Recent developments are breathing new life into an established technology for the measurement of the most traditional of all industrial gases: oxygen. Innovation in analytical instrumentation for industrial gases, for example, the expanding use of NDIR sensors and miniaturization for CO2 measurement, have seemed to pass by the measurement of oxygen. That situation is no longer the case.
The oxygen molecule has mystical magnetic properties. These allow it to be measured using the paramagnetic technique. The discovery of this principle is credited to Sir James Dewar in 1891. (Dewar, a Scottish chemist, also invented and gave his name to the vacuum-insulated flasks that are extensively used today for cryogenic gas storage.) The operating principle of a paramagnetic oxygen analyzer has traditionally relied on a dumbbell, with two glass spheres that contain nitrogen, which is suspended on a fine wire in a strong magnetic field. The sample to be measured is passed over the dumbbell and oxygen in the sample is attracted by the magnetic field, which causes the dumbbell to rotate. Various techniques can then be used to determine the rotational torque, which is related to the amount of oxygen in the sample.
As an alternative, compact electrochemical cells are often used in oxygen gas detectors, but they have a finite life and are prone to drift and various interferences that make them unsuitable for high-precision measurement applications. Zirconia sensors are increasingly used for oxygen analysis in combustion applications, and tunable diode lasers (TDL) are also gaining popularity, especially for measurement of oxygen in flue gases. Despite these alternatives, the paramagnetic method has remained one of the favored analytical principles due to its linearity and robust operating principle. For measuring oxygen at percentage-level concentrations in inert background gases, it has been a default choice for instrument engineers for many years.
Figure 1: This solid-state "microwing" overcomes the drift often seen in paramagnetic oxygen analyzers that use traditional nitrogen gas-filled dumbbells. Source: ABB Automation GmBH
Despite decades of incremental product development, some paramagnetic oxygen analyzer designs have suffered from a small, but noticeable, drift, which led to the requirement for frequent calibration. A recent innovation has overcome that problem by development of a digital dumbbell, which has been incorporated into the Magnos28 analyzer by ABB. The main technical development that this instrument brings is replacement of the traditional nitrogen gas-filled dumbbell with a solid-state electronic “microwing” (Figure 1).
The microwing sensor reacts very quickly and accurately to oxygen concentration changes due to its very low mass, high width-to-thickness ratio, and optimized magnetic field distribution. Avoidance of lead solder and the use of advanced coatings also mean that the internal wetted parts of the Magnos28 oxygen sensor are highly robust (Figure 2). Furthermore, the influence of moisture is drastically reduced with this patent-pending technology.
Suppressed zero and high sensitivity
“One of the challenges for oxygen analysis in air separation [ASU] unit operations is measurement of the final product, as supplied to the customer,” says Micheal Moede, product manager, ABB Automation. “The difficulties associated with accurate measurement at and above the 98% level have, until relatively recently, meant the continued use of time-consuming, outdated and off-line wet chemistry techniques.
Figure 2: The microwing of Figure 1 mounted in an analyser chassis. Lead-free solder and advanced coatings make the internal wetted parts of the oxygen sensor highly robust. Source: ABB Automation GmBH
“When we developed the Magnos28 microwing paramagnetic oxygen analyser, one of our ideas was to apply the instrument in advanced air separation unit process control strategies. We can manufacture the instrument with various measurement ranges and of high relevance to industrial gases production is the 98 to 100% range. Imagine that we have compressed all the data that would normally be gathered in a 0 to 100% measurement range and crammed it into that tiny 2% band between 98 and 100%... that’s how ultra-sensitive the Magnos28 instrument can be.”
High sensitivity within the critical 98 to 100% measurement zone is not the only technical advantage. “The use of a suppressed measurement range is enabled by the introduction of a pressure sensor in the instrument,” Moede says. “This compensates the oxygen concentration reading and means that we can minimize the effects of air pressure changes on the sensor sensitivity to almost zero.”
When used in the 98 to 100% measurement range, calibration of the instrument should use a test gas with an oxygen concentration within this range. A high-accuracy gas mixture with a measurement uncertainty of only plus or minus 1% would be an appropriate choice to ensure that the accuracy of the calibration gas is consistent with the measurement accuracy of this high precision instrument.
The benefits of accurate final oxygen product measurement are realised on the ASU with reduced power consumption. Every small increase in oxygen purity requires additional reflux in the cryogenic distillation column, which requires additional electricity. To be able to measure oxygen with high repeatability and accuracy means that the operation can be run close to the optimum point with minimal risk and maximum reward. Furthermore, the very low drift on the instrument also reduces the required calibration frequency, which minimizes the required man-hours and labor cost for periodic calibration and testing.
Figure 3: Conventional and microwing analyzers were compared on this air separation unit at AlzChem in Bavaria, where distilling gases at unnecessarily high purities can be a costly waste of electricity. Source: AlzChem Group AG
Proven in the field
AlzChem, located in Bavaria, is an innovative manufacturer of specialty chemicals. The site uses different air gases for a range of production operations. These are produced on their own captive ASU (Figure 3). The operating costs associated with their ASU are primarily related to the cost of electrical power. This cost can be burdensome to site efficiency targets if process variables on the ASU are not closely scrutinized. Gas analyzers are used throughout the ASU to ensure efficient use of electric power and guarantee product quality.
The principal of ASU operation is to compress vast quantities of air and pass it through a series of heat exchangers and expansion turbines to liquefy the air. In this state, the cryogenic air is distilled and thereby separated into argon, nitrogen and oxygen. On a large ASU, the main air compressor can draw up to 15 MW—similar to the electricity consumption of a mid-sized town of 15,000 people. With rising energy costs, it’s becoming increasingly essential to optimize the output of the ASU and minimize the power consumption. This relies on robust process control strategies and high-precision process gas analyzers to guide the required process adjustments.
One of the most critical process control measurement locations on any ASU is the final oxygen purity. If the oxygen is impure, it will not be suitable for use in the subsequent downstream process applications. If the oxygen is over-pure, it’s an indication that the distillation has proceeded for longer than is required, and has been wasteful of precious electrical power. So, hitting the sweet spot drives energy cost savings directly to the bottom line and minimizes the production of off-spec product, which would be wastefully vented to atmosphere.
AlzChem has been using paramagnetic oxygen analyzers on the ASU for many years to measure pure oxygen final product concentrations in the range of 99.9 to 99.95%. In a recent field trial, they tested the Magnos28 oxygen sensor in parallel with their established device. Over a period of several weeks, the results of this field test showed that the Magnos28 provided better performance in terms of improved accuracy, tighter repeatability and reduced drift (Figures 4 and 5).
Figure 4: This comparison of microwing and conventional analyzers shows the microwing analyses stay in a tighter range with fewer abnormal readings. Source: AlzChem Group AG
Jürgen Wimmer, who is responsible for plant inspection at AlzChem, says: “We always work on continuous improvement to get the best-in-class manufacturing processes for our innovative products. The Magnos28 oxygen analyzer uses the latest technology with its unique design and manufacturing process. Therefore, it was a natural choice for us to test the Magnos28 in our air separation unit. We established that the oxygen measurement from the Magnos28 is more accurate, more precise and within tighter tolerances compared to the instrument that was previously in use. We are convinced of the improved repeatability and stability of the measurement, and confident that this will lead to reduced power consumption and reduced calibration-related operating costs on our site.”
Combined measurements
The compact design of the microwing technology allows it to fit alongside another analyzer inside a single housing. For example, oxygen measurement with the Magnos28 can team up with CO2 measurement using an NDIR sensor. Or, the paramagnetic device can be mounted in the same housing with a thermal conductivity detector (TCD) instrument, which could be suitable for measurement of nitrogen in argon.
Figure 5: Overlaying conventional and microwing analyser results in this histogram shows the microwing readings have a more normal distribution and smaller sigma than the conventional readings. Source: AlzChem Group AG
With the requirement to measure multiple components at various concentration ranges on a typical air separation unit, this can be an attractive option. Instrumentation capital cost savings result from avoiding the expense of an additional housing and power supply unit for the second analyzer. And, with space at a premium in most instrumentation shacks, the fact that two sensors are combined in one rack-mounted instrument leaves more room for other essential equipment.
“Technical innovation at ABB means that we can ‘write the future,’ and we are delighted when this can be combined with commercial benefits for our customers,” Moede says. “We’re very pleased with the market feedback, which tells us that the Magnos28 is absolutely fit for purpose and simply better value for money than anything we have been able to offer in the past.”
About the author
Stephen B. Harrison, managing director, sbh4 GmBH, can be reached at [email protected].
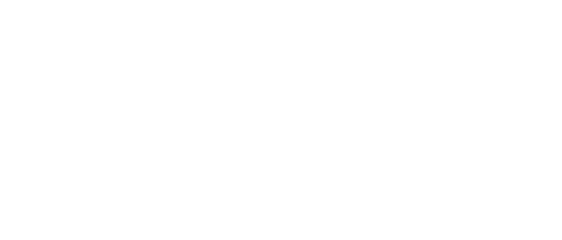
Leaders relevant to this article: