With its October 2009 launch of the DeltaV automation system with "I/O on Demand," Emerson Process Management set out to revolutionize one of process automation's most onerous and time-consuming activities: the engineering and management of input/output (I/O) subsystems.
I/O on Demand proposes to eliminate broad swaths of time and effort over a process automation system's lifecycle, to shorten project schedules and minimize system footprint, even while increasing future flexibility. In so doing, I/O on Demand promises to deliver for its users "the greatest degree of flexibility with the least amount of effort and risk," Chief Strategic Officer Peter Zornio told Control at the time.
After just four years, Electronic Marshalling with CHARMs (characterization modules) technology, the cornerstone of I/O on Demand, already has logged more than a billion hours of operation at 300 sites worldwide. How these users—throughout the process industries and around the globe—are using Electronic Marshalling to deliver previously unthinkable results is the focus of this special report. First up, though, Control visits with Claudio Fayad, Emerson marketing director, DeltaV platform, for the big picture view of what's made Electronic Marshalling such a game-changer for how automation is done in the process industries.
Q. Electronic Marshalling technology has really taken off since it was first introduced. Why do you think so many users have opted for this approach?
A. The great thing about Electronic Marshalling is that people make their own conclusions about the benefits of the technology very, very quickly. Its ability to compress project engineering schedules has clear advantages in both greenfield plants and in retrofits.
Read Also: Electronic Marshalling Slashes Costs for Sulfuric Acid Maker
With Electronic Marshalling, users can literally create new time and space where there was none before. The sheer amount of benefit is simply that big.
Q. How is it that Electronic Marshalling has eliminated so much time and effort?
A. If you think of the old way of doing things, a project engineer had to have a pretty firm handle on the number and type of I/O points that would be needed before he could start doing his hardware design. Each type of I/O required its own type of I/O card, typically in groups of eight. Further limiting system flexibility, each I/O card was tied to its respective controller. And when those inevitable late changes in process design trickled through, he may or may not have allowed for an appropriate number of the right type of I/O. The end result of all this inflexibility was to incur expensive change-orders late in the project cycle, or to push hardware design back later in the timeline, potentially delaying overall project delivery.
"Automation is no longer a project bottleneck and is off the critical path." — Claudio Fayad, Marketing Director, DeltaV Platform, Emerson Process Management
But with Electronic Marshalling, all our project engineer needs to get started is an approximate total I/O count. Each and every channel is fully characterized by its respective CHARM plug-in, which can be added or changed even up to the last minute without impacting the overall hardware design. Each I/O channel is mapped in turn to its appropriate controller automatically through the DeltaV system software, and can be logically reassigned even on the fly. And, in the rare case of a CHARM failure, annunciation is instantaneous and replacement of a single CHARM is much easier than that of an entire board, significantly reducing mean-time-to-repair.The decades-old practice of landing wires in a marshalling cabinet, then wiring each landed pair to an I/O channel on the right kind of card connected to the right controller, is eliminated—along with the marshalling cabinets themselves. All of this greatly streamlines system engineering and documentation. Plus, you can begin building—or just order—the cabinets you need before you've even finished the process design. Automation is no longer a project bottleneck and is off the critical path. And the benefits don't stop when a project is completed. Because each I/O channel can be re-characterized at any time by simply changing its CHARM, flexibility for the future is preserved as well.
Q. So, the need for physical marshalling cabinets essentially disappears. Have some traditional work processes disappeared as well?
A. When you think of the traditional hardware factory acceptance test, or hardware FAT, it's really all about the I/O. You're not testing the controllers themselves; you're testing all the wires that were pulled, the screws that were turned, and the cabinets that were built over perhaps the past 10 months on a big project. But if all of that custom panel-building and cross-wiring goes away, you can cut much of the FAT as well. With Electronic Marshalling we're seeing an extreme reduction in FAT and commissioning time. One large oil company, for example, is going as far as creating a new "no hardware" FAT methodology that acknowledges this new reality.
Q. Is there more to I/O on Demand than just Electronic Marshalling?
A. While Electronic Marshalling is at its heart, I/O on Demand also describes a broader human-centered design (HCD) effort at Emerson Process Management that includes both WirelessHART and FOUNDATION fieldbus networks. Emerson Smart Wireless networks, which are approaching 2 billion hours of operation across more than 10,000 wireless systems, provide an easy, seamless way to add "wireless I/O" wherever and whenever the need for a new measurement point arises.
"HCD helps us transcend work processes that as an industry we long believed were unavoidable."
FOUNDATION fieldbus technology normally requires third-party power supplies and power conditioners—along with the necessary engineering and wiring and cabinet space. But with DeltaV S-series and I/O on Demand, we've integrated the power circuitry within the FOUNDATION fieldbus H1 card itself. The additional cabinet footprint associated with use of external segment power supplies is eliminated, along with segment power design, installation and troubleshooting tasks. In short, the third-party power conditioners and dedicated power supplies—and all the engineering and testing that went with them—also are a thing of the past.Another way in which we allow users to further leverage their I/O investment is in the seamless communication of the DeltaV SIS process safety system information to the basic process control system. In this way, information from safety I/O can be used to allow the control system to make more informed decisions.
Q. How else has HCD driven changes in the original I/O on Demand offering to meet other user needs?
A. Key technology extensions over the past few years include the launch of the modern DeltaV SIS with Electronic Marshalling, which delivers all the same time, space and flexibility benefits to the engineering of safety system I/O. And, just as Electronic Marshalling eliminated marshalling cabinets, intrinsically safe CHARMs have eliminated standalone safety barriers—and the need to engineer, install and enclose those components as well.
The beauty of HCD is that it provides a powerful way of helping change the way we do things. It can help us to transcend work processes that as an industry we've long believed were unavoidable. Electronic Marshalling is representative of the ways in which Emerson is striving to remove complexity where we can, eliminate work where possible, and embed knowledge where practical.
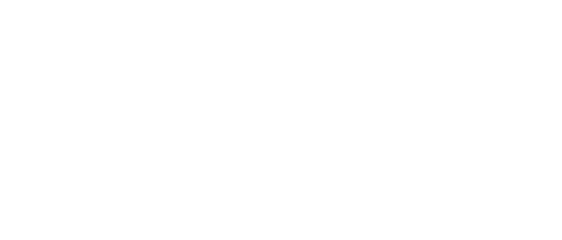
Leaders relevant to this article: