[sidebar id =1]Advanced Process Control (APC) has been used in the process industry and in various forms for many decades. From DCS-based primary control schemes and computer-based Multivariable Predictive Control (MPC), to a wide variety of process units such as atmospheric and vacuum distillation units, conversion units (hydrocracker, FCC, coker, visbreaker), hydrotreaters, gasoline reformers and often some other units like isomerization, steam reformers and distillation trains. While many organizations focus only on major process units, the best in class ones expand APC footprint to secondary units to achieve additional benefits. This may include APC for environmental emissions control, fuel gas network control, sulphur complex control, steam networks control, H2 networks control and more.
The benefits of implementing APC applications on these secondary units and networks are significant from both a margins increase perspective and an operational excellence perspective. However, due to a lack of understanding of achievable benefits, shortage of APC resources and gap in APC technology, among other reasons, some organizations do not expand their APC footprint, leaving significant benefits on the table.
Environmental emissions control
In a typical refining or petrochemical site both Fuel Oil (FO) and Fuel Gas (FG) are combusted in some furnaces or boilers. Analyzers are available at furnace level (typically O2, CO) while others are available at stack level (typically SOx, NOx) with multiple furnaces sending flue gas to the same stack.
Ideally, facilities would have a system in place that would measure the environmental limits in the furnace and stack level, however due to the local, regional and specific country regulations, the process to respect these limits can be extremely complicated. Limits tend to become more and more stringent over time, they may apply for dust, CO, NOx, and SOx for both concentration and mass and they sometimes apply to single furnaces, boilers, single stacks and/or the overall site. Moreover, these limits are not to be applied “as-is” and rules like “(97% of 48h averages) < (LIMIT * tolerance)” often apply. In addition, to make things more complicated, limits are actually changing depending on the fuels mix, e.g. the FO/FG ratio.
[sidebar id =2]
Given the above complexity, operators typically only control the real-time measure, taking a huge safety margin compared to what an APC system can do. This leaves on the table a relevant amount of money that could be measured in millions of dollars per year. For instance, APC systems have been successfully designed and commissioned as part of a bigger scope to address the specific problem of emissions limiting the plant load for major units like crude columns or ethylene crackers. Moreover, controlling the environmental limits (not just monitoring the environmental limits) in closed-loop provides owners and operators a distinctive advantage in managing environmental constraints and regulations with ease.
Fuel gas network control & optimization
Fuel Gas Network control is another very difficult control problem within the refineries and petrochemical plants. Today, it is common to see sites with an unstable Fuel Gas Network which becomes a major issue, as any upset can affect the whole site, impacting both operations and the site energy spend. However, with APC technology, these sites can benefit from a stabilized Fuel Gas Network and optimized energy management.
A Fuel Gas Network can be really complex with multiple headers, KO drums, flares, gas recovery compressors, LPG vaporizers and more. Off-gas flows change continuously (particularly when the units load changes) and if enrichment gas with a high heating value is added to achieve the volume balance, i.e. to control the pressure, the heating value of the fuel gas increases. The COT controllers on the furnaces will cut back on consumption which will upset the volume balance, and the enrichment gases will also be cut back. This behavior keeps going, leading to a self-propagating cycle with the system possibly becoming unstable. Fuel gas instability can lead to units having to cut back load or result in flaring events - both very undesirable situations.
[sidebar id =3]
Fuel Gas pressure and calorific value are interactive and pose a highly non-linear problem that can only be addressed using the proper tools and technology. Volume balance models are integrating processes as pressure builds up as a ramp and exhibit strong non-linearity. Model gains can flip signs as the quality effect of the enrichment gas depends on the current Fuel Gas Network’s calorific value.
[javascriptSnippet]
Adding makeup gas can increase or decrease the overall calorific value which may change over time depending on the specific makeup being used. Adding additional makeup gas has less of an affect as it approaches the current quality. There is no way of easily calculating how much enrichment gas should be added and for how long, as the consumption changes with additions. However, by implementing APC applications and creating a Fuel Gas optimization solution, organizations can achieve major results. For example, APC can:
1. Dramatically reduce the variability in the refinery Fuel Gas system
- Simultaneously stabilize pressure and calorific value
- Stabilize furnace operations
- Stabilize process unit operations
2. Minimize overall fuels cost
- Typically maximize use of Fuel Oil
- Minimize, whenever possible/convenient, use of enrichment gas (LPG/Propane/Butane/CH4)
3. Strictly respect the furnace’s/stack’s environmental limits while making money
- Closed-loop control of emissions; not just emissions monitoring
- Minimize fuel cost until the process unit’s constraints or emissions limits become active
4. Help other APC controllers to maximize throughput and overall profit
- Consistently push local and overall constraints, taking the benefit of a more stable Fuel Gas Network
5. Minimize/completely eliminate routine flaring which is a cost and impacts the environment
6. Minimize blow down gas recovery compressors consumption
7. Reduce the Energy Intensity Index (EII)
- Improve furnace efficiency through more stable firing, enabling further reduction in excess air
{pb}
The proper knowledge and APC technology is required to simultaneously stabilize Fuel Gas pressure and quality and address the inherent strong non-linearity’s in the system. Below is an example of a fuel gas header pressure control before and after deploying the APC solution. Benefits audited in this small 90 KBPD refinery were more than $2.1M per year.
[sidebar id =4]
Sulphur complex control
Sulphur complex, which is made up of multiple lines and equipment is a very important part of the refinery and must work properly. Any upsets in the complex, like ammine absorbers/regenerators, sour water strippers (SWS), sulphur recovery units (Claus), tail gas treaters (TGT) and incinerators, has a significant and costly effect on the overall refinery and on the environment. This is where APC applications can provide benefits.
For example, a constrained Claus unit should maximize feed whenever possible as it permits increasing load to profitable desulphurization units or even the overall refinery. The unit should work “well”, recovering as much sulphur as possible and maximizing conversion through a Dew Point Margin minimization. The unit should also minimize O2 consumption and all other specific utilities consumptions (fuel, EE, and downstream TGT unit load).
A key point is the Dew Point Margin reduction as this requires explicit Dew Point control. Conversion is limited by reaction equilibrium. The liquid sulphur forms at dew point in condensers, but if it happens on catalyst it can reduce activity (reduces conversion), increase pressure drop (increases pressure in the boiler which is usually one of the major constraints) and condense Sulphur in catalyst pores (shortens catalyst life and requires expensive regeneration or rejuvenation procedures).
[sidebar id =5]
On the other hand, a Dew Point Margin that’s too high will reduce conversion, increase energy consumptions (temperature is too high) as well as increase downstream TGT consumptions and loads.
Best in class refiners are able to maintain around a 10-15 °C Dew Point Margin but it is not uncommon to see sites where the margin is greater than 35 °C. This is a large margin, paid heavily with reduced conversion and increased consumptions. Not to mention the case where a refinery is sulphur limited, causing a loss in money measured in multiple millions of dollars per year. Building first principle Dew Point inferentials permits to address these issues. Not an easy task since sulphur condenses in catalyst pores and a capillarity condensation effect occurs. The Dew Point Limit is a function of many variables, including feed quality, air flow, air humidity, pressure of the system, reactor temperatures and more. These variables affect the partial pressure of sulphur in a vapour phase over the catalyst and, consequently, the related saturation temperature that is already reduced by the presence of inert gases (N2, H2O, not reacted H2S, etc.). The accurate first principles Dew Point inferential can be built, but it requires appropriate competence and integration of both APC and kinetic modeling technologies.
Achievable benefits can vary significantly depending on the specific layout and constraints distribution, but benefits are typically between $0.8 and 1.1 million per year for a small 100 KBPD refinery (not considering the case when the refinery is sulphur limited where benefits can be measured in multi-million dollars per year).
Steam networks control
A Steam Network can be quite complex with multiple pressure headers. The major components include steam headers, steam imports/exports, boilers/HRSGs, gas turbines, steam turbines, let-down valves and vent valves.
By implementing APC technologies, facilities can experience a number of benefits. These include:
- Improved steam headers pressure control by manipulating boilers, turbines, and let-downs in order to stabilize operations and maintain the required steam production levels
- Minimized downgrading steam through let-down valves mainly by manipulating turbine loads, extractions and, whenever possible, boiler loads
- Minimized vent flows by manipulating turbine loads and extractions and, whenever possible/convenient, boiler loads
- Control of all constraints, including emission limits during the transition, while optimizing boiler load changes
- Optimization of boiler and gas turbine loads, maximizing the most efficient machine utilization (as defined by a higher level closed-loop rigorous optimizer)
APC applications need to cover the all steam production side and meet steam demand as required. They permit to address significant issues like the one depicted below where the HP steam let-down valve and flow are reported. More than 10 t/h of HP steam is downgraded during normal operations in this example.
[sidebar id =6]
In this specific case, benefits achieved by deploying the APC solution on this steam network were above $1.5 million per year if counting only those due to reduced let-down flows and vent flows. A more comprehensive and efficient solution can be built where a model-based optimizer is also used to drive the APC system based on overall economics and efficiencies. The figure below shows a very simple case where an optimizer suggests swapping the load between two boilers to achieve around $3,000 per day of benefits. Many opportunities like this example exist in a Steam Network.
[sidebar id =7]
The path forward to a best in class APC program
APC benefits on major units are well understood and accepted. However, to achieve best in class performance in margins and operational excellence, organizations must expand their APC footprint to secondary units. Organizations often do not fully understand the benefits that are available to them and/or face a shortage of engineering resources to capture APC benefits from secondary units. APC engineers often have a significant workload maintaining existing applications. This is often due to the use of traditional APC technology. Advances in APC software like Adaptive Process Control empowers end users, automates many tasks, adapts and calibrates models in the background with no disruption to operations and provides increased robustness. All of this can help reduce the APC maintenance workload and maintain peak APC performance with ease. Advances in APC technology can enable organizations to shift focus from just maintaining existing APC applications to deploying additional APC applications, capturing benefits from secondary units and enabling a best in class APC program.
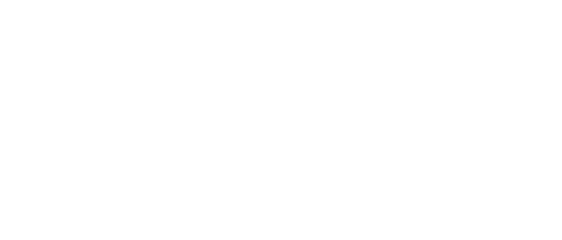
Leaders relevant to this article: