This article was printed in CONTROL's May 2009 edition.
By Greg McMillan
I can envision a wireless world, but is wireless control ready for prime time in industrial processes? Is wireless reliable, secure and fast enough for process control? Will battery life be long enough? What is the motivation other than to be part of a neat new technology?
Why Wireless?
The savings in installation costs is the most obvious benefit for using wireless devices. My six years in E&I construction makes me more appreciative of the potential savings. I can remember sorting through rolls of schematic diagrams, installation and termination details, and the drawings for the fabrication and layout of the cable tray, conduit, junction boxes and interface panels. It took the best electrician supervision to get the whole picture right and correct the inevitable design and drafting mistakes. Projects routinely used a factor of three to four times the instrument cost to estimate the total commissioned cost of an instrument, most of which was associated with design, implementation and checkout of the wiring system. The other biggest part was the making the process connection. One leading chemical company and some plants have standardized on the elimination of sensing lines and sample lines by using of inline meters for flow and liquid analysis and connecting differential pressure or pressure transmitters directly to the process pipeline or vessel. While the original goal was to improve reliability and maintainability, since most of the performance problems originate in the sensing and sample lines, it turned out the side benefit of savings in installation cost was impressive as well. The combination of direct process connections and wireless communication can drop the total commissioned cost for a transmitter to less than twice the hardware cost for large projects where there is an economy of scale.
But for me, cost takes a backseat to performance. So what are the functional benefits of wireless? One possibility is that more instruments can be used to provide a better view and understanding of the process because of portability.
In the old days, we added extensive standardized pressure and temperature gauge pipe connections and bought an assortment of gauges. The field operator would pick a gauge with the right range and connect it to the process to better track down problems. The gauges provided information on the source and profile of changes in plant performance.
For distillation column control, we sought the tray that had the largest and most symmetrical change in temperature for a change in the reflux-to-feed ratio and, in some cases, the steam-to-feed ratio. While simulation programs could give you some insight, that best tray was not found until after startup. Additionally, the best tray would change with process improvement and debottlenecking projects. More tray temperature sensor connections were provided than used, with the expectation that the best points for monitoring and control needed to be found online.
We started to use packaged equipment on skids significantly in the 1990s to service multiple-unit operations and meet multiple needs with reduced installation and operating cost and time. There is an increasing variety of skid operations. A significant example is the single-use bioreactor (SUB) with a disposable plastic liner that eliminates the bioreactor sterilization step time and cost. Originally used in pilot plants, the SUB has greatly increased in size to the degree where the SUB can be used for the commercial production of high-value-added biopharmaceuticals. Figure 1 shows a 100-liter SUB skid with WirelessHART pH, temperature and pressure transmitters and a lab-optimized DCS for research and development.
Today, we have the advantage of wireless transmitters to provide the flexibility and portability needed for process analysis and diagnostics, process control improvement and packaged equipment.
For the E&I plant people in the trenches, the time spent troubleshooting instruments is a primary concern. Even if the wiring is not the source of the problem in the instrument signal, it needs to be checked out. When grounding and noise problems occurred, they were difficult to track down. Signal shielding and grounding standards were developed in the 1970s. However, even systems designed per the standards developed rampant problems with electromagnetic interference (EMI) when inexpensive inverters for variable-frequency drives (VFD) were installed. It took years for some plants to sort out their VFD-induced EMI problems.
The instrument suffering the most from ground problems for the last 50 years is the pH transmitter. I wish I had a dollar for every spike I have seen or users reported in a pH trend chart. The spike is usually caused by ground noise. In some cases, the spikes disappear when the electrode is removed and inserted in a beaker, indicating one side of the ground loop is through the process. In most cases, the ground noise is gone when the electrode is left in place, and a lab meter is connected to the electrode cable instead of the transmitter wiring. This indicates the other side of the ground loop is somehow established in the transmitter wiring. Figure 2 is a trend chart of a WirelessHART transmitter and a wired conventional pH transmitter on the SUB in Figure 1. A spike from ground noise appears in the wired pH, but not the wireless pH.
Figure 1
Single-use bioreactor with wireless transmitters and a lab-optimized DCS.
Most of the new measurement diagnostic research and development is going into wireless transmitters. For example, wireless pH transmitters have improved glass impedance measurement, enabling better glass diagnostics, finer measurement resolution and the setup for smart electrodes that have calibration history and electrode health embedded. If you want the latest advances in measurement technology, you need to consider wireless.
Figure 2
Spike in wired pH from ground noise not seen in wireless pH.
Security and Reliability
The WirelessHART protocol is a good example of an inherent sophisticated security mechanism design. Specific keys are required at both ends for a device to join the wireless mesh network. Rolling encryption protects devices as they communicate. For more information on security checkout the November 2008 Control Talk column “Secure Answers to a Risky Business.”
WirelessHART networks are self-organizing and optimizing, making setup surprisingly fast, easy and efficient. The mastermind is the network manager, which determines the routing to maximize reliability and performance. The number of hops is minimized. Routers and line-powered devices are used preferentially in the route if more than one hop is required. A time slot is allocated each second for communication by each device. Channel-hopping and blacklisting channels with interference cuts that interference to a minimum.
So, we have assurance the security and reliability of the network is solid. But is the battery life and speed good enough for closed-loop control? The answers can be found in the communication rules and the PID algorithm.
Battery Life
Battery technology is on a growth curve that will accelerate. With present-day technology, battery life is estimated to be three to five years for a wireless transmitter that makes a measurement every second, but only transmits every 15 seconds. If we can increase battery life, the total drift in a measurement signal will need correction before the battery wears out, at which time it would be convenient to replace the battery.
WirelessHART communication rules for extending battery life are simple. The measurement sensing is kept relatively fast at once per second. Exception reporting is used for communication where a new measurement is transmitted only if the change in the measured process variable since the last transmission exceeds a resolution setting. Periodic reporting is used as a backup with a refresh time that is the maximum allowable time between successive transmissions.
For the WirelessHART pH transmitter in Figure 2, the resolution setting was 0.001 pH, which is much finer than the desired 0.02 pH tightness of control quoted for bioreactors. Even with this overly fine resolution setting, the number of communications was reduced by 60% for this pH transmitter, compared to periodic reporting every second. The resolution setting should be larger than the noise band so that the communication frequency is not based on noise. At a minimum, the resolution setting must be less than the desired control band (peak-to-peak amplitude of allowable fluctuations). To handle fast process disturbances, the measurement resolution should be finer than 1/5 of the control band. The limitation for tightness of control may depend more upon the resolution of the control valve, which varies from 0.2% to 2.0%.
The damping adjustment can be used in the transmitter to filter out measurement noise so that the resolution setting can be smaller, provided the setting does not delay the recognition of fast disturbance excessively. The use of too much damping can be misleading because the trend will look smoother even though the true unfiltered process deviations are greater. Check out the Control Talk column “Sensible Sensor Speed” on page 71 in this issue for more info on damping adjustment and consequences.
So, we possibly can save money and get smarter and more accurate measurements with a reasonable battery from wireless devices. But can we control as well as we need to with the variable update times from exception reporting?
Control Solution
One might think a dead-time compensator would help the traditional PID deal with the dead time from a larger measurement sample time. However, these dead-time compensators are notoriously sensitive to a mismatch between the actual process dead time and the estimated dead time used in the compensator. The loop dead time from unsynchronized digital devices, control valve stick-slip and transportation delays is extremely variable and can at best be estimated after the fact.
The control solution for WirelessHART requires no estimate of dead time and is more robust than a traditional PID. The PID execution is kept relatively fast (once per second). The contribution of the proportional mode is computed every execution. The proportional action every execution provides a good setpoint response for a PID structure with proportional action on error. The contribution of the integral and derivative mode is only computed when the measurement has changed per the resolution setting of the wireless device. Furthermore, the time used in the integral and derivative mode calculations is not the execution time, but the elapsed time from the last measurement update.
The use of the elapsed time in the integral calculation and a reset time the same as the process time constant provides an integral correction that is equal and opposite to the process response in the elapsed time. Even if the process time constant changes, making an integral correction only when there is update eliminates the extraneous ramp of the integral mode in the traditional PID acting on old information. The suspension of integral action until there is new information also helps the PID deal with a valve that is momentarily stuck, provided position read-back is used for dynamic reset limiting.
The use of elapsed time instead of PID execution time in the derivative calculation spreads the change in the process over the elapsed time, rather than taking it to all occur in the single execution time. This more intelligent rate action eliminates spikes in the controller output that would occur in a traditional PID when there is an update. Also, the enhanced PID smoothly resumes control upon reestablishment of communication after a measurement failure eliminating the sharp spike seen in a traditional PID.
Test results show that the enhanced PID algorithm for wireless devices has benefits for any loop with a significant sample time or a significant delay due to resolution limits, such as valve stick-slip. For example, at-line analyzers have a large sample time due to sample transportation and processing delays and analysis cycle time. In control studies, the wireless PID greatly stabilized the glucose control of a bioreactor which had at-line analyzer sample time delays that varied from six to 12 hours. The improvement is greatest for self-regulating processes and controllers tuned for maximum performance.
Summary
With the wireless PID algorithm, a comprehensive battery life management approach, exception reporting, and a secure, reliable self-organizing and optimizing network, wireless process control is ready for all but the fastest processes, provided the transmitter resolution settings are right for the application. Use of wired devices will be relegated to processes requiring scan and PID execution times much faster than once per second, such as compressor surge and pressure control.
Thanks to Scott Broadley for providing the bioreactor and sponsoring the tests of wireless process control. Thanks also to Trish Benton for setting up the cell culture and Michael Boudreau for running the tests.
Greg McMillan is an ISA Fellow, an authority on pH and APC and a member of the Process Automation Hall of Fame.
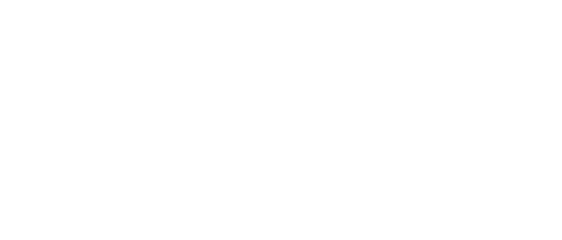
Leaders relevant to this article: