Few events of any kind survive for 40 years, but today in San Antonio 1,200 attendees from 34 countries, representing 302 companies in 47 industries, paused for a moment to celebrate the 40th anniversary of the Honeywell Users Group (HUG) conference, the oldest running event of its kind in the industrial automation business.
Then they got down to business. “Since Q4 of last year, since oil prices have changed, capital investments have been reduced,” said Vimal Kapur, president, Honeywell Process Solutions (HPS). Investments were up about 20% in 2010 and 2011, and remained flat through 2014, but so far, 2015 is down about 12%. Operational expense spending is also off. “We are highly sensitive to this and understand the business challenges,” Kapur said. “Different experts offer different future scenarios, but for now and for the foreseeable future, we are in a challenging time when it’s harder to justify investment and spending is reduced.”
At the same time, half of plants are more than 30 years old, and the baby boomers who built, ran and maintained them are “retiring very quickly," Kapur said. “With older plants and loss of talent, technology must play a larger role.”
The open systems of past decades are reaching obsolescence, and operating systems such as Windows XP are no longer being supported, which is causing disruption. “Cyber attacks are increasing,” Kapur said. “They say there are two kinds of plants: ones that have been attacked, and ones that don’t know they’ve been attacked. Every day I hear of another incident. The intensity is rising dramatically.”
“Different experts offer different future scenarios, but for now and for the foreseeable future, we are in a challenging time when it’s harder to justify investment, and capital spending is reduced.” Vimal Kapur, president, Honeywell Process Solutions at HUG 2015.
Environmental compliance calls for ever more monitoring and reporting. “We must do it, but it’s hard to see the ROI,” Kapur said.
“Safety remains our highest priority, but progress is plateauing,” Kapur said. “For all industries combined, we’re down to about 3.5 incidents per 100 full-time workers, but we’ve stuck there since 2009. How can we break through to lower levels?”
Owner/operators, Kapur said, are specifically challenged to do more with less, operate safely and in compliance, leverage technology to stay relevant and manage the rising skills gap. Kapur described how Honeywell is helping operators meet those challenges with strategies, technologies and services.
First, Honeywell will expand the role of the distributed control system (DCS). “Historically, we created islands of automation in the DCS, PLC (programmable logic controller) and electrical systems. It’s been productive, but complex beneath the covers,” Kapur said. Now, the DCS has become a focal point of all control functions, taking on the functionality of PLC, alarm, safety, power management, historian, turbine control and more. Having a single system and user leverages scarce resources, and a single platform leveraging standards does more with less.
Second, cloud computing is becoming a standard part of HPS automation projects, with a logarithmic increase in the number of virtual machines in the HPS cloud over the past two years. Using virtualization simplifies the factory acceptance test (FAT), and using cloud tools to provide configuration data directly to transmitters can reduce configuration and setup cost as much as 60%, Kapur said. “For one or 100 instruments, it’s OK. For thousands, it’s a big deal.”
The cloud also is facilitating training, offering higher flexibility and accelerating availability of operator training services (OTS). Kapur said, “The cloud is real; it’s not just a Powerpoint slide. Adopt it or be left behind.”
Third, while process safety management has always depended on detecting unsafe situations, preventing them from causing an incident or accident and protecting people from any consequences, “We must push those principles to raise the level of safety performance,” Kapur said. He asked attendees to look to technology for ways to improve safety and to share use cases. “More can be done to make safety a more rigorous solution,” he said.
Fourth, for cybersecurity, Honeywell has created a team of specialists who can do audits, identify vulnerabilities and recommend solutions. But cybersecurity requires constant monitoring, so consider using a cybersecurity dashboard, “a step toward enabling a much higher level of proactivity by identifying cyber threats before it’s too late,” Kapur said.
Fifth, standardization holds great promise for reducing cost and time to production by allowing pre-engineering of control systems. For example, shipping an engineered gas skid with controls already installed takes automation off the critical path and reduces the time to first gas by six months. HPS is working with sister company UOP to apply the same approach to large process units, such as for aromatics or naphtha, using standard schematics, master tags and interfaces.
Sixth, Honeywell continues to expand and refine its field device products to offer a complete line of smart instrumentation that can be preconfigured and use the cloud for fast auto-commissioning, and that have full auto-alerts and diagnostics to enable predictive maintenance.
Seventh, OPC UA is becoming the key to leveraging the Industrial Internet of Things (IIoT). “We see two kinds of things—the ones connected to the DCS and everything else,” Kapur said. “OPC UA provides standard communications for everything else. There’s something big here that we all need to think about.”
Eighth, Kapur told attendees their existing investments are not fully leveraged. “Point solutions are solving specific issues, but those issues are not aligned with objectives like safety, efficiency and optimization,” he said. “Bring point solutions together through dashboards and workflows to make your existing investments work harder.”
Ninth, expansion of mobility is changing workflows and the responsibilities of individuals. The way we work will change dramatically in ways we are only beginning to see and imagine.
Tenth, Honeywell is driving more outcome-based solutions in services. For example, if uptime is what you need, that becomes the definition of the solution, rather than a specific product or service. “Outcome-based contracts broaden the scope and let us bring our full range of capabilities to bear,” Kapur said.
In summary, Kapur said, as you deal with the challenges to do more with less, operate safely and in compliance, leverage technology and manage the skills gap, think about tools and methods to make technology a resource.
“We live in a world of apps that make tasks easy and simple, so you expect a similar ease when working with Honeywell,” Kapur said. “We have taken it seriously that not only great products, but also great service will differentiate us. So we will continue to improve with your feedback, so we continue to solve the right problems.”
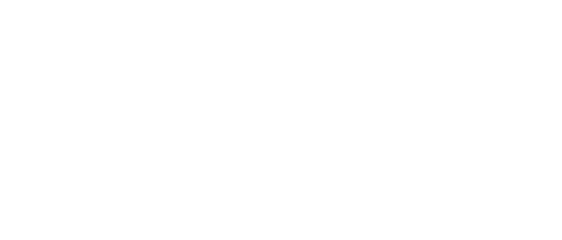
Leaders relevant to this article: