The PLCs and Data Highway Plus networks existed prior to the isntallation of the new server. The new system plugs in via gateways.
FIGURE 1 shows how the server communicates to the gateway via the Ethernet business network using a network path that already existed. The gateway is equipped with a DHRIO module which provides the connection to the two distinct DH+ networks via separate channels. The DH+ cabling required to reach the gateway location was much less than what would have been required to reach the server room had we connected the server directly to the I/O. Other benefits realized using this approach is the decoupling of the communication hardware from the server (which eliminated the potential hardware compatibility issues), and the ability to easily expand the gateway by adding more communications modules. Kettle Foods plans to add other processing lines (baked chips, for example) to the reporting system later, which may require connection to a third DH+ network.For the database server computer, a solution was needed that would provide not only a good vehicle for the collection and storage of the information, but also a platform that was well supported with easy to use tools for developing reports needed by varied users on the business network.Our solution was to install a rack-mounted PC as the server computer, with a redundant array of disk drives. To collect and display the process information, enabling the evaluation of the performance of critical production assets, we recommended the installation of RSBizWare software, a graphical application suite built on Microsofts SQL Server. The software suite was selected for its flexibility, providing a tool with wizard-driven configuration of data collection points and the ability to create custom transactions for population of user defined data tables. It also allowed the customer to interact with the reports via a web browser plug-in.Another element of the networked software suite, PlantMetrics, provides users with a set of tools to build on the reporting, analysis and management capabilities of the RSBizWare framework. Our system solution also included RSBizWare Historian, a trending tool that captures time series data, and RSBizWare RSSQL, a tool used to commit data to user-defined database tables via event driven transactions. RSSQL is especially useful when collecting a single record composed of several pieces of related data, such as the time, date, storage bin and quality factors for a received load of potatoes.The RSBizWare suite includes a set of tools for generating reports that can include elements such as charts, graphs, and tables. We used the QuickWeb feature of RSBizWare to distribute the reports throughout the organization via a company intranet. QuickWeb allows users to interact with the reports via a web browser without need for additional software on their PC. Using the Web application package, users can call up any of the reports and select the desired time/date range or shift to suit their information needs (See Figure 2).
FIGURE 2: WEB REPORT SCREEN
THE KETTLE FOODS batch processing requires that the installation use PlantMetrics in a non-conventional way. Rather than monitoring the equipment to calculate OEE (Overall Equipment Effectiveness) values, they employ an event-driven data collection scheme to log the process data only when it changes. This method is well suited to a process where individual batch tracking is crucial, the data changes slowly, and it collects operator-modified setpoint values. Using the software to configure this event-based data collection provides the companys engineers with a simple interface for making additions and revisions to the collection settings.The results seen so far by Kettle Foods have been impressive. Production staff can now track near-real-time processing performance in both the cooking and packaging areas. This drives the quality and efficiency goals down to the operator level where real changes can be effected. Engineering can track trends and match production data with quality data to determine root causes of production and quality problems and to determine the impact of process improvements. Downtime between shifts and batches, packaging changeovers, and product has been reduced. Combined, the data acquisition and reporting tools have allowed Kettle Foods to increase its effective production capacity by 10-15%, thereby delaying costly capital expansion.
About the Author |
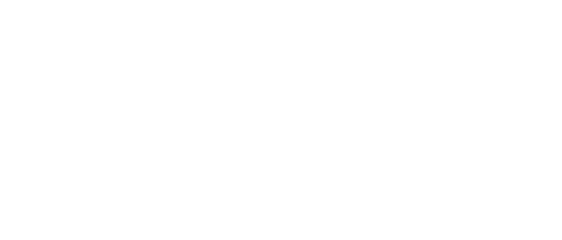
Leaders relevant to this article: