Advances in model predictive control
Terry Blevins and Willy Wojsznis are members of the Control Process Automation Hall of Fame. Blevins is principal technologist and Wojsznis is a member of the applied research team at Emerson Process Management.
Advances in processors and memory make it possible to embed MPC in the DCS. If the DCS controller supports MPC, it is possible to justify applying MPC to small processes that have historically been controlled using single-loop and multi-loop techniques. MPC may be used for the control of single input-single output (SISO), as well as MIMO processes. Also, the ability of MPC to use measurements provided by wireless transmitters provides a new level of flexibility in addressing control applications.
Embedded MPC
In its simplest form, MPC may be used to address a SISO process. For example, MPC can be used to effectively control a SISO process that is "dead-time-dominant" (process dead time is equal to or greater than the process time constant) where PID may not provide satisfactory performance (Figure 1).
The improvement is possible because the MPC algorithm is generated based on process response to a step change in process inputs (the step response model), rather than being predefined, as it is with PID. When a change is made in an input of a dead-time-dominant process, unlike the PID algorithm, the MPC algorithm is aware that this change will not be immediately reflected in the process. This allows the MPC algorithm to do a better job of controlling dead-time-dominant processes.
See also: Killing model-based control dead time
If a disturbance to a process can be measured, it may be incorporated into the MPC. In this way, MPC may be used to address applications that traditionally use a feedforward input to PID. The MPC block can automatically compensate for the disturbance and thus do a better job of maintaining the controlled parameter at setpoint. When a process output is a constraint parameter, that measurement is simply added as an input to the MPC block. The design and implementation of an override control strategy using an MPC block is thus much simpler than implementing override control using two PID blocks and a control selector block.
When a process is characterized by multiple manipulated inputs and multiple controlled outputs, there is a potential for interaction; that is, a change in one manipulated input may impact multiple controlled outputs. When the resulting interaction between control loops is significant, detuning the PID controller is the most common way to deal with it. When MPC is used, the interaction of the manipulated inputs and controlled outputs may be addressed by one MPC block (Figure 2).
Figure 2. In an interactive process where a change in one manipulated input may impact multiple controlled outputs, the common workaround is detuning the PID controller. Instead, the interaction can be addressed by a single MPC block.
Since the impact of each manipulated input parameter on each controlled output parameter is identified by the step response model used in MPC block generation, any interactions are automatically compensated for by the MPC block. Thus, each controlled parameter may be independently maintained at setpoint without interaction.
Commissioning MPC
When MPC is supported in a control system, a software application is provided to automatically identify the process step response model. Similar to the tuning applications provided to tune PID, the MPC application is designed to allow the process to be automatically tested. With the push of a Test button, the step response model is automatically identified, and the MPC algorithm is generated and transferred to the MPC block used for control.
Before initiating a test, the user may specify how much the manipulated parameter is to be changed during testing. The user must also input his or her best guess, based on observation, of how long it takes the process to fully respond to a change in the manipulated parameter—the process time to steady state. The duration of the automated test is based on the estimated time to steady state, and it also determines the maximum time duration of pulses generated during testing.
When testing is initiated, the controller output will automatically generate a series of pulses of pseudo random duration to allow the process response to be observed and collected for model identification. After testing is complete and controller generation is selected by the user, the test variations of input and output are automatically analyzed, and the step response model and MPC controller are generated.
MPC and wireless transmitters
With the rapid spread of wireless measurements in the process industry, many measurements used in MPC can be wireless. Therefore, MPC should be ready to operate with partially or completely wireless measurements. Conventional MPC is based on the process model, which can also be used in wireless MPC. The process model can estimate control parameters between measurement updates provided by wireless transmitters, and those estimates can be used by the MPC controller much like observer estimates are used in a PID controller. It follows that MPC should have a flag that directs it to use a process model simulated measurement when a wireless measurement reading is not available, and should update the model and use a new measurement when a wireless reading becomes available.
In many recent MPC designs, a similar mechanism is used to facilitate MPC operation over a predefined period of time using a simulated measurement when a wired measurement failure is indicated by analog input (AI) status Bad. The same principle of using a simulated measurement is applied for lab measurements that are available at irregular periods of time with a much slower update rate than the MPC scan rate. The user may specify the maximum time that a simulated process value may be used without a new measurement update, and the type of MPC Fail mode if this time limit is exceeded.
To enable wireless MPC operation, wireless measurement status may be used to indicate whether a new value has been communicated or the last communicated value is being held. It follows that MPC will work with wireless measurements, provided the wireless measurements status is updated in this manner. If a wireless measurement status does not change as required for MPC wireless operation, then in most cases the required status indication can be created using tools provided by the DCS.
Wireless MPC provides continuity of operation independent of irregular measurements. MPC uses a simulated or a measurement value depending on the measurement status. This allows wireless MPC to operate when the measurement scan period is significantly longer than the MPC operation scan period. It also operates well when wireless measurements are delivered at irregular intervals. Wireless MPC uses its own internal model for simulating process parameter values in periods when there is no new measurement transmitted. When a new measurement is available, the model prediction and the simulated parameter value are updated.
In one implementation, measurement status "constant" causes MPC use its own model for measurement parameter simulation. Wireless measurements therefore should develop status Constant in the periods when a new measurement is not delivered. This approach allows the application of common MPC design to wireless operation. Another advantage of this approach is the same model and controller may be used for both wired and wireless control.
For more information on control using wireless transmitters, see Chapter 5 of the book, Wireless Control Foundation – Continuous and Discrete Control for the Process Industry. Workshops contained in the book are used to highlight key points. YouTube videos showing workshop solutions can be viewed at the book’s web site. The book may be purchased through the ISA web site and on Amazon.
The divided wall column (DWC) design can provide savings in energy and capital cost compared to a conventional column design. Numerous articles have been published over the past 10 years that address the potential savings in energy and capital cost that may be achieved in some applications using the DWC design. However, very little has been published on DWC control design. Therefore, a project has been initiated by the University of Texas (UT) Separation Research Program to study and document size exclusion column (SEC) operation and control based on tests conducted using a 6-in. divided wall distillation column. The basis for base level control design is proposed by Ling and Luyben (2010) where an inferred measurement of composition is based on column temperature measurements.
The interactive nature of the DWC process presents challenges when composition control is implemented using single-loop PID. The tuning necessary to minimize loop interaction may result in slow control response. Since model predictive control accounts for process interactions, many researchers have reported that control performance achieved using MPC is better than single-loop PID. Thus, the MPC capability embedded in the DCS is incorporated into the DWC control installed at UT (Figure 4]. Since the temperature measurements on the DWC are only accessed using wireless transmitters, the MPC implementation supports control using wireless measurements.
As a starting point, a simulation of the DWC process was created to support testing of base level and MPC control. Simulation of the temperatures used in composition control allows the temperature measurements to be selected as wired or wireless. A module containing an MPC block was configured to address composition control and energy consumption (based on column temperature). Thus, the MPC block was configured to address four temperature measurements (defined as controlled parameters that could be wired or wireless):
- Distillate composition, indicated by top/stripping temperature in the column
- Side stream composition, indicated by column mid/main fractionator temperature
- Bottom composition, indicated by column bottom/rectifying temperature
- Energy consumption, indicated by pre-fractionator temperature
The column feed (defined as a disturbance parameter in the process simulation) and four manipulated parameters for composition control (PID setpoint for reflux flow, the ratio setpoints for liquid split and side stream flows, and the setpoint for bottoms steam flow) are used in the composition control.
Initial testing was conducted off-line using a dynamic simulation of the DWC process. In this environment, MPC operation using wireless temperature measurements could be compared to operation under similar conditions using wireless temperature measurements. Testing led to the following conclusions:
- Wireless MPC provides stable operation when the measurement transmission scan period is many times greater than the MPC operation scan period. Tests of wired MPC vs wireless MPC were done using wireless transmitter update rates of 8 and 16 seconds. The MPC scan period was set at 1 second.
- The integrated absolute error (IAE) for temperature setpoint changes for wireless MPC in any case does not exceed the IAE for wired MPC by more than 10%, which is an insignificant performance change.
The step response trend of wireless MPC does show small "bumps" when a new measurement value is transmitted and the process model is corrected. The bump size depends on the model accuracy and how unmeasured disturbances affected the trended process output.
Commissioning of the DWC process at UT began in early March, 2015. WirelessHART temperature transmitters used in composition control are configured for periodic update rates of 8 seconds. Control using these wireless transmitter with PIDPlus (see Control, May issue) has been commissioned the control performance is comparable to that previously achieved by other researchers using wired transmitter. Commissioning of wireless MPC is targeted for May-June, 2015 timeframe.
- Blevins, T., Roach, B, Wojsznis, W., "Wireless Model Predictive Control (MPC) for a Divided Wall Column," Emerson Exchange, 2014, Dallas, TX.
- Blevins, T, Briggs, S., Jensen, K., "Using Wireless Throttling Valves in Column Control," Emerson Exchange, 2014, Dallas, TX.
- Blevins, T., Nixon, M., Control Loop Foundation – Batch and Continuous Processes, Research Triangle Park: ISA, 2011 (ISBN: 978-1-936007-54-7).
- Cutler, C. and Ramaker, B. "Dynamic Matrix Control—A Computer Control Algorithm," Proc. Joint Automatic Control Conference, San Francisco, CA, 1980.
- Ling, H. and Luyben, W. "Temperature Control of the BTX Divided-Wall Column" Ind. Eng. Chem. Res. 49, pp.189–203, 2010.
Continue Reading
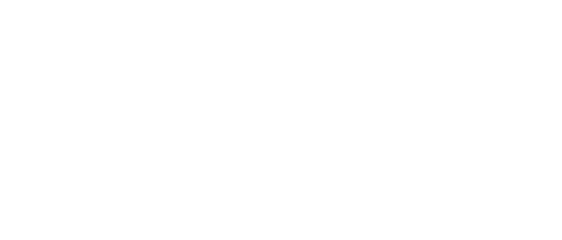
Leaders relevant to this article: