Power producers making room for renewables
Across industry, energy management has become part of the way we do business. In many cases, regulations are forcing industry to meet new standards, and many are making sustainability a long-term goal before they’re caught behind the curve. In the power generation industry, renewables are growing rapidly, and coal power plants are being decommissioned. While this boost in renewable energy will go a long way to create a more sustainable industry, it does present challenges for the power grid, as the supply of renewables varies more.
Three industry experts gathered for the Automation Fair Industry Forum on Power and Energy this week to discuss how the rise in renewables has affected other segments of the market and solutions for dealing with power variability. On the factory side, many facilities also deal with intermittent power quality issues, or voltage sag, which can disrupt operations, but solutions exist to identify and remedy power issues at the end of the line too.
The new market behind renewables
Pat Begley, vice president of sales at TTS, said the company does “everything from soup to nuts in the power plant side.” It started primarily in the gas turbine space but has expanded into pipelines and pumping stations. “We do a lot of systems work. We don’t work on the internals of the gas turbines; we do all the systems around the gas turbines. So, we design process systems, gas systems, liquid fuel, water and steam and more recently, with the advent of hydrogen as a fuel, we’ve been involved in hydrogen-blending skids,” said Begley. “We tend to work on older equipment. We give our customers unique, dedicated solutions for their problems.”
The rush to renewables has created some interesting opportunities for TTS, as utilities look for complementary backup systems. “The grid is becoming less stable,” Begley said. “It was once big coal plants and nuclear power with smaller gas turbines and diesels; they had a predictable operating profile and were generally very stable when they were operating,” he said. But hen you start adding renewables that are dependent on weather fluctuations and other factors, you get more variability. “That’s created a need for a backup,” Begley said. “Old gas turbines and smaller hydro units that were almost forgotten, or at the back of the plant and weren’t used, have now become important elements in the solution.”
This older technology has the advantage that it can get online quickly, both for initial set up and when it’s needed intermittently. “Availability, reliability and flexibility are key, so you have to have control systems and equipment that is reliable, that you know will work when you need it to work and be flexible, so you can get it on and off quickly,” Begley said.
He discussed the company’s first hydro application for a municipality in the city of Redding, California, in response to the variability of other clean energy sources. The hydro unit was remote, on a lake about 30 minutes from the plant, and the customer needed access controls to the hydro unit at the main location.
“Basically, a hydro turbine is a really simple thing; you open what’s called a wicket gate, water goes in, turns a turbine, and you get power out,” Begley said. The old system in Redding had outdated parts and no technical support. “It wasn’t an integrated system,” he added, “and very complicated as a result.” In general, the system was difficult to maintain and calibrate. “This thing was mostly full of stuff trying to connect all the bits together,” Begley said. “It worked, but it was very, very complicated.”
The engineered solution included a turbine controls upgrade and integration of the generator, controls, protection and metering, including a more up-to-date HMI. “We went from a miscellaneous collection of junk in the panel, to a system that was able to talk digitally to all of the existing equipment,” Begley said.
The viability of existing power generation equipment depends on simplified control systems and unit flexibility, Begley said. “This old stuff, vintage units with predictable reliability and availability, is a real need now. It’s become a very fast-moving market,” Begley said.
Thermal energy storage
Steve Balek, automation manager at Stellar Energy, joined the group to discuss thermal energy storage (TES). Stellar builds custom chiller modules for many different kinds of customers, totaling 150 projects in 15 countries. “We cool the air going into a gas-fired turbine to help augment the power during high ambient conditions,” Bagley said. “Turbines are constant volume machines, so when the air warms up it becomes less dense, so it loses power.” During ambient conditions, chillers cool that air down, which brings power back up. Stellar Energy works in many different industries, including district cooling, data centers and combined heat and power (CHP) plants.
“What is thermal energy storage? Basically, it’s a thermal battery that you use chillers to charge during off-peak or low demand periods of time. Then, during on-peak period of time, you either reduce the number of chillers you’re using or shut them off completely and use that thermal energy in your process,” Balek said. “With the use of TES tanks at turbine power plants, we help balance the unpredictability of renewables.” The automated equipment monitors how much energy is being used to charge the tank and how energy will be used the next day, and shifting that energy load appropriately can provide big cost savings.
Power quality and soft switching
Brian St. Pierre, regional business development manager of power quality at Rockwell Automation, discussed how lags in power can affect manufacturing operations. Most commonly, facilities are affected by a voltage sag, a momentary dip in voltage. This drop in power can significantly disrupt manufacturing operations, and often times, they don’t know why. Most utilities provide little help with the quality of the power they serve. Facilities are often left to find their own solutions.
The editors of Control, Control Design and Smart Industry are reporting live from Automation Fair. When the event comes to a close, the editors will compile a report of the best, most important coverage from the event. Register now to pre-order the report and be among the first to receive it in your inbox. Pre-order your copy now.
“We’ve been monitoring this for 20 years, collecting data all across North America about what power quality looks like when it finally gets to the end user,” St. Pierre said. Their research on voltage sag events has told them that relays will drop out when only 70% of the power is remaining, and at 60% remaining power, PLCs will shut down.
St. Pierre gave many industry specific examples. What can a split-second sag in power do to automotive operations? It can interrupt robots, break tool bits, lock up machine tool controllers, trip transfer lines, kick compressors offline or disable inspection systems. For food and beverage, a momentary voltage sag can compromise sterility in packaging lines, clog dry extruders, shut down dryers, or idle compressors, pumping systems and chillers. In the world of semiconductors, power quality can compromise clean room integrity and damage expensive, hard-to-replace equipment, creating major and costly production delays.
With Rockwell Automation’s DySC (for Dynamic Sag Correction) solution, which detects those voltage sags and replaces that missing voltage to keep power quality stable, plants can see a power quality efficiency jump from 92 to 98%, as one steel and glass manufacturer measured it, St. Pierre said.
The invention for the energy storage mechanism in the DySC came out of the University of Wisconsin work for the Navy on nuclear powered submarines to stop glitches. They needed a solution, but it couldn’t be a big battery-based uninterruptible power supply (UPS) solution. “They created a switching solution, and then they realized what they actually had was a battery-free UPS. It just has limited duration,” St. Pierre said. The system works essentially by stealing current to prop up voltage. “At the heart of it, we don’t need stored energy,” St. Pierre said.
While power generation is changing with new renewables, what is old becomes new again, as gas turbines serve as backup power to balance the unpredictability of renewables. Factories have their own set of sustainability and energy management goals for their in-house processes, but many also deal with power quality issues. Solutions for both power generators and the factories that use that power will keep power on and operations running.
Latest from Automation Fair (Rockwell Automation) 2021
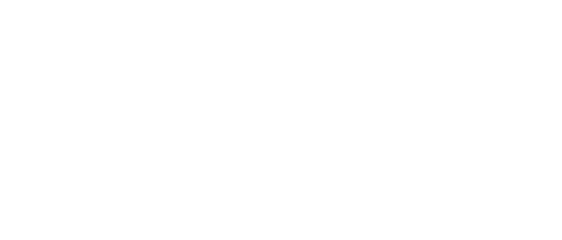
Leaders relevant to this article: