By Ahmed Hafaifa, Attia Daoudi and Mouloud Guemana
The most efficient operation of gas and oil installations is subject to many technical and economic constraints. Certain installations cannot stop functioning without incurring enormous financial losses, but technical defects can also harm the quality of their products. The SCADA system can prioritize necessary maintenance activities to prevent inopportune breakdowns, reduce the time fixed assets are under maintenance and optimize their operational life though just-in-time intervention. SCADA systems have successfully addressed numerous industry problems [1], [13], [15], [18] and [19]. In this article, we describe how SCADA systems could be applied to maintenance challenges in facilities of the Algerian oil company Sonatrach.
To illustrate the efficiency of the proposed supervisory schema for the process control, the SCADA system has been constructed as a centralized system using a proprietary control computer and operating system. The use of a SCADA system in a gas compression plant facilitates planning, assigning, supervising and participating in the operation, maintenance and repair of the system, and related work. The disadvantage of this centralized system is that when a facility wants to improve or add some functions, it sometimes has to upgrade the existing computer’s memory capacity or replace it with a higher-grade computer.
On the other hand, a recently emerging trend in the development of computer and communication technology has been making it possible to establish open, distributed computer systems. Such technology is also being introduced into SCADA systems in gas compression plants. In this article, we give the experimental results of the use of the SCADA system in a gas compression system for supervision and control and data acquisition. We found that the high reliability, functionality, performance and high-level human interface add to the expandability and flexibility in configuration.
This paper describes tools and techniques that can and have been used to model transient flows and performance, mechanical and control responses, and time-dependent head in compressor systems. The tools used by SCADA control include finite time step programs that simulate control systems, valve actuators and the opening (or closing) rate of valves, with the resulting flows. The volumes and lengths of station piping, scrubbers and coolers, including temperature effects are accounted for. SCADA supervisory control models also track the performance of centrifugal compressors at different speeds, account for the rotation inertia of compressor trains, and evaluate the thermo physical properties of gas streams.
Industrial compression system
Compression systems are used, for example, as part of a gas turbine for jet and marine propulsion or power generation, in superchargers and turbochargers for internal combustion engines, and in a wide variety of industrial processes [4]. In this paper we focus on centrifugal compressors that are used in natural gas pipeline transportation. This type of centrifugal compressor can exhibit a variety of instabilities under different operating conditions. Moore and Greitzer in [20] developed a phenomenological model for rotating stall and surge. This pioneering work modelled the compression system with just three components:
- The first component is the inlet duct that allows infinitesimally small disturbances at the duct entrance to grow until they reach an appreciable magnitude at the compressor face.
- The second component is the compressor itself, modelled as an actuator disk, which raises the pressure ratio by doing work on the fluid.
- The third component is the plenum chamber (or diffuser) downstream, which acts as a large reservoir and responds to fluctuations in mass flow with fluctuations in pressure behind the actuator disk.
In this paper, we are considering a compression system consisting of a centrifugal compressor, valve, compressor duct, plenum volume and a throttle (Figure 1). The throttle can be regarded as a simplified model of a turbine [7], [8], [10]. The system is shown in Figures 1, 2 and 3.
The model to be used for controller design is in the form:
The present work has analytically integrated the right hand side of equation (1), presented by three ordinary differential equations of the Moore and Greitzer model that give rise to modelling the compression system: the first for the non-dimensional total-to-static pressure rise across the compression system; the second for the amplitude of mass flow rate fluctuations m; and the third for the non-dimensional, spool moment of inertia [20]. The two first equations of (1) are equivalent to the model of [4]. Note that the Moore-Greitzer model does not attempt to explain what physical mechanism triggers these instabilities.
Surge in industrial compressor gas pipeline
Given the potential risk of damage due to violent surge oscillations, compression systems are usually operated at a safe distance from the surge line. The imposed safety margin limits the achievable pressure rise and ability to operate at off-design conditions [5], [6], [9], [12]. Surge initiation measurements are performed to determine the stability of the compression system. In Figures 4 and 5 the initiation of surge is shown. By closing the throttle valve of anti surge (Figure 2), the mass flow is decreased, and surge is initiated, as can be seen in the pressure ratio. The initiation of surge is defined as the point at which the amplitude of the pressure trace starts to grow, and a distinct oscillation frequency appears, which is pointed out in the lower right plot. Upon surge initiation, a surge development is recognized in which the fully developed surge occurs in the gas pipeline system (Figure 6). Due to a constant shaft power, the reduction of mass flow results in a slight increase of the mean rotational speed, N. The figure also shows that while the throttle valve is kept at a certain value, the rotational speed still increases due to inertia of the rotating parts.
The development of the surge is sketched in a compressor map in Figure 7. As the throttle is closed, the compressor performance follows the steady-state characteristic. (For simplicity a constant rotational speed scenario is followed.) At a certain pressure ratio the surge limit line is reached, and a surge cycle is initiated. Before reaching the limit cycle, some smaller cycles occur, as is seen in the pressure ratio. The stability line of the compressor is determined also from the transient measurements. Since for transient measurements into surge, the instrumented orifice cannot be used for reliable mass flow measurements, the relation between the throttle valve position and the mass flow, Equation (1), is used to determine the surge initiation mass flow. First, for different rotational speeds, the surge initiation points, i.e. pressure ratio, rotational speed and throttle valve position at initiation, are determined. Then the mass flow is calculated. As can be seen, the determination of the mass flow via the throttle valve position is reasonable, since the surge initiation points are close to the lowest measured steady mass flows [17], [21].
SCADA in Compression Gas Pipeline Systems
The SCADA system used in surge control of centrifugal gas compressors uses a high-performance PC-based data acquisition system, including Ethernet I/O, data loggers and programmable automation controllers (PACs)[14]. The system is shown in figures 8, 9, 10 and 11. PC-based data acquisition systems ready to fit a total solution for containing the constituents of distributed control system. Easy logic processes are effortlessly executed without involving the master computer because of the presence of a smart PLC or ladder logic [2], [3]. Ladder logic is a block programming language usually used to create programs running on remote terminal units (RTUs) or PLCs [11], [16].
A different software environment managed by a UNIX system is found in the SCADA center. SCADA system applications of the compressor station remote supervision and control to remote supervision of all pipeline facilities are shown in Figure 12.
Our proposal for detecting and isolating surge using the SCADA system approach to surge control follows. The idea is to control the compressor speed with feedback from mass flow so the compressor can operate in a stable mode even to the left of the surge line and thereby avoiding the unstable operation demonstrated in the results above.
Figure 13 shows the response of the compression system to the mass flow input and the associate residual. There is a value that the residuals consistently exceed during the surge operation. Figure 14 shows the response of the compression system for the mass flow input and the associate residual. In this case, the behavior of our compression system is considered nominal (without surge) and the residuals values are at zero.
Figure 15 shows the response of the compression system for the pressure rises and the associate residual. We remark a value that the residuals consistently exceed during the surge operation. Figure 16 shows the response of the compression system to the pressure rises and the associate residual. In this case, the behavior of our compression system is considered nominal (without surge). There is no a value for the residuals. These signals are exactly zero.
Conclusion
This paper described the implementation of a novel approach in gas compression system pipeline supervision using a SCADA system and substation controllers of the centrifugal compressor. Surge can be successfully detected and isolated, even though only a limited amount of the input/output data is available. The integration of advanced pipeline applications into the SCADA system in gas compression system supervisory guarantees safe operation of gas transportation. Other safety-improving features include the distribution of gas flow, SCADA system redundancy, dynamic line in SCADA displays according to pipeline content, and automation of compression stations with fault-tolerant surge protection. SCADA systems have been implemented using proprietary equipment, already including the effects of uncertainties that are based only on the input-output data in the tested gas compression system, but in this application we have described a way of implementing such systems over a distributed control system network and taking full advantage of generic, general purpose equipment. In addition, the results of the examined example demonstrate the quality of performance, and it was found that the system exhibits better performance responsiveness than the conventional system while maintaining the same high level of reliability.
Dr. Ahmed Hafaifa is associate professor in the Department of Technology Science in the University of Djelfa, Algeria
Attia Daoudi is associate Professor (MAA) at Djelfa University. He received his magister diploma in electrical and control engineering from the University of Blida, Algeria.
Mouloud Guemana is an associate professor at the University of Boumerdès, Algeria. His research interests include optimization of a measuring equipment of flow in natural gas, maintenance and reliability systems.
References
[1]. S.A. Avlonitis, M. Pappas, K. Moutesidis, D. Avlonitis, K. Kouroumbas, N. Vlachakis, "PC-based SCADA Systems and Additional Safety Measures for Small Desalination Plants." Desalination, Elsevier (2004), vol. 165, no. 15, pp. 165-176.
[2]. Chi Ki Sun, Varanon Uraikul, Christine W. Chan, Paitoon Tontiwachwuthikul, "An Integrated Expert System/Operations Research Approach for the Optimization of Natural Gas Pipeline Operations." Engineering Applications of Artificial Intelligence, Elsevier (2000), vol. 13, no. 4, pp. 465-475.
[3]. Gordon Clarke and Deon Reynders, Practical Modern Scada Protocols: Dnp3, 60870.5 and Related Systems. Newnes (2004), Book.
[4]. J.T. Gravdahl, O. Egeland and S.O. Vatland, "Drive Torque Actuation in Active Surge Control of Centrifugal Compressors," Automatica, vol. 38, issue no. 11, 2002, pp. 1881-1893.
[5]. A. Hafaifa, F. Laaouad and K. Laroussi, "A Numerical Structural Approach to Surge Detection and Isolation in Compression Systems Using Fuzzy Logic Controller." International Journal of Control, Automation and Systems, (IJCAS), Springer (2011), vol. 09, no. 01.
[6]. A. Hafaifa, K. Laroussi and F. Laaouad, "Robust Fuzzy Fault Detection and Isolation Approach Applied to the Surge in Centrifugal Compressor Modeling and Control." Fuzzy Information and Engineering, Springer (2010), vol. 02 no. 01, pp. 49-73.
[7]. A. Hafaifa, F. Laaouad and K. Laroussi, "Fuzzy Approach Applied in Fault Detection and Isolation to the Compression System Control." Studies in Informatics and Control (SIC), (2010), vol. 19, no. 01, pp. 17-26.
[8]. A. Hafaifa, F. Laaouad and K. Laroussi, "Fuzzy Logic Approach Applied to the Surge Detection and Isolation in Centrifugal Compressor. Automatic Control and Computer Sciences, Springer (2010), vol. 44, no. 01, pp. pp. 53–59.
[9]. A. Hafaifa, F. Laaouad and M. Guemana, "A New Engineering Method for Fuzzy Reliability Analysis of Surge Control in Centrifugal Compressor." American Journal of Engineering and Applied Sciences, (2009), vol. 2 no. 4, pp. 676-682.
[10]. A. Hafaifa, F. Laaouad and K. Laroussi, "Fuzzy Modelling and Control for Detection and Isolation of Surge in Industrial Centrifugal Compressors." Automatic Control Journal (2009), vol. 19, no. 01, pp. 19-26.
[11]. L. Krutz Ronald, Securing SCADA Systems. Lavoisier (2005), Book.
[12]. Marko Gerbec, "A Reliability Analysis of a Natural-Gas Pressure-Regulating Installation." Reliability Engineering & System Safety, Elsevier (2010), vol. 95, no. 11, pp. 1154-1163.
[13]. P.A.S. Ralston, J.H. Graham, J.L. Hieb, "Cybersecurity Risk Assessment for SCADA and DCS Networks." ISA Transactions, Elsevier (2007), vol. 46, no. 0 4, pp. 583-594.
[14]. David J. Smith, "Reliability of Software-Based Fire and Gas Detection Control Systems." Reliability Engineering, Elsevier (1985), vol. 12, no. 03, pp. 161-173.
[15]. A. Boye Stuart, Scada: Supervisory Control and Data Acquisition. ISA (2009), Book.
[16]. M. Scarrone, N. Piccinini, C. Massobrio, "A Reliability Data Bank for the Natural Gas Distribution Industry." Journal of Loss Prevention in the Process Industries, Elsevier (1989), vol. 02, no. 04, pp. 235-239.
[17]. W. J. Turner, P. S-J. Kwon, P. A. Maguire, "Evaluation of a Gas Pipeline Simulation Program." Mathematical and Computer Modelling, Elsevier (1991), vol. 15, no. 0 7, pp. 1-14.
[18]. Vinay M. Igure, Sean A. Laughter, Ronald D. Williams, "Security Issues in SCADA Networks." Computers & Security, Elsevier (2006), vol. 25, no. 07, pp. 498-506.
[19]. Zafer Aydogmus, "Implementation of a Fuzzy-Based Level Control Using SCADA." Expert Systems with Applications, Elsevier (2009), vol. 36, no. 03, pp. 6593-6597.
[20]. F. K. Moore, and E.M. Greitzer, "A Theory of Post-Stall Transients in Axial Compression Systems. Part I: Development of Equations," ASME Journal of Engineering for Gas Turbines and Power, 1986, vol. 108, issue no. 01, 1986, pp. 68-76.
[21]. Zhao Yang, Zhuang Xiong, Min Shao, "A New Method of Leak Location for the Natural Gas Pipeline Based on Wavelet Analysis." Energy, Elsevier (2010), vol. 35, no. 09, pp. 3814-3820.
Latest from Flow
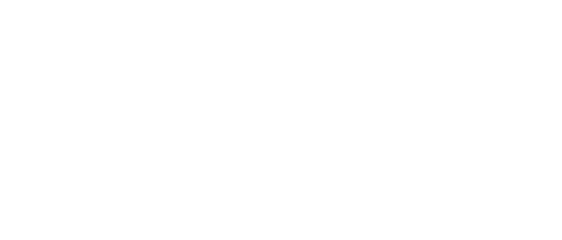
Leaders relevant to this article: