By Gary Nichols, PE, Jacobs Engineering Group
ANALYZER Lifecycle Costing (LCC) is an accurate, descriptive, short name for an analyzer system reliability program, and “analysis and optimization of full lifecycle costs” is a functional, short description of the activities and results of a well-planned and well-run analyzer reliability program. This article describes and quantifies the lifecycle cost impact of typical analyzer system project issues and line items, which, if addressed early in the lifecycle of the project, can result in lifetime cost savings. It’s important to note that “project,” as used in the current context, means from concept to retirement, though retirement isn’t addressed here.
One can’t open a current issue of many trade publications without seeing an article with “reliability” in the title or section headings. In his article, "The Top Five Reasons Why Companies Don't Measure Reliability," Ricky Smith (Plant Services, December 2005) notes that, surprisingly, reliability still may be struggling to become part of routine management. Related terms include “asset management” and “asset lifecycle management.” Concurrent engineering (CCE) as Rich Merritt pointed out in "Back From the Grave," CONTROL, Oct. '04, is a closely related concept and project management tool that involves “…multiple people, organizations and/or companies in a control system project,” which “…goes beyond control systems to include the rest of the plant’s operations and functions, from design and construction to startup.”
Figure 1 below shows the lifecycle cost of a hypothetical, but representative, analyzer system project. For simplification, we’ll assume this is a small, standalone project to install a new analyzer system in an existing process unit. Figure 2 below shows the cash flows for the same project. Teh costs don't consider interest, inflation, and tax consequences.
FIGURE 1: LIFECYCLE COSTS(Click image to enlarge.)
If we define the major lifecycle stages of a capital project or generic device as: 1) concept and planning, 2) design and development, 3) production and manufacturing, 4) operation and repair, and 5) wear out and disposal, then 65% of the project or device’s total lifecycle costs have been determined at the end of concept and planning, and 85% of its total lifecycle costs have been determined at the end of design and development, according to Robert Dovich and Bill Wortman in The Certified Reliability Engineer Primer, 3rd Edition. Of course, this doesn’t mean the money is spent and reflected as cash flow early in stages 1 and 2. Instead, its meaning is more subtle.
For those with experience in capital project engineering and maintenance management, the implication is that ongoing maintenance, service, and lifecycle costs can be optimized (minimized!) with more thought and attention in the early lifecycle stages before capital equipment, direct labor, or direct materials have been purchased or, perhaps, even estimated. This article will use these and other assumptions, which may or may not apply to the readers’ analyzer system projects and installations. Readers must work with their engineering, maintenance, and accounting organizations and relevant data to implement a valid, working analyzer system reliability program for a particular technical and business environment.
FIGURE 2: CASH FLOW*Assumed percentage of cost commitment in respective stage for discussino purpose. Calculation Basis: Total Lifecycle Cost = $300,000. (Click image to enlarge.)
Production and Operation
Whether the figures of 65% and 85% apply to analyzers can be debated, but many readers can readily relate to stages 3 and 4 of a process analyzer’s lifecycle, especially when unnecessary costs are incurred. For example, during stages 1 and 2, special DCS needs may have been overlooked; an improper sample-handling system alloy may have been specified; ergonomics may not be fully vetted; and basic principles of sample-handling system design may not have been fully considered. Any of these oversights can necessitate inconvenient and costly (safety, time, money, and quality) reengineering, redesign, and replacement during commissioning and start-up. Even a Stage 1 decision can cascade to Stage 2 redesign because the design team failed to note that the analyzer is more critical during process plant upsets and other irregular operations than in steady-state or normal operations.
The following lists describe several typical project scope development and preliminary engineering-stage items for capital analyzer projects at stages 1 and 2. Though all should be addressed during these early stages, they’re grouped to characterize the stage of an analyzer project when they’re most likely to arise if not addressed early.
Project Scope Developments
- Analyzer scoped and specified on outdated process information has to be redone with current information
- Failure to specify correct sample handling system metallurgy
- Failure to recognize and request incidental infrastructure upgrades essential to the analyzer system during scope development
- International, national, industry, and company standards not clear about a non-customary feature on the analyzer system
- Failure to note need to purchase additional DCS hardware to handle multiple analyzer signals for stream component concentrations, safety-related alarms, functional faults, and maintenance actions
- Failure to recognize that no spare homerun wires exist between the field junction boxes and the motor control center or DCS marshalling panel
- Requests for post-completion documentation, job books, etc., not originally estimated nor approved for purchase or collation
Supplier-Related Events
- Competitive bids difficult to compare due to different proposed analytical technology, in-house and third-party capabilities, grouping of line items in proposals/bids, etc.
- Parallel analyzer system integration suppliers don’t coordinate effectively
- Integrated analyzer system and associated purchased items don’t pass factory acceptance test (FAT) the first time (and possibly not the second time)
- Supplier delays because of back ordering, internal reorganizations, personnel changes, etc.
Instruction and Constructability
- Overlooking required safety features until construction begins
- Construction delays caused by operations or maintenance that could have been anticipated during scope development
- Awkward accessibility to construction site due to other work in the area, lifting near hazardous piping, lack of elevator or hoist for heavy capital items and construction tools
- Changing on-site construction contractors during construction
- Failure to note the need for special construction safety precautions during scope development and estimating
- Multiple personnel changes of engineers, designers, and other key project team members through project construction, start-up, and commissioning
These lists aren’t exhaustive. The financial impact of each item in the above list is different for each project, company, and analyzer engineer, so it wouldn’t be helpful to categorize their respective impacts on safety, cost, schedule, and quality. If we look at the cost impact of a given analyzer project’s problems by size, the important point is that, in each case—small, medium, or large, there’s a considerable cost premium associated with discovering the problem and correcting it late during stages 3 and 4, instead of catching it early during stages 1 and 2. Just one each of the small, medium, and high impact items costs an additional $23,200 over the lifecycle of the project, and this doesn’t include the costs associated with their unpredicted occurrence during Stage 4.
In addition, another $10,000 in capital costs can be depreciated at $1,000/year over a project’s 10-year lifetime. This $10,000 can be justified if it will prevent a $100 per month, or $12,000 per lifecycle, service action over the same 10-year period. You can perform a similar analysis that includes interest, inflations, cash flow, tax consequences, etc. The point is that “a penny saved now is not necessarily a penny earned later.”
The issue isn’t ignoring nor minimizing the legitimacy of these concerns. Instead, the task is to know, understand, and consider their inclusion in the analyzer project scope as early as possible, and decide how best to include them, or to address them outside the scope of the project. Obviously, the correct metallurgy for an analyzer system must be in the scope, while completing incidental work not required for the analyzer system may often be addressed better and at lower cost outside the analyzer project’s scope. Nor is it practical to avoid all such oversights. Sometimes a decision must be made for safety or financial reasons to change construction contractors. Sometimes it’s necessary to work around unscheduled shutdowns and turnarounds for process safety or economic reasons. However, many oversights can be avoided during stages 1 and 2 if the right questions are asked of the right personnel at the right time. It’s even better if the need for the information is recognized and volunteered early in the project lifecycle.
Historically, reliability was more associated with maintenance than with project engineering and management, as in the foregoing discussion. This notion is excusable because 1) an article or device that fails is judged to be unreliable, and requires repair or replacement, which are the customary functions of maintenance, and 2) a large body of practical input to improving the reliability of devices and systems comes from organizations that perform maintenance. More formal references to “reliability” often refer to its esoteric tools, such as mean time between failure (MTBF), mean time to repair (MTTR), design of experiments (DOE), redundancy, failure mode effects and criticality analysis (FMECA). These are only tools that can be used to measure the effectiveness of true reliability, which is lifecycle costing.
Unfortunately, reliability is sometimes substituted for “maintenance” just to achieve a favorable image, rather than to make real improvements in the reliability of installations such as analyzer systems. Fortunately, reliability is coming to refer to lifetime safety, quality, and costs as a means to safely and legitimately defer repair and replacement, rather than as post-failure data collection and analysis, or as a meaningless, dressy name.
Bibliography
- Dovich, Robert, and Bill Wortman, "The Certified Reliability Engineer Primer, Third Edition," The Quality Council of Indiana, West terra Haute, IN, USA, 2002, pg. II-7.
- ibid. pp. II 18-20.
- Smith, Ricky, "Everybody's Got an Excuse: The Top Five Reasons Why Companies Don't Measure Reliability," Plant Services magazine, December 2005, pg. 54.
- Peterson, S. Bradley, "The Future of Asset Management," CONTROL magazine, November 2004, pp. 34.
- Clambaneva, Stephen, "Transforming Your Business With Asset Liefecycle Management," Plant Engineering magazine, August 2004, pp. 29.
- Merritt, Rich, "Back From the Grave: Concurrent Engineering Died in the '90s, Is its Resurrection at Hand?" CONTROL magazine, October 2004, pp. 30.
About the Author |
Latest from Asset Management
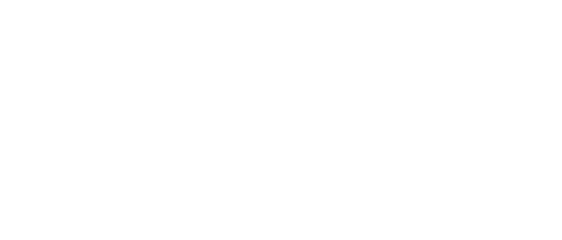
Leaders relevant to this article: