1
Networking to higher-level platforms
2
Advanced control algorithms
3
Extensive database manipulation
4
HMI functionality in one platform
5
Integrated custom control routines
6
Complex process simulation
7
Very fast CPU processing
8
Memory requirements exceed PLC specs
9
Interfaces thorough multiple protocols
10
Wireless access
"Distributed and remote I/O for use with PC-based control systems in industrial process industry applications is forecast to increase from $143 million in 2001 to $254 million in 2005. This gives PC-based control about 10.6% of the total control market in 2001 and a projected 14.5% of the total in 2005," according to Jim Taylor, a group manager with Venture Development.
Industry acceptance is growing, but what about cost effectiveness? This is perhaps the area where PCs have made their greatest inroads, and this trend is sure to accelerate.
Office-grade PCs decline in price on a seemingly daily basis, and industrial grade PCs now follow the same trend. "Several years ago the cost ratio of an industrial PC to an office-grade was about 4:1, but now the ratio has declined to around 2:1 or less," says Ed Boutilier, president and CEO of Stealth Computer (www.stealthcomputer.com).Industry acceptance is on the rise and costs are declining, so the only hurdle left for PCs in process control is reliability. Unfortunately for PC-based control vendors and their supporters in the user community, this is a high hurdle, largely due to poor past implementations of PC-based control.Windows Won't WorkIt is hard to escape history, and PCs in process control have a rather unpleasant past. Many users have fallen to the temptation of using low-cost desktop Windows-based PCs for critical process control, often with disastrous results. "The whole PC-based control scenario is riddled with amateurish implementations," observes George Turnbull, managing director of Open Automation and Control in Essex, England (www.oacg.co.uk).One of the main problem areas has been the Windows operating system. Desktop Windows is primarily designed for non-real time and non-critical applications. Earlier versions of Windows (prior to NT) were especially plagued by unexplained glitches, the blue screen of death, and frequent re-boots.As detailed in our May 2002 cover story, this problem has largely been alleviated by the use of real-time PC-based operating systems. In addition to the various embedded versions of Windows, such as CE and embedded XP, real-time PC operating systems are also available in Linux. Firms such as VxWorks (www.windriver.com), QNX (www.qnx.com), and LynxOS (www.lynuxworks.com) also offer rock-solid real-time operating systems.Table II: Industrial Grade PCs vs. Office PCsFeatures to consider
Industrial Grade
Office Grade
Can it withstand extended temperatures?
Yes
No
Can it withstand shock & vibration?
Yes
No
Is it dust proof, or does it have filtering?
Yes
No
Is it splash proof?
Yes
No
Does it have RFI/EMI shielding?
Yes
No
Does it have power surge protection?
Optional
No
What type of chassis construction?
Cold rolled steel, rigid
Flimsy, often plastic
Does it meet industry classifications?
NEMA/IP, MIL, etc.
None
What type of security does it provide?
Locking doors & drive bays
None
How much lifecycle technical support?
3-5 years
6-12 months
Does it provide Intrinsic Safety?
Optional
No
Mean Time Between Failure Data
Sometimes provided
Not provided
Mean Time to Repair
5-15 minutes
1-2 hours plus
Mounting & enclosures
Multiple Options
desktop or tower style
Is it fault tolerant?
Optional
No
How reliable are these systems? The control engine for Westinghouse's Ovation DCS (www.westinghousepc.com) is the VxWorks operating system running on dual redundant PCs. Ovation DCSs are used to control power and water/wastewater plants worldwide with some systems controlling over 10,000 I/O. The VxWorks operating system also is used to control the NASA Mars rover. The QNX operating system is used to control robot hands in surgical applications.Desktop Windows may not be ready for real-time process control, but other PC-based operating systems are. This leaves one last remaining hurdle for PC-based process control, and that is the reliability of the PC itself.
Gritty Bricks
A white box PC is not designed to run 24/7 in a harsh environment. Unfortunately for proponents of PC-based control, the first image most people have of a PC is the ubiquitous white box. Another problem is the moniker "soft PLC" to describe PC-based control. Users don't want soft, they want hard real-time. Vendors are trying to change perceptions, and some have chosen the lowly and humble but always reliable and rugged brick as a suitable icon.
"The small form factor, about the size of a brick, combined with DIN rail mounting allows the integrator to place the PC-based processor in areas not easily serviced by desktop or laptop PCs," says Wayne McGee, vice president of business development with SBS Technologies (www.sbs.com)."We currently only make PCs that plug into our PLC backplanes, but we are investigating standalone or brick-style I/O footprints," says Jim Allison, the PC control product manager with AutomationDirect (www.automationdirect.com).Bricks are good, and so is grit. "Our embedded CE-based controller is a PC with PLC grit," says Tom LeBay, director of marketing for Online Development (www.oldi.com). It is obvious vendors of hardened and embedded PCs are trying to change user perceptions about the ruggedness of PCs.The changes go beyond mere terminology. These PCs often have totally different form factors than a desktop PC. In addition to the aforementioned brick, other form factors include cards that plug into PLC backplanes, rack-mounted computers, and single-board computers. Table II summarizes some of the key differences between a desktop PC and an industrially hardened PC. Most industrial PCs won't meet all of these criteria, but all satisfy some of these specifications. Application needs drive users to select PCs with proper specifications, and we will next look at some process control applications to see where these rugged PCs are used.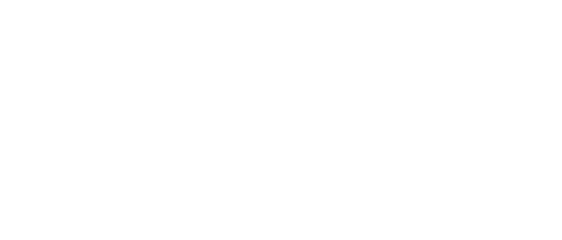
Leaders relevant to this article: