Data Collection and Optimization, Part 1
See Part 2, ...to Tango
By Jim Montague, Executive Editor
Wanna dance? Great. But you may need some new moves. Inexorably cheaper and more powerful computing are pumping out a frantic beat of exponential jumps in data generation and storageand process control applications are caught on the dance floor too. Sadly, more information often doesnt mean more intelligencejust more stuff to overlook and ignoreand less costly and more widely deployed control components combined with fewer staffers to monitor them make the steps more complex.
Logically, the only way to survive this data tsunami is to seek out and prioritize the few useful gems in that swelling ocean of data ruthlessly, and then get them in front of engineers and operators trained and motivated to use them to improve and add value to their processes.
For instance, Comisión Federal de Electricidads Valle de Mexico power plant in Cuautitlán near Mexico City is reportedly unique because its four-unit, 550-megawatt, combined-cycle facility can generate power in four ways (Figure 1). Ricardo Gandara, Valle de Mexicos instrumentation and controls (I&C) department manager, says the combined-cycle plants 300-megawatt steam turbine produces power by the usual steam-recovery generation method, but it can still run its old boiler, burn gas in conventional open-cycle mode or use a hybrid combination of these three processes.
Figure 1. Engineers and operators at Mexico de Valles combined-cycle power plant use data acquisition units and a process information management system to better manage thermal and generating efficiency in their 550-megawatt, four-unit, combined-cycle generating plant.
To operate its combined-cycle units more efficiently, however, Valle de Mexico recently installed about two dozen DAQstation DX paperless recorders and several MW100 data-logging systems from Yokogawa Corp. of America and plans to install another two dozen soon. The engineers also asked Yokogawa to help design a plant-wide data acquisition (DAQ) system to secure and help analyze common measurements from the close to 50 DAQ units it will possess. The plants four units already had distributed control systems (DCSs) from three different suppliers, but Gandara reports they couldnt deliver information in a single, common format. As a result, Yokogawa installed its Exaquantum plant information management system (PIMS) software, and it connects to the combined-cycle plants DAQ units via Kepware Technologies OPC servers. The resulting network also uses fiber-optic cabling and ProSoft Technologys radios for several longer-distance connections. The whole project has cost about $75,000 so far.
DAQ units were more convenient and had more long-term memory storage, but we also needed to bring all our data into one smaller system, play with it and analyze it, so we could manage the fuel we use, the electricity we sell, gas quality, and do it in real time, says Gandara. Consequently, the plants staffers began installing their new DAQstation units and Exaquantum PIMS earlier this year, and are still in midst of the project. In fact, Gandara and his colleagues plan to use DAQ units and their PIM system to analyze the efficiency of all seven units. Mexico de Valle also has three conventional natural-gas units for a total generating capacity of 1,000 megawatts.
The two primary measurements that Mexico de Valles engineers pull from their data, run though the PIMS and perform calculations on are regemin termico or thermic efficiency and estatismo or generating efficiency, which is the ability to hold a constant, 60-Hz frequency under load changes. The plants operators view data for each unit on a display, request detailed batch efficiency reports for each generator using load, frequency and power data, and then plot and archive resulting report data. Thermal efficiency reports also can be requested for each turbine. Operators also can call up historical trend data for any previous time period on any measured data point. These real-time efficiency and historical reporting capabilities allow the operators to continuously optimize their plants performance as generating load demands change.
We used to bring data in on clipboards, enter it manually on a PC and do calculations once every eight hours. Now, we can get this information in seconds and do the calculation in minutes, adds Gandara. We already know what the efficiencies should be in each unit, and now we know immediately when theres a deviation, so we can take corrective action and bring our process back to specified design conditions. Its difficult to say what they savings are, but were running more efficiently and safely. Were also using less energy to generate the same capacity, and this is the doing more with less that every business wants to do.
Eyes on the Parameters
This single-minded focus on precisely what you need to know to improve your process is the starting point, forms the backbone of good data collection and is the foundation for future optimization and advanced process control (APC).
For example, ExperTune Inc. recently helped Borealis Polymers Oy upgrade the ethylene cracker at its facility in Porvoo, Finland, increase annual capacity from 330,000 to 380,000 tons and meet subsequent weekly production targets needed to pay for the project. The 2007 project included equipment upgrades to a gas compressor, hydrogen purification unit and several distillation columns. Regulatory controls and APCs were updated to handle the modified process. The complex makes ethylene, propylene, butadiene, acetone, phenol and polyethylene, and has an upstream refinery.
To better manage the crackers close to 1,000 control loops, Mikko Rönkä, Borealis automation engineer, reports his company adopted three upgrade strategies: train operators with a simulator, revise its APCs, and improve its regulatory controls with ExperTunes PlantTriage software. The software connects to the control system via OPC and then identifies and prioritizes opportunities to improve regulatory control, explains Rönkä. The software allowed us to see, for the first time, the performance of all the important control loops in our plant, and we uncovered a host of control system opportunities.
Presentation Priorities
While accurate numbers and precise calculations are the heart of data collection and optimization, the way in which meaningful information is presented also is gaining importance. To quickly view and respond to their own loops, Borealis engineers and operators check PlantTriages dashboard displays and use its Biggest Payback Loops list, which shows specific loop details and likely root causes.
Temperature controls used to be notoriously difficult in the ethylene facility. Previous manual attempts left us with controls that worked, but werent optimal, but PlantTriages integrated tuning and loop-optimization tools let us push closer to optimal, adds Rönkä (Figure 2). The robust controller tuning eliminated loop cycling and interactions, which added stability to the process, and allowed us to use APC. We also focused on the control valve, because its the most likely point of failure in a loop. Using valve-travel diagnostics, we identified control valves with the most wear. The root cause usually is related to tuning or inadequate instrument signal filters, and can be addressed easily.
Figure 2. Repaired valves and better loop tuning provided more optimal control of temperature and other process variables and improved performance of Borealis Polymers Oys ethylene cracker in Porvoo, Finland.
Ramping Up to Real Time
Besides being archived out of reach, data in traditional historians often are accessed too late to aid their processes. Sure, they can provide some after-the-fact indicators and trends, but todays applications require intelligence much closer to real time, so they can make corrections as production occurs.
For instance, Sasols Infrachem Utilities and Syngas division recently collaborated with Invensys Business Performance Services to improve operations at two steam plants at its Sasol One facility in Sasolburg, South Africa. Sasol and Invensys developed dynamic performance measures (DPMs) to provide underlying real-time performance measures for each of its steam production units, and also deployed real-time financial metrics to calculate cost and profit for each process unit and area. Next, they staff created management and operator dashboards that use the DPMs and financial data to give managers real-time information so they can make better-informed decisions.
These DPMs bring together accounting, engineering, management, operations and maintenance to discuss Sasols overall business. Sasol and Invensys report that this interdepartmental interaction creates understanding across business functions, helps develop strategic performance measures across those functions and creates new business processes for improving the bottom line.
In the first month after the DPMs were installed and gained more consistent fuel oil use and boiler tuning, Sasol saved 6% on its energy feedstocks and 4% on electricity costs for making steam at Stations 1 and 2, and these results improved over the next two months. Overall, Sasol Infrachem and Invensys are saving more than the $400,000 per year they expected to from Sasol Ones two steam plants, and the partners are now rolling out their real-time performance measures at five other plants. Bow to your partner.
Jim Montague is Controls executive editor.
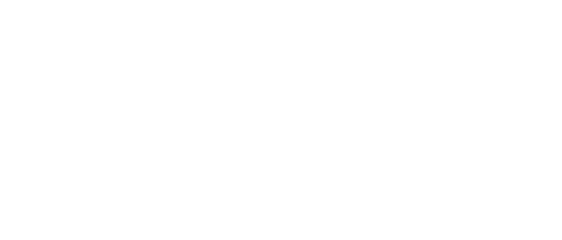
Leaders relevant to this article: