cloud and extract useful information for plant operators, engineers, supervisors and managers, as well as people at the enterprise level. Data analytics also will be used to analyze video for security and safety, in collaborative operations and in support of artificial intelligence applications and operator on-line and personal advisors.
Figure 3. Once analytics have massaged, manipulated and crunched the data, and analyzed, collated and organized the information, they must present it to the operator. Here, Honeywell's MAXPRO VMS analyzes and prioritizes video to support safety and security.
Data analytics are already available—one example is Honeywell's MAXPRO VMS for safety and security (Figure 3)—but wider use is expected when the flood of data begins to overwhelm the existing systems. Once the data analytics have massaged, manipulated and crunched the data, and analyzed, collated and organized the information, they must present it to the operator or other plant personnel using graphics and visualization tools. Processing speed will be of the essence where real-time information is required.AI beyond Siri
We've become familiar with artificial intelligence (AI) in the form of smart, virtual personal assistants (SVPAs), which entered the market in 2013. Examples include Apple's Siri and Microsoft's Cortana—software agents that can perform tasks or services for an individual. In process control, operator SVPAs will be more sophisticated, with an inherent understanding of the process, the operating context, the operating environment (using plant historical database), operator preferences and practices, data analysis, case-based reasoning and the ability to learn and remember. It is reasonable to expect that an operator can have such a mobile personal assistant, as well as more sophisticated plant digital advisors with more capability and a larger knowledge base, all connected through the local cloud or fog. IPSoft's Amelia software might serve as a prototype for such a personal assistant or plant advisor.
Artificial intelligence will be increasingly embedded in the process control world. It's currently in limited use, typically due to past failures and support issues (and support will still be an issue in the future). Some model-predictive, multivariable control may have an AI-based model or use AI and collect data to create a dynamic model. Fuzzy logic is already in use, and the future should bring self-aware sensors and control systems that automatically determine their relationship to variables and control loops, understand the effects of disturbances, be goal-orientated, spot and analyze patterns, do case-based reasoning, know the past and project the future as well as a human being.
Microsoft's HoloLens augmented-reality goggles merge the physical world with virtual reality by projecting holograms into the user's view of physical space. The holograms may be of three-dimensional objects, a virtual physical space or operator displays.
A built-in camera, computer, lenses and microphone enable the goggles to place the holograms appropriately in the operator's view of real space, and allow the operator to manipulate them via gesture, voice and gaze. Holograms also may be pinned in place so operators can move around them or through a virtual landscape.
According to Wired magazine, HoloLens will be introduced this year to developers and commercial partners, who will create applications and help Microsoft refine its design and performance. When its performance and value are proven, you might expect to start seeing it in control rooms and on the plant floor as a tool for engineering and operator interface, equipment maintenance and more.
More Help for Operators
Many people feel that the operator is the weak link in the control system, which is another way of saying the human factor is the weak link in the whole system. Warren G. Bennis (1925-2014) proposed that, "The factory of the future will have only two employees, a man and a dog. The man will be there to feed the dog. The dog will be there to keep the man from touching the equipment." It is doubtful that the role of the operator will be diminished in the near to intermediate future, as they are the primary element that provides resilience (flexibility) in the system, but a long-term trend is there.
Inexpensive computing power and memory, and advances in computing technology have made virtual reality (VR) more technically feasible. The Oculus Rift, a head-mounted VR display, so interested Facebook that it shelled out $2 billion for the company. It seems unlikely that operators will be wearing a one-pound set of goggles all day long and living in a virtual world (though the goggles have cameras that allow you to "see through" to the real world). There may be short-term activities where VR will excel, such as in collaborative efforts in engineering or with people who are in remote locations, during data visualization or interacting with virtual objects within the control system.
The next new technology is Google Glass, a form of augmented reality where a view of a physical, real-world environment is augmented by computer-generated sensory input such as text, sound, video or graphics to provide additional information. Google Glass's basic technology has been around for awhile, but the packaging and capabilities are new. It has the potential to provide operators with a continuously available heads-up display of important data and additional information on demand.
Google Glass exploded on the scene in 2012 with a large fanfare, but was recently pulled off the market. It appears that Google released it before its time to the wrong people for a stiff price and, like a turtle with problems, it has withdrawn its head back into a shell of secrecy. The Google Glass website says, "The journey doesn't end here," and has a place to sign up for updates, so stay tuned.
Microsoft recently announced its answer to Google Glass, called HoloLens, which will be bundled with Windows 10 for release to developers this year. (See sidebar.) This device has the potential to revolutionize the operator interface by providing data visualization and a collaborative operating environment for operators, engineers and corporate experts, as well as trusted third parties and vendors. It will allow engineering and maintenance to easily access system drawings, equipment manuals and specifications; to have third-party or vendor assistance in troubleshooting and repair; and to visualize design activities and perform virtual design tasks and modeling. It is unlikely that standard displays will be replaced by the HoloLens, but the technology can help operators deal with Big Data, alternate visualization of process data, virtualization, video data and collaboration.
Safety Systems to Get Proactive
- Brent Leimer, market manager, Winsted Control Room Consoles
- Pierre Skonnegard, control room designer, CGM
- Susanne Timsjo, manager, software architecture and user experience, ABB
- Bernie Anger, general manager, GE Intelligent Platforms
- Dave Cronberger, customer solutions architect, Cisco, on behalf of Industrial IP Advantage.
- Bob Voss, director, applications research, Panduit, on behalf of Industrial IP Advantage.
- Adrian Fielding, Andrew Stuart, Paul Hodge and Paul McLaughlin, Honeywell Process Systems
- Jonathan Crane, chief commercial officer, IPsof
Predictive data analytics and artificial intelligence such as expert systems and artificial neural nets (ANN) will be used to catch incipient and degraded conditions, and alert the operator to developing hazards. Systems will be able to detect degraded process equipment or operating conditions that might move a process closer to the safe operating constraint line, giving the operator an early warning. Big, small and sparse data analytics can be used to dynamically identify, online and in real time, when a system is approaching the cusp point of an incident, much like a surge controller identifies approaching the surge line.
Cybersecurity: The Killer App
New control system growth will be constrained by cybersecurity concerns. Users will expect cybersecurity to be built in, not just added on. While it will retain its reactive nature, cybersecurity will also become predictive, based on artificial intelligence, and will use data analytics, case-based reasoning, cognitive functionalities and other AI methodologies to prevent access, detect and block or eliminate intruders, learn from its mistakes and the mistakes of others, find system vulnerabilities, and eliminate or place roadblocks to intruders.
It's hard to predict the future, but it's clear that a number of emerging technologies—augmented and virtual reality, artificial intelligence, cloud and fog computing, and data and predictive analytics—are poised to change the industry.
[javascriptSnippet]
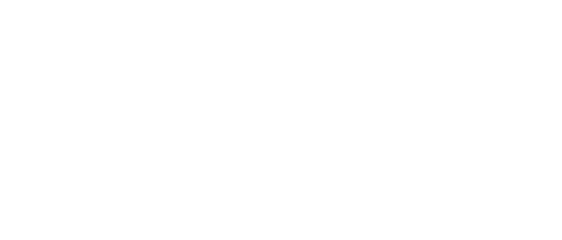
Leaders relevant to this article: