IT'S IRONIC; in their endless quest to reduce costs while increasing output and quality, many manufacturers have been ignoring one of the most potent technologies for achieving those ends. Not only that, its a technology in which most of them already have made substantial investments!
The technology? HART. For years, instrument and systems vendors have been incorporating HART communications capabilities into field devices, enabling those devices to send digital information, including diagnostic information and secondary variables, to host systems. (The HART Communications Foundation estimates that more than 15 million HART-capable devices are installed worldwide.) But with the exception of maintenance personnel tramping into the field with handheld communicators to configure instruments, most users have left HARTs benefits untapped.
Those days are coming to an end, however. Instrument vendors are providing open access to their devices through readily available device descriptions; control systems providers are including HART I/O hardware in their products as well as asset management software; and many vendors are marketing products that enable the owners of legacy, analog-only systems to access the power of HART.
So, with HART data more accessible and potentially useful, key questions users face are:
- Whats the best way for my company to access that data?
- How do we identify applications in which we can use HART to generate business value?
A Brief History
HART, an acronym for Highway Addressable Remote Transducer, was developed in the late 1980s and became publicly available in the early 1990s.
Unlike other recent field communications protocols, such as Foundation Fieldbus and Profibus, which are totally digital, HART is a hybrid analog/digital technology. An instruments primary variable is transmitted via the industry standard analog 4-20 mA signal, but up to four secondary variables and device diagnostic information can be digitally piggybacked on it. As a result of these digital communications capabilities, users have access to extensive data from their devices, including diagnostic information and -- in the case of some instruments -- multiple process variables (i.e., a pressure transmitter also might be capable of providing temperature data).
In 1993, the former HART Users Group formed the HART Communications Foundation (HCF), which assumed ownership of the protocol and responsibility for administering and maintaining it. As part of its mission, HCF tests systems and devices for HART compliance and provides educational services to vendors and users.
In HARTs early years, many instrument vendors quickly adopted the technology, but kept a proprietary hold on the device descriptions that enable a host--such as a control system, an asset management system or a configurator--to communicate with its devices. Sandro Esposito, a Masoneilan digital products specialist, recalls that nearly every instrument maker had its own software package for talking to its device, effectively rendering that device an island of automation.
Charlie Piper, fieldbus product manager for Invensys Foxboro business unit, agreed. There are more than 500 different HART devices in the marketplace, and theres lots of information you can get about their performance, such as when valve positioners are starting to wear out or stick, he says. But until recently no one had come up with a way for all the host vendors to have a user interface to do these neat things with everyone else's device.
Today, however, most vendors make their Device Description (DD) files openly available. HCF maintains and distributes a library of hundreds of DDs that enable any HART host (e.g., control system, configurator, asset management system, safety system, etc.) to communicate with a vast array of field devices. That development is coupled with the development of comprehensive applications to monitor assets, such as Siemens Process Device Manager, Emerson Process Managements AMS Device Manager, and Honeywells Asset Manager PKS. As a result, users now are able to access most if not all of their device information from a single screen, regardless of device manufacturer.
In recent months, HCF has developed new tools and technologies to make development of HART-complaint DDs easier. These include the new Device Description Integrated Development Environment (DD-IDE), which is designed to streamline development, testing and maintenance of DDs and facilitate the creation of product applications with DD capabilities.
The DD-IDE supports the iterative DD development style with a fast and efficient integrated tool set. Each step in the edit-build-test cycle is supported in a DD-aware editing environment, says Wally Pratt, HCFs chief engineer.
Also near completion is the Enhanced Device Description Language (eDDLEDDL) specification. eDDLEDDL gives vendors the ability to add new capabilities to DDs while improving cross-platform compatibility and facilitating device set-up. (See details elsewhere in this supplement.)
HART-enabled instruments deliver greater value than ever before, says Dave Smith, manager of Yokogawas plant network technology center. The processing power of the devices is increasing greatly, says Smith. Therefore, field instruments feature additional functionality, including diagnostic type functions, predictive functions and others.
Jim Cobb, marketing manager of Emerson Process Managements Rosemount Division, notes that users are increasingly aware of the capabilities of the digital field. One of the reasons is that suppliers are better implementing features to use the capabilities of HART devices, says Cobb. Another reason, ironically, is that theres been so much talk about fieldbus in recent years. People are realizing that HART is capable of delivering many of the same benefits as fieldbus.
Identifying High-Value Applications
Industry experts are nearly unanimous that the greatest return on HART technology investment lies in the ability to continuously monitor the field instruments. Masoneilans Esposito notes that drastic reductions in maintenance staffs during the past decade have made automated monitoring of field instruments an absolute necessity in many plants. By being able to watch and track the condition of plant floor devices, maintenance and operations personnel can spot problems in the making and take action before they cause process upsets and unplanned shutdowns. Conversely, being able to see that a device is working well enables users to avoid unnecessary maintenance activities.
"If you have a lot of HART devices in your installation, and you're not monitoring them on a continuous basis, you're missing a great deal of opportunity, says Tom Holmes, president of MACTek, a manufacturer of HART modems. There's diagnostic information, alarms, alerts and confirmations of whether the analog signal is good or bad."
Industry experts recommended a number of strategies to help users identify the most high-value applications involving continuous monitoring.
Emersons Cobb suggests that plants go about taking advantage of HART gradually.
One of the nice things about HART is that you can add its capabilities to your plant, loop by loop, and gradually take your facility from analog to a fully integrated HART plant, says Cobb.
Id start with online monitoring of my most critical assets. Thats where Im going to get the most value from predictive diagnostics, such as being able to avoid unplanned shutdowns and preventing off-quality products, adds Cobb. At the same time, I might start using HART to monitor other instruments offline and gradually, as my maintenance budget allows, bring other assets online.
Marcelo Dultra, vice president of sales and marketing for Smar International, recommends plant audits as a means of identifying areas ripe for improvement via HART. They should do a full check of what equipment they have installed and what technologies theyre using. This kind of thing usually takes a maximum of two or three days, says Dultra, who adds that Smar, as well as other vendors and consulting firms, provide such services.
"It's always good to get opinions from outside the plant, from people who have seen other operations. If you work a long period in your own plant, you miss some points that are important, especially when it comes to the technologies available today, he adds.
Prasad Raghavendra, Honeywells product manager for all systems-related HART products, recommends that users review a history of process upsets and their causes to identify areas that are ripe for HART-enabled continuous monitoring. Make a business plan out of that to determine if the cost of incidents are higher than the cost for investing in HART-enabled I/O, says Raghavendra. Thats a fairly simple method that would clearly indicate whether it was worth it for the customer to make the investment.
In some instances, he says, the benefits from investing in HART will be plain. For example, your plant could be having problems caused by simple incidents like sensor failures. If youre simply relying on a 4-20 mA signal, the operator will see a local trip, but everything in that group of devices becomes suspect. This requires the operator calling maintenance and what could be an extensive debugging process. With HART, however, if theres a sensor failure, the device tells you that its the source of the problem, saving you time and resources in correcting the malfunction.
Processes that could benefit the most from this technology are those with a large number of remote-connected HART devices that can be brought in to a control system through remote HART I/O, says Eric Olson, a senior product manager with ABB. This could include processes such as those in the oil and gas or wastewater treatment industries, where there are many satellite I/O stations.
Foxboros Piper recommends that users employ a diagnostic tool such as ExperTunes PlantTriage, to monitor loops and field instrument performance and identify potential troublespots that could benefit from full time monitoring via HART.
HART can play an important role in refineries, mills and power plants that employ process safety systems. To maintain a systems Safety Integrity Level (SIL) rating, safety system valves must be periodically tested to ensure that they will move if called upon in an emergency. Full-range tests can be conducted only during plant shutdowns, but these occur only every two to three years. However, by stroking a valve by as little as 10 percent, which does not disrupt a process, plants can ensure the reliability of their safety valves. A valve positioner has the ability, via HART, to confirm to operators that the valve actually responded to the movement command.
Robert Hotard, a product manager with instrument-maker K-Tek, also suggests that users take advantage of HCFs expertise in planning HART-based projects. The first thing Id recommend to anyone interested in HART is to go to the HART Communication Foundations website, says Hotard. Theres a lot of information there thats available to everyone and explains in great detail how to use the protocol and the benefits that are possible. Im currently writing some manuals for K-Tek products, and in them I specifically reference the HCF website.
Dont Overlook Control Opportunities
While most facilities use HART for applications related to device configuration and maintenance, users also should look for opportunities to use HART data for process monitoring as well. For example, in applications where conditions such as temperature, pressure and levels change relatively slowly, users can reduce the number of instruments they need in the field by acquiring multiple variables from a single device. Hotard points to tank farms as being ideal sites in which to make use of HART for applications such as inventory monitoring.
In relatively small operations, users can set up set up modest, but effective SCADA systems that utilize HART technology, says Macteks Holmes. You could continuously monitor up to eight points using a PC equipped with eight USB HART modems. Thats very do-able, says Holmes. For software, you could use a dedicated data acquisition package such as Wonderwares InTouch software, or something as basic as a Microsoft Excel spreadsheet. I think there are plenty of operations such as bakeries or small specialty chemical plants that cant justify spending the money for a large control system. But with HART input and a PC, you can build yourself a quick and dirty DCS, he adds.
Liberate the Genie
Having HART capabilities at your disposal, but not taking advantage of them, is like keeping the genie stuffed in the lamp. By carefully examining your facility, looking at the HART capabilities you already have, and carefully weighing the need for additional investments, you can take full advantage of opportunities for improvement.
Keys to HART Value
- Identify the most critical loops in your plant first and begin monitoring them via HART on a full-time basis. Other less essential loops can be monitored offline periodically.
- An outsider can bring fresh perspective. So consider bringing in an outside consultant to help you identify areas where you can realize maximum benefit from HART-based solutions.
- Make a business plan out of that to determine if the cost of incidents are is higher than the cost for of investing in HART-enabled I/O.
- Employ a diagnostic tool to monitor loops and field instrument performance and identify potential troublespots that could benefit from full time monitoring via HART.
- Take advantage of resources and training provided by HART Communications Foundation.
- While HART is used primarily for equipment monitoring and configuration purposes, dont overlook opportunities to use it in appropriate control applications.
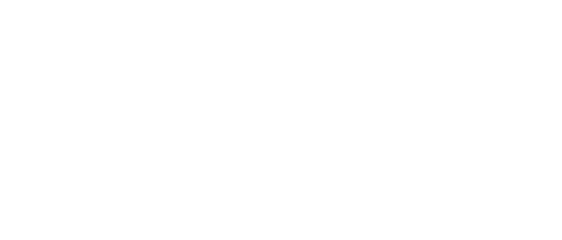
Leaders relevant to this article: