Joe Feeley is Editor in Chief of Control Design and Industrial Networking magazines. He joined Putman Media in 1997 to help start up Control Design. He has more than 20 years of engineering and management experience in the U.S. and Europe in industries that include high-purity semiconductor products and other specialty materials that require direct involvement with the associated machine designers.
Check out ControlGlobal.com on Google+
Condition monitoring is the process of detecting, identifying and acting on faults before a failure occurs or before a machine can no longer perform its intended function. "But the process of a traditional 'Walk-Around Predictive Maintenance Program' has its share of challenges," says Scot Wlodarczak, regional marketing lead at Rockwell Automation. "This mode of predictive maintenance largely relies on the vibration expert and data collected on intervals as long as monthly or quarterly. So you can miss failures."That person would later download the data to a stand-alone software package to create and manage alarms that help flag changes, Wlodarczak continues. "He might review alarmed data, identify each change and analyze the data to determine the presence of new faults or the propagation of known faults. He'd then collect additional data to confirm suspected faults and report this back to operations. If the fault or its indication is affected by machine or process status, then this can be problematic. He'd repeat this until maintenance was performed. After maintenance, he'd perform analysis to confirm repairs and to create new baseline."
"The problem is that these traditional programs are expensive, with recurring costs for skilled technicians or trained, experienced rotor dynamics engineers," Wlodarczak says. "There are annual support, equipment service and training costs, and one-time costs for data collectors, software and computing hardware. Plus a lot of the basic expertise is disappearing through retirement and other attrition."
Wlodarczak says that legacy automated stand-alone systems from Rockwell Automation collected the data, but still needed an involved, separate software and analysis to figure out what was going on.
So it's reasonable to ask "How can a labor-intensive, skills-based and personality-driven program be sustained as personnel change, program needs change, budgets grow and wane, and organizations evolve?" The product developers at Rockwell Automation believe that "It can't be sustained."
Toward Self-sustained Condition Monitoring
Self-sustaining condition monitoring is how the company believes condition-monitoring systems and programs should be applied to ensure that they can be sustained as personnel change, program needs change and as organizations evolve.
The Dynamix 1444 condition-monitoring module allows users to leverage the Rockwell Automation Integrated Architecture, rather than an isolated condition-monitoring device, to assess current equipment health, predict potential issues and help avoid damage to critical machinery.
Wlodarczak says integrating your condition monitoring into the plant automation system is what the new Dynamix 1444 Series Integrated Machinery Monitoring System is about. The system is newly designed to serve the protection and condition monitoring requirements of rotating and reciprocating industrial machinery. It will become available later this year.The company says the 1444 Series system simplifies application design, reduces cost for spares, training and support; and lowers engineering, manufacturing and inventory costs.
"The Dynamix 1444 allows you to leverage Integrated Architecture, rather than an isolated condition monitoring device, to assess current equipment health, predict potential issues and help avoid damage to critical machinery," says Paul Whitney, commercial program manager - Integrated Architecture, Rockwell Automation. "Integration of machinery health into control architectures using Ethernet brings unprecedented flexibility to machine instrumentation design and operational efficiency in the plant. The Dynamix 1444 line provides integration that simplifies your solution for equipment monitoring applications and includes EtherNet/IP communications with dual ports for Device Level Ring."
"By leveraging this into an integrated environment, we not only automate the data collection, we automate analysis, which was not the case with the previous generation systems," Wlodarczak says.
"We have our Integrated Architecture with our PACs managing different disciplines, such as CNC, motion, integrated safety on servos," Whitney says. "It’s all about being integrated into one architecture and designed and developed in one software package within the application code and residing in the controller, be it ControlLogix or CompactLogix. It can feed data to the enterprise system, getting the right information to the right people at the right time, all on Ethernet/IP. That’s what’s new with the 1444 line. We’re bringing integrated condition monitoring into the architecture. You’re building it in Studio5000, your design and configure environment. And it sits on an EtherNet/IP network, which is important since we’ve had customers clamoring for that for a long time."
The system will offer toolkits and faceplates, which are pre-canned pieces of code for the PAC and display screens for the HMI, Wlodarczak explains, adding, "Now the data is pulled into the PAC where we can include code that will automatically look at the data, analyze it, and give the operator or technician actionable data or trigger an alarm." There’s no separate software required as was the case in the past, Whitney stresses. "That’s one of the real values here."
Wlodarczak says the modules in the 1444 series have been greatly simplified. "We had multiple function-specific modules to pick through, and they were more complicated than they needed to be," he explains. "Now it’s down to six catalog numbers—a dynamic measurement module, three expansion modules and two terminal bases."
The dynamic measurement module is a four-channel, general-purpose monitor that provides measurements of dynamic inputs such as vibration and pressure, as well as static inputs such as thrust, eccentricity and rod drop. The module is designed for monitoring shaft, casing,and pedestal vibration, shaft and rod position, casing expansion and other critical dynamic and position measurements on rotating and reciprocating machinery. It also incorporates one SPDT relay for local trip functionality.
The tachometer signal conditioner expansion module is a two-channel monitor that converts the signal from common speed-sensing transducers into a once-per-rev, TTL-class signal suitable for use by the dynamic measurement module. This module—as is the case with all three expansion modules—is designed for use with the dynamic measurement module, which provides the power and manages the module configuration through the backplane.
The relay expansion module is a four-relay module that adds relays to the dynamic measurement module, while an analog output expansion module is a four-channel module that outputs 4-20 mA analog signals that are proportional to measured values provided by the dynamic measurement module.
Each Dynamix module must be installed in a terminal base, which, when linked together with ribbon cable, serves as the backplane of the 1444 Series system. There are two types of terminal bases–one for the dynamic measurement module and one for the expansion modules.
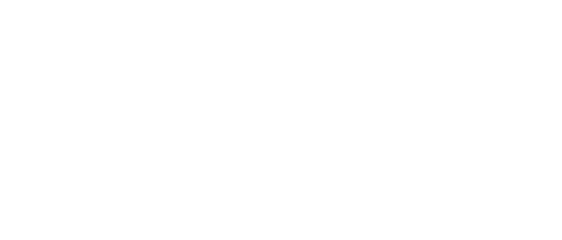
Leaders relevant to this article: