Mining industry leverages technology to optimize production
The benefits of modernization were front and center at this week’s Mining & Metals Industry Forum at Automation Fair 2022. First, attendees learned how Chicago Heights Steel benefitted by modernizing its aging control systems. Then, how mining companies around the world can become more sustainable by taking a second look at traditional grinding technologies.
Moderator Mauricio Alfonso, industry process director at Rockwell Automation, first welcomed panelists Antonio Ambra, managing director, North America at AIC; David Zapata, general supervisor of engineering at Chicago Heights Steel; and Gillian Holcroft, president of ReThink Milling and innovation manager at the Canada Mining Innovation Council.
Ambra and Zapata took the stage first to outline a production system upgrade at Chicago Heights Steel, with the help of AIC, a power control supplier and system integrator.
Chicago Heights Steel was established in 1893, and today is the largest special market mill the U.S. The mill recycles rail steel into many products for farms, ranches, municipalities and job sites, including fence tee posts, U-channel posts for signs or other custom products. The plant takes the rail steel and splits it at high heat into three sections (the head, the web and the flange/foot). Each part is rolled to a predetermined shape and size by a series of rolls. “We roll a different product out of each one of those sections,” Zapata said.
The plant had many issues with reliability. Equipment was constantly failing without warning, and diagnosing issues was nearly impossible, all causing significant losses in production. In addition to improving automation reliability and diagnostics, the project also needed to accommodate a new open system that would allow for modifications down the line; reduce maintenance costs for spare parts and downtime; sustain consistent production and mill capacity; and install an integrated and comprehensive control network infrastructure.
“The distributed control system (DCS) that we had in the plant was very antiquated with very little feedback,” Zapata said. Most of the equipment had reached the end of its life, and spares were no longer available. “When I took over the electrical department three years ago, I was tasked with the job of finding a solution,” Zapata said, and he started working with AIC. “At Chicago Heights Steel we’re very hands on,” he said. “I go with my guys. I put my hands on the equipment with them. And we picked AIC because they had the same mentality. They were able to basically get in there with us and find the solution.”
The solution included a ControlLogix control system and other Allen-Bradley components from Rockwell Automation. The AIC rolling mill automation and control system (RACS) solution has been installed in more than 50 plants around the world. The solution also uses the Rockwell Automation FactoryTalk View SE HMI, another product very familiar to AIC. The plant’s two production lines were kept separate. “So that one day the mill would be able to roll on a single line,” Ambra said. “It’s also a system that allows expansion.”
The previous configuration was dangerous for operators, and the new panel design included many safety features, such as safety door options and arc flash detectors. Also, with a lock box on the main floor, operators can request access to a machine, and the mill will automatically stop rolling. Then, the operator can access the needed key. “When the key is out, we are making sure that everything is off inside the cabinet,” Ambra said.
With only 10 days to commission the project on-site, scheduled during an annual shutdown, AIC relied on Rockwell not only during design to help properly configure the network, but also at the panel manufacturing facility in Italy to test the products before they were shipped on-site.
With the new system after only three months of rolling, performance increased by 15%. “This gives an idea of how much time the mill was losing before with the old system,” Ambra said. The mill also produces much less scrap steel from its new production process.
Disruptive technology for grinding equipment
In the second Industry Forum presentation, Holcroft outlined a pilot project to develop conjugated anvil hammer mill (CAHM) platform technology, which has the potential to reduce energy consumption by 65% compared to high-pressure grinding rolls (HPGRs).
Holcroft detailed the work being done to develop CAHM and how the Canada Mining Innovation Council consortium is supporting the project. Her work with CMIC helps to encourage mining companies to work together to solve common problems in the industry and is focused on disruptive technologies. “If we pool our resources together, share risk and share reward, maybe we can accomplish something great,” Holcroft said. She began managing the project four years ago.
Mining consumes between 3 and 6% of the world’s energy. “Grinding equipment really hasn’t advanced at all in the last 20 years with the last major advancement being a high-pressure grinding roll,” Holcroft said.
The consortium in charge of advancing new grinding technology includes CTTI, the inventor and product developers, Anmar as the fabrication partner, Corem as the testing experts, and Rockwell Automation as the automation partner. The consortium also includes a number of mining company partners, who are investing resources and funding to advance the project. It has the potential to greatly reduce operating and capital costs for grinding operations. “And of course, with all these things together, we can have a big impact on environmental, social and governance (ESG) and decarbonization targets,” Holcroft said.
The project has $11.9 million of investments to date. “When you’re going after government grants, if they see that you have major mining companies putting money behind this, it must be good,” Holcroft said.
The key innovation is unconfined thin particle breakage, which is a more energy efficient way to break rock and works for every hard rock and most soft rock mines. The energy benefits come from eliminating small rock crushing and compression and shear fractures, maximizing voids allowing crushed rock to expand, and minimizing wear with synchronized crushing surfaces. There is very little hold up of material in the machine. “The hammer pushes the material from the slot as soon as it’s fine enough,” Holcroft said. It eliminates repressions and significant fines and maximizes voids in the material. “The novelty is in maintaining a thin particle bed,” Holcroft said.
Once material leaves the CAHM, it enters the MonoRoll, which is designed to replace the ball mill. “The combination circuit of the future would not have recirculated pebble crushers or hydrocyclones. All the screening is happening within the machine,” Holcroft said. “Less equipment means less operating costs.”
The design was optimized by CTTI based on discrete element method (DEM) modeling. “They did over 200 simulations optimizations to figure out what should be the angle of the tooth and the hammer and the anvil,” Holcroft said. “They optimized that slot geometry to maximize energy efficiency and minimize wear, so before we ever engineered or built anything, they had simulated everything.”
This was necessary in part because the machine is massive. It weighs 27 tons. It measures 8.5 meters long, four meters wide and six meters high, and processes 50 tons of rock per hour. Hot commissioning of the prototype was underway in August 2022. They are running experiments on the protype to determine the limits for capacity, energy reduction, reduction ratios and product size distribution. They anticipate that further updates to the machine can reach a 72% energy reduction compared to HPGR, as well as superior product and higher reduction ratio in a single pass.
“Because of the way this machine is designed, and the hydraulics that are pushing forces to crush the rock and force the hammer and the anvil together, if we have a situation where we get trapped metal inside the machine, we need the hydraulics to react to that event in less than 10 milliseconds to not damage the liners in the machine,” Holcroft said.
The technical team wants to track 150 analog, digital and vibration inputs at 200-Hz and react to events within milliseconds. “At 5 milliseconds, we are really at the sensor and hardware limits,” Holcroft said. Rockwell’s FactoryTalk Edge Gateway and variable speed drives helped make it possible, she added.
ReThink Milling wants to be a licenser of the CAHM platform technology for one or multiple original equipment manufacturers (OEMs). Holcroft said the project still needs additional strategic mining partners and funding, and hopes a commercial rollout can happen with one of the consortium’s mining company partners.
Get the best of Automation Fair 2022
When the event comes to a close, the best, most important coverage will be compiled into a report. Register now to pre-order the report and be among the first to receive it in your inbox.
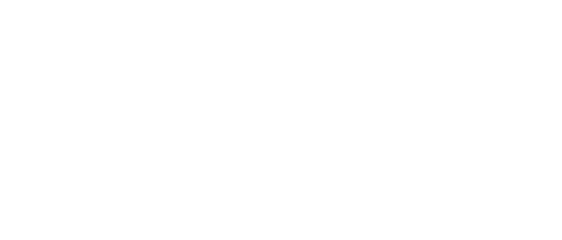
Leaders relevant to this article: