By Bob Sperber
About a decade ago, Kris Zywicki began studying ways to make Dow Cornings information technology (IT) infrastructure as high-performance as the silicones it produces. Starting at the companys hometown plant in Midland, Mich., he zeroed in on calculating the costs and risks of manual data entry on both sides of the production process, from enterprise resource planning (ERP) to the plants distributed control system (DCS).
By 2002, integrated data between the two platforms was saving the plant $650,000 a year. Today, Zywicki says, just by doing automated data transfer, were looking at $4 million in cost avoidance. And Zywicki, Dow Cornings enterprise integration architect, continues standardizing and streamlining systems across more than 15 plants in the Americas, Europe and Asia.
So far, the company has implemented a single, global instance of SAP business software serving 9,000 users. Operational systems in various stages of implementation include laboratory, maintenance and historian/data-manager systems. Control platforms have been whittled from just about every system you can name to four.
Manufacturing and software standards are converging to produce a fundamental flattening of the DCS architecture. Today, instead of proprietary interfaces and custom programming, engineers and IT management can find common connections in standards that grew from Windows and the Web.
Today, penetrating a firewall is getting as easy as Web browsing. But before going Pavlovian at the prospect, and leaving the security issues inherent in this arrangement aside for the moment, engineers have to ask questions of such Zen-like simplicity, the answers arent always obvious.
- What data do I need from the business system to run my process better?
- What data does the business need from me to run the plant better?
Data Down, Data Up
Most plants arent very integrated; reports circulating in the process industries indicate that fewer than 10% of plants have actually achieved a data path from the DCS up through the plant and into the ERP system.
Most orders and reports are still shared using email, phone calls, whiteboards and spreadsheets, but we are seeing more and more requests from our DCS users to automatically receive schedules, says Dave Emerson, director of Yokogawas U.S. development center. Likewise, he says, production, compliance and quality reports coming up from the DCS should be automated at any reasonable cost. At the top of the ERP-to-plant data pipe, a single human error can foul up inventories and schedules for days or weeks, and be discovered only when when trailers and tankers pull up or away.
The data an ERP system sends down to the plant depends on the bill of material. At Dow Corning, data import/export varies with batch, semi-batch and continuous processes. In addition to tracing and tracing material inputs betweeen the DCS and SAP, production reporting up from the DCS is typically every four hours for, say, a week-long production run; batch reports are sent at the close of each batch.
The whole business workflow is affected by these reports, so we cant allow plants to under-produce or over produce or run out of raw material, Zywicki says. Before his SAP-to-DCS integration project, he says process schedulers would create process orders in SAP, then go back to the batch execution system and retype the whole production scheduledate, time, materials to be made, resources to be used... it was a lot of work, and mistakes happened.
Typically the first data DCS users start integrating are final production outputsnumber or barrels of oil filled, gallons of gas, liters of material. But getting to and making use of even this low-hanging fruit has its challenges. Integrator Dennis Brandl, president of BR&L Consulting, says, the hardest thing is to figure out what that data actually means, to understand the production context.
Single-value data transmissions are obsolete; todays plants and businesses require much bigger data containers and manufacturing-specific software interfaces that can handle full, complex pieces of information; were talking about whole histograms of data, Brandl says. That kind of integration requires you to build processes on your shop floor or into your DCS system to keep collecting data and making calculations on it. Thats when integration gets harder.
Use the App Map
Brandls into building processes; hes chair of the ISA committee behind the ISA88 batch standard and editor of the ANSI/ISA95 family of control-to-enterprise integration standards. With roots in Ted Williams early-1980s Purdue Reference Model, 95 provides a model that end users, integrators and vendors can share in integrating applications at key layers in the enterprise. (For details on this model go to www.controlglobal.com/0810_Integration.html.)
Figure 1. Service-oriented architecture simplifies the links between upstairs and downstairs.
Only a fraction of production data need ever reach the business office in any direct fashion. Only about 10% of management data is exchanged with operations management applications; and only about 10% of operations management data is exchanged with the business side, says Dave Woll, consulting vice president with ARC Advisory Group. Every step up represents less information by an order of magnitude.
ERP may own cost accounting, and control systems may own loop parameters, but theres lots of functional overlap, in particular, at ISA5 Level 3. So while DCS and ERP vendors offer interfaces between their systems, usually the connection is through the DCS vendors historian, which reaches up to Level 3, which serves as a demilitarized zone to negotiate the architectural conflicts between real-time control processors and transactional business systems. It provides that middle zone where key enabling technologies meet.
For Zywickis ERP-to-DCS integration project at Dow Corning, RLINK, part of OSIs Pi System, provides the data map from above and below.
Ask a Historian
Historians and application databases have been relatively easy to access from above or below using SQL Server-type databases. Since the early 1990s, Open Database Connectivity or ODBC has provide a standard way to map data paths between business and plant systems relational databases.
In the mid-1990s, OLE for Process Control (OPC) advanced this mapping. The most familiar OPC protocol, DA (Data Access) provided a format to map data in real time and made custom drivers, such as the drivers that were once the basis for many a HMI/SCADA software vendor, obsolete. Another OPC protocol, AE (Alarm and Events), offers transactional, on-demand transfers; a host of others protocols specifically address historical data, batch data, server networks and a platform-neutral XML documents. The latter illustrates the convergence of IT and Web standards in the plant, which is no longer the exclusive domain of engineers.
The most ambitious OPC standard further reflects this. The first draft of OPC UA (Unified Architecture) was released in February 2008, with a final approved specification planned by years end. UA combines all OPC protocols into one, while shedding its Microsoft underpinnings for one based on a service-oriented architecture (SOA) that follows the World Wide Web Consortiums Internet standards. But UA will be years in coming.
The link between the DCS and the plant data system has become easier with the maturing of OPC, says Pat Kennedy, CEO of OSIsoft. The real issue is configuration and maintenance, not installation. Also the systems are getting so big that some sort of meta data is useful to understand the information, and this has to be configured too.
Integrator Timothy Alosi, vice president of engineering services with New England Controls, Mansfield, Mass., knows it. To connect two computers with OPC servers via an OPC mirror in an Emerson Delta V DCS, he first sat down at one computer and pinged the other one by IP address. Then I pinged it by name; then I created a shared directory on each side, and logged-in with the user I thought wed use for this computer. Then I checked to see if I could browse for the user and if I could copy files back and forth. Also in my Delta V, I had to set user priveliges for the right process areas... and I hadnt even gotten to OPC yet!
The two computers were sitting next to each other with nothing but a cable between them. Alosi says connections become exponentially more complicated by network swtiches, and once you want to connect to another site, its essentially impossible. Ive seen engineers pull their hair out and do a lot of yelling and cursing for two weeks to make an OPC connection work.
Markup of Maturity
In the control arena, all DCS vendors either offer a historian or tie to others, and they are typically installed with a firewall above. This presents problems for OPC, but not for SOA-generation tools such as Web services and XML that, by design, can traverse firewalls with the ease of Web browsing. And both have their purpose for plants trying to bring data above and below the firewall.
OPC is well known and understood by control engineers, and Web services are well known and understood by the IT guys, says Yokogawas Emerson, whose latest DCS architecture offers Web services. A few, or possibly a single engineer at a site will want to learn enough XML to convert ERP-level data into operational or control systems, so the guys doing the control applications and function-block work wont have to worry about it, Emerson says.
This will make life easier in the real world for empathetic IT leaders who seek to keep engineers as far from becoming IT specialists as possible, so they can focus on engineering their products and processes, says Zywicki, who is co-leader of Dow Cornings global SOA initiative.
The WBF organizations XML committee, which Dave Emerson chairs, is in its fourth release of Business To Manufacturing Markup Language (B2MML), a set of XML schemas based on ISA95 data models. Co-authored by Brandl, B2MML provides a royalty-free, common data roadmap. At present, the data mapping is still a manual affair, but broad adoption could lead to automation analagous to OPCs elimination of custom software drivers more than a decade ago.
At minimum today, SOA, Web services and XML serve as the state of the integration art and a utilitarian software linga franca.
Bob Sperber is a contributing editor to Control.
Web It
For more information of integration standards and techniques, log on to the following Web sites.
- OPC
- B2MML, BatchML
- WBF, The Forum for Automation and Manufacturing Professionals
- ANSI/ISA95
- SOA/World Wide Web Consortium
- Purdue Reference Model
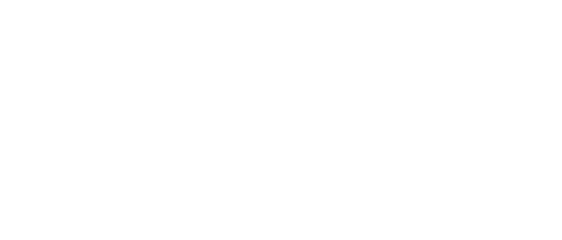
Leaders relevant to this article: