Royal Dutch Shell’s Prelude (Figure 1), the world’s first floating liquid natural gas (FLNG) facility, measures 485 meters and hosts 14 production facilities about as tall as an eight-story building—each brimming with FieldComm Group technologies. When it’s completed next year, it will be towed from its temporary berth in South Korea, and moored to underground wells in the Timor Sea off Australia’s northwest coast.
From the earliest planning stages, Shell knew FieldComm Group technologies would achieve lifecycle benefits from design through testing, commissioning, operations and future upgrades. These benefits are only possible with full connectivity from HART and Foundation Fieldbus instruments to control room and maintenance host systems.
“The main reason wasn’t to reduce engineering or cable costs, but to make use of advanced diagnostics that will enable proactive, condition-based maintenance,” says Rong Gul, subject matter expert for smart instrumentation and instrument asset management with Shell Global Solutions.
About half of the vessel’s tens of thousands of I/O points will come from Foundation Fieldbus devices and the other half from hybrid, 4-20 mA, analog-digital HART devices, Gul explains. The latter are used for many applications, as well as safety, other skid-mounted systems and third-party PLCs.
[sidebar id =1]
Challenges persist for users who perpetuate a culture of “do things the way they’ve always been done,” and fail to fully implement FieldComm Group technologies, adds Gul. For instance, process plants fail to connect HART to their DCS and asset management systems, contributing to a staggering finding—up to 63% of trips to the field are wasted because operators unnecessarily send maintenance to diagnose problems, and no problems are found (Figure 2).
Progress is being made in two areas to tame the complexity of FieldComm Group technologies—clear work processes and simpler device replacement. These are being addressed by FieldComm guidelines, as well as work with U.S. and international standards committees.
Prelude has already demonstrated successful engineering and commissioning from testing through loop check. Gul adds it’s achieved “massive savings, and we’re now automating work processes.” These include an 80% reduction in commissioning times by using templates that are slated to become available from FieldComm Group.
Clear work processes
What constitutes a clear work process? Gul defines it as “bringing the problem to the people.” This means, in a fieldbus, including an online HART scenario, all device data is visible in the distributed control system (DCS) and asset management system (AMS), so operations can interrogate off-spec devices, and may not need to call maintenance. If the problem isn’t found, then the instrument tech can do further diagnostics and troubleshooting, perhaps solving the problem without a trip into a hazardous environment.
On Prelude, the tens of thousands of I/O points coming from smart devices are organized into actionable work processes. Staff will monitor diagnostics to prevent operators from ignoring or turning off functions. Also, criticality rankings are assigned to instruments and applications based on priority levels.
Shell is also working with Emerson Process Management, which supplied Prelude with multiple automation systems, to generate automated reports. These are built on condition-based device diagnostics and in accordance with the NAMUR 107 standard. The huge vessel’s maintenance staff will convert this “pervasive data” flow into their daily activity plans.
Plants seeking to gain full device diagnostics benefits need to have a role in the maintenance organization, Gul says, “who is assigned to work continuously on converting those diagnostics into work tickets. If you don’t, you’ll fail. This fact should be known by the entire organization from technicians to planners.”
Shell plans to share its approach with the FieldComm Group, as well as the closely aligned ISA108 committee covering work processes that use diagnostic data from intelligent field devices.
[sidebar id =2]
Simplified device replacement
“There needs to be an easier way to perform field device replacement,” adds Gul. The Prelude team is pursuing this by using the ISA 108 committee’s incomplete standards to make Foundation Fieldbus easier to configure, install and maintain in two primary ways.
First, Gul reports his team created work processes to make certain, “before a helicopter brings a new device, that someone will connect it on a workbench, and check the model and device description (DD) revision to ensure it will be compatible with the target host system.” This is not a traditional instrument tech task, but Gul adds it’s “absolutely necessary” to streamline the lifecycle, and deliver remote diagnostics and condition-based maintenance.
Second, the team developed reusable software templates that speed calibration, testing and installation of similar smart instruments. This paves the way for virtual marshalling or software-based distributed I/O connectivity—configuration of complete control strategies without physical devices.
Consequently, a technician on Prelude sets up communication with the default DD file, and then creates a standard template for each fieldbus device model and/or revision. At this point, 80% or more of parameters are entered for all similar devices, leaving only the need to enter information for individual devices. Reusable templates and offline configuration also verify all instrumentation is installed to specifications, and does it faster and without human-error-prone duplication of efforts.
While common-sense budgeting and prioritization dictate the use of HART and WirelessHART for half the floating facility’s instruments, Gul says the extra up-front work of implementing Foundation Fieldbus pays for itself during commissioning.
Foundation Fieldbus offers:
- Faster factory acceptance testing (FAT) and device verification testing by a factor of “about eight devices compared to one,” and
- Faster commissioning by a factor of three or four, depending on the device. Gul says a trained technician can tune a smart valve in “about 45 minutes versus three to four hours with HART.”
Other than industry-specific requirements, such as the American Gas Association’s rules for natural gas facilities, Gul reports, “These procedures are all you need to do a successful Foundation Fieldbus project. It’s as simple as that.” Even better, while templates are not yet industry standards, Gul has offered to share them with FieldComm Group. Perhaps the next stop will be integration with ISA108.
Embracing new mindsets
With technical resources marshalled for FieldComm Group technologies, what’s left to change are the minds of users. Gul emphasizes, “Awareness and training, training and more training. You can’t start soon enough.” He also calls for cultural change because without it, “You don’t stand a chance.” He holds two weekly classes on Prelude, one on theoretical training where staffers learn about installation, noise, jitter, imbalance and diagnostics for Foundation Fieldbus and HART, and a second with a DCS and instruments including DP pressure transmitters, guided-wave radar level transmitters and vortex flowmeters.
“You have to give people the right training, tools and confidence, or the gold-plated bells and whistles won’t work,” adds Gul. He reports this training culture is changing minds, including “an older guy, who came up to me after theoretical training and said, ‘I wasn’t a believer, but you converted me.’ ”
Several suppliers agree with Gul that human issues precede technology choices. For instance, as project teams design and plan systems, stakeholders need to be kept in the management loop to prevent mistakes such as uninformed engineering, procurement and construction (EPC) contractors overwriting preconfigured devices.
“To avoid such issues, it’s important as early as possible to have a clear commissioning strategy that’s aligned with all parties,” says Christian Walter, field network engineer at Endress+Hauser Process Solutions. “There’s no one size—or fieldbus—that fits all,” but HART and Foundation Fieldbus can handle online diagnostics to optimize costs and benefits.
Ready for the future
Because human factors weigh heavily on the automation value chain, more recent trends like the Industrial Internet of Things (IIoT) come slower to process plants than elsewhere. Tim Shea, senior analyst at ARC Advisory Group, explains that smart sensors are the “tip of the spear for IIoT-enabled solutions.” However, he laments the lack of users connecting smart sensors for online diagnostics—reportedly only 10-15%. Still, he offers a strong case for greater use of smart sensors as advanced by ISA108, including increased equipment productivity, workforce efficiency and equipment life, and decreased downtime, inventory costs and unplanned breakdowns (Figure 3).
Tom Watson, manager, corporate marketing, Moore Industries-International, adds, “FieldComm Group technologies let users quickly verify and validate control loop and device configuration. It’s a good first step to bringing analog devices into the digital stream, from connecting 16 temperature sensor inputs on one twisted pair to taking instruments wireless.”
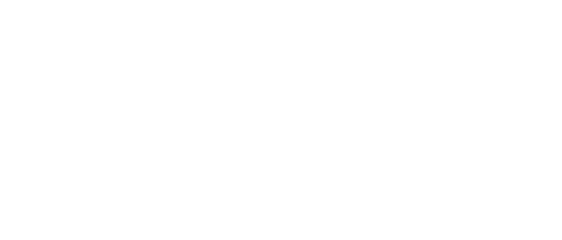
Leaders relevant to this article: