This Control Talk column appeared in the April 2019 print edition of Control. To read more Control Talk columns click here or read the Control Talk blog here.
The golden years of my career are dedicated to maximizing the synergy of the best I&E and PID design, as seen in “Meeting of minds” for temperature and “Meeting of minds encore” for pH. Here, we look at flow measurement with the insight that the process is defined and manipulated by the mass flows as seen on the process flow diagram (PFD). While volumetric flows may be useful, mass flows define the material balance for changes in production rates and operating conditions, plus the process gains derived in the Appendix F of my ISA books (e.g., 101 Tips for a Successful Automation Career).
Accurate mass flow measurements are particularly critical for reactors. Any reactant concentration not in the exact ratio per the stoichiometry for the reaction will limit the reaction, reducing capacity. Also, the unconverted reactants cause a loss in process efficiency. To prevent this, one or more reactants are attempted to be kept in excess of what is required, but this corresponds to a loss in efficiency as well. Correction by analyzers is always playing a game of catch-up where transportation delay, sample time and analysis time mean a lot of wasted time and material.
There are many mass flow measurements, but most depend on adding temperature and pressure measurements and assume a constant composition, often not realized by the user or in the process. A composition of each stream being exactly what is shown on the PFD is a rare occurrence. The fact that processes are not perfect is realty, and is why process control systems are so valuable.
The Coriolis meter offers a true mass flow measurement with extraordinary accuracy and rangeability, particularly for liquid flow measurement, independent of chemical concentration, density and viscosity. The accuracy can be as good as 0.05% of rate for liquid flow with a rangeability of 200:1. Additionally, the density measurement offered is as good 0.1 kg/m3 for measurements between 300 and 5,000 kg/m3. For streams where a single component has a density that is quite different than the solvent or other component, the density provides a fast, reliable measurement of the component concentration. This is especially important for reactant streams to detect changes in the composition of raw material or recycle streams. It can also be used to closely monitor the excess reactant in a product stream.
True mass flow measurements are critically important for control of many other types of process equipment besides reactors, such as crystallizers, evaporators and distillation columns. The Coriolis flowmeter provides this capability up front and retains this capability, holding its calibration despite many adverse situations. There are no upstream or downstream straight run requirements and basically no maintenance requirements. While the upfront cost is higher, the lifecycle cost is typically less, particularly when you consider the cost of maintaining impulse lines. If you consider the impact on process efficiency, the extraordinary accuracy and rangeability, and a true mass flow measurement, translates into an incredible return on investment. The challenge is, how do we estimate and recognize this potential? A digital twin with a first-principle dynamic model, as described in “Virtual Plant Virtuosity,” can readily show the loss in process performance from an error in the mass balance.
While the Coriolis flowmeter is far less susceptible to problems, it’s useful to explore possible effects to gain confidence and justification for future applications and to alert the user to the special cases where this extraordinary performance is threatened. “Knowing the best is the best” is my goal. I am impressed how technical advances seen in Smart Meter Verification (SMV) for smart meters can help us in this path. The following conversation is offered to gain insights on SMV capability and achieving the best by Tom O’Banion, director of chemical industry innovation for Emerson Automation Solutions.
What is the effect of corrosion and erosion?
Tom: Although rare in practice, corrosion causes a thinning of the tube, which in the short term usually causes the meter to over-register (mass flow) and under-register (density). The thinner tube twists a bit more (so the flow reading is now biased high) and the frequency increases (so the meter thinks the fluid density has gone down). SMV can “see” this happening before the sensor tube integrity is affected. The goal is to get that meter out of service before a (very rare) tube breach could occur. We have a great case study of a SE USA refrigerant manufacturer that, after six years in service, saw a meter suffer from a process upset. SMV “saw” the damage, and the customer was able to schedule a replacement—safely preserving the plant’s production. Erosion also thins the sensor tubes, with virtually identical effects as corrosion. In both examples, it’s difficult to predict how uniform the corrosion or erosion is, so there is no 1:1 correlation to accuracy. The Pipeline Research Council (PRCI) did a fantastic study a couple of years ago.
Greg: What is the effect of coatings?
Tom: Tube coating in general does not affect mass flow very much, but it does affect the density reading, and thus, concentration measurement and volume flow (Coriolis volume flow = mass/density). Coatings tend to be denser than the fluid, but it varies. It’s more difficult to detect, but our new SMV Professional has a coating detection feature. If the coating is somewhat uneven, it’s relatively easy to see. If it’s highly uniform, we also look at other variables from the meter (drive gain, trend of density) to ferret out what’s happening. We have a number of field trials currently underway to better understand the range of coatings from various industries and applications.
Greg: What is the effect of freezing?
Tom: Freezing (water) will cause swelling of the tubes, and thus an increase in stiffness. This will cause the flow reading to under-register (tubes twist less for a given amount of flow, since they are stiffer). The effect on density is difficult to predict, but accuracy will be degraded. Note that in most cases, the meter is permanently damaged.
Greg: What is the effect of plugging?
Tom: When I first started at Micro Motion in 1987, I worked in the repair department for a couple of weeks. One of the meters we received was found to have one flow tube completely plugged with an asphalt-like substance. The flow capacity was greatly reduced, but the meter calibrated to within 0.5% of its original accuracy. One tube would twist while the other tube would merely vibrate. Density accuracy was way off (25%), but the meter was cleanable, and returned to its original condition. No permanent damage. Not always the case!
Greg: What is the effect of gas bubbles in liquids?
Tom: We’ve done a lot of research on two-phase flow over the past 15-plus years. It’s a complex fluid interaction. Small amounts of gas and good mixing cause only small accuracy degradation. Larger amounts of gas, whether it’s well mixed, bubbles or actual gas slugs, cause more adverse effects on flow and density accuracy—the gas and liquid decouple from the tube vibration, causing larger errors due to a velocity of sound effect. We see a wide range of aerated fluids, some with intentional vapor introduced (ice cream), to high-vapor-pressure fluids (LPG, cryogens) to produce crude oil with gas breaking out of solution.
Improved two-phase flow measurement ability is a big subject in industry, and so our research continues. We have a few software options that help mitigate the effect. Advanced Phase Measurement is one prominent one. It reads the last “good” values for density and uses that to “steer” through the chaotic and periodic periods of substantial gas bubbles. Check out the YouTube videos:
“How two-phase flow (entrained gas) affects a Coriolis meter”, “Webinar: Enhancing Coriolis Performance in Entrained Gas with Advanced Phase Measurement”, and “Bubble Flow, Slug Flow and Empty-Full-Empty Flow in Fluid Applications.”
Greg: What is the effect of liquid droplets in gases?
Tom: Liquid or “wet” gas has a somewhat similar effect as gas bubbles in a liquid stream. The liquid tends to stream down the tubes, dampening some of the vibration, causing density to over-read. Flow and density readings may both become erratic and less accurate. Wet-gas research is ongoing by multiple groups (primarily for upstream oil & gas), such as Colorado Engineering Experimental Station Inc. (CEESI), South West Research Institute (SWRI), and American Gas Association (AGA). World-class papers have been presented at the North Sea Flow Workshop and International Symposium of Fluid Flow Measurement (ISFFM) as examples.
Greg: What is the effect of improper sizing?
Tom: If the meter is undersized, excess pressure drop may result. That creates more pumping or compression cost. For high-vapor-pressure fluids, an undersized meter may induce flashing or cavitation, adversely affecting the flow and density accuracy. If the meter is oversized, it may operate outside its accuracy sweet spot. Coriolis is often not a line-size meter—sizing is based on actual process conditions, seeking an optimum balance between accuracy, pressure drop and cost.
Greg: What is the effect of poor installation?
Tom: In the early days of Coriolis (pre-1990s), installation was more critical, as some designs were sensitive to pipe mount, stress and cross-talk. These have largely been eliminated now. The most common field issue I’ve seen recently involves the meter not staying full of liquid, or trapping bubbles, or trapping liquids in a gas application. It’s a piping design challenge, usually easily rectified. Occasionally we see a meter under large axial or radial forces, and the meter zero is shifted. We occasionally get a report from the field of an installation problem, but it usually turns out to be something else. In very rare cases, a modification needs to be made to the installation (e.g., moving one meter and adding more stiffness to the piping supports).
Greg: What can cause measurement noise?
Tom: Noise on the measurement signal can arise from a few sources, usually excessively high flow rate (large pressure drop) or gas breakout (e.g., flashing). High measurement noise necessitates some filtering (time constant), which will slow down the meter’s rate of response. In a continuous flow application, that’s not usually a problem, since flow total is often more important than flow rate. In a critical chemical reactor feed application, speed of response is very important, and rate can be critical.
Greg: Can we put Coriolis meters in series and parallel?
Tom: Absolutely! Two common applications that come to mind are safety instrumented systems (SIS) and large flow rate applications. In SIS, the application may require 1oo2 or 2oo3 voting, so two or three meters will sometimes even be mounted in series, flange-to-flange. Large fiscal transfer stations often rely on multiple large Coriolis meters in parallel. I’ve seen applications for Coriolis in 30-in. crude oil lines requiring four or more large Coriolis meters. These are well known for working well in high-accuracy, custody-transfer-level conditions.
Greg: Could we temporarily insert a Coriolis meter to verify the calibration of other meters, or to find the real density for their calibration?
Tom: Yes, our meters are often used in regulated industries such as food & beverage and life sciences, where master meters are installed on portable carts and moved around the plant, calibrating other meters. These masters are available with full ISO-17025 NIST traceability. On a side note, customer needs still include a clamp-on Coriolis, to measure mass flow and hopefully fluid density. It’s still a “gleam in our eye,” but very challenging to do.
For much more on Coriolis meters, check out “Smart Meter Verification—Latest Developments in Coriolis Technology” and “Coriolis: The Direct Approach to Mass Flow Measurement.” Also, an American Petroleum Institute (API) standards committee is embarking on a comprehensive rewrite of the Manual of Petroleum Measurement Standards Chapter 20.3 Measurement of Multiphase Flow. A list is being compiled of many different multiphase technologies with some of their capabilities, key features, application uses and limitations. The intent is to have a chart in the API multiphase standard listing different technologies, and that may help with multiphase metering.
(10) The stream composition, density and flow must be exactly what are on the PFD.
(9) Meter sizing was so easy; we just went with line size meters everywhere.
(8) We put flowmeters at the high point in the line to make sure they are empty for maintenance.
(7) We put flowmeters in the pump suction to reduce the required pressure rating.
(6) We standardized on the same materials of construction for all applications.
(5) My impulse is to use impulse lines.
(4) What is a Coriolis meter?
(3) If we get a reading during water batching, we are all set.
(2) Who needs turndown and ratio flow control?
(1) We must minimize instrumentation costs.
Latest from Flow
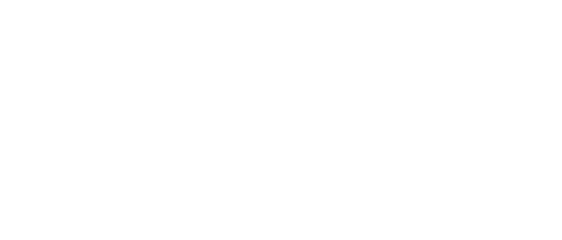
Leaders relevant to this article: