The manual, in-house approach means hours measuring, marking and drilling/cutting enclosures and back panels by hand, using basic drills and jigsaws. Most marking and measuring consists of placing the physical components, marking their locations, removing them for drilling/tapping and finally, placing the components again for final mounting. To ensure consistent and professional results, extra precaution must be taken, adding time to the process.
"It's common for panel shops to do their own holes and cutouts due to their perceptions of speed and cost, but they often use an expensive wireman with a slow, imprecise jigsaw," says Rick Maday, marketing manager, Hoffman and Steinhauer, Pentair Equipment Protection. On a stainless steel cabinet, they may take one or two days making cutouts before they can start populating with components.
"It's ironic that they're using the most manual, un-automated way possible to make automation panels," Maday continues. "And the vast majority are designed using CAD, but then they're printed out as PDFs with all the information stripped away so the panel shop can manually measure and mark the cabinets to drill, tap and saw."
Figure 1: A common belief is that castings machine like wrought alloy. In fact, machining castings can raise issues with porosity (NADCA standards), tool breakage, speeds/feeds and draft angle compensation.
Phoenix Mecano
"A lot of people downstream think customizing enclosures is easyācut, paint, labelābut it's not," says Bruce Bator, engineering director, Phoenix Mecano. "A cast aluminum panel is not like 6061āyou can break a lot of tools. A lot of special things have to happen to get a polycarbonate panel painted or molded in the right color. It's not just a rattle can of Krylon."
Source it out
Many panel shops recognize these problems and choose to outsource modifications to enclosure companies or specialized suppliers. "Our Focus Factory makes holes and cutouts in doors and mounting panels, and arrangements of mounting rails," says Steve Sullivan, training supervisor, Rittal. "We can include climate controls or busbars. We can bay the enclosures together and ship them on a single pallet, all sealed and ready. We can leave the sidewalls off or put them on, and meet specifications like NEMA 12, 4 and 3R, in 28 standard colors, with mechanical maintenance locks hooked up and ready to go from the factory."
{pb}
Enclosure manufacturers are a logical choice for rigorous, complex applications, especially if they specialize in the kind of enclosure you need. When NestlƩ decided to put electronics on their production floor, the company turned to ITSENCLOSURES for advice. ITS assessed the environment, including temperature extremes and chemical washdown, as well as the requirement to use off-the-shelf PC systems and desktop monitors. It recommended a NEMA 4X stainless steel enclosure, and appropriate input (keyboard and mouse) devices (Figure 2).
Figure 2: NestlĆ© chose purpose-built NEMA 4X stainless steel enclosures to house off-the-shelf PCs and desktop monitors for extreme temperatures and washdowns. Ā
ITSENCLOSURES
With control panels full of components such as terminal blocks, DIN rails, controllers and relays, "You may find you want a 140-in x 78-in. enclosure, and nobody makes that," Bator says. "We can make a custom ābuild a box' as deep or as long as you want. They're fixed in two dimensions, but the third can be anything. This can allow you to be pretty flexible, but they're more expensive than a standard enclosure."
Along with meeting the specifications required for the ratings, Bator points out that as a supplier, they take responsibility for problems or mistakes. "In polycarbonate, ABS or nylon molded cabinets, there are design issues and molding stresses," he says. "If you order 100 enclosures from us, you get 100 good enclosures. If you order 100 raw enclosures and something goes wrong in machining, coating, etc., that's on you."
Automate it
While suppliers strive to supply perfect enclosures quickly, "typically in two weeks," says Bator, many integrators and end users want the flexibility, control and value-add they feel they can only get by doing it themselves. Some are increasing in-house productivity and precision by using automated cabinet drilling, tapping and cutting machines.
Utility Control & Equipment Co. (UCEC) a panel shop in Arvada, Colo., has been using a Steinhauer ModCenter MD80 for more than a year. "We considered laser cutters and plasma tables, but they were not the right fit," says Zach Fothergill, operations support manager, UCEC. "We saw a competitor's cabinet machine at Automation Fair two years ago, then we learned about Steinhauer, which was more cost-effective, more accurate, and has a bearing spindle which is more durable. It also has pneumatic clamps, a conveyor and automatic zero, which are more user-friendly."
Figure 3: The Steinhauer ModCenter uses an X-Y spindle with multiple, interchangeable tools to CNC-machine cabinets, back panels or any flat material that fits.
Pentair
UCEC has trained on AutoCAD, and has been building a library of components for programming the machine. "We don't have to have the components to do the layout but we like to see the parts before we add them to the library," Fothergill says.
Before UCEC got the MD80, "Laying out by hand, drilling and cutting with a jigsaw could take a week," Fothergill says. "Now we can design ahead of time and machine quickly. Panel users get their panels a week faster, which can make a big difference. And we save the files so for repeat jobs, there's no additional design or layout time."
Fothergill says now that they have enough experience, every job runs through the machine unless it's too large to fit. "Even very small jobs, the kind where I initially thought, āOh, it's too little to bother with. We'll just have a guy drill it manually' goes through the machine. A recent small job took about three minutes to program and five minutes to drill. Meanwhile, my team did other things.
"In the past, that small job would take one shop craftsman 30 minutes. So, added up all together, as we've become more fluent with the CAD design, the shop is saving time on each job, no matter how large or small."
Along with speed and labor savings, "Accuracy is huge," Fothergill adds. "Things end up exactly where they need to be, cutouts are the right shape and not oversize so they seal correctly and we don't lose purge."
The ModCenter is "a huge opportunity for efficiency and productivity gains," says Maday. "The value-add in a panel shop is not cutting holes. Technicians spend less of their time on non-core activities and more on value-add."
A ModCenter can pay for itself with a few enclosures per week and many end-user companies in Europe are putting them in-house, but most U.S. enclosures are modified by independent panel shops or system integrators. Hoffman has announced a program to distribute ModCenters in Hoffman Certified Modification Centers across the United States. "Integrators can stop wasting time making holes and cutouts manually, and let their local Hoffman distributor deliver enclosures and back panels pre-drilled and ready to populate," says Maday. "By using the extensive local market inventory, integrators can enjoy pre-modified enclosures and back panels in as little as one day."
{pb}
Refine your design
Regardless of who modifies your enclosures, it behooves designers to draw on their expertise to get the best results. "We are experts in our productsāwhat can be modified and how," says Phoenix Mecano's Bator. "Leveraging our expertise and knowledge can eliminate a lot of heavy lifting. We advise on manufacturability to quickly, efficiently and cost-effectively give you the product you're looking for."
Using a proven CAD library can help prevent problems, streamline communications and build a knowledge base to save trouble later. "Sometimes rookie engineers scale drawings inaccurately," says Fothergill. "We used to find that out at layout, now we find them in design. Then we can communicate problems and changes with highlighted CAD drawings where I used to have to get up on a ladder and take a picture."
Fothergill incorporates the necessary clearances (for example, 4-in. or 2-in. spacing to dissipate heat) into the symbol library so they're not overlooked.
"We can provide layouts for customers who don't do their own, and can quickly offer alternative layouts," Fothergill adds. An open communication pathway from the panel shop to the engineers "is always nice," he says. "They are not always as familiar with all the components, and what other companies and other industries are doing. Since we work in many areas, we're a little more well-rounded than any one firm, so we can offer different perspectives."
Rittal's Solutions Engineering Group can figure out how to do unique designs using standard product, to convert a custom cabinet to standard. "We can take your vision, keep your features and lower the price," says Sullivan. "Most people only think of purchase price. They need to include āuse costs,' and those tend to have an inverse relationship. We are not the highest and certainly not the lowest price, but we minimize use costs."
Bator sums it up: "Sit down and talk with one of us early to get what you need at a price you know about ahead of time. Avoid sticker shock. It's not just a box."
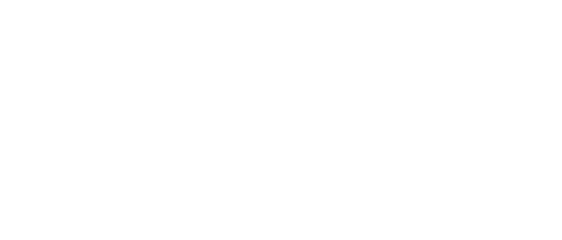
Leaders relevant to this article: