The global process industries have never been under more pressure. Plants are expected to meet new standards of safety and environmental compliance even as they are pushed to explore new operating limits. Asset utilization is connected so directly to corporate profits that planned turnarounds are ever shorter and further apart, and a single unscheduled shutdown can negate a whole year's worth of optimization effort. People and processes must operate more efficiently and productively, even as industry must bring a new generation of less experienced workers online. In the face of all this, how will the process industries continue to manage?
Tom Moser believes that instrumentation is a big part of the answer. Moser, president of the Rosemount Measurement business unit of Emerson Process Management, offers as evidence the ongoing evolution of instrumentation capabilities as well as the application revolution enabled by wireless technology. Control's Keith Larson caught up with Moser at the 2012 Emerson Global Users Exchange in Anaheim, Calif., to hear his views on how instrumentation is helping users boost plant performance across a range of important metrics. Read on for the highlights of their talk, or visit ControlGlobal.com/moser to watch the full video version of their conversation.
Q: Today's process instrumentation is capable of doing far more than just reporting back a process variable signal. What are some of the new instrumentation capabilities that Rosemount is bringing to bear on behalf of its process industry users?
A: At Emerson, we've been measuring pressure, temperature, level and flow for quite a long time. And as the industry has moved from a traditional 4-20mA signal into smart instrumentation, it started to bring in more information from those devices and we have begun to do many more things with that information, such as provide instrumentation diagnostics.
Control's Keith Larson talked with Tom Moser, president of Emerson Process Management's Rosemount Measurement business, at the 2012 Emerson Global Users Exchange in Anaheim, Calif. Watch this video interview.
Instrumentation also is being used for statistical process monitoring: measuring not just the static variable, but understanding the dynamics of the process itself. If you know you have a good pressure or temperature measurement that's well coupled to the process, the noise level of the measurement can tell you a lot. Customers are starting to find some very unique ways to apply that capability. But the foundation is still the fundamentally reliable measurement for which Rosemount products are renowned. Bring that together with fast I/O and signal processing capabilities and you can begin to capture more transients in the signal and gain a better understanding of what's happening in the process.
Q: Smart instruments are in widespread use today, yet many have been installed without the ability to continuously communicate the additional information they posses. Is the time at hand to finally put those diagnostics to work?
A: One of the early functions of smart instrument diagnostics was to quickly determine if there was a problem with the loop. Is the measurement itself okay? If the instrument can tell you that the measurement itself is good, the maintenance technician can start to move downstream, to more quickly find out the root cause of a problem. For HART-based transmitters already installed with straight analog 4-20mA wiring, our Smart Wireless THUM Adaptor provides an easy, cost effective way to extract that HART diagnostic data and send it over a wireless network.
But today, looking at applying instruments in new applications, it's really about taking the core measurement itself and allowing that to be a diagnostic for a piece of equipment. If a pressure relief valve goes off, you want to be able to find it quickly and determine what caused the release in the first place. I think that diagnostics will continue to be increasingly important, along with applications like our AMS Suite and its online monitoring to bring them forward.
Q: Over the past several years, human centered design has been a central strategic initiative across the entire Emerson Process Management organization. Can you speak to how HCD is manifesting itself in the Rosemount offering?
A: Human centered design begins with making our products easier to use, so we really started with our AMS Suite software—making sure that templates are consistent and intuitive across all of our products. Now we're starting to move that into our hardware, which means more consistency in our local displays to make configuration and startup easier to do. If a customer understands one product, they should be able to apply that knowledge to using other products of ours. We want to make the time spent on our products as efficient and productive as possible.
All of our multivariable measurement technologies also are examples of HCD at work. We're putting multiple variable measurements together into a single package, and now we're even adding the differential pressure flow element. The end result is time saved in engineering, procurement and installation effort.
Q: Instrumentation has an obvious role in safety instrumented systems (SIS), but new applications such as safety shower and pressure relief valve monitoring address entirely new aspects of safety that traditionally have not been instrumented. Can you tell me more about instrumentation's role in safety?
A: Traditional safety systems identify upsets and take the plant to a safe condition as quickly as possible. But safety in a broader sense means safety of the local environment as well as safety of workers. As we start to evolve our wireless technologies, we see customers focus on how they can reduce the number of people walking around the facility. Any time an employee is in the plant, on the wellhead, on the platform, there's the potential for a safety incident. Wireless with online monitoring is taking away some of the reasons for these trips to the plant, to help improve overall safety.
Customers are looking at ways to apply measurements in different ways to fundamentally improve the safe operation of their plants. In the case of safety shower monitoring, as soon as that safety shower is pulled, there's a message to the control room and an emergency response team is sent out. Mustering, or people tracking, is another example—you can easily and automatically know if someone has reported in during an emergency situation.
Q: Obviously, a lot more than technical functionality goes into the typical process instrumentation purchase decision. Can you speak to the new differentiators in the instrument market today?
A: While the criteria are evolving all the time, I think our customers still rely on the quality and reliability that comes with the Emerson and Rosemount brands. In addition, more customers around world are looking for more help in properly applying those technologies. There are lots of ways to measure level and lots of ways to measure flow. As new instrument engineers are coming online, and lots of expertise is retiring, there's a need for help in applying products in the best way possible. We help our customers understand the best technology for their application and how to make the most of it. That's a differentiator for us.
Further, we can bring the full solutions capability of Emerson Process Management to bear on behalf of our customers. HCD is making our products easier to use. And wireless is really opening up the whole solution space including the ability to solve entirely new problems.
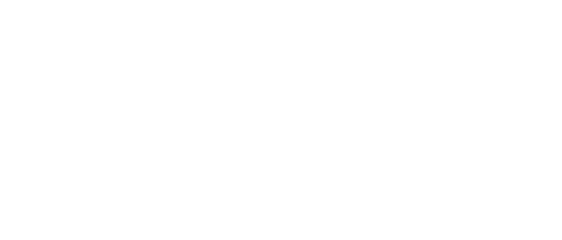
Leaders relevant to this article: