Figure 1: The surface mine at the top of the photo feeds CTC Crushing’s dry processes. The wet process at the bottom left of the photo feeds washed final product to the bulk storage piles (not shown). Source: AutomationDirect
Impact Sand and Gravel is the leading supplier of aggregate and sand in the Las Vegas area, producing and distributing millions of tons of material to construction trades each year. The company began in the 1990s by brokering sand and gravel before eventually entering the production side of the industry.
Production started with a small crusher and one gravel pit surface mine, and has since grown to four gravel pits and crushing plants (Figure 1). CTC Crushing is staffed with highly trained technical personnel, heavy machinery equipment operators, welders, electricians and mechanics.
Recently, CTC recognized the need to upgrade its crushing plants to better support custom products because reconfiguring to run different products often required time-consuming changes to the control system and extensive rewiring. To modernize and simplify control of its dry and wet plants, CTC Crushing partnered with InterConnecting Automation, an AutomationDirect system integrator, to upgrade an aging, inflexible and highly manual control system into a modern and easy-to-configure design.
Turning rocks into gravel and sand
Simply put, CTC turns big rocks into small ones. At the gravel pit, the native material is surface mined down to 50-100 ft. below grade. When mining is complete, the area often is converted into a retention basin for storm water or a sports facility.
Initially, the entire industry’s source material was native and virgin, and companies mined the material they crushed. Over recent years, a large part of the industry has transitioned to recycle by obtaining concrete and excess material and then reprocessing it. CTC operates both recycle and virgin material plants, producing aggregate for road bases and dry sand for landscaping. Washed native material, concrete sand, washed rock products and golf course materials are part of the operation, as well as concrete recycling.
Material is processed on-site. Equipment crushes the rock to a specific size and washes the sand, the resulting material is stockpiled, and eventually, trucks deliver the product to end users or brokers. As the largest rock supplier in Las Vegas, many end users purchase materials directly from CTC.
At the facility near Boulder City, Nevada, new control systems were recently installed on the crushing and washing processes, while the clarifier (water reclamation) control system upgrade is in process.
Figure 2: The dry process vertical shaft impact crusher uses twin 400 hp motors to crush 1.5-in. rock to 1/8-in. minus sand that is fed to the wet plant. Source: AutomationDirect
The dry process features a primary crusher handling material brought into the plant. This material enters the primary jaw crusher sized at 24-in. minus (all material is 24 in. diameter or less) and its output is 6-in. minus, which, in turn, feeds a secondary cone crusher to take that material down to 3/4-in., ½ in. or less depending on the crusher’s configuration. Two additional vertical shaft impact crushers are used to make sand down to 1/8-in. minus (Figure 2).
From the dry crushing application, material is conveyed to the wet process where the material is washed through auger screws (Figure 3). Transporting the material through the spinning screws with water added cleans out the mud. The muddy water is then transferred to the clarifier process to remove the mud so the water can be reclaimed and reused.
The finished product is moved by conveyors in its wet state and stockpiled, ready for delivery to the customer.
Figure 3: Wet process auger screws wash the rocks or sand with water, which is recycled through a clarifier. Source: AutomationDirect
A crushing automation history
About 20 years ago, CTC implemented a motor control center (MCC) operated by a PLC using the DeviceNet industrial communications protocol. This was a relatively new method at the time, with few installations. The system worked well and ran the entire plant, but was difficult to operate, maintain and support. An emergency stop or electrical issue might require a technician to fly out from the east coast to correct the problem.
The original control system was very difficult to troubleshoot but was used for many years. Eventually, it was running so poorly that about eight years ago, the plant moved away from automation and went back to more of a manual system. The manual system consisted of large start-stop pushbutton stations, and each of the 50 motors had its own hardwired switch.
Control remained manual for about seven years until discussions started about modernizing the processes. This included equipment on both the dry and wet sides of the process, and later the clarifier. At that time, the manual system was easy to troubleshoot and operate, but management wanted to investigate the benefit of automating with contemporary PLCs.
Plant operations personnel were initially resistant to the idea of making the system more complicated again with PLC control, but they started looking online at different options when they realized a change was required. CTC had dealt with AutomationDirect over the years as an industrial component supplier, but not as a PLC supplier. Additional research revealed their new Productivity2000 series controllers were very capable of controlling processes such as those at CTC.
CTC personnel were already equipped to install the new automation equipment, but support was needed from an outside organization for specification and programming. Further investigation on AutomationDirect’s website, specifically the section for PLC training and integration, identified Doug Bell at InterConnecting Automation as an integrator fitting the bill.
Figure 4: CTC Crushing’s electrician installed and wired the Productivity2000 controller in 15-slot racks to handle the high I/O count. Source: AutomationDirect
Processing details
In the first phase of the project for System 1, InterConnecting Automation recommended, designed and supplied a Productivity2000 PLC system for just the wet process, controlling about 20 motors. This was a test case to prove the reliability of the system, explore how user-friendly it was, and confirm CTC electricians could successfully install it in-house without needing outside resources. The System 1 PLC has 51 discrete inputs, 55 discrete outputs, four analog inputs and four analog outputs. There is an EtherNet/IP digital communications link to a VFD, and a Modbus TCP/IP communications link to 10 scales.
Plant electrician Brandon Sembrick installed and wired the Productivity2000 system, and InterConnecting Automation programmed and started it up (Figure 4). The wet process control system was then tested for four months without failure or equipment downtime.
After this wet plant test, reconfiguration of the dry side process began. A second Productivity2000 for System 2 was specified, installed, wired and programmed. This dry side process includes control of close to 70 motors, from 400 HP in the crushers down to 5 HP on a few pumps and conveyors. This control system upgrade also went well. The System 2 PLC has 51 discrete inputs, 55 discrete outputs, four analog inputs and four analog outputs.
With two PLCs controlling close to 100 motors in the plant with no problems, CTC is now moving ahead to add a third PLC to automate System 3, the clarifier portion of the plant. The System 3 PLC has nine discrete inputs, 17 discrete outputs, 24 analog inputs and one analog output.
When the final phase is complete, the entire plant will be controlled by three Productivity2000 PLC systems purchased from AutomationDirect, programmed by InterConnecting Automation and installed and wired by CTC Crushing.
In place of operator control panels with about 100 start-stop buttons and lights, there are now two AutomationDirect C-more HMIs, each with onscreen virtual buttons to start-stop all the equipment. In addition, all the controllers and HMIs communicate with each other using a plantwide Ethernet network.
The PLCs, HMIs and VFDs all have web server capability, allowing plant personnel to access these components via any browser to see data, make changes and perform other tasks. For tasks requiring a higher level of access, the automation system can be remotely and securely accessed via AutomationDirect’s StrideLinx Secure hosted VPN solution (see sidebar).
The hosted VPN solution used by CTC provides secure IIoT connectivity with simple setup and network configuration. It includes a local VPN router, a cloud-hosted VPN server and a remote VPN client. The automation system components are connected locally to the VPN router, which connects to the cloud server. The VPN client connects by laptop or PC to the cloud, and ultimately to the local automation system components (figure).
To accomplish this, the local VPN router makes a VPN connection to the cloud server immediately upon startup, but the VPN client only connects upon a verified request from the remote user. Once both connections have been made, all data passing through this VPN tunnel is secure.
This hosted VPN solution only required simple router configuration because the router is connected to a predefined cloud server. This allowed AutomationDirect to deliver the router preconfigured, so CTC only needed to add basic network information. The router’s default firewall settings keep the plant floor network separate from the corporate network.
The VPN router includes Wi-Fi and 4G LTE connectivity options in addition to a wired LAN option. The Wi-Fi option allows the router to operate in access point or client mode. With access point mode, wireless devices connected to the router are on the LAN network, allowing plant personnel to access the control system local area network (LAN) wirelessly, rather than opening the panel to access the physical LAN connection ports. With the 4G LTE option, access can be provided from remote locations without internet access, or from locations that will not provide access to their corporate network.
Security risk is minimal with this solution because the remote client connection to the cloud server uses the robust encryption standard SSL/TLS. The required TLS key exchange, crucial for security, is done in accordance with industry standard 2048-bit RSA with SHA-256.
To further enhance security, AutomationDirect provides advanced user management, event logging and two-factor authentication. This method of authentication requires a second time-based password generated at login, providing an extra level of security.
AutomationDirect’s hosted VPN solution has a free monthly bandwidth allocation for basic operation, with a premium plan offered for additional bandwidth. The free plan has proven sufficient to handle CTC’s troubleshooting and programming needs.
Rock solid control
The PLCs are controlling the system from beginning to end to bring material into the plant, control the crusher functions and speeds, operate material feed conveyors, and monitor motor amps and conveyor weights in various locations.
“The Productivity2000 was a great fit for this application,” says Nick Bell, a programmer from InterConnecting Automation who wrote the code for both the wet and dry process PLCs. “Its I/O capabilities and networking were more than sufficient, and its 15-slot base was needed considering all the I/O on each system. Another important feature was the new Productivity Network (ProNET), which added the ability to share data between Productivity series CPUs. The feature is set up in the hardware configuration window. The data updates about 10 times per second, allowing for sharing of data among the PLCs at an acceptable rate for these processes.”
Each program consists of 50 latching circuits functioning as interlocks. The use of arrays, indirect addressing and relay logic allowed configuration of the interlocks via the C-more HMI, which enabled CTC to reconfigure functional aspects of the system by filling out a chart (Figure 5).
Figure 5: A mobile tablet device displays the C-more HMI screens, adding remote monitoring capabilities to the system. Source: AutomationDirect
Control system details
The HMIs each have five to six screen pages. Two of the screens are used for control and monitoring of the dry and wet plant. A configuration screen is used to configure VFD speeds in Hertz, and another is used to monitor motor amps in the crushers and the belt weight scales by displaying tons per hour.
Discrete signals from the Productivity2000 PLCs control VFD starting and stopping, while 4-20 mA analog output signals from the PLCs provide a speed reference to the drives. Current transformers connected to 4-20 mA analog inputs on the PLC monitor the electrical current used by the large crusher motors. This motor amperage data is used to determine if more product can be fed to the crusher. If a 400 HP motor is only drawing 200 amps, it can handle more work—more rocks—and make more product, maximizing production. The Productivity2000 PLC uses Ethernet communication to monitor the weight scales.
A big concern for CTC was eliminating downtime. With that in mind, electricians installed a hand-or-auto configuration for each motor. In the unlikely event that a PLC fails, a panel of relays enables switching all the motors from PLC control (auto) to manual start-stop control, using one latching relay for every PLC output. Therefore, it is still possible to use manual motor control capabilities as a backup, but this functionality was only used while starting up the new control system and has not been needed since.
Another CTC concern was the durability and longevity of PLCs and HMIs operating in the gravel pit environment. The PLCs are installed in control panels inside conditioned 40-foot trailers and the HMIs are in a control tower. Surviving the heat and dust of a Nevada summer was a concern, but there have been no problems. There is a lot of traffic in and out, but they have worked well in this harsh environment.
The rock-bottom line
Cost savings, flexibility and simplicity are the key reasons CTC chose AutomationDirect controllers and InterConnecting Automation. The system cost considerably less than other hardware and installation options while delivering high-quality results.
Their partners’ flexibility allowed CTC to self-perform installation using in-house electricians. Experience indicated it would have cost more than $100,000 to hire an outside crew to install the system. Self-performing this work cost about $30,000, with an additional $15,000 spent on hardware, and plant personnel are now much more familiar with the entire system because they installed it themselves.
The Productivity2000 PLC made the plant very simple to operate. The integrator took a complex process and built a control and HMI scheme for it where all the motors could be named through the HMI, with interlocks assigned in any order desired. In the past, CTC had to hardwire interlocks between conveyors, and if a downstream conveyor stopped then the upstream conveyor would stop. This wiring was time-consuming and hard to change. If CTC physically changed the plant by moving conveyors and adjusting processing steps, a lot of control changes were required.
With this upgrade, CTC can now name each motor and configure its upstream and downstream interlocks. Changing the position of a conveyor on the HMI changes the order of the interlocks. This activity now takes only minutes, with no rewiring or reprogramming needed.
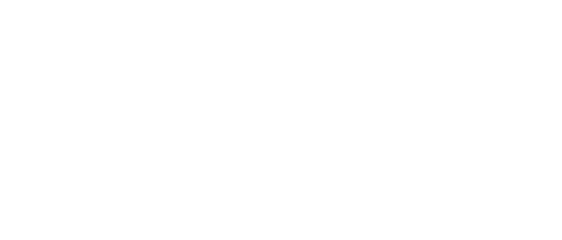
Leaders relevant to this article: