Dave Perkon is technical editor for Control Design. He has engineered and managed automation projects for Fortune500 companies in the medical, automotive, semiconductor, defense and solar industries.How do you duplicate a legend? Very carefully.
The oldest registered distiller in the U.S., Jack Daniel's Distillery, was running at capacity and landlocked at its one distillery in Lynchburg, Tenn. Not only was expansion required to meet demand, it also needed a new facility because there was no room to expand at its current location.
So in 2014, Jack Daniel's collaborated with Cross Integrated Systems Group in Knoxville, Tenn., and Siemens Industry to design and build a greenfield plant to increase whiskey production. Key to the new plant's success was selection of Siemens Simatic PCS 7 distributed controls, as well as a virtualized computing architecture, wireless HMIs, and Simatic Batch and Route Control software to fully automate the process, reported Juan Merizalde Carrillo, project engineer and processing manager at Jack Daniel's parent company, Brown-Forman Corp. in Louisville, Ky.
The existing distillery's controls consisted of a Siemens APACS+ distributed control platform with PCS 7 human-machine interfaces (HMIs) and 11 APACS controllers managing 4,000 I/O. By contrast, the new distillery's PCS 7 controls can run the whole facility at full capacity with just four controllers.
Carillo and Jeff Clark, PhD, lead systems integration engineer at Cross, described the design and startup of Jack Daniel's Distillery 2 (JD2) at the Siemens Automation Summit 2016. They reported that implementation of PCS 7, virtualization, hardware and software such as Simatic Batch and Route Control led to control design advantages, operator and maintenance improvements and system flexibility. In recognition of their project's success, Jack Daniel's and Cross were even recognized with a Siemens Customer Excellence Award during the Summit.
Celebrating 150 years of whiskey making this year, Jack Daniel's produces more that 14 million cases of whiskey products that are sold in 160 countries. The distillery's 575 employees produce five primary brands, including Old No. 7 Black Label, Single Barrel Select, Gentleman Jack, Tennessee Honey and Tennessee Fire.
New plant, old philosophy
"When we started meeting with the engineering, operations and maintenance groups and analyzed our current situation, it was obvious we needed to expand to meet current and future demand," said Carrillo. "At this point, with every drop of Jack Daniel's whiskey made in a single distillery and no room to expand, it was time for a second distillery."
[sidebar id =2]The team set out to build an automated plant that kept Jack Daniel's existing operating philosophies in place, but would also be scalable, flexible and modular enough to add more capacity in phases. They also wanted to implement new technologies as needed, such as HMIs, instruments and wireless equipment. And, though JD2 had to be in a new location, they wanted to connect JD2 and JD1.
"We wanted to make sure the first drop of whiskey coming out of JD2's stills was Jack Daniel's-quality whiskey, and that the new distillery could do it for at least the next 150 years," said Carillo.
Best-practice controls—virtually
Once its goals were established, the team selected Siemens as the automation vendor, which allowed for a common vendor for JD1's APACS+ and JD2's new PCS 7 system, including installation and configuration of operator stations and Simatic software. Siemens also helped set up JD2's new virtual server and virtual machine (VM) workstation as part of its Simatic Virtualization as a Service (SiVaaS), which enabled the new plant to start up more quickly.
Virtualization at JD2 was established with two identical host machines. Each machine has an operator station (OS) server, Batch server, Route Control server and an engineering station providing redundant pairs for all critical functions. Each host also has different OS clients that can be accessed by the virtual machines.
For its thin clients—the operator interfaces—JD2 uses several options. They included strategic placement of touch-panels and iPad tablets. "A big thing we like about the thin clients is that they provide restricted access to the physical hardware. They also are inexpensive to replace compared to standard machines," said Carrillo.
Another advantage of the virtual system is maintenance. "The engineering station is also a thin client, and serves as a management console for the system." continued Carrillo.
Also, Siemens Scalance wireless access points provide WiFi connectivity throughout the plant. "Wireless access allows iPads to be used as thin clients throughout the distillery,” said Carrillo. “This is very useful during commissioning, operation and maintenance of the system. As a thin client, they can also run Simatic Batch and Route Control," he said.
Software development
To develop and deploy all the software for JD2, Clark reported that Cross worked closely with Jack Daniel's from the start of I/O list development through commissioning and startup. User requirements and process descriptions were used to develop interlocks, automated logic, equipment modules and necessary route control to run the process along with required batch recipes.
"The programming from the old facility was used as much as possible to try to maintain the old distillery's operating philosophies," noted Clark. "However, the new facility had significantly more automation capabilities that had to be considered. The question was, how are we going to utilize the most potential of the new automation capabilities while maintaining the integrity of the whiskey?"
Route Control software, for example, is used to facilitate transferring product between processes and the multiple units within each process. "Route Control is used for material transfer – it provides increased flexibility, easy expandability and reduced configuration time," said Clark. The plant's routes are actual-built as a series of partial routes or short segments of a route, which reduces configuration effort.
Batch and Route Control software also made the operators' lives easier, which is one of Clark's favorite accomplishments. "Routes are triggered by sequential function charts (SFCs)," noted Clark. "The operator can run the SFC from the HMI, view the route sequence, see what devices are being controlled on the active route and what actions are made. Though it's not needed very often, it's a great troubleshooting tool."
Whiskey-making is clearly a batch process, and Simatic Batch software easily met Jack Daniel's requirements. "Simatic Batch was configured with 14 different recipes for whiskey and clean-in-place batches," added Clark. "It provides future expansion and ease of master recipe modification. Simatic Batch provides tighter control of the entire process, and yet it has the built-in flexibility for the operator to easily change individual orders if required."
In a final analysis of their new plant project, Carillo and Clark reported that JD2 still makes the same Jack Daniel's Old No. 7 black label Tennessee sour mash whiskey, but the new automation system with PCS 7 controls and Batch and Route Control software is delivering many added benefits. They're built for expansion and designed for the future, while virtualization and wireless access makes work easier for operators. Further, JD2's new production processes achieve improved consistency, even as whiskey production capacity increases.
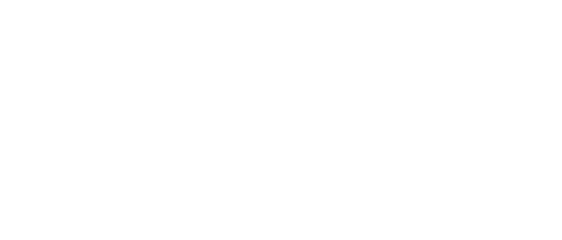
Leaders relevant to this article: