DSM Dyneema uses process analytics to improve business results
DSM Dyneema is the global supplier of Dyneema, the world's strongest fiber. Dyneema is manufactured and sold in various forms to a wide range of industries ranging from offshore oil and gas to sports and lifestyle. The Dyneema trademark or logo on an end-product provides users with a guarantee that they're investing in performance and quality. Meeting those two guarantees requires achieving the highest excellence in operational performance. Here’s one way that DSM Dyneema has become a data-driven organization (Industry 4.0), and how our operations department is rapidly transforming with the help of self-service analytics solutions.
Mission and strategy
Royal DSM is a global, science-based company in health, nutrition and materials. Within the group, DSM Dyneema manufactures Dyneema in three locations: The Netherlands, the U.S. and China. On a strength-to-weight basis, the fiber is almost twice as strong as the second strongest fiber, aramid, and more than 15 times the strength of a steel fiber. Dyneema is manufactured and sold in several forms to many heavy-duty industries and used for human protection in bulletproof vests, helmets and gloves. Everywhere you can use steel cables, you can use the Dyneema fiber to reduce weight and increase strength for lower costs.
Because many competitors are constantly trying to do what Dyneema does, it's crucial to continuously improve performances to remain the most successful and high-quality performer in the market.
DSM’s company motto, “Bright science. Brighter living,” expresses our mission to make the world a better place for current and future generations by creating sustainable value for all stakeholders simultaneously. To execute on this mission, it's vital to achieve operational excellence while maintaining overall profitability. This is reflected in our strategy to drive profitable growth from our constituted portfolio of activities. The strategy has been transformed into the site targets for the Netherlands: increase capacity and improve process stability.
Road to Industry 4.0
Traditional methods for reaching the aforementioned goals typically disturb commercial production. They involve R&D and making trial runs on industrial production lines. As an alternative, data and analytics activities can be used to contribute to these goals by increasing production volume, reducing waste and optimization of asset performance, including reducing downtime.
To avoid production disturbance, DSM Dyneema moved to big-data regression. We approached a variety of companies to come up with the answers we needed. The projects proved to be a lengthy process with many hurdles of data conversion and cleaning, and included the challenge of combining variables with different time steps without compromising the data quality.
Why self-service analytics?
Figure 1: Multivariate scatterplots provide visualization of tags and their dependencies in a matrix of graphs, so users can quickly identify the most promising candidates—where correlation is strong—for root-cause analyses.
After three big-data modelling projects, we still didn’t have the answers for how to increase capacity and improve process stability, so we started looking for alternative analytics tools that could be used by process engineers and deliver results quickly. TrendMiner was selected for its relative ease of use, fast response times and useful functionality for process engineers. The tool also provides alerts when process parameters exceed defined limits, leading to improved process control and reduced off-spec product. Comparison of parameters of series of trials runs is fast and provides meaningful overviews of values and discrepancies among the runs.To extract the most value from their process data, the subject matter experts needed to be able to easily use the new analytics tools without having to become data scientists. DSM started with a proof of concept, and because of TrendMiner’s plug-and-play functionality, the software was quickly up and running. The trained key users, however, thought something was missing for adoption of the tool. The process engineers wanted to have a clear understanding of how to apply the self-service analytics tool in their daily work, so the project team worked with TrendMiner on practical use cases based on actual production processes that demonstrated the added value of self-service analytics.
Value proven in performance
TrendMiner’s self-service analytics have proven their value in various areas including troubleshooting, product evaluation and root cause analysis. In the case of troubleshooting, too many production variables need to be considered for an operator to monitor performance. With TrendMiner, multivariate fingerprints can be created and alerts can be set. During production, both positive production results as well as deviations can trigger notifications to various stakeholders. During or after the run, the process engineers and operators can review all the captured notifications for further analysis and production improvements. This has helped to reduce the production failures dramatically, reducing downtime.
Figure 2: From quality, environment, safety, security and health (QESSH) to more highly satisfied customers, process analytics offer DSM Dyneema a practical method for leveraging data into business improvements.
For all the production runs, there are many parameters (tags) to be considered. To compare various trial runs, the selected tags can be compared for the periods of the product in question. The production comparison is available almost instantly and can be exported for reporting purposes. These capabilities are reducing the time spent gathering information for optimizing product quality and production reliability.To find root causes for production issues, TrendMiner provides a very quick way to investigate the correlations among the process parameters (tags). The process engineer can easily zoom in on the most promising hypothesis via the multivariate scatterplots (Figure 1).
Visualization of the tags and their dependencies in a matrix of graphs helps users quickly identify the most promising candidates in root-cause analyses. What would previously take three weeks or more to do can now be done within an hour.
The use of analytics impacts not only the corporate goals of increasing capacity and improving process stability, but impacts quality, health and safety as well (Figure 2). It also improves customer satisfaction through improved troubleshooting, root-cause analysis and facilitated evaluation of product trials.
Continuous improvement 4.0
To become a fully data-driven plant, the site management team expects every process engineer to become a Six Sigma Green or Black Belt. Currently, only a few Six Sigma “define, measure, analyse, improve and control” (DMAIC) projects, with an average duration of five to six months, are taking place for improving operational excellence. TrendMiner can be applied to most of the DMAIC project phases and reduces the time needed to complete each phase considerably. In one test case, the define and measure phases, which originally took two weeks to complete, were redone with TrendMiner, and were completed in two afternoons.
While self-service analytics solutions are easy to use, users need training that solves real-life problems and support to make engineers fluent in the tool, so that its use becomes a habit. Without this, momentum will be lost. DSM Dyneema plans to roll out the use of TrendMiner to the Greenville site in the U.S. to expand the user base into other business units, as well as into other focuses such as HAZOP, energy saving programs and process stability studies. We plan to create and nurture a TrendMiner community to further strengthen adoption and continue to drive data transformation.
Renzo Rondags, data expert, DSM Dyneema, can be reached at [email protected].
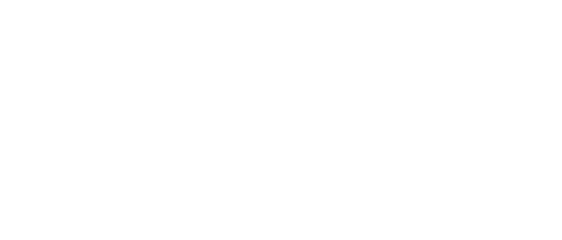
Leaders relevant to this article: