By Margaret Walker, Ed Sederlund, Jerry Gipson and Eric Cosman, The Dow Chemical Company
Innovation has always been at the heart of The Dow Chemical Company (Dow), Midland, Mich., and today it is the essence of its stated mission “to constantly improve what is essential to human progress by mastering science and technology.” To achieve this mission, we are committed to the principles of sustainable development and to achieving the triple bottom line of economic, social and environmental progress. These principles form the basis of our philosophy and approach to process automation.
For more than 100 years, Dow has been striving for true “operational excellence,” long before the term was coined by industry analysts. Over the past 30 years alone, we have evolved a standardized, redeployable process control strategy that supported our goals of overall consistency, productivity improvements, global operating discipline and innovation—all while maintaining high safety performance.
Indeed, consistency and sustainability are the foundation of that strategy. As a global company, it’s important to operate facilities in the same way every single day to achieve consistently high quality, process reliability and repeatability of best practices. Consistency and sustainability are paramount to global competitive advantage, enabling us to drive down costs while earning us the right to grow.
In the first article in this series, “The MOD Squad: Process Automation at Dow,” we described how our process control strategy led to the development of a series of proprietary process control systems, culminating in the MOD 5. That system—still in use today—has several capabilities that are not commonly available in many commercial systems. Each of these capabilities was developed in direct response to a specific business need. As a result, the application of this system has resulted in tremendous productivity benefits.
However, in early 2000, due to the speed of changing technology, we realized it would not be cost-effective to continue to invest in proprietary hardware and software systems. We needed to focus on our core manufacturing business without losing the advantages that we had gained.
After a detailed analysis of the capabilities of the MOD system, we defined a set of high-level criteria that we consider essential to any commercial process automation system. This process was described in the second article in this series, “Process Automation at Dow: Part 2.” Each criterion corresponds to a specific value that we have achieved with our proprietary MOD system.
Reduced Downtime Through Automation
One criterion for process automation is directly related to increasing process availability. According to a November, 2006, report from ARC Advisory Group, about five percent of production in the process industries—valued at $20 billion a year in revenues—is lost to unscheduled downtime. Most of this, says ARC, could be readily avoided through improved automation capabilities.
As part of an ongoing collaboration with Dow, industrial automation system vendor ABB recently introduced the “Load-Evaluate-Go” feature for its industrial IT System 800xA. The newest version of System 800xA includes new engineering functions that enable one to make changes to a copy of the running program, and then load that copy into the running production system with the old version of the program. This, in turn, makes it possible to evaluate the impact that such changes would have on the production process by examining the differences between the “old running program” and the intended “new program.” It is then possible to choose to commit to the new program or back out of it with the old program still running, make necessary changes, and go through the process again. This capability provides two key benefits. First, it significantly reduces the risks associated with making application changes in the running process. Second, it improves overall efficiency by avoiding production stops, missed or delayed product deliveries, and costly downtime.
Load-Evaluate-Go complements other jointly developed elements of System 800xA, including the innovative System 800xA High Integrity combined control and safety option. With embedded safety and control within the same flexible architecture, it is possible to combine control and safety functions within the same controller, or to keep control and safety functions separate within the same system. This improves process availability while reducing risk to overall plant operation by providing a common high-integrity system environment for production control, safety supervision and production monitoring.
A Collaborative Foundation
Well before any real collaborative development took place, however, the foundation for a true collaborative relationship needed to be established. The beginning of this process was described in the third article in this series, “Collaborative Process Control: The Dow/ABB Story.” Over time, Dow and ABB have forged a relationship that nurtures ongoing development activities. This relationship consists of four key elements of collaboration:
- Shared vision
- Trust in each other
- Open communication
-
And perhaps most important, a willingness to confront each other and use conflict constructively.
With this foundation in place, it was possible for both teams (Dow and ABB) to work closely together to build a strong collaborative relationship that transcended all levels of our mutual organizations and provided the innovative environment needed to develop successful solutions.
The Elements of Collaboration
In working with ABB, Dow quickly discovered that we shared the first element of collaboration: a shared vision. ABB’s vision of automation was completely compatible with ours. ABB staff have been very open with us on the topic of system strategy and willing to capture our safety control philosophy and incorporate it into its commercial offering. ABB also had the dedicated resources for ongoing system and technology development that we could not possibly have as a manufacturer, as well as centers of excellence for safety and bench strength in systems engineering. Furthermore, ABB showed a willingness to adapt its development program to accommodate our desired capabilities.
Our vision for automation remains that of using a commercial system that meets all of the criteria for operating discipline. At the same time, this system must be successful in the marketplace to keep it cost-effective and to enable the rest of industry to benefit from Dow’s leadership in automation. We did not want another proprietary solution developed exclusively for Dow. We wanted the rest of the industry to have the opportunity to benefit from what we had learned with our unique approach.
The second element of collaboration is trust. Our collaborative relationship has required tremendous organizational commitment from all parties. As we worked together, we found that both of our organizations had very similar cultures that fostered mutual respect for each other, leading to shared trust. That respect and trust was pervasive throughout the organizations, from the executive level management to the development teams to the field engineers.
Even in some of the early implementation projects, our technical and engineering teams worked so closely together that when one encountered a group of them, it was difficult to tell who belonged to Dow, and who belonged to ABB.
Open communication is also an essential element of collaboration. Team members from Dow and ABB make every effort to stay in touch with each other on a continuous basis and have organized working groups to maintain a good rapport through a combination of electronic media and face-to-face meetings. Each party in such a collaborative effort must have the mindset that it is part of the same whole, so that collectively, we are all part of the same team.
While you can do all the team building you want, collaboration is really about bringing together diverse perspectives, because this is really what stimulates creativity and out-of-the-box thinking. As mentioned, this requires an environment of trust and open communication to not only express one’s opinions, but also to debate and discuss openly and agree upon potential solutions. A mutual focus on the details and continuous measures of forward progress are also essential to stay on plan. This is how constructive and successful change takes place.
To summarize, the key elements of any successful relationship include a shared vision, trust, communication and the willingness to confront each other. All are all critical components of the joint development process.
In the classical customer/vendor relationship, the vendor asks “what do you need?” and then goes away, reappearing later to present “the answer.” We, however, chose a different, side-by-side parallel approach that has ultimately delivered against our goal.
The Dow and ABB relationship has become stronger with the passage of time. When we began, each company had its own view of the world of automation. These visions were compatible, but different in some respects. Dow’s MOD 5 FORTRAN-like language and ABB’s object-oriented programming appeared to be on a collision course, with two different automation suppliers’ philosophies. This collision, however, began the long process of actually integrating the ABB System 800xA product into Dow as the preferred and standardized automation platform. Trust and collaboration evolved as each company learned more of the capabilities of the other, and thus began the process of listening and acknowledging the possibilities of the others’ ideas. Today our relationship is much more than supplier and customer, and we strongly believe that our working relationship will continue to generate enhanced value for Dow and ABB, for industry and for the marketplace.
Closing Thoughts
As the collaborative development relationship between Dow and ABB continues to grow, the process industries stand to benefit from the commercial availability of even more capabilities that support Dow’s operating discipline. In our ongoing quest to share its innovative approach and best practices for the greater good of the entire industry, Dow has collaborated with ABB to transform key elements of our operating discipline into commercial product features. We will continue to make these widely available so process manufacturers can operate their own facilities more safely and productively. This innovative relationship and collaborative business and development effort provides a win-win-win scenario for Dow, ABB and customers in all process industries.
Margaret Walker, Ed Sederlund, Jerry Gipson and Eric Cosman are Dow emploees.
The Dow/ABB Story, The Story Continues
In 2006, the first three articles in this series appeared. The current article is a wrap-up, including lessons learned over time as the collaboration has continued.
The three earlier stories can be found as follows:
- Article 1—“The MOD Squad: Process Automation at Dow,” Control, February, 2006.
- Article 2—“Process Automation at Dow, Part 2,” May, 2006.
- Article 3—“Collaborative Process Control: The Dow/ABB Story.”
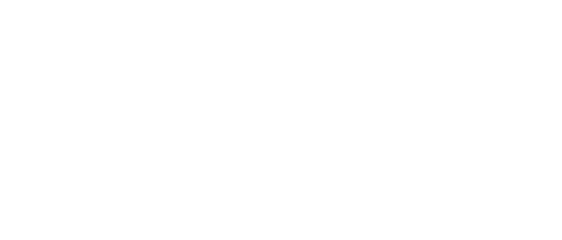
Leaders relevant to this article: