Not knowing the implications of the PID Form in an existing control system being migrated or the PID Form learned in a University course can cause gross errors in the tuning parameters and potential instability. The PID Form predominantly used today is not the Form in most of the controllers installed before the 1990s and is not the Form seen in most control theory textbooks. Here we alert you to the differences and consequences. An Appendix provides simple equations to convert between the different PID Forms and block diagrams in the time frame that are not available in the literature.
Various terms such as “Interacting”, “Non-interacting”, and “Ideal” are used often to describe a PID Form, which is confusing at best. The terms are often incorrectly applied. For example, the Wikipedia definition of the PID Ideal Form reflecting more of the theoretical view of the PID is drastically different than the ISA Standard Form also known as the Ideal Form. Not realizing the distinction can lead to integral and derivative settings that are off by orders of magnitude.
The two predominant PID Forms used today are the Series Form and the ISA Standard Form. Some Distributed Control Systems (e.g., Bailey DCS) and Programmable Logic Controllers (e.g., Allen Bradley PLC) offer the Parallel Form, which is the theoretical view of the PID that is often shown in textbooks. The so called Ideal Form in Wikipedia is this Parallel Form. Before we get more confused, how can one know which of these three Forms is in the control system actually being used?
One should check the supporting documentation and of the control system and verify with their supplier’s technical support the PID Form and the engineering units of the tuning settings or use an experienced PID consultant. One can also use the following checkpoints to get an idea of what PID Form is in the plant control system.
If the derivative mode contribution is computed in series before the proportional mode and integral mode contributions, The PID probably has a Series Form. If the proportional mode, integral mode, and derivative mode contributions are computed in parallel and the proportional mode gain has a multiplicative effect on the integral or derivative mode contributions, the PID probably has the ISA Standard Form. If proportional band (PB) is used, the factor is 100%/PB. If there is no derivative action, then the Series Form and ISA Standard Form should be essentially the same. If the mode contributions are computed in parallel but the proportional mode gain or proportional band does not affect the contribution from the integral and derivative modes, the PID probably has the Parallel Form. The integral and derivative tuning parameters for the Parallel Form are drastically different than what are commonly used in industry for PID gains values that are not near one (proportional band values not near 100%).
If you know enough to cut to the chase, see “Appendix K PID Forms and Conversion of Settings” for the equations and block diagrams. Normally PID block diagrams are simplified representations using Laplace Transforms. The block diagrams in the appendix are in the time domain reflecting the difference equations used in the implementation in a DCS. The block diagrams show the setpoint weight factors for the proportional and derivative modes (beta and gamma) that determine the different PID structures used. For example, a structure with derivative on process variable instead of error (PI on error, D on PV) would have a setpoint weight factor (gamma) that is zero. A “two degrees of freedom” PID structure (2DOF) would have adjustable gamma and beta factors. A future Control Talk blog will go into the definition and common uses of key PID structures.
Finally Appendix K seeks to provide the block diagram for the ISA Standard Form with setpoint weight factors and the positive feedback implementation of integral action, which provides the considerable advantage of external reset feedback (e.g., dynamic reset limiting) that is the key to the enhanced PID for wireless control and many other opportunities. Showing this in the time domain is no easy task since what is in the literature is the simple Laplace representation for the Series Form without setpoint weight factors and without feedforward control. With the help of ISA Mentor program protégé Hector Torres I developed Figure K.4 in Appendix K, which is my best attempt at a block diagram in the time domain that shows the implementation of these enabling PID features. In the enhanced PID there feedforward control and setpoint changes will affect the PID output whenever they occur. However, there is no proportional, integral, or derivative action until there is a change in the process variable. At this time the integral contribution is computed as a first order exponential response over the elapsed time since the last update with a time constant that is the filter time in the positive feedback path (reset time). The derivative computation uses the elapsed time as well.
Appendix K and the following text are excerpts from my Tuning and Control Loop Performance - 4th Edition to be published this December by Momentum Press. The book was principally reviewed by ISA Mentor Program participants Brian Hrankowsky, Danaca Jordan, Hector Torres, and Keneisha Williams.
PID controllers developed before this century used the Series Form (Figure K.2 in Appendix K) also known as the interactive algorithm where the derivative mode is computed first in series with proportional and integral modes. The Series Form minimized the cost and complexity of analog controllers. Early digital controllers retained this Form to give the same feel in tuning and enable the use of the same tuning settings. Pneumatic and many electronic controllers actually used a positive feedback implementation of the integral mode giving external reset feedback. The conventional integral mode principally appeared with the advent of digital controllers where an integrator could easily be implemented, coordinated, and limited.
In the Series Form the derivative mode result is the input to the proportional and integral modes. The advantage of the Series Form is that interaction factors prevent the effective rate time from becoming greater than effective reset time that could cause instability. As the rate time setting increases, the effective gain and rate time decreases and the reset time increases. The primary disadvantage of the Series Form is the lack of understanding of the interaction factors detailed in Appendix K. There is also greater magnification of noise from multiplicative effect of the derivative and proportional in series especially if there is poor measurement resolution and no signal filter or derivative filter.
Most modern PID controllers use the ISA Standard Form (Figure K.1 in Appendix K) also known as the Ideal Form. The contribution from each of the modes is computed in parallel with the proportional mode gain or proportional band affecting all modes. If the derivative action is zero due to structure or a rate time of zero, the ISA Standard Form and the Series Form are effectively the same if the implementation of the integral mode is identical.
The ISA Standard Form eliminates interactions between the modes in the time domain leading to the name "non-interacting". Often not recognized are the interactions between the modes in the frequency domain of ISA Standard Form. The Laplace transform of the ISA Standard Form and Series Form algorithm reveal interaction and no interaction, respectively between the terms. To reiterate, the label “non-interacting” is technically inappropriate in that while the ISA Standard Form is non-interacting in the time domain, this Form is interacting in the frequency domain. Correspondingly the Series Form algorithm is interacting in the time domain but non-interacting in the frequency domain. These are some of the reasons why I don’t like using the terms “non-interacting” and “interacting”.
In the Parallel Form (Figure K.3 in Appendix K) the contribution from each mode is computed in parallel but the gain tuning setting only affects the proportional mode. The tuning setting for Parallel Form integral and derivative modes are sometimes called integral and derivative gains rather than reset time and rate time. Since there is no multiplication by the gain setting for the integral mode, the units of repeats per minute or seconds per repeat are meaningless. The units for integral and derivative gains may not even be given.
The Parallel Form is rarely used in industrial systems but is commonly seen in control theory textbooks. Consequently the Parallel Form is mistakenly programmed into dynamic models for control studies and operator training systems causing potentially disastrous results if tuning settings are moved from simulations to industrial systems since the difference in integral and derivative settings can be quite dramatic. For PID controllers with gain settings far from one (proportional bands far from 100%), the Parallel Form reset and rate tuning settings could be an order of magnitude different than what would be used in the ISA Standard Form or Series Form.
Appendix K shows the equations to convert tuning settings between Series Form, ISA Standard Form, and Parallel Form. The user should use these equations paying close attention to units because some proportional mode tuning settings are a Proportional Band (PB) with units of % instead of a dimensionless gain. The integral mode tuning settings can be in repeats per time unit or the inverse that is time units per repeat for the Series and ISA Standard Form. For this inverse, the setting is simply given in time units instead of time units per repeat. The derivative mode setting is in time units. The time units for the integral and derivative mode tuning settings can be minutes or seconds. In the book Tuning and Control Loop Performance - 4th edition, the ISA Standard Form is assumed and used to generate the test case results. The proportional mode tuning setting is a dimensionless gain. The integral mode tuning setting is seconds per repeat (simply given as a reset time in seconds). The derivate mode tuning setting is a rate time in seconds.
The beta and gamma factors in the block diagrams are setpoint weights for the proportional and derivative modes in terms of setting PID structure. The inverse of the alpha factor for the derivative mode is the fraction of the rate time that becomes the time constant of a filter applied to the derivative mode input. If the filter is missing or the factor is zero, the derivative mode output can be a full scale spike for a step change in the mode input. Alpha factors range from 8 to 16.
Hopefully, this knowledge will help your PID Form to not be a trick but more like a treat.
Continue Reading
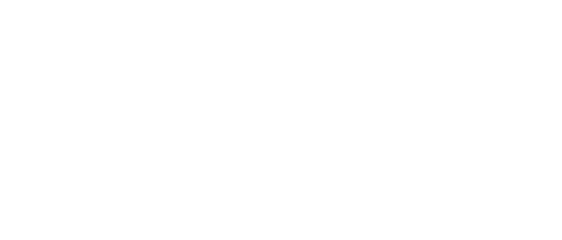
Leaders relevant to this article: