The automation industry faces an unprecedented loss of knowledge over the next decade as seasoned workers retire in droves. Finding a way to retain departing workers' knowledge and provide the training, information and tools that will position new workers to succeed is a key driver in the design of digital user experience and the need for changes in culture and management, says Dr. Arnold Lund, GE Connected Experience Labs Technology Leader.
Sharing the stage at Minds + Machines 2015 with David Cronin, executive design director, GE Digital, Lund said the approaches of previous industrial generations—too often adapted from other sectors' business models—will not suffice. Industrial workers have specific needs that can only be addressed through intentional design, Cronin said.
Messy, loud and dangerous
"Industrial workers have special requirements for technology," Cronin said. "You can't take machines that are designed for offices and consumer use and expect them to work in industry. But that's what we have done in the past. Field workers perform their jobs in messy, loud, dangerous, mobile environments. They need their hands free, and they need to focus their attention on the task at hand, not on complicated software."
Lund said the field worker of tomorrow will be intimately synched with the technology supporting him. Sensors in the worker's clothes will provide the input he needs without having to hold equipment. Smart eyewear and augmented reality will provide access to real-time data provided not from static manuals but from data analysis and machine learning based on a digital twin of the asset being serviced. Cameras on a field worker's eyewear will stream video feeds to remote workers providing additional support.
"What we're talking about is realizing worker potential and the business potential that comes with it." GE's David Cronin on the use of the Industrial Internet to enable the digital industrial workforce of tomorrow.
"These are not dreams of a future Utopia," Lund said. "They are the tools we require to succeed in an environment of increasing complexity."
But success means more than new tools; it also requires a change in culture to support the realities of the digital revolution. "When I started my career everything was about quality; systematize, understand and then make incremental changes in order to drive improvement," Lund said. "Now you need to be adaptive. Business requirements are changing. Technology is changing. How do we make dynamic organizations that can handle that? It requires a culture of collaboration and tools that truly enable collaboration."
Collaboration among workers and machines
And that collaboration will not just happen between people, but between people and machines. Cronin said we will shift from a world of human-machine interfaces and humans controlling machines to one in which humans and machines collaborate. But that doesn't mean workers will outsource their judgment and decision making to computers. In fact, decision-making needs to move even more quickly from hierarchical models to decision-making at the edge.
"The people in the field and the ops centers have to perform quick problem solving in situations that they're being dropped into in response to the automation that we're providing," Lund said. "These are tools to empower, not replace. Not by any stretch of the imagination."
And about those retiring workers? Lund envisions a day when not just machines, but workers themselves have a digital twin, a machine-learning repository of experience and knowledge. While that may be a ways off—and maybe a little creepy—Cronin believes it is part of the necessity of the future.
"What we're talking about is realizing worker potential with the Industrial Internet, and through that the business potential that comes with it," Cronin said.
Latest from Asset Management
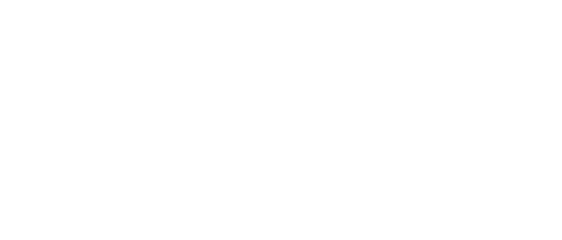
Leaders relevant to this article: