Labor looks different in the food & beverage industry
Labor issues topped the list of concerns faced by participants of the Food & Beverage Industry Forum at Automation Fair this week in Chicago. “Workforce is one of our biggest challenges,” said Brian Marsh, senior director, digital manufacturing, at Nestle, who was part of a panel of industry veterans from diverse companies leading the discussion. “There’s just not a large labor pool out there to fill our needs. It’s important to be able to create a new environment. Manufacturing isn’t sexy, so how do you create an environment that attracts them and keeps them? Nobody wants to sit around in training and read from binders. We want to get them on the floor and let them start doing something valuable for the company. It’s all about the people and the technology going at the right speed.”
Most organizations aren’t sure where to start, warned Joe Francel, director, business programs, manufacturing service line at Microsoft. “Start with the business problem,” he advised. “A lot of us are engineers and are comfortable going to the solution first. Don’t look at the technology. Use cross-functional teams and get input from a lot of different areas. Once you start, where do you go from there? What’s impacting overall equipment effectiveness (OEE)? Give me information that’s actionable. A lot of customers say they have a data lake, but they’ve not gone through and used the input of the people to determine which data matters. Don’t just collect data because you can.”
The more things change, the more they stay the same. “Ten years ago, when I started working with customers,” recalled Andrea (AZ) Zaman, chief operating officer at Pearson Packaging Systems, “the number one thing we heard was the workforce. There was turnover. We needed to design equipment that was easy for operators to use. The issue is still workforce, but it’s different. Now the equipment needs to be easier to use so your employees go home every day feeling accomplished. That’s where technology can take us. As we look forward, we look through the eyes of our customers.”
Workers need to know they’re part of a team, agreed Marsh. “The work cell is just part of the whole entity,” he said. “What’s going on upstream and downstream?”
And once those workers are indoctrinated, trained and aware of their roles in the overall business outcome, retaining them can be difficult. But retaining what they know is within closer reach than it’s ever been. “How do you capture the tribal knowledge?” asked Francel. “How do you force more interaction with the workforce and give them more tasks of value vs. mindless labor? Let automation do the mindless tasks, so employees can do more meaningful tasks.”
Zaman cited an example of a customer that didn’t even know it needed new programming to improve productivity, but Pearson Packaging was able to push it through using remote connectivity without interrupting the customer’s workforce.
Digitalizing for good
The ability to connect remotely and to analyze data creates as many new challenges as it does opportunities. “My focus is trying to do things in real time,” said Francel. “Years ago, when I worked for a coffee company, we had both historical models and real-time demand metrics. That winter, we ran out of Christmas blend coffee. We had that information from the stores, and it told us the demand was higher, but nobody looked at it. It’s important to use real-time information and not just historical analyses.”
Nestle is looking to streamline processes, which is challenging in a regulated industry. “We use lots of metal detectors in our factories,” explained Marsh. “When they’re good, no one cares. We need to pay attention to any variations in our metal-detector checks. Sometimes we get cartoner stock that causes problems with our packaging equipment. It’s easy to take vision equipment and identify when something abnormal is going on in the factory.”
Zaman looked back at when Pearson’s service technicians had to be in front of a machine to troubleshoot it. “Days and hours matter for production,” she said. “We’ve moved into Vuforia and Emulate3D. We’re able to remote into machines with cameras when the machine calls in. Where are we going next? Everything will be in the cloud. We want the information to come up safely into the cloud and ping us. Those things are going to evolve. We get pinged. We reach in, and we solve it.”
Operational complexity
With consumer markets demanding more personalization, the number of stock-keeping units (SKUs) continues to rise, which means machines must be flexible to accommodate changeovers. “A while ago, P&G called it, ‘Set it, and forget it.’ That is no longer where we are,” explained Zaman. “Baby Wipes, for example, come in so many different SKUs. Marketing departments change things, so machinery needs to be flexible. We look at our design differently. We look at production needs over the life of the equipment. It’s not just different SKUs. Different production lines have different operations. Production variables are different from machine to machine. Artificial intelligence (AI) will help us to identify these better than humans can.”
Francel looks at the issue from a different angle: “How do you minimize changeover?” he asks. “The product is the same, but how do you minimize and consolidate the changeovers? One customer minimized the changeovers by looking at the data. Can I stage everything to minimize the impact of the changeovers? If I have one plant that does a changeover in 30 minutes and another takes an hour, what is the 30-minute changeover facility doing differently?”
Changeovers are an excellent application for the digital twin, explained Marsh. “How many times have we had situations when we want to make changes on our line?” he asked. “There’s a lot to that. You have to be sure that works. You can use the digital-twin model. Being able to build these virtual environments decreases the risk. That’s something that’s never been available before.”
Chaney agreed on the digital twin’s potential. “The beauty is: the more you learn, the more you can feed back, and the better the digital twin gets,” he said. “We put it in a 3D model so I can see a plant running. We’re moving toward smart manufacturing. A lot of us in food and beverage are dealing with natural ingredients. Every bit of corn or flour is not the same.”
The cybersecurity conundrum
The ability to remotely optimize production, troubleshoot problems, leverage data and enable the digital twin hinges precipitously on secure connectivity, and it’s a team sport. “Cybersecurity is not just an ideal,” cautioned Francel. “There’s an operations element to it. You need remote support. You need to have operations, IT and engineering all involved. It’s about universal governance that all three parties influence. The biggest advantage of the cloud is focusing on who has what access. Give them what they need instead of what they want. Risk tolerance is part of the equation."
Adding an IoT device in a factory requires a process that does that quickly, said Marsh. “It’s happening more and more,” he stressed. “How do we get all of this stuff connected quickly and safely? At our factory levels, it’s trying to get employees educated as they’re picking new devices. Every company we deal with is different. Some of them do cybersecurity great, and some not so well.”
The silver lining of the pandemic was that it finally enabled remote access into equipment. “It made everybody pucker,” explained Zaman, “but the alternative was not available. It’s hard to be safe if you don’t know. Now we need to be careful to find those ways to be safe. The thing that stops us is fear. If you can play in a digital world, you’re advancing yourself.”
Remote monitoring of data is OK with Marsh at Nestle but making adjustments to machine controls from a remote location can be problematic, if there’s no one at the site to oversee what happens. “We’d want a person there if someone is making adjustments to the controls remotely, in case something goes wrong,” he said. “We don’t want to put someone in danger.”
Get the best of Automation Fair 2022
When the event comes to a close, the best, most important coverage will be compiled into a report. Register now to pre-order the report and be among the first to receive it in your inbox.
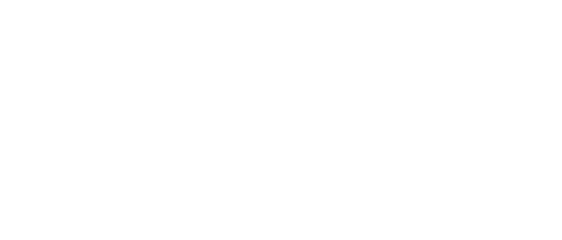
Leaders relevant to this article: