“Leaders should look at efficiency and sustainability as mutually beneficial goals,” said Allie Schwertner, sustainability and energy leader at Rockwell Automation. “Improving the efficiency of operations will reduce waste, which improves the sustainability of processes. This introduces cost benefits, which can then be reinvested in future projects.”
Schwertner spoke as moderator for a keynote session on “Sustainability: From Vision to Impact,” at the ROKLive 2021 virtual event. The session visited with Rockwell Automation partners that have made sustainability a priority and have committed to a positive feedback loop to continuously make processes more efficient and more sustainable.
“In order to help customers meet sustainability goals, it’s important that we hold ourselves to a high standard,” Schwertner continued. “Everything needs to be managed to maintain high sustainability standards in areas such as energy consumption, operational efficiency, waste and recycling.” She welcomed three projects and organizations that are focused on sustainability for waste, energy and water.
Chemical recycling feeds a circular economy
At packaging company, Sealed Air, the makers of Cryovac food packaging and Bubble Wrap protective packaging, “We have a very high sense of purpose—to leave the world better than we found it,” said Sergio Pupkin, growth and strategy officer at Sealed Air. The company has made a pledge that by 2025 100% of its packaging will be recyclable or renewable.
“We want to recycle more in order to drive that circular economy, but the recycling stream for many of our products are still under development,” Pupkin said. So Sealed Air is driving some of that development with its customers, who share a similar recycling journey. “We have the same problems that they have,” Pupkin said.
The transformation into smart factories and beyond would not be possible without automation technology and the partnership with Rockwell Automation, Pupkin added.
Ron Cotterman, vice president of innovation and sustainability at Sealed Air, took attendees on a tour of the company’s innovation center at its Charlotte campus. The tour focused on three areas: one of its automated packaging lines and two of the labs where the company makes new types of packaging material and recycles plastic back into new materials.
At the food packaging lab, a Cryovac auto loader automatically inserts blocks of cheese into the package and seals them, “with a labor- and energy-efficient process,” Cotterman said. “Before that equipment was available, you would have seen a lot more people manually packaging that cheese into those plastic bags, but because of that automated equipment, it happens in a fraction of a second,” he said.
Next, in a small-scale processing lab, “This is where we demonstrate that we can incorporate recycled content into our products and that our products are recyclable, as part of our 2025 pledge,” Cotterman said. The company’s iconic product, Bubble Wrap, for example, is now loaded with recycled content. “We take the same plastic resin that’s used to make it originally and use it again and again,” he said. Sealed Air can also use material that comes from the food side of the business (and all the scraps that are generated there) and recycle that material into the protective side of the business, where it makes products like Bubble Wrap.
“We go through a series of process steps to melt it down and to make new plastic material that performs as if it was brand-new, virgin material,” Cotterman said. The lab is where Sealed Air does its experiments and the essential R&D work for material innovation at a small scale, before it’s practiced at the large-scale facilities. “This capability is brand-new within our industry,” Cotterman said.
The final stop on the Sealed Air tour was the chemistry lab, what Cotterman called the “future of recycling,” where the chemistry is done to make plastic recyclable. “Plastic, whether in the form of a tray or film or bag, can be recycled into raw materials, such as this oil here, that can then be used to make a new plastic. We call that advanced recycling or chemical recycling,” he added.
“We do it because it’s not only good for the planet, but it’s also good for business,” Cotterman said.
Reducing the compressed air carbon footprint
Compressed air systems are crucial to many production processes, but they often represent a plant’s largest energy consumer. Case Controls, which provides control solutions for the compressed air industry, has long been working to help companies reduce their carbon footprint with automation. “We were always about energy reduction from a cost standpoint. When the green movement started, we were already doing that. We were already working with our customers to help them reduce energy, save costs and have a good return on investment,” said Lou York, director of Case Controls. The company also has solutions already built to help customers reduce energy consumption, without reinventing the wheel.
Case offers local controls on individual compressors, or its full suite of products to control an entire plant system. “We manage the amount of horsepower you have online in order to meet the plant demand,” York said.
Over its 30 years, the company has reduced a significant amount of energy usage at a number of large manufacturing plants. “But having only done a fraction of plants, the opportunity to reduce energy consumption in industry remains a large opportunity,” York said.
Devin Sullivan, engineering manager at Case Controls, showed off a number of Case products at its R&D and quality control lab, including a PLC-based control system for a centrifugal air compressor for an automotive manufacturer and another version going to a power plant. Products are tested, including exercising every I/O, the start/stop modulation of the inlet and bypass valve, and monitoring vibrations, temperatures and pressures.
Case can also retrofit old systems with its suite of products. “The retrofits are designed to replace and establish the same footprint as what the compressor OEM control system takes up inside the panel,” Sullivan explained. “We design and engineer a retrofit that is literally plug-and-play.”
From reclamation to revenue
Where Dr. Paul Ziemkiewicz, director of the West Virginia Water Research Institute at West Virginia University, grew up in western Pennsylvania, all the big rivers and the small streams were dead from acidic mine drainage. Today, his work at West Virginia University is cleaning up the environment and those waters from the legacy mines that continue to leach contamination. Acid mine drainage typically happens when pyrite in coal is exposed to oxygen in the air and water, reacting to form sulfuric acid, Ziemkiewicz said.
In 2015, the U.S. Dept. of Energy showed an interest in identifying sources of critical minerals and rare earth elements. “I talked to people in the industry. I accessed some old data sets and turns out there were a lot of rare earths in acid mine drainage that no one had ever looked at before,” Ziemkiewicz said.
Over a period of about four-and-a-half years, the university developed a process for extracting the rare earth metals. “In order to make this into a commercial product, you have to be able to put feedstock in, hit some buttons and have good stuff come back out the end of it,” Ziemkiewicz said. “We couldn’t do this without Rockwell providing that automation, the sensors and control technology that make the process work.”
The session then toured two West Virginia sites making use of the technology to address acid-mine drainage contamination, including a centralized, integrated acid-mine drainage treatment plant that was built through a special reclamation fund managed by the West Virginia Department of Environment. The plant cleans up forfeited and abandoned mines sites and has restored aquatic life to many waters in the area.
And at “Site #834,” a unit is being built to do both reclamation work on the contaminated waters and extract the rare earth elements for profit. “It is strictly treating the water coming off the #834 site that was previously contaminating the headwaters of the Potomac River,” Ziemkiewicz said. “The #834 site is the first integrated demonstration of our technology.” Most importantly, the process is doing reclamation work, and the treatment process itself creates a revenue stream to support the work.
The full ROKLive presentation, “Sustainability: From Vision to Impact,” on which this article is based remains available on demand through October 2021.
Latest from Sponsored Content
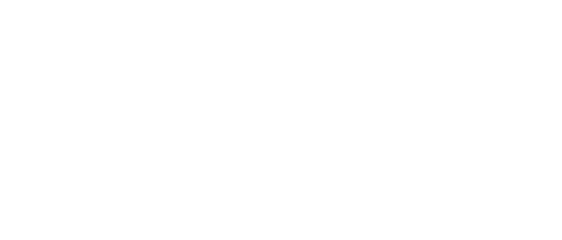
Leaders relevant to this article: