A |
T BRITISH PETROLEUMS PTA (Purified Terephthalic Acid) PLANT in Wando, S.C., managers are facing a dilemma familiar to their counterparts at thousands of manufacturing facilities throughout the country: do more with less.
BP is investing heavily in plant construction in China, so our objective is to lower costs and increase our availability. We need to use what we have and use it better, says A.J. Lambert, an instrument and electrical reliability specialist with BP.
One way plant personnel are achieving that goal is by using a previously underutilized technology that is providing them with a remarkably detailed view of conditions throughout their plant and the ability to reduce asset management/maintenance costs.
The silver bullet thats generating these benefits: the HART Field cCommunications protocolProtocol. Through the use of HART diagnostic information, this BP plant is saving approximately $300,000 per year in just maintenance and production costs alone, says Lambert.
Feel the Power
Of course, not every plant will attain such dramatic results, but most users can achieve all, or nearly all, of the functionality they seek by tapping into the proven power of the HART-enabled field devices they may already own. As a result, most of the benefits they achieve through the use of HART drop right to the bottom line. Few automation projects are as easily justified economically as that.
HARTs exceptional value to process manufacturers lies in its ability to simultaneously communicate an instruments primary variable via a standard 4-20 mA analog signal and and up to three secondary valuesadditional process variables and plus diagnostic information via digital signals on the same wire. Initially, HART was initially embraced by maintenance staffs who were delighted to be able to use handheld communicators and calibrators, such as those made by Meriam Process Technologies or Emerson Process Management and , and take them into the field. All they had to do was attach them to any HART-compliant instrument--regardless of manufacturerand they were immediately able to retrieve critical information about an instruments condition, its health and its range, as well as perform calibrations, document them and obtain much more digital information besides.
Since then, manufacturers have developed a wide range of new intelligent products and added HART capabilities to existing ones, providing even greater benefits to a broader base of users. For example, field device makers such as Siemens differentiate themselves by communicating additional HART data that are unique to the companys instruments. Siemens pressure transmitters have the ability to monitor and store data on the highest and lowest pressures experienced by the entire instrument, the instruments pressure capsule and its electronics, says Lou DiNapoli, marketing manager for the companys pressure and temperature transmitters.
All users have to do, says DiNapoli, is use a HART handheld device or our Device Description Language-enabled Process Device Manager (PDM) software to get that information, which is highly useful in diagnosing process problems. If you use someone elses equipment and software, you just need the Device Description for our instrument.
Sophisticated Asset Management
In recent years vendors have developed sophisticated asset management software packages, including Yokogawas Plant Resource Manager (PRM), Siemens PDM, Emerson Process Managements AMS and Honeywells Asset Manager PKS, that enable maintenance engineers to view, track and analyze the condition of instruments remotely. In this situation, data from a device is split into separate analog and digital signals. The analog signal, carrying the primary variable, is routed to the control system, while the digital secondary values and diagnostic data are conveyed to the asset management systems.
Asset management systems and their ability to use HART data are proving enormously beneficial as numerous users will attest.
BPs Wando plant started tapping the full potential of HART about five years ago, when it installed Emerson Process Managements ValveLink software to gain diagnostic information from its approximately 125 most critical control valves. Among the areas in which the plant has cut costs is in valve maintenance during planned shutdowns.
Before using HART, we would pull out 35-50 valves for maintenance during shutdowns every two years, says Lambert. There might have been a work order or some concern about a particular valve, but we really didnt know what might be wrong with it. As a result, wed spend a lot of money and time. Now, with more information from ValveLink and HART, we pull only five or six valves during a shutdown. And we have a lot more information about why were pulling it. Our diagnostic system can show us when a problem assumed to be in a valve really isnt, but is perhaps somewhere else in the process. In other cases, were able to see potential problems in valves before they become serious.
A senior engineer for field instrumentation with another major oil company refiner says that digital HART instrument data, routed back to the refinerys asset management system, has enabled it to improve its processes as well as realize savings on maintenance.
According to this petroleum industry source, Right after we started capturing this data, we were picking up diagnostic alerts for valve travel deviations, air pressure problems on valve actuators and other variances., he says. We were skeptical at first, but when we investigated those alerts, we discovered that we had actual problemsbent positioner feedback rods, filter regulators that were either failing or malfunctioning, leaks in diaphragms and other problems. So what we learned from our HART-enabled asset management system was that our system was still operating, but it was not controlling the process as well as it could, and that we might be facing pending failure because of these problems. We were able to correct these problems before they had an impact on the process.
Petro-Canada, which is implementing projects at its Montreal and Edmonton refineries to reduce sulfur in its gasoline and diesel fuels, also will use HART data from for troubleshooting on valves and field instruments, says Pat Castellino, an engineer with the companys process technology and reliability group.
I expect a manpower reduction in the startup phase of the project and then on a lifecycle basis, he says Castelino, when asked about potential benefits stemming from the use of HART data. We feel that the additional information we incorporate into our asset management solutions will help us establish more effective predictive maintenance practices.
Several factors make HART solutions relatively easy and cost-effective to implement. First, HART does not require a costly rip and replace strategy. The HART protocol runs on standard wiring that most plants already have in place and, as mentioned, there are millions of HART-enabled devices already in use. Often, field instruments that are not HART-ready can be easily and inexpensively upgraded.
Because HART represents an enhancement of the standard 4-20 mA analog field communications standard, there is no need for companies to undertake major retraining programs. Courses offered by HCF, vendors and other sources generally provide all the background information plant personnel need to use HART Effectivelyeffectively.
In addition, HART network architecture is simpler than that of most all-digital fieldbus protocols, making it the ideal option for many plants.
If Im putting in a 4-20 mA system with HART, the engineering is very simplified; its basically a matter of routing wires from the control system to the final elements, says Petro-Canadas Castellinothe major refiners senior engineer. Designing a HART system doesnt require a great deal of specialized knowledge concerning matters such as the number of devices to assign per segment, to which segment should each device be assigned, failure modes on loss of communication, surge protection, signal reflections, power and signal-attenuation calculations.
"When I increase the amount of engineering that has to go into a system, Im increasing my opportunity for human error, and those are things Id like to avoid., he adds.
Easy and Effective
In addition to being relatively easy and cost-effective to implement, plants can adopt HART very gradually and realize benefits, even on a small scale. For example, many users get their first experience with HART by commissioning instruments on the bench in maintenance shops. All thats required is a PC equipped with DDL-enabled asset management software and an interface between the computer and the field devicetypically a HART modem.
Tom Holmes, president of HART modem manufacturer MACTek Corporation, says there are significant advantages to using a desktop or notebook computer for bench or field configuration of devices rather than using handheld configurators.
What is HART? In 1993, the HART Communication Foundation (HCF) was established to provide worldwide support for application of the Highway Addressable Remote Transducer technology or HART Field Communications Protocol. HCF owns the HART technology, manages the protocol standards, and ensures that the technology is openly available for the benefit of the industry. The ARC Advisory Group, Dedham, Mass., estimates that, of the approximately 40 million field devices installed worldwide, 26% percent are HART-enabled, making it the mostly widely used protocol for smart field instrumentation. |
Few industry observers question that, in the long run, the process industries will eventually migrate to fieldbus protocols. But dont even think about mothballing your HART devices anytime soon. HART is probably the most economical and best solution for modernizing existing plants.HART combines the reliability and robustness of todays analog signal with the power of tomorrows digital field network. Considering the millions of HART devices already installed, the most responsible action for the industry is using HART to its full potential.After all, people are still using pneumatic devices today, says Moore Industries Emmett. And if you think about all of the millions of HART instruments already installed around the world, you can be sure that HART is going to be with us for at least the next decade or two.
Latest from Home
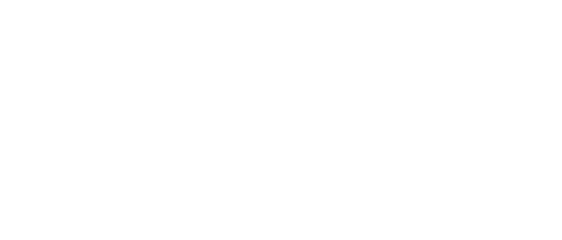
Leaders relevant to this article: