Understanding asset utilization is key to maximizing productivity in any industrial process. In manufacturing, production can be held up by mechanical breakdowns, material shortages, external delays, operator errors and equipment degradation.
In part one of this case study, we showed how advanced analytics can classify lost productivity with a basic set of assumptions, without requiring operator- or equipment-provided reason codes. This enables fine-tuned targeting to deploy limited resources where improvements are most likely and impactful.
When investigating deviations from ideal profiles, multivariate correlations between sensors must be considered in addition to individual sensor profiles (Figure 1). Frequently in industry, we find the low hanging fruit of univariate issues have already been solved, increasing the likelihood that chronic issues are multivariate in nature. In part two, we demonstrate how Seeq was deployed at Syngenta to benchmark operations against ideal practices, and identify operational anomalies using univariate and multivariate approaches.
Benchmarking against the best (univariate)
The fastest 25% of batches can be used to create a reference profile for each relevant process sensor, for example, those that directly impact phase duration or product quality. Slower batches in the upper percentiles can be compared to this reference profile to look for possible delay causes. Rather than targeting the entire batch profile, attention is given to phases responsible for a high proportion of losses.
To illustrate this, focus can be applied to the combined separation phases, where characteristic temperature and pressure profiles are known to directly influence overall batch quality. The “best separation phases,” a subset of all the “separation phases,” are identified quantitatively, based on a duration of less than or equal to the 25th percentile benchmark. These results can be easily examined by users (Figure 2).
Next, “golden” or best profiles for temperature and pressure signals are calculated as the ±3 standard deviation limits, based only on data from the best separation phases (Figure 3). With the best operation profiles developed for temperature and pressure, current operations can be benchmarked using auto-updating reports easily shared with operations teams. Here, reporting date range functionality displays the last X number of batches (where X is user-configurable), and abnormal deviations are highlighted whenever temperature or pressure falls outside of best operating limits (Figure 4).
With this approach, any relevant signals can be monitored univariately to identify operating issues in a timely manner.
Connecting the quality result to corresponding process batch data can be challenging because this result is commonly lab-measured and reported at varying time intervals following completion of the process batch. Seeq provides a single-line, built-in formula function to join batch and quality-result time periods just above in the trend, based on matching batch number values (“Overall batches joined to quality results,” Figure 5).
From this point, with quality results automatically transferred as a capsule property on the resulting condition, it’s easy to create the “Line 1 batch quality aligned to process batches” as a signal representing the quality result, which is shifted back in time by varying amounts to align with the batch operation.
With quality results now listed, along with lost time and time outside best operation metrics in the monitoring dashboard (Table 1), users can rapidly identify which batches merit investigation, and whether the anomalies resulted in inadequate quality or waste.
This lets users differentiate between lost productivity due to different operating profile characteristics compared to other causes.
Benchmarking against the best (multivariate)
While anomalies in single process variables are often easy to detect visually, multivariate issues are typically more complex. Sometimes, profiles for various sensors may be within the individual reference boundaries, but combinations of profiles can create unexplained quality issues.
These multivariate anomalies can be difficult to detect, but they’re critical to understanding underlying causes of lost productivity and inferior quality. To identify these anomalies, Syngenta used the multivariate pattern search (MPS) function in Seeq to make multivariate comparisons of batches against a reference or “golden” set. After training on the best historical separation phases, MPS produces overall “dissimilarity” and individual signal dissimilarities for each batch (Figure 6).
The resulting MPS model can be used in near real-time to monitor dissimilarities for each of the recent separation phases. In Table 2, Batch 747 was the most dissimilar to the historical best separation phases during the time of analysis. In particular, the L01 signal for Batch 747 was the most dissimilar, and it contributed the most to anomalous operation.
These sorts of diagnostic insights equip users to investigate suboptimal operation in a targeted, streamlined manner, identifying many process improvement opportunities.
This showed signal L01 with the largest deviation from ideal. With this information, a user can apply process expertise to understand the contrast of the L01 profile with the best operational time periods, which can lead to improvements that eliminate this issue in the future.
Investigating operational anomalies
Syngenta identified multiple areas for operational optimization by leveraging modern data analytics in Seeq, identifying operational anomalies using univariate and multivariate approaches, and benchmarking current operation against ideal profiles.
Multivariate approaches can reveal valuable insights that aren’t easily detected via visual inspections of signal trends. Alo, subject matter experts can efficiently examine individual batch profiles in the same trending and visualization software environment to identify further actionable root causes from process sensors. By leveraging modern software, companies can implement process improvements to increase productivity and maximize uptime in their manufacturing environments.
Dr. Stephen Pearson is a principal data scientist at Syngenta. He helps manufacturing sites improve data management and analyses. John Cox is a principal analytics engineer at Seeq, where he works on advanced analytics use cases.
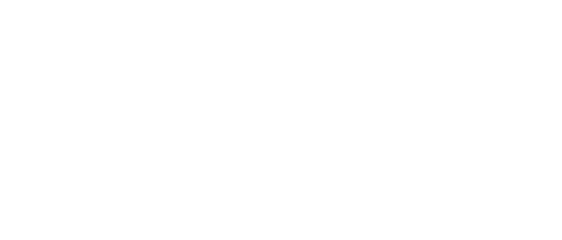
Leaders relevant to this article: