A look ahead: what does the next year hold for U.S. manufacturers?
Amanda Del Buono is joined by Deanna Nord, Principal of Nord Strategy Group, speaker and contributing writer to plant services in the journal magazines, as well as other publications, to discuss how the industry was impacted by 2020, and what 2021 has in store.
Transcript
Amanda: Hello, and welcome back to Manufacturing Tomorrow's Workforce. The podcast that discusses today's workforce challenges in the U.S. manufacturing industry. I'm Amanda Del Buono.
Kicking off season three, the manufacturing industry is coming out of what could be argued as one of the most challenging years we've seen in quite a while. Some manufacturers had to completely shut down, while others significantly reduced their workforce to accommodate COVID safety regulations and try to continue to produce products. And yet others even started producing different products from their normal. I'm thinking companies in the food and beverage alcohol space who swapped production to make sanitizers, and other products that helped the costs.
So, to kick off our season, Deanna Nord, Principal of Nord Strategy Group, speaker and contributing writer to plant services in the journal magazines, as well as other publications, is joining me today to help us reflect on the challenges that were overcome in the past year, and take a look ahead as to how the pandemic could change the industry and impact its workforce going forward and what solutions are available.
Deanna, thanks for joining me today.
Deanna: Thank you. I'm happy to be here.
Amanda: So, I kind of want to start out simply, everybody was challenged by 2020. And you're in touch with a large number of manufacturers. What were some of the challenges you heard manufacturers facing last year—March, April, May—and how did they overcome them?
Deanna: Well, first, I think we're all familiar with some of the challenges, but many mentioned lack of raw materials, disrupted supply chain, so lack of supplies. Therefore their rising costs of materials and supplies. Or just, I guess, still not having some shutdowns, layoffs, and then just a constrained workforce with getting used to masks and all the procedures that were required for temperatures taken, more breaks, staggered work attendance, staggered lunch breaks, the workstations were definitely more spread out than before times. And in some cases, manufacturers moved to a different location to save money, save on taxes. And as far as talent, there were also restrictions where they wanted talent from outside the U.S. and could not bring them in.
So, there's many ways that they overcame those, just trying to find different supply chains, you know, they brought people back. A lot of the manufacturers I've talked to have slowly brought everyone back. So, they're finally back to at least a pretty full workforce. And they're just sort of in the routine now of all the procedures taken. There's still of course restrictions on talent from outside the U.S., but they are managing their costs in every area, and managing the precautions they need to take.
Amanda: So, now we're into 2021, based on what you're hearing what marks or maybe permanent changes has the pandemic, or the past year or so, left on the industry?
Deanna: Well, there's still a lack of materials and supplies. You've probably heard, in fact, President Biden talked about the need for more computer chips. I have a contact in the automotive industry, he is a supplier to the automotive industry. He can't supply what they need from him because of lack of raw materials, metal to be exact, and there is a dearth of computer chips that is expected to continue, and they are expected to be more expensive. That alone just the computer chips, for example, in the automotive industry has taken it has removed 3.4 million cars out of the first quarter built. So, just simple supply chain disruptions can have quite an impact.
There's still time delays and deliveries of supplies because, you know, customers want products in a normal timeframe, and the constraints on labor are still there. Since we're early in the vaccine rollout, the measures are still in place, and they try to perfect them even more. Just still maintaining social distancing, good hygiene, making sure all employees are fit and healthy, and also working with remote collaboration with the plant floor or with the central office as much as possible. And, you know, I'll get more into that later on.
Amanda: Clearly, there were some verticals that saw growth during this pandemic. I'm thinking pulp and paper and chemical processing, but others didn't. And supply chains were also stressed quite a bit. What trends are you predicting for the next year as we hopefully start coming out of this pandemic?
Deanna: Well, I would say that some of those verticals that saw growth will continue to. Plastics is another one particularly for consumer products, home products, of course the health industry experienced a lot of growth. And I would say manufacturing 4.0 is having its moment. So, that I feel was a big area. A good note is that this pandemic and the challenges have accelerated investment in digital technology, and I think this will help to use a word we've been throwing around a lot, immunize manufacturing against future pandemics or health issues of any kind, weather issues across the world. A survey from Hitachi Vantara said that 48 of manufacturers already use robotics and automation, and that helped them overcome the challenges of the COVID. And 41% plan to increase those investments.
And what I've been hearing across the board is that automation is, and we've seen it before, improving worker safety, job satisfaction, labor productivity and reduces their cost as well. And that remote collaboration we'll just continue with that. There's also a recent McKinsey survey report on manufacturing 4.0, which I would recommend, and they surveyed manufacturing and supply chain professionals at 93 plan to focus on resilience of their supply chain and 90% plan to invest in talent for digitization. And since I've talked to a lot of small and medium-sized enterprises, I will say that what I've observed and know is that there's a lot of inexpensive retrofit automations that can be done for digital work instructions, augmented reality-based operator assistance, digital performance management, digital maintenance, regardless of what kind of infrastructure they have for automation right now.
I've seen it in practice on a very old piece of equipment where you simply add a digital sensor, and make sure that data is collected, and seen real time on a dashboard somewhere. So, there's a lot even in this financially challenging time for small to medium-sized companies, there's changes they can make like that. And then, of course, companies that already have IT or OT manufacturing, execution systems, data lakes, they will just accelerate those even more. They can really increase their supply chain planning, operational issues, delivery challenges. A lot of planning for all parts of manufacturing have been really siloed. So, when people start automating more, and bringing in these digital solutions, they can really improve that transparency and end-to-end visibility.
And what I also think is encouraging is that some of the new forecasting will go beyond some of the previous ways of using algorithms that maybe only use internal data to use AI and machine learning so they can take advantage of external data from suppliers and customers use weather, demographic and economic indicators in a greater way, incorporate it day-to-day. And two, I'm very fond of wearable technology, as we all are, and that has of course started to be a big boon with manufacturers. There's a company I'm thinking of in particular that has sensors that really improves workers' safety on the shelf on the plant floor. There's machine vision technology, contact and location tracing. Yeah, there's a lot of fixes as well as more long-term, bigger investments that can be made.
Amanda: Right. And that's interesting, because I have noticed in Putman's Control magazine, on the robotic side, they reported some statistics from the Robotics Industry Association about the growth in robotics orders in 2020, highly driven by pharma and food, which is abnormal considering it's normally driven by the automotive industry. And in that magazine, they've also talked a lot about recent growing interest in digital transformation investment, which was something that's been talked about for quite a while, but it seems like nobody had such a fire lit under them to really invest until now.
Deanna: And it's interesting, you know, we used to talk a lot about just-in-time manufacturing. Now, manufacturers are starting to talk about ways to stabilize the inventory rather than rely on that just-in-time because of this situation, which I think is really interesting. Though, to your point, more than a third manufacturers in a recent MPI study plan to implement IoT, and 32% plan to embed it into their products. So, yeah, it's a big change or a big acceleration.
Amanda: Yeah. So kind of switching gears here, I'm curious what you're hearing regarding organizations that underwent furloughs or temporary layoffs. Are these still ongoing or have manufacturers been able to start bringing people back since vaccines have become somewhat available?
Deanna: What I have been hearing is they have brought them back. It was a slow process, but they now have them back, and I think partly it was just a way to, as business started improving, they began bringing them back and also develop more routines to keep people safe. There's a few that I've been told still have people on furlough, and there's still the concern about bringing other talent in from outside the U.S. But I will say just on that note, I'm reading a lot about shortening supply chains, bringing them closer to their plants. Of course, some manufacturers have plants in many places, so that doesn't always work. But there is a trend away from China to consider U.S. or elsewhere. Mexico, Canada, Europe. But I think that that said, I think, and what I've heard from people, is that if you have products to export, there's really a great opportunity for that right now. And in the opinion of some manufacturers, they feel that manufacturing in general is not taking full advantage of that, and that probably will come with time as we get farther past this pandemic.
Amanda: Right. Well, to take a look ahead, if you were a manufacturer looking at the next year or two, what would you be preparing for and what would you be doing now?
Deanna: Again, to underscore what I was talking about before, you want to build the muscle to address future disruptions, whatever they are. Take stock of what you've learned, so better ways to do business like automation, like old supply chains, you know, establishing those relationships or developing new ones. Looking at long distance customers and establishing new ones. Build your exporting business. But I have to say that one of the key things when I say build a muscle, all manufacturers, all businesses need to be agile. So, you want supply chains that will withstand these disruptions. Be prepared for higher labor costs, possibly higher trucking costs, higher costs of supplies and raw materials. That's kind of an unfortunate thing I'm hearing.
And this, again, could change over time. You can reduce cost with some of the investments and automation over time, or even in some of the short-term, lower cost investments. But I would continue making the investments in automation and also in talent. I'm hearing over and over again that manufacturers need training and new technologies that know their culture in their plant. So, I would reinforce that as much as possible, and that means really looking across and reinforcing diversity in hiring. Looking at any biases and looking at social responsibility and diversity, of course, but labor practices sustainability because buyers in B2b and B2C are looking at that. They're looking at the supply chains, corporate government, social good.
So, I think it means looking at yourselves, looking at vendors, and I think it's a great way to build relationships with vendors and customers. But to start all that out, you want to establish criteria. Do social impact assessments, something that I do and others do, because there's a book I read, which I'll recommend, I'm reading actually, "The Riches of This Land" by Jim Tankersley, who's a writer for The New York Times. And when I speak of diversity, when you think back, and many people have talked about this as well, he's not the first one, but it's a good book. When we brought women and others into the workforce with World War II, we had the biggest era of productivity ever in the United States, and in this book, he is looking back at that and how that happened and where we are now.
So, I think that that's important. And I think that it's as important as financial performance when you are looking at your entire industry. And there is an organization I've worked with from time to time or talked to some of their clients, Manufacturing Renaissance, which has a 35-year history of advancing sustainable development in manufacturing, and they have looked at all these areas and just did a pilot project, a really promising demo project last year, working with government agencies, labor industry partners, and successfully worked with small to medium manufacturers who were able to utilize parts of the program for growth transitioning in different areas. So, they hope to grow this model with the learnings from the pilot. So, they looked at all the areas I'm mentioning, and just dependent on the manufacturer as well as some larger manufacturers.
Amanda: Well, here's to staying optimistic about the year ahead. Thank you so much for joining me today, Deanna. I really appreciate your time and insights. And hopefully some of our listeners will take some of your advice in that last question there and get themselves prepared and protected for whatever could come in the future.
Deanna: Thank you.
Amanda: For Manufacturing Tomorrow's Workforce, I'm Amanda Del Buono. Tune in next month when Tom Moriarty joins me to discuss how manufacturers can attract employees when they begin hiring again. Thanks for tuning in.
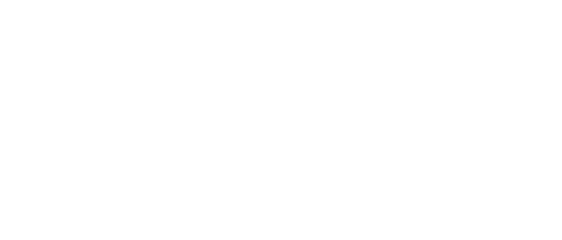
Leaders relevant to this article: