On December 10, 2005, Tank 912 at the Buncefield Oil Storage Depot in Hertfordshire, England, was filling with gasoline. According to a report by the European Process Safety Centre, the tank had two forms of level control: a gauge enabling personnel to monitor the filling operation; and an independent high-level switch (IHLS) which was meant to shut down operations automatically if the tank was overfilled.
The first gauge stuck and the IHLS was inoperable, so there was no means to alert the control room staff that the tank was filling to dangerous levels. Eventually, large quantities of gasoline overflowed from the top of the tank. A bund retaining wall around the tank and a system of drains and catchment areas that were supposed to ensure that liquids could not be released to the environment failed. More than 66,000 gallons (250,000 liters) of gasoline escaped from the tank before the explosion occurred.
[sidebar id =1]A vapor cloud formed, ignited, and caused a massive explosion and fire (Figure 1). The fire, the largest seen in peacetime UK, engulfed more than 20 fuel tanks and burned for five days. The explosion itself registered 2.4 on the Richter scale.
Five companies were charged with offenses arising out of the investigation of the Buncefield incident. Proceedings were completed at St Albans Crown Court on 16 July 2010, and fines amounting to $5 million (£4,081,000) were assessed.
Detecting Leaks
As a result of the Buncefield and other incidents, refining and petrochemical storage areas are under increased pressure to monitor for tank leaks. Even when there are no explosions or fires, leaks result in lost product and harm to the environment if retention areas are breached. Leaks contained in retention areas also pose a problem as the affected area must be decontaminated.
Fuel leakages emit oil vapor, generating a hazardous area where a spark can cause an explosion. Fuel has a high ignition temperature, but if the leakage goes near a heated point such as a mechanical pump, it’s very difficult to fight the fire. Tank farms often have several pump stations near retention bunds.
Hi-Hi level switches are increasingly being deployed, even in tanks that have an IHLS. The Hi-Hi switch mounts above the high-level switch and acts as a second alarm switch. The problem with a Hi-Hi switch is that it won’t be activated unless the first level switch fails, so it may never be tested except during maintenance activities. Some switches have built-in diagnostics that verify proper operation, but this is not a foolproof solution. Dual radar or ultrasonic level instruments are also being used, with each acting as a backup to the other.
While level switches and redundant level instruments can guard against tank overflows, a storage tank can leak from several sources such as inlet and outlet piping and valves, chopper mixers, pumps and cracks in the tank. Because the storage tank is an “island” in the center of a retention pond, fuel leaks drain directly into the pond, requiring the use of a hydrocarbon leak detection system.
Unfortunately, the costs of installing wired hydrocarbon leak detectors can be very high. A single storage tank may require six or more leak detectors, all of which must be wired back to the automation system. Additional inputs may have to be installed at the automation system to accommodate the new leak detectors, and application software for tank monitoring must be configured to diagnose the inputs and signal an alarm.
Because of the high cost of leak detection, in an average refinery with 100 storage tanks, only 5% have leak detection. Considering that the U.S. currently has 122 refineries, that means more than 10,000 storage tanks are operating without leak detection in U.S. refineries alone, with tens of thousands more unmonitored tanks worldwide in refineries, tank farms and chemical plants. One way to reduce the high cost of hydrocarbon leak detection is with WirelessHART leak detectors, which not only cut or eliminate the cost of wiring, but also allow alarm processing to be performed by a PC.
Detecting Hydrocarbons
[sidebar id =2]One type of WirelessHART hydrocarbon detection device is a TraceTek TT5000 fuel sensing cable (Figure 2). The entire length of the cable is sensitive to the presence of liquid hydrocarbons. The core of the cable is composed of a bundle of wires formed into a spiral construction. Two of the wires are electrodes. The two electrodes have a metal conductor core and a jacket of conductive polymer. The electrode wires are on opposite sides of the spiral bundle of wires and do not touch each other. They are somewhat smaller than the other wires in the core bundle. A tubular jacket of conductive, rubbery polymer is extruded over the top of the wire bundle.
[sidebar id =3]Monitoring circuitry constantly checks for any conductivity between the two electrodes. An open circuit between the two electrodes is an indication that the cable has not been exposed to hydrocarbons.
When a liquid hydrocarbon comes into contact with the cable, a very small amount of the spilled liquid will be absorbed into the rubbery tube, causing it to swell. After sufficient fuel has been absorbed into the rubbery tube, it will thicken enough to come into contact with the two electrode wires in the core of the cable.
When contact between the jacket with the two electrodes occurs, an electrical pathway exists from one electrode wire to the other through the conductive material in the rubbery tube. The monitoring circuit detects the sudden drop in resistance between the two electrodes and reports via WirelessHART that a leak has been detected via a wireless mesh network.
[sidebar id =4]Sensing cables can be configured in various ways for mounting on pumps, valves and pipelines (Figure 3) to provide local detection of hydrocarbon leaks.
For leak detection in or near retention ponds, the fuel sensing cable is installed in a TraceTek Fast Fuel Sensor probe. The probe is immersed in the retention pond, where it is exposed to water. Should a liquid hydrocarbon come into contact with the probe, a very small amount of the spilled liquid will be absorbed into the polymer, causing it to swell.
The probe detects the sudden increase in conductivity and reports via WirelessHART that a leak has been detected (Figure 4). Reaction time is typically less than a few seconds for light or middle weight fuels such as gasoline, jet fuel or diesel. It is also responsive to crude oil and some heavier weight fuels and heating oil, but response becomes progressively slower as fuel viscosity increases and volatility decreases. In most cases, the sensor will reset when removed from contact of the spill after the fuel evaporates.
Monitoring Retention Ponds
[sidebar id =5]To monitor a retention pond, the probe is installed on a floating pad (Figure 5). This allows the sensor to function in periods of drought, when the water level might drop or completely dry up, or during rainstorms when the water can rise.
Depending on the diameter of the tank, a retention pond may require from one to six detectors. Typically, a field assessment is done for each tank to determine the fuel flow, identify the hydrocarbon fuel being stored, calculate the number of detectors needed, and determine where to place them. On large tanks—30 feet diameter or larger—it may be advisable to also install leak detectors on the drain, valves and chopper mixer. This is because a large tank has a large retention pond, and small leaks can be dispersed in the water.
The WirelessHART transmitter sends data to a wireless gateway, which is hardwired to a PC, usually via Ethernet. Depending on the distances between the leak detectors, the transmitters and the gateway, a single Wireless Gateway may serve the entire tank farm.
At the PC, software analyzes the data from the detectors and proves and sounds an alarm if a leak has occurred, and provides leak location information.
Monitoring Tanks and Ponds
At a tank farm in southeastern France, Vegase installed hydrocarbon leak detectors on 46 storage tanks (Figure 6). As the map shows, some tanks required only one detector, while others required 2, 3 or 4 detectors.
The entire tank farm required 141 detectors. The project was accomplished in three phases, following a single-tank test case in 2012. Phase 1 in 2013 added 18 tanks with 52 detectors, Phase 2 in 2014 added 12 tanks with 28 detectors, and Phase 3 in 2015 added the final 15 tanks with 58 detectors.
In this refinery, the tank farm is on a mountain with a big retention bund. Floating detectors are placed in the retention ponds surrounding tanks, taking into account the normal flow of rain water, while fixed point detectors (without floating devices) are put on the opposite flow line. This ensures detection no matter where a leak or spill progresses.
Emerson’s AMS Wireless SNAP-ON software was used to design the WirelessHART mesh network, determine how many gateways and repeaters were required, and where each should be installed. Based on the software results, three Emerson 1420 wireless gateways were installed along with 40 Emerson 708 wireless transmitters acting as repeaters.
[sidebar id =6]
[sidebar id =7]
The gateways and repeaters gather data from the detectors, provide redundancy, and ensure the data arrives at the main gateway in the control room. The main gateway is hardwired to a PC via Ethernet, and the PC is connected to the automation system via a hardwired Ethernet link.
At the PC, software analyzes the data from the detectors, and proves and sends an alarm to the automaton system if a leak has occurred. Facility personnel can then go to the PC and view leak location and other detailed information.
Today, the entire tank farm is covered with leak detectors for 100% coverage. The cost for the entire turnkey system was about $1 million, one-third the cost for a wired system, and the system has been operating to the satisfaction of the facility since its installation.
[sidebar id =8]
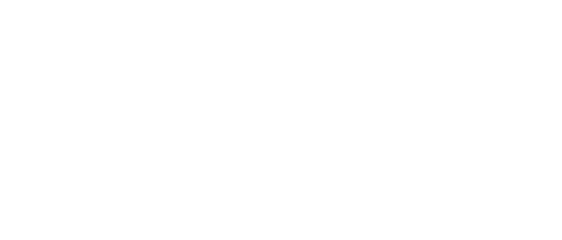
Leaders relevant to this article: