- Benchmark & Assessment
- Alarm management philosophy
- Alarm analysis / rationalization.
- Implementation and execution
- Continuous improvement
- Maintenance
This article will examine the first phase, Benchmark & Assessment, as it relates to justifying alarm management projects. For more information about the other Alarm Management Project phases, please refer to Senior Applications Engineer, Michael Marvin’s whitepaper, “Five Steps: Integrating Alarm Management to Boost Production.”
The Alarm Management Assessment
Alarm management assessment is comprised of three sub-sets:
- Technical Benchmark & Assessment
- Business Justification
- Project Plan
Technical Assessment addresses measurable and philosophical information associated with the current alarm system. Quantifiable metrics are based on static alarm configurations (static alarms are the alarms that are configured on an analog or digital input, or control block on a control system) and real-time, or dynamic alarms (alarms that ring in and appear on the operator’s console). Assessing the static alarms reveals whether too many alarms are configured, thus generating too many real-time alarms for the operators to handle. Similarly, by analyzing real-time alarms, operators can determine whether there are too many alarms (irrelevant or nuisance alarms) in normal load conditions and during upset situations.For the sake of simplicity, the target alarm counts for each metric are summed up in the following two figures.
Alarms are designed to help the operators mitigate safety, environmental and financial loses. Incident investigations repeatedly show a very real financial loss associated with any safety and environmental incident, therefore, any properly configured alarm that is missed by an operator has a financial loss associated with it. All too often, it is the dramatic events that are scrutinized and brought to attention, yet it is the small, lower priority alarms that create a significant compounding financial effect. To accurately define the priority of alarms, all alarms must have an Impact Category assigned to them to determine both the level and area of concern.
- Environment, health, and safety issues
- Insurance costs
- Plant and operational reliability
Some sites have identified alarm management as part of their ISO practices. If specified as part of the ISO procedures, the site must have the proper procedures and tools in place to ensure their alarm system is properly managed. Without the right tools it is usually difficult and time consuming to achieve these objectives - often, it is impossible.Justification #3: Operational Financial Benefits
Evaluating incident databases and recording whether a missed alarm resulted in a particular incident, can determine the financial impact associated with alarm management. For most plants this will often be around 15 related incidents per year based on close analysis of the data. When developing an alarm management plan as part of a six sigma project, it is important to document both the financial situation before and after an alarm management program so that progress can be tracked. Based on estimated incident costs, an average savings of $250K is often achieved by reducing incidents and improving plant reliability.The next task in evaluating the financial benefits is to examine alarm and event data, assuming this data exists. By analyzing alarm floods, significant and costly events that were not immediately evident, can be quickly identified. Alarm floods need to be analyzed to determine if there is a cost, what the cost is, and whether proper alarm configuration would prevent similar events from occurring again. Moreover, additional benefits will usually arise with the identification of previously unnoticed control or equipment related problems.Operator actions have direct costs associated with them. Analyzing the top 50 operator actions will provide concrete problems and costs that often go unnoticed. Controllers that are often switched from auto to manual, or set points that are frequently changed, are indicative of control or equipment problems. With an experienced person on site, the associated cost can be quickly determined.Finally, a very real benefit, although less tangible, is that an improved alarm system will significantly reduce the number of operator alarms. Reduced alarm volume means the operator has significantly more time, as much as 50%, to monitor and optimize the process. Process optimization can result in significant throughput and quality benefits.Justification #4: Insurance Findings, Premium Savings, and Requirements
A growing number of insurance companies are demanding that sites and organizations implement alarm management programs because of the correlation between alarm management and equipment damage. The reason for this change in policy is that each year within the petrochemical industry alone, North American insurance companies pay out $22 billion in claims related to equipment damage. Insurers that do require alarm management programs, typically offer a reduction in insurance premiums. For self-insured plants, financial savings can be even more significant and are identifiable once an assessment has been completed regarding the cost of damaged equipment caused by poor alarm management.Justification #5: Operational Reliability
Alarm management plays a significant role in any corporate operational excellence program. Since alarms settings are based on equipment protection limits or process limits, exceeding these limits results in excess wear on equipment and loss of production or lesser quality product. These alarm indications can provide insight into how equipment is being used and how it is affected by both manual and automatic operations. With this insight, adjustments can now be made to prolong the operating life and reliability of the process. Most maintenance departments will attest that the life of an asset is strongly tied to its operational use.The Chicken and the Egg Conundrum
How can the justification to acquire the appropriate alarm management tools be made if the very same tools are required to develop the business case justification? Matrikon offers an alarm assessment service to address this paradox. Matrikon’s alarm management tools serve a dual purpose: to perform a concise and efficient assessment of the plant’s current alarm management system and to provide the client with a firsthand evaluation of Matrikon technology.The data and analysis gathered from an assessment will provide a clear understanding of the problems and weaknesses in the alarm system. This becomes the foundation of a sound business justification and project plan.Project Plan OutlineThe project plan is a logical outline of the proposed work and deliverables. The details from phase one, benchmarking & assessment, will help determine whether an entire plant’s alarm system needs to be configured or if it can be limited to key areas.All project plans should now have the remaining 5 phases:
- Benchmark & Assessment
- Alarm management philosophy
- Alarm analysis / rationalization
- Implementation and execution
- Continuous improvement
- Maintenance
Again, for more information about the other Alarm Management Project phases, please refer to Senior Applications Engineer, Michael Marvin’s White Paper, “Five Steps: Integrating Alarm Management to Boost Production”.
Conclusion
Alarm assessment is a well-defined process that provides the technical situation, business justification and plan of action for a particular site. The main ideas addressed are:
- Every alarm configured has a financial impact associated with it.
- Every alarm that is missed, both small and large, costs money.
- Is the alarm system properly configured?
- Are all levels of operation reaping the benefits from the alarm system?
Assessments are standard practice for experienced integrators and can typically be performed within 1-2 weeks after which a very high quality and accurate assessment is delivered.
About the Author |
Jeff Gould is the ProcessGuard Product Manager responsible for overseeing the development, marketing, and sales of Matrikon’s Alarm Management product line. Jeff joined Matrikon in 1996 and helped to develop Matrikon’s driver business, and for the last few years has been responsible for growing and shaping Matrikon’s alarm management solutions. Jeff graduated as a computerengineering technologist from NAIT, and his background includes several years of software development management, and sales and marketing of software solutions for the process control industry.
Latest from Safety Instrumented Systems
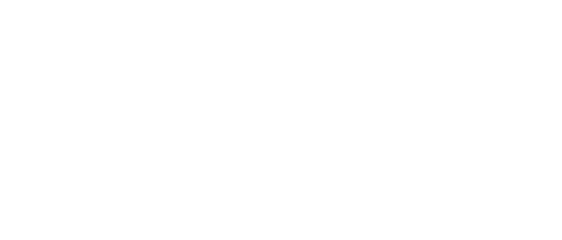
Leaders relevant to this article: