In the recent years, the processing industry has also started exploiting IoT technology. One of the most critical and often overlooked assets in the processing industry is the control valves. IoT can be applied to improve the performance and efficiency of control valves, which in turn, will save maintenance costs and create a more secure work environment.
Let’s see how IoT is enhancing the performance of the control valves.
1. Improved Operational Efficiency:
Perhaps the biggest benefit of IoT will be improved operational efficiency of control valves. In a typical processing plant, media or fluids flow through processing equipment. Control valves perform the critical function of regulating process variables such as pressure, temperature, and flow rate. All these factors contribute to the overall operational efficiency of the process and the plant. Smart control valves can improve operational efficiency in the following ways.
a. Preventing Costly Valve Leaks:
Most processing plants have to operate under harsh physical conditions such as extreme temperature and pressure exposing the equipment to wear and tear. For example, in an oil refinery, flare control valves often end up leaking hydrogen and hydrocarbons. Unfortunately, when excessive pressure opens the valves up, there is no way to close them completely. If such leaks are not sealed off quickly and effectively, they can lead to hundreds of thousands of dollars in losses. It can also turn into a safety hazard which may eventually bring the entire plant to a standstill.
b. Troubleshooting Valve Misfires Due to Voltage Sags
Voltage sags are the most common events that affect the operational efficiency in almost all processing plants. They are particularly common downstream, on long runs. As the complexity of the equipment used in a processing line increases, it becomes more sensitive to voltage sags.
They can sometimes lead to valve malfunction and cause irreversible damage to equipment such as process controllers, Programmable Logic Controllers (PLCs), adjustable speed drives, and robots. Solenoid valves, for example, can suffer substantial damage as the reduced voltage at the wrong time will stop the needed magnetic force from developing. Without sufficient magnetic force, the spool inside the valve will also fail to operate, resulting in malfunction.
Voltage sags can occur due to faults on either side of the meter. In other words, you can’t blame your local power utility every time a voltage sag accident occurs. Your equipment or internal wiring may be responsible for the accident.
However, it is almost impossible to diagnose the cause of voltage sag under normal circumstances. You can use an oscilloscope to monitor the voltage signal at the time voltage sag occurs. However, this isn’t a feasible solution for a processing plant with hundreds of devices and power cables.
IoT-enabled control valves can be modified to collect and analyze voltage levels across the processing line during specific periods of the cycle. You can alter each valve manifold node to include a voltage sensing device. You can record voltage levels across the machine using a “sweeper” program for particular time periods. This data can prove invaluable in troubleshooting power issues in your processing plant.
c. Real-Time Remote Access
Cloud storage allows plant managers to share the data in real-time with all concerned parties including plant supervisor, resident engineers, and the original equipment manufacturer (OEM). For example, if you notice irregularities in the data collected from a temperature-humidity sensor, you can readily shut down the respective valve using a smartphone application or a laptop. Engineers don’t need to be on the factory floor to control the devices or the process. Most manufacturers have created web and mobile apps to provide engineers with direct control over smart devices.
2. Leaner Maintenance Time and Costs
Most processing plants are looking for ways to cut down maintenance costs and downtime. However, the conventional approach towards regular maintenance and repair is time-consuming and expensive. But, IoT technology can not only reduce the maintenance costs but also decrease the resulting downtime.
a. Real-Time Data Sharing with OEM
Although large-scale plants can afford to have skilled engineers and residents on the factory floor round the clock, most small and medium processing plants can’t. They often rely on the OEM equipment manufacturer to troubleshoot the problem.
Manually calling the OEM, checking the problem, and ordering the new valve is a time-consuming and costly process. But, with IoT, plant engineers will be able to share the device data with OEM via cloud storage in real-time. OEM will be notified of the problem directly. Thus, plant owners can resolve the issue relatively quickly, saving both money and time.
b. Predictive Control Valve Maintenance Based on IoT
The conventional break-fix maintenance approach is expensive. The next alternative is time-based maintenance in which an entire section of the plant is shut down for maintenance at regular intervals, say once every month. However, this approach is also costly and leads to more downtime.
IoT offers a third alternative called predictive maintenance which is relatively inexpensive and less time-consuming. In this approach, the data collected from IoT devices is used to track the efficiency, life cycle, and potential chances of failure for each device.
Each smart control valve comes with a sensor that continuously monitors its physical properties. Usually, the monitoring system compares the device data with a pre-established baseline. If a valve starts operating below the pre-set thresholds, the system sends an alert to the plant supervisor and engineers. Thus, you can replace a malfunctioned valve well-in-advance, preventing costly delays and product loses.
Conclusion
IoT technology isn’t limited to smart homes and smart cars only. It is also transforming the processing industry through real-time monitoring and optimization of control valves. It has lead to efficient maintenance processes, elimination of unreliable manual intervention, better worker safety, and reduced production costs. Hopefully, seeing how this technology is changing the processing industry will encourage you to be a part of it. Feel free to tell us more about your IoT experience and future plans in the comments below.
Continue Reading
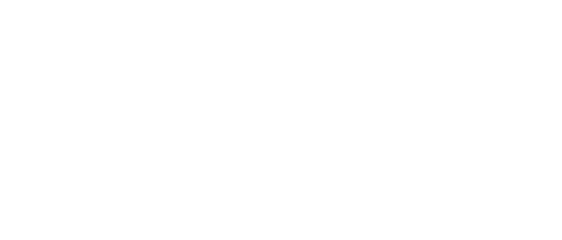
Leaders relevant to this article: