Siemens Automation Summit: US Manufacturing Renaissance
Featuring Patricia Panchak, editor in chief of Industry Week, Raj Batra, president of Industry Automation Division, Siemens Industry Inc., Jerry N. Gipson, Jr., retired Senior Technology Director for The Dow Chemical Company and immediate past chair of Fiatech's board of advisors, and Bonnie Knopf, president of Intrepid Plastics Manufacturing and Intrepid Idea Innovators, Siemens offered a panel discussion about the apparent renaissance in US manufacturing.
Why is manufacturing a better place today than it has been in recent years?
Gipson: Progress in pursuing opportunities. The energy sector is mentioned most often, and our response to challenges like the global economic downturn. The response of American manufacturing was resilient. Advanced manufacturing is a combination of people and processes that is advancing across all industries. Is employment increasing? It is. Is productivity increasing? It is.
Can you talk about virtualization in manufacturing?
Batra: This is one of the takeaways from the Curiosity rover. Our customers want to view their supply chain as an integrated whole. We talk about the integrated production process, and the concept of one supplier for the entire integrated process. We talk about innovation and transformative tools, especially virtualization.
How does this integrated model address the challenges?
Batra: It is about driving top line growth in revenue. It is hard. Half of all product launches fail to meet expectations. We did a qualitative study and the executives told us that their chief challenge was to increase productivity. The other issue is managing risk and getting transparency in the process.
How did you bring contracts back from China?
Knopf: Everything is cyclical. We have been focused on cost. The triad is cost, quality and delivery. Being local allows us to provide timeliness in delivery, high quality, and reasonable cost. We have a very heavy emphasis on quality, higher than ever before. We try to manage up with our customers. We drive response from our engineering team, because we are in the end held accountable.
What about the skills gap?
Gipson: There is good news, but it has to be communicated in context. Total is about 12 million manufacturing jobs. The jobs are evolving with a requirement for more advanced skill sets and more accountability embedded in these jobs. The gaps-- companies do have difficulty filling open jobs, yet we have historically high unemployment. So there's a mismatch. There are not enough STEM trained people. Companies and industry are taking more responsibility to address theses needs, with partnerships with academia and programs to close those skill gaps. We still also have to encourage our young people to want to get into these jobs. The more we see manufacturing in the news, the more reinforcement we see, the more attractive these jobs will become.
Batra: This keeps me tossing and turning at night. You have to have an environment where people want to stay, because there is no pension obligation that forces people to stay. The Charlotte steam turbine plant is a case in point. We had to go to non-college bound people and put together an apprenticeship program that was highlighted in the President's State of the Union speech. We have to go down to the elementary schools and get kids interested in manufacturing jobs. We have spent money on this in our project GoPLM.
Knopf: We get involved in SME a lot, with certification programs all the way from production floor to engineering. We allow workers to work with the Geek Group and kids learn how to do things that are applicable to manufacturing. We pay for workers' memberships in societies and groups that support increased skills. Our competition is not local, but international, and in Michigan there is a lot of cameraderie and sharing between companies.
What about the age of assets? What does a manufacturing company risk?
Batra: We are in a brownfield migration market in the US. We don't see the greenfield boom that China had. We see roughly $65 billion in aging assets (ARC Advisory Group), and this didn't become an issue until manufacturing became once again center stage in the enterprise. Henry Ford would be happy that manufacturing has come back to life. Having these aging assets is a problem. They are susceptible to cyber attacks, breakdowns directly affect productivity, common processes, KPIs and such are not easily achieved in these assets. You simply can't get productivity with a 286 computer that's still running a line. Companies are realizing that they have to make changes to get more productivity out of their operations.
Gipson: Do companies understand the need to move faster and adopt global solutions? The answer is advocacy around better solutions sooner. This incorporates new technology but technology is not a solution, it is a solution enabler. One of the things I spent my career doing is figuring out how to bring technology to the business folks in such a way that they can see a good investment. How can we create sustained results and leverage that value? We have to have standards, and industry solutions for advocacy internal and external and continue to up the ante.
Knopf: It is about building a relationship with our customers so that we can share the costs and the responsibility. The supplier needs the customer as much as the customer needs the supplier.
Batra: In the end it is about creating sustainable value using advanced technology to provide manufacturing efficiency. The journey we are on at Siemens with our acquisitions is to make us a strong and capable industrial software provider. Manufacturing is becoming central to the enterprise. The wage gap between the US and China is narrowing and the US is becoming a large exporter again.
Can the skills gap be closed through immigration reform?
Knopf: They bring a set of skills we don't have here, and there's a benefit to using immigrants.
Gipson: It is only part of the answer, but it can't be a large part of the answer. If we make the mistake of saying that we are going to import engineers we're missing a huge opportunity to encourage STEM careers here...It is a strategic imperative here in the US.
Batra: Somehow we've dropped innovation in academia. I don't think immigration reform is the answer to cover up the lack of STEM skills and interest in manufacturing...it isn't about patriotism it is about encouraging the best and brightest minds to want to work in the USA.
How do you think the millenials will affect manufacturing?
Gipson: One of the things we see is that there is a new focus on the use of IT and connectivity skills, and this is part of the interaction on how work is done. This is a productivity innovation that is an advantage.
Batra: It is an interesting topic because we are looking at behavioral models as a new way of working inside Siemens. We cramp their style as we work the way boomers do. Their stature isn't tied to an office, but rather to being wired and what they do. These people get it after about a year. It is the older workers that we may have to retrain. It is about how connected they are.
Knopf: We don't understand just how much people can use things like Facebook to get work done. But watch out for a move back to Face to Face.
Do you think wage wars will be the company answer to keeping skills?
Gipson: There have been some very fast increases in salaries. If we are in balance, we'll see skills being valued properly. We'll see wage wars in the short term.
Batra: People don't leave corporations entirely for 10 to 15% more money. People leave managers rather than the company. Accommodative work environments are much of the answer. We have to have a very effective work environment.
Panchak: We need to create a learning work environment.
Gipson: Salary is very important, but probably almost as important is the organization and how people will work together.
Knopf: People can be more flexible. I agree that the way people feel about the job is as important as pay.
Batra: The stress test for companies in the game of people is when the economy is booming.
We have boomer retirement and we have to attract and retain employees. What about 3D virtual reality training to attract and retain and train employees?
Batra: This is central to our innovative strategies. Using virtualization tools, virtual prototyping, and applying it to training gives younger engineers an incentive to learn manufacturing. And besides it is fun. We don't have grease under our fingernails anymore.
Gipson: Dow's virtualization technologies are long established for product lifecycle from design to retirement. There are significant opportunities.
What about cybersecurity? Can it affect manufacturing's renaissance?
Gipson: It will if we don't do something about it. It is coming to the forefront and we're seeing some of the potential for damage if we don't manage the risk properly. It has to be industry driven, company driven around a holistic approach to cybersecurity.
Batra: This is a very important topic for Siemens, because of the nuclear centrifuges in Iran, so we have worked very hard on actually hardening our products and working on enabling defense in depth with our customers, and NIST is working on a plan to achieve the best practices for cybersecurity.
There's going to be a lot more rigor.
What about US investment tax credit for manufacturers to do more investment in new technologies?
Gipson: Should there be tax credits? I think yes. But I think we have an opportunity under the umbrella of advanced manufacturing that is a real opportunity for investment.
Knopf: Tax credits are beneficial, and it helped Chinese manufacturing grow. But tax credits are almost too hard to get. Everybody has been burned in the past five years.
How did you survive the downturn?
Knopf: It was the worst time we went through. We moved to a new factory in August, and by December 2008 everything stopped. We were fortunate that we had a lot of low volume and service work that kept us going. We went to four days a week, we shut down lights, cut our electric bill, and did whatever we could to keep going. We have changed our business model, and we have partnered with another larger company to get us to the next level.
How should companies provide incentive to project managers to realize long term rather than short term goals?
Gipson: Change the scorecard. Look at the way project managers are judged today, and change the way they are scored.
Knopf: The first 80% is easy. It is the last 20% that's hard. We don't have incentive programs per se, but we make sure project managers care about the long term.
Batra: We are seeing more of the service contract behavior that continues to lock us into the health of the asset over its life span. I'd like to pose that question to the capital markets and institutional investors, too. (laughter)
Gipson: This can be used to create accountability in higher management.
Dow has increased ethylene production due to cheap feedstock..
Gipson: Speaking for myself, and not Dow, I think this is a play to Dow's strengths.
Overproduction of natural gas is causing storage problems...
Gipson: This is a critical management issue to improve the infrastructure, keep prices high enough and wait until demand rises.
What is your view on introvert engineers and forcing teens in the workforce?
Batra: we keep doing these talent forums and we put these people in front of a hundred people and watch them go all fishbowl. Taking a concert pianist and try to make him a percussionist doesn't really help the pianist. We need to encourage specialization on topics, but not reposition them into something they aren't comfortable with.
Gipson: We had for years programs within the entire global engineering organization to advance people's skills in the area of relationships and self improvement. It is about being more effective in doing your job and creating more value for yourself and your employer.
Knopf: If we aren't pushed out of your comfort zone we don't know how far we can go.
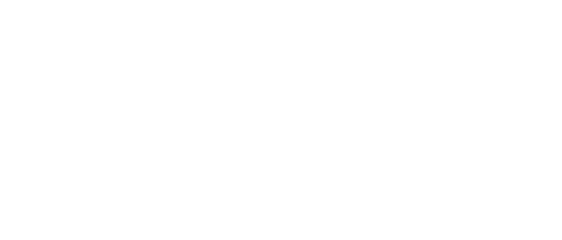
Leaders relevant to this article: