Strategically positioned in Bathinda, Punjab, HMEL’s Guru Gobind Singh refinery is an industrial anchor for the economic development of northern India. It sits at the northern terminus of a 1,017-km pipeline from Mundra, Gujarat, on India’s west coast, where tankers deliver the refinery’s raw inputs from abroad.
Formed in 2007 as a public-private partnership joint venture between Hindustan Petroleum Corp. Ltd. (HPCL, a government of India enterprise) and Mittal Energy Investments Pte. Ltd. (MEIL) of Singapore, HPCL-Mittal Energy Ltd. (HMEL) broke ground on the new refinery in 2008 and commenced operations in 2012. From the start, process automation had been at the heart of HMEL’s strategic vision of building a smart refinery. Leveraging the latest technology and partnering with the best helps the organization to deliver superior operational performance and profitability with strict adherence to environmental and safety standards. And at $5 billion USD, the 225,000-bpd refinery represents Punjab’s largest capital investment at a single location, and features a who’s who of technology licensors and partners—from UOP to IBM and SAP.
But if Krishan Tuteja, VP-Operations & Maintenance, has his way, they’ll be adding FCG to that list of acronyms on the company’s website. Indeed, the Guru Gobind Singh refinery credits FieldComm Group technologies with increasing company margins by $25M USD annually, and has just been named the 20th annual winner of Plant of the Year honors by the FieldComm Group. Each year, the leading standards development organization for process instrumentation recognizes an end-user company for exceptional and innovative use of the organization’s FDI, Foundation Fieldbus and HART technologies in real-time applications that improve operations, lower costs and increase availability. HMEL’s implementations accomplish all three.
“In our endeavor to maximize value creation, we continuously look to improve our processes, including more high value end-products, and pursue opportunities to expand our business,” explains Jatinder Kansal, Assistant General Manager, Instrumentation, who is responsible for implementing advanced analytical communication protocols. “As a young and technology-driven organization, HMEL moves swiftly to respond to the ever-changing energy market. Working with the communities around us, we aspire to build an organization that would shape a bright energy future for the country.”
Realizing the Industrial IoT
In addition to investments in state-of-the-art process automation, WirelessHART implementations at HMEL fall into the category of the Industrial Internet of Things (IIoT) and are part of a framework that HMEL calls the Digital Refinery of the Future. These use cases include using wireless sensors to track the sounds made by steams traps and valves, the temperature and vibration signatures of fin fan heat exchangers, and even the real-time location of plant personnel.
Leveraging the data from WirelessHART acoustic sensors from Emerson has allowed HMEL to monitor 138 control valves and pressure safety valves across eight refinery units for the passing of hydrocarbons. This can help to proactively manage environmental issues, advance the realization of odorless operations and recover the value of hydrocarbons that would otherwise be lost to flaring. The associated management application, part of Emerson’s Plantweb Insight offering, can alert personnel to issues via persona-based email notifications.
According to FieldComm Group's Intelligent Device Maturity Index, HMEL is pushing the envelope of best practices when it comes to leveraging the capabilities of digital field devices. See how your organization stacks up.
Steam traps, too, make different noises when they’re working than when they’re not. HMEL is also using WirelessHART-based acoustic sensors to monitor 23 steam traps across the FCC unit; stuck traps are flagged for fixing to control energy losses. Performance monitoring of 16 critical fin-fan heat exchangers draws on the wireless data created by magnet-mounted vibration probes as well as clamp-on-style temperature transmitters with surface-contacting RTDs. Five temperature transmitters and two probes per fan can detect and diagnose inefficiencies and emerging malfunctions before they escalate into an equipment outage.
Finally, field personnel at the fluidized catalytic cracking (FCC) unit are fitted with active RFID tags that a network of 66 location anchors and gateways can resolve to within 10 meters. The associated Plantweb Insight application can monitor the employee head count within the monitored area, alert when personnel cross into or out of their designated zone and facilitate safety mustering. And by pushing a safety alert button on their RFID tag, an employee can inform personnel that help is needed—and the system knows just where to find them.
Kansal attributes these successes not just to the choice of FieldComm Group technologies and their multi-vendor interoperability, but also to leadership support and to cross-discipline teams, including those responsible for instrumentation, process, operations and IT. In the days to come, HMEL plans to further its Digital Refinery ambitions by extending its successful valve and heat exchange monitoring to more as sets across the site, and to implement real-time location services in the sulfur recovery unit. It’s also on the lookout to develop more IIoT use cases within the refinery, and well as for associated petrochemical units.
Focus on innovation and efficiency
HMEL has also implemented world-class methodologies in areas such as manufacturing execution systems, operator training simulation and corrosion inspection management. “We optimize operations using a multitasking and cross-training of operations and maintenance personnel,” Kansal adds. “A best-in-class integration framework and enterprise performance management and reporting systems further support informed decision-making.”
In the realm of process automation and instrumentation, the refinery’s many systems include those for distributed control (DCS), machine monitoring, anti-surge control, tank farm management, fire & gas detection, governor control and emergency shutdown. Advanced instrumentation technologies at work include Coriolis, vortex and clamp-on ultrasonic flowmeters, nuclear and radar level gauges plus online stack gas and process analyzers.
The refinery’s installed instrumentation totals 61,521 devices, 24,440 of which are process instruments that communicate via 4-20mA HART (64%), Foundation Fieldbus (31%), WirelessHART (2%) or standard 4-20mA (3%). The other 36,081 devices are switches and other on/off devices (digital I/O). The refinery also features Yokogawa’s Plant Resource Manager (PRM) instrument asset management system; all Foundation Fieldbus and 80% of the plant’s HART devices are continuously connected.
Optimized for polypropylene
Polypropylene is one of the high value products for HMEL because of its wide range of application in petrochemicals. Consequently, the refinery’s FCC unit operates in high polypropylene production mode to serve the company’s captive polymerization units. It also relies heavily on Foundation Fieldbus for safe, reliable and robust process control, with 80% of the unit’s instruments on Foundation Fieldbus.
Because operation of the FCC process is particularly critical and complex, some Foundation Fieldbus instruments execute closed-loop control in the field overseen via advanced process control algorithms in remote cascade mode. These process instruments and associated control logic are configured in the unit’s CentumVP DCS leveraging fieldbus infrastructure from Pepperl+Fuchs. “We use fieldbus blocks where control is within field devices only,” Kansal says. “This helps in maintaining closed process loops in case of hardware failure in the DCS. All of our Fieldbus Foundation segments are designed with multiple link masters so that in case of DCS master card failure, Link Active Scheduling can be handled by any of the link master segment devices.”
Foundation Fieldbus instrument alarms are configured in the DCS with suitable priority according to EEMUA-191 guidelines so that early detection of instrument failures can be ensured. These Foundation device alarms are available not only for real-time monitoring, but are also connected to the refinery’s Yokogawa Exaquantum Alarms & Reporting Analytics (ARA) server for proactively deciding maintenance actions to head off potential failures.
Analog 4-20mA HART instrumentation is also used in the FCC unit. For example, to realize three-element control logic of steam-drum level in the unit’s flue gas heat recovery boilers, which provide both economic and environmental benefits. In short, the required boiler feed water flow is calculated based on both steam demand and drum level setpoint.
Other units, such as for hexane recovery and liquified petroleum gas (LPG) treatment also run with Foundation Fieldbus devices in closed-loop applications. “By following good maintenance practices and ensuring increased availability of Foundation instruments, we are able to sustain refinery operations and are continually improving our refining capacity in a safe and clean manner,” Kansal says.
Benefits from execution through maintenance
The early decision to use Foundation Fieldbus instruments when the refinery was first designed provided advantages in terms of execution schedule and project cost, according to Kansal. “With various good engineering practices and meritorious maintenance techniques, we at HMEL not only reduced capital expenditure by selecting Foundation Fieldbus technology for complex process applications, but also increased availability of instruments and reduced maintenance costs.”
One tangible demonstration of the power of Foundation Fieldbus data was in February 2021 when FCC throughput was restricted due to flooding issues in the debutanizer and depropanizer columns. Staff were able to diagnose and resolve the problem in short order owing to the higher availability plus higher accuracy, repeatability and response time of Foundation Fieldbus instrumentation. Quickly resolving the column problems led to an incremental improvement in FCC throughput of 7%, which in turn translated to a $11.2M USD gain in annual output.
Some of the best practices and design improvements for Foundation Fieldbus carried out at HMEL for increased availability of the refinery process include:
- Use of trunk/spur signal ground correction to avoid noise issues,
- Use of field barrier terminators for signal level improvement,
- Use of silica gel bags and canopies for Foundation Fieldbus junction boxes and instruments to increase life of electronic components due to varying ambient conditions,
- Installation of spur-level protection barriers to protect Foundation Fieldbus devices in same segment, and,
- Ensuring lightning protection device integrity for field junction boxes.
Field instruments with HART capabilities also offer high availability, accuracy, response time and repeatability. Further, the ability to digitally share HART diagnostics data facilitates real-time monitoring of field instruments and their performance.
For HMEL, the combination of Foundation Fieldbus and 4-20mA HART technologies offered the following qualitative benefits:
- Reduction in capital expenditure,
- Fast project execution to schedule,
- Higher availability of instruments (i.e., lower downtime),
- Reduction in maintenance expenditures,
- Uninterrupted plant operation,
- Reliable, stable plant operations for more effective optimization efforts,
- Higher accuracy, repeatability and response time,
- Ability to detect failures in advance,
- Easy and quick diagnostics/troubleshooting, and
- Higher rate of on-spec production
A role for wireless
While wired FieldComm Group technologies are widely used and contribute significantly to HMEL’s safe and reliable operations, FieldComm Group’s WirelessHART technology has also been used to troubleshoot problems and implement solutions impractical or impossible with wired solutions.
Back at the FCC, for example, the flow of catalyst between the unit’s reactor and regenerator are controlled through slide valves installed at the regenerated catalyst and spent catalyst standpipes. Air and nitrogen purges promote proper fluidization and helping to minimize blockages and ensure smooth transfer of catalyst. During normal operations, it became important to continuously monitor purge pressures so that any blockage of catalyst can be detected and dealt with early.
For this situation, HMEL turned to Rosemount WirelessHART pressure transmitters as well as wireless repeaters and gateway from Emerson, which were connected to the DCS via a Yokogawa Modbus TCP card. Wireless pressure transmitters were installed at 13 different points to understand the pressure profiles more completely.
Using wireless instruments significantly improved execution schedule with minimum manpower compared to conventional wired instruments for this same application. More than 2-km of control cabling was avoided, saving nearly $100,000 USD in project costs. More importantly, the ability to characterize the pressure profile more completely in the standpipes has allowed the operators to proactively clear any imminent blockages during a relatively brief pit-stop—rather than the 20-day shutdown required to clear a larger, more complete blockage. With downtime due to this issue effectively cut in half, HMEL estimates a $14M USD gain in refinery output for the year.
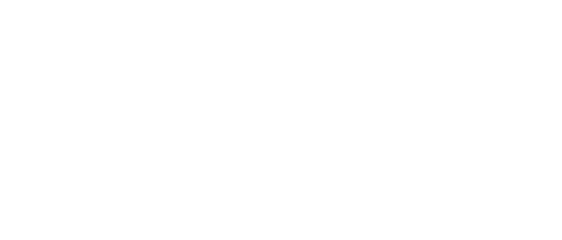
Leaders relevant to this article: