The tools, tactics and talent transforming manufacturing
The challenges are familiar to all of us. Supply chain disruptions are limiting our capability to procure parts needed for manufacturing, while simultaneously customers are demanding full customization capabilities, and they expect to receive their custom products ASAP. Within our facilities we struggle with aging workforces, dwindling workforces and workforces that are being challenged to adopt newer, smarter ways of working in the digital era.
Yet—weirdly—there is tremendous optimism, particularly among solution providers here at Automation Fair 2022 who promise they are developing the right tools to right the industrial ship.
During their presentation titled “How Innovative Technologies Are Improving Productivity,” David Vasko, senior director of advanced technology, Rockwell Automation, and Jerry Foster, chief technology officer at Plex Systems, noted how there are currently 800,000 unfilled domestic manufacturing jobs. That scarcity is limiting productivity and inhibiting manufacturers from achieving true digital transformation. By 2030 that gap will balloon to more than 2 million unfilled jobs, which just might cripple the U.S. industry.
So, what tools can be employed to solve these problems? Take your pick!
Automation, in the broadest sense, has the power to do more with less. Vasko referenced a bio-tech company that replaced its small team of overworked, overqualified scientists with tabletop production units that performed the repetitive cartilage-building tasks.
Robots, of course, are filling many of the ranks vacated by human workers. Among the most appealing aspects of modern versions is the ease of training—a factory worker can instruct a robot to perform a task about as quickly as he can learn it himself.
The presenting pair described the benefits of artificial intelligence (AI) in the modern manufacturing space this way: AI can give your newest operator all of the powers of your best operator. “Superpowers,” Vasko said of AI, when used properly.
And, lastly, the duo celebrated the value of the digital twin in stressed industrial workplaces, which enable every member of teams to access, test, tinker and optimize processes for their real-world asset counterparts.
These are more than just cool new toys. Modern digital technologies are recruitment levers, workforce enablers, staff-training and retention devices. The challenges we see in the global industrial arena are spotlighting the value of them—pressure makes diamonds. And hard times are prioritizing new skills.
The ideal modern worker, according to Vasko, is flexible, as she must adapt to constantly evolving tech. She is a natural problem-solver, a strong communicator, and an eager collaborator, as the Industry 4.0 approach depends on sharing data across functions. The ideal modern worker is digitally inclined, capable and eager to learn and quickly put to use new tactics. This duo described the value in “leveling up” operators, technicians and engineers as they adopt additional skills, roles and responsibilities. This helps keep them around.
“The solution is really simple,” said Foster. “We need to leverage these advanced tools by making sure the people in the factories know how to use them. It all has to be about productivity—making us more efficient, more productive. These things like cloud and AI and robots give us a fighting chance over the next 10 to 15 years.”
Foster referenced fallout from the pandemic in recent years—those using cloud-based manufacturing execution systems (MES) were able to operate much more smoothly (oftentimes remotely) than those shackled by on-prem systems. “Factories using local software really struggled during that period,” he said, before asking the audience to imagine the industrial worker of the not-too-distant-future. She is operating a complex asset, but she’s doing so miles away from the factory, sitting on the couch in her living room, equipped with virtual-reality goggles that enable her to interact, digitally, with machines and to connect with a global network of fellow expert operators in the metaverse. “This is a real possibility,” he said. “It’s still a few years away, but it’s coming quickly.”
Presently, cloud computing and remote technologies are shifting strategies. The presenters detailed three ways smart approaches are affecting the modern industrial workplace:
Business impact: These approaches can help industrial enterprises weather unexpected disruptions (think pandemics, bad weather and war). “Decision-makers can still make decisions,” said Foster. “They can still get real-time updates on operations via cloud computing, rather than the on-premise approach, where information was trapped in a black box within facilities.”
Employee impact: When the workplace adopts these smart approaches, the workers can more often keep working. Shutdowns are reduced. Remote access enables personnel to, as Vasko described one employee, work from his RV while traveling the country. “Happy employees are more productive employees,” he said.
Additionally, cloud computing widens the talent pool, enabling employers to find the skills they need from a global selection of workers.
Technology impact: Simply put, cloud technologies boost productivity. The presenters used as an example augmented-reality glasses, which can enable one field engineer to access the intelligence of his full team back at headquarters. “You can pull others into your environment to help with challenges. The technology impact of the cloud is huge,” said Foster. “And in combination with the IoT and 5G capabilities, there are massive benefits.”
The wins in adopting this mindset and embracing these tools are plentiful for employers and the teams that help them realize their plans. But this transformation of tactics and upskilling of workers can prompt a surprising, challenging side effect, the presenters explained. As they become more technically skilled, workers become more attractive to hi-tech employers eager to hire them away.
The solution?
Making their current jobs as rewarding as possible. “We want to elevate the perception of manufacturing,” said Foster. “We want young people to think this is a really cool job that they want to pursue. This is not your father’s manufacturing facility.”
Get the best of Automation Fair 2022
When the event comes to a close, the best, most important coverage will be compiled into a report. Register now to pre-order the report and be among the first to receive it in your inbox.
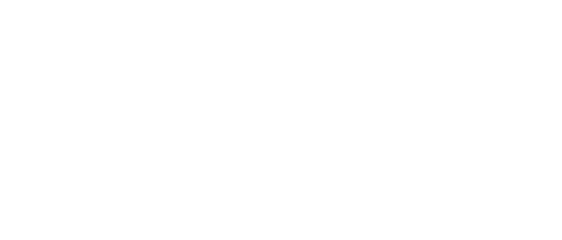
Leaders relevant to this article: